Amr Hassan
NCQ Manager at Novartis- Claim this Profile
Click to upgrade to our gold package
for the full feature experience.
-
English Full professional proficiency
Topline Score
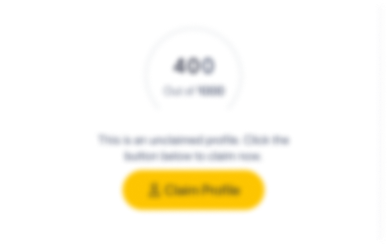
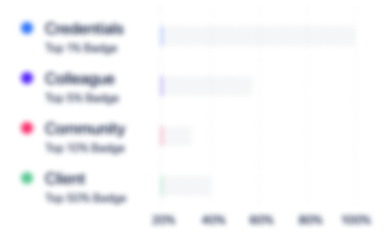
Bio


Credentials
-
Certified Investigation Coach
PfizerMar, 2020- Nov, 2024 -
Effective Technical writing
PfizerFeb, 2018- Nov, 2024 -
M1 for Investigations
PfizerFeb, 2018- Nov, 2024 -
TTT (Train The Trainer)
PfizerJul, 2017- Nov, 2024 -
QRM (Quality Risk management)
PfizerOct, 2016- Nov, 2024 -
GB Six Sigma
PfizerOct, 2015- Nov, 2024 -
Pfizer Human Performance
PfizerMay, 2015- Nov, 2024
Experience
-
Novartis
-
Switzerland
-
Pharmaceutical Manufacturing
-
700 & Above Employee
-
NCQ Manager
-
Jan 2022 - Present
**Third Party Management:- Ensure all aspects of GxP operations are compliant with the requirements of Novartis QM/Policies and regulatory/legislative requirements.- Due diligence and qualification are in place for all GxP Third party.- Manage Quality agreement process for all GxP Third party, Vendors, suppliers and external service providers.- Manage inspections and audits for Third Party and ensure relevant CAPAs have been completed/closed.**Business Development & Licensing (BD&L):- Act as NCQ BD & L single point of contact (sPOC) for relevant activities till products' launch.- Manufacturing, Storage, Distribution due diligence.- Management of Quality Assurance Agreement (QAA).- Management of Qualification Risk Assessment (QRA).- Act as QARP in audits & inspections as relevant.**Complaints system Management:- Manage complaints according to the Novartis Corporate QM and local procedures and ensure relevant CAPAs have been completed/closed.- Support GMP QA in recalls, counterfeits and product tampering according to the Novartis Corporate QM and local procedures. Participate in NEM cases and ensure relevant CAPAs have been completed/closed.- Accountable for end to end Health Authorities & above-country escalations in cases require HA/Management attention according to Novartis QM/Policies and regulatory/legislative requirements.**Change Controls system Management:- Manage Transfer projects & CC system.- Ensure that an effective CC process is in place.**Data Integrity Champion.**Documentation system management:- Ensure organization local procedures are in compliance with Novartis global standards through; relevant QM & Global SOPs gap assessments & track related actions as applicable.- ESOPs/CONDOR system management.- SOPs Periodic review**Training quality system management.**Management of artworks NCQ QA responsibilities.
-
-
-
Viatris
-
United States
-
Pharmaceutical Manufacturing
-
700 & Above Employee
-
Site Quality Assurance Manager
-
Dec 2020 - Dec 2021
Lead team of 22 QA colleagues.Advises junior colleagues on significant or complex issues associated project team oversight, ensuring appropriate resolution and escalation, as required.Drive team engagement, effective communication, and the development of Quality leaders within the QA team.Continuously monitor KPIs in QA team and provide coaching and feedback.Reviews and approves various GMP documents including batch records, protocols/reports, all types of investigations (i.e Laboratory, suppliers, manufacturing, contractors, …), change controls, product specifications, etc.Provides Quality oversight for project-related investigations and issues and advises on policies and procedures. Contributes to the interpretation of GMPs for functional areas.Supports authoring of Quality Assurance Agreements.Leads and/or participates on limited duration teams, continuous improvement initiativesPeriodic product review: Approval of risk assessments for annual review plan insures its implementation and approve of annual product reviews.Manage the overall assurance and disposition of products produced at the manufacturing site.Ensure a system is in place for validation/qualification/calibration activities.Member of routine and Ad hoc SQRT meetings.Revision of AQRT/NTM Reports.Coordinate Technology Transfer activities of Manufacturing Procedures to other sites.Ensure implementation of data integrity program within QA and on-site operations level.Plan the preparation for and management of quality-related audits conducted by Corporate and regulatory agencies.Interface with regulatory agencies to discuss lot records, manufacturing procedures, test results, and labeling.Internal Audit & CAPA system: Approval of annual audit plan and communication of critical internal audit finding in SQRTs.Responsible for QA resource planning.Preparation of budgets.Monitoring budget adherence with QO Leader.
-
-
-
Pfizer
-
United States
-
Pharmaceutical Manufacturing
-
700 & Above Employee
-
Site Quality Assurance Manager
-
May 2020 - Nov 2020
Lead team of 22 QA colleagues.Advises junior colleagues on significant or complex issues associated project team oversight, ensuring appropriate resolution and escalation, as required.Drive team engagement, effective communication, and the development of Quality leaders within the QA team.Continuously monitor KPIs in QA team and provide coaching and feedback.Reviews and approves various GMP documents including batch records, protocols/reports, all types of investigations (i.e Laboratory, suppliers, manufacturing, contractors, …), change controls, product specifications, etc.Provides Quality oversight for project-related investigations and issues and advises on policies and procedures. Contributes to the interpretation of GMPs for functional areas.Supports authoring of Quality Assurance Agreements.Leads and/or participates on limited duration teams, continuous improvement initiativesPeriodic product review: Approval of risk assessments for annual review plan insures its implementation and approve of annual product reviews.Manage the overall assurance and disposition of products produced at the manufacturing site.Ensure a system is in place for validation/qualification/calibration activities.Member of routine and Ad hoc SQRT meetings.Revision of AQRT/NTM Reports.Coordinate Technology Transfer activities of Manufacturing Procedures to other sites.Ensure implementation of data integrity program within QA and on-site operations level.Plan the preparation for and management of quality-related audits conducted by Corporate and regulatory agencies.Interface with regulatory agencies to discuss lot records, manufacturing procedures, test results, and labeling.Internal Audit & CAPA system: Approval of annual audit plan and communication of critical internal audit finding in SQRTs.Responsible for QA resource planning.Preparation of budgets.Monitoring budget adherence with QO Leader.
-
-
Site Investigation Lead
-
Feb 2018 - Apr 2020
Site Investigation System and Strategy:- Own and ensure a robust investigation process for the site, through the consistent and effective use of investigation system SOP/s and tools, and strong investigation culture across the site. - Actively performing routine assessments and analysis of the site investigation system by analyzing related metrics, seeking out trends and discussing opportunities regularly at the Site Quality Review Team and/or Site Leadership Team meetings.- Work with site leadership and partner with center global teams (Quality/Training/OpEx/EHS) to develop a robust site strategy and action plans for improving the Investigation system.Capability Building and Site Collaboration- Implement the Global Investigations Training Curricula for QO and EHS investigations; ensure ongoing support, active coaching, and the use of the structured on-the-job documents for qualification of new originators/investigators/approvers and for those that may need additional knowledge and skills. Work with Center resources as necessary.- Ensure sufficient training and coaching resources are available and occur in a timely manner to meet site investigation goals.- Collaborate with the site PHP Lead (Pfizer Human Performance), site training lead, site OE colleagues, site EHS colleagues to ensure that all investigations training, tools and methodology are consistently used, including DMAIC methodology (M1/M2/M3) to ensure adequate RC analysis and CAPA, and PHP to reduce and prevent Human Error.Global Investigation Sharing- Participate regularly and contribute to global discussion groups by sharing information between the groups and the site colleagues, replicating practices, and promoting/enabling site colleague participation.- Work as needed with global teams (Quality/Training/ OpEx and EHS) SME’s to keep up to date with activities regarding the Investigations system.- Collaborate as needed (along with site PHP Lead) with the Regional PHP Lead.
-
-
QA IPC/Deviations Section Head
-
Feb 2016 - Apr 2020
Lead Team of nine colleagues.Act as investigations SQA (Site Quality Authority) through;- Managing the “Deviations Handling system”- Reviewing and approving all kinds of investigations (Laboratory investigations, Manufacturing investigations, Complaints, Contract manufacturers investigations…).- Responsible for having a robust system in place to ensure that all NTM “Notification to Management” procedures are in place for incidents that require SQL (Site Quality Lead) and OpuQl / VP (Operational unit Quality Lead / Vice President) attention.- Responsible for approving and follow-up of the Corrective Actions/Preventive Actions generated from deviations.- Ensure that each confirmed case is investigated appropriately including ensuring investigation timelines are met.- Responsible for preparing the “Area Quality Review Team Reports” for issues/deviations that require AQRT attention.- Annual Deviations trending.Leading & Supervising the In-Process Control laboratory through:- Trouble shooting the daily production deviations.- Ensure & oversight the GMP standards in the production.- OJT for IPC team.- Managing the lab resources & equipment status.- Ensure that IPC procedures & test methods are complying with the updated Pfizer & reg. requirements.Aid IPC/Deviation team to specify their annual objectives & follow-up the objectives’ progression & conduct their annual appraisals.Review & approve the site’s standard operating procedures, Quality assurance profiles, master bill of material & Master batch records.Share in the preparation for and escorting of quality-related audits conducted by Corporate and regulatory agencies.Interface with regulatory agencies to discuss lot records, manufacturing procedures, test results, and labeling.Managing & Execution of Cleaning & Utilties validation Master plans.Development of various risk assessments.
-
-
Quality operations - Quality systems/Deviations
-
Dec 2014 - Jan 2016
Responsible for managing the “Deviations Handling system”.Act as the site point of contact regarding Quality system/Deviations at Cairo site.Responsible for approving and follow-up of the Corrective Actions/Preventive Actions generated from deviations.Share in the preparation for and escorting of quality-related audits conducted by Corporate and regulatory agencies.Interface with regulatory agencies to discuss deviations and related incidents.Managing & Execution of Utilities validation plans.Development of various risk assessments.Part of the internal audit team in internal audits.Participate as impact assessor in any site’s utilities change control.Report PHP (Pfizer Human performance) utilization monthly.
-
-
Quality operations - Validation & Qualification specialist at Pfizer
-
Sep 2013 - Nov 2014
- Responsible for planning, execution and reporting of validation/qualification/calibration activities:1- Process validation include sampling of validation samples and follow-up of validation samples testing with QC.2- Packaging validation3- HVAC Qualification.4- Purified Water system qualification.5- BMS (Building management system) qualification.6- Equipment qualification.7- Temperature Mapping Activities.8- Development of relevant validation master plans and SOPs.9- Development of validation protocols and reports.10- Development of calibration program, calibration plan and execute/verity/witness calibration activities either internally or through approved vendors.- Participate in deviations investigations- Part of the internal audit team in internal audits
-
-
-
OTSUKA PHARMACEUTICAL S.A.
-
Spain
-
Pharmaceutical Manufacturing
-
100 - 200 Employee
-
Production Sterile LVP Supervisor
-
May 2013 - Aug 2013
- Supervise the subordinate operators during any operation held in sterile large volume parentrals department.- Continous development for local SOPs to be in compliance with global & regulatory standards.- Ensure proper GMP and SOPs implementation.- Suggest any idea concerning process development.- Supervise and control all activities done in Central Dispensing, aseptic processing area and packaging areas.- Distribute the subordinate operators according to the need of work to stick to the production plan.- Monitor production plan execution and ensure that daily targets are met.- Update departement KPIs on daily basis.- Evaluate each subordinate operator attendance and manage their vacations.- Revise all Batch Records before delivery to QA for missing signatures, reconcile yields and justify any out of limits/trends.- Participate in scheduling a monthly plan for requested productivity.- Report any GMP deviation arises at any manufacturing stage during night-shift to QA.
-
-
-
Hikma Pharmaceuticals
-
United Kingdom
-
Pharmaceutical Manufacturing
-
700 & Above Employee
-
Production Specialist
-
Mar 2012 - Apr 2013
- Supervise the subordinate operators during any operation held in liquid department.- Read the SOPs concerning my work, adding suggestions to improve any of them.- Create new SOPs to improve the work and overcome any problem.- Ensure proper GMP and SOPs implementation.- Suggest any idea concerning process development.- Supervise and control all activities done in Central Dispensing, Liquid and Packaging areas (Products, Machinery, and Personnel) during Night Shift.- Distribute the subordinate operators according to the need of work to stick to the production plan.- Try to handle operator's physical and psychological problems to achieve maximum productivity from each, give them moral support and encouragement (a supervisor, 7 foremen and an average of 80 operators distributed between a central dispensing area, a preparation room and 4 packaging lines besides other auxiliary machines and equipment).- Monitor production plan execution and ensure that daily targets are met.- Update Liquid departement KPI on weekly basis.- Evaluate each subordinate operator attendance and manage their vacations.- Ensure that every process preparation is done according to it's PBR.- Revise all Batch Records before delivery to QA for missing signatures, reconcile yields and justify any out of limits/trends.- Participate in scheduling a monthly plan for requested productivity.- Work on SAP® computerized system for process orders confirmation and goods issue/ receipt of BLK, SF and FN orders.- Report to Production Manager the work done in Central Dispensing, Liquid and Packaging areas during night-shift with a report visually aided by timelines.- Report any GMP deviation arises at any manufacturing stage during night-shift to QA.
-
-
-
AIESEC
-
Canada
-
Non-profit Organizations
-
700 & Above Employee
-
OGX member
-
Aug 2010 - Mar 2012
- Held SRBs (student review board) for applicants to choose the best calibers for the exchange process.- Help EPs (exchange participants) to get matched to the project of their choice.- Held cultural orientation session for EPs to increase their awareness for the traditions of the country they are going to visit.- Organize the tasks between our team members to achieve our goals and stick to the plan.- Held a meeting with the EPs after returning from the exchange to evaluate their experience and stand for our strength and weakness points.
-
-
EP (Exchange Participant)
-
Aug 2010 - Sep 2010
- Held presentations at related institutions as nursery academy to increase awarness about prevention and cure from AIDS- Socialize and work with a team of international students.- Visit shelters for patients infected with AIDS.- Work with HIV/AIDS NGOs in organizing charity events for infected patients.- Teach the new interns about the disease and how to perform effective and interesting presentations.- Improving the points of the presentation and activities done within it.- Attend cultural nights in which we present our traditions, folk food and music to other international students.
-
-
-
-
Hospital pharmacist
-
Sep 2011 - Feb 2012
- Dispensing prescription medicines to the public.- Ensuring that different treatments are compatible.- Checking dosage and ensuring that medicines are correctly and safely supplied and labelled.- Liaising with doctors about prescriptions.- Selling over-the-counter (OTC) medicines.- Counseling and advising the public on the treatment of minor ailments.- Advising patients of any adverse side-effects of medicines or potential interactions with other medicines/treatments.- Monitoring blood pressure and cholesterol levels.- Arranging the delivery of prescription medicines to patients.- Overseeing the ordering and safe storage of medical products.- Maintaining computerized records.- Budgeting and financial management.- Attend surgical operations out of my working shifts.- Manage the in-patient and out-patient pharmacy within the night shifts.
-
-
Education
-
Cairo University
Bachelor of Pharmacy (B.Pharm.), Pharmaceutical Sciences -
The American University in Cairo
Business administration diploma, Principles of management -
Tarek Language School
A
Community
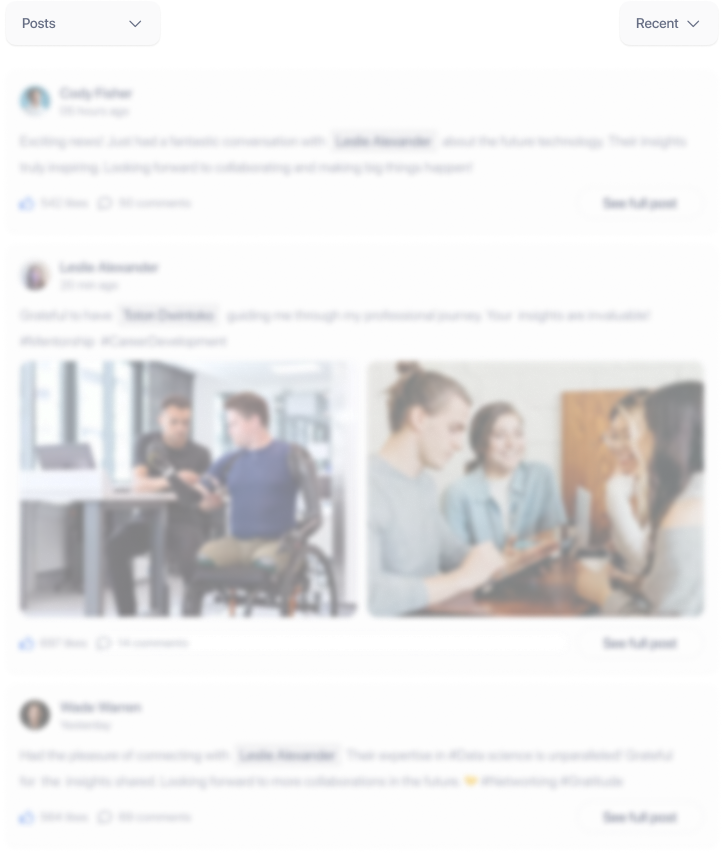