Allen Kuusela
Senior Associate at RQM+- Claim this Profile
Click to upgrade to our gold package
for the full feature experience.
Topline Score
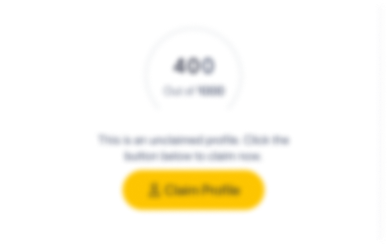
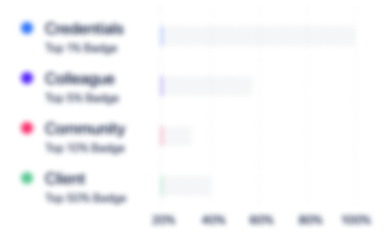
Bio
0
/5.0 / Based on 0 ratingsFilter reviews by:
Experience
-
RQM+
-
United States
-
Business Consulting and Services
-
300 - 400 Employee
-
Senior Associate
-
Sep 2020 - Present
NOTE: In Summer 2020 R&Q Solutions purchased Maetrics (see employer below). I transitioned to the newly named RQM+ in Sep 2020. NOTE: In Summer 2020 R&Q Solutions purchased Maetrics (see employer below). I transitioned to the newly named RQM+ in Sep 2020.
-
-
-
Maetrics
-
United States
-
Business Consulting and Services
-
1 - 100 Employee
-
Senior Associate
-
Oct 2016 - Sep 2020
IN SUMMER 2020, MAETRICS WAS PURCHASED BY/MERGED WITH R&Q SOLUTIONS to become RQM+(above). • • CAPA Consultant to a Medical Device client to evaluate/remediate previously closed CAPAs based upon FDA Audits • Function as CAPA Coordinator for new CAPAs in all phases of Medical Device manufacturing, including performing failure investigations and deviation using FMEA tools, 5-Why’s, fishbone, cause/effect and other tools. • Review QMS documents against MDSAP requirements, identify gaps and remediate. Review quality procedures and revise according to MDSAP requirements. Revise CAPA program, drive all CAPAs to completion. • Developed training plans, provided training for Complaint Handling and Corrective and Preventive Actions (CAPAs). • Performed Quality Management System (QMS) audits for Medical Device companies in US, Canada, Australia & Puerto Rico. • Performed Vendor/Supplier audits in US, Canada & Puerto Rico for global Pharmaceutical client. • Developed QMS for pharmaceuticals for a combination Device/Drug Product manufacturer. • Function as client’s “Quality In Plant” at their API manufacturer. • Review/certify Batch Production Records for Peptide API manufacturing. • Provide review, and client approval, for deviations, change controls, CAPA, and Data Integrity verification. • Train API Manufacturer’s staff in how to write effective Deviations and CAPAs.
-
-
-
-
Validation/Regulatory Professional
-
2007 - Oct 2016
• Provide regulatory compliance, Quality Assurance, validation project management, auditing, & consulting service to clients including Regeneron, Cardinal Health, Stryker/Olympus Biotech, Compli LLC, R. Donnelly & Associates, VTS Consultants, Inc., Biosan, Akorn Inc., AppTec, Sharp Corp., Intracom LLC, Integrated Project Services (IPS), Validation Inc., Validation Plus, Inc. (VPI), Virbac Animal Health, Xellia Pharmaceuticals, and NNE Pharmaplan. • Responsible for remediating deviations, CAPA’s and NOE’s, and for aseptic process failure investigations. • Liaise with client QA Director to ensure project quality needs are met in consent decree remediation. Ensure adherence to Quality Management System. • As Project Quality Manager, review & approve SOP’s, FAT/SAT’s, URS’s, Validation protocols, etc. • Develop/execute FAT, SAT, CQV protocols (Commissioning, IQ, OQ & PQ) for vast array of pharmaceutical/ biotechnological manufacturing equipment, support equipment and utilities, SIP validation of Bioreactor vessels & other biological systems, and cleaning validation/clean hold studies; with summary report preparation. • Develop Periodic Qualification Assessments, Continuing Validation Assessments, and Part-11/Annex 11 Assessments for all automated manufacturing and laboratory equipment and utilities. • Provide Validation and CIP/SIP Engineering services in start-up biologics facility; performing both CIP and SIP cycles using Delta V, including troubleshooting, fine-tuning and documenting cycles. • Perform vendor audits, and GMP / Validation audits. • Review/approve equipment validation protocols, cleaning validation protocols, completed validation packages and Manufacturing/Batch Records for content and Good Documentation Practices.
-
-
-
Xellia Pharmaceuticals
-
Denmark
-
Pharmaceutical Manufacturing
-
700 & Above Employee
-
Quality Project Manager - Site
-
Mar 2016 - Jul 2016
• As Project Quality Manager, review & approve all documents, i.e., SOP’s, FAT/SAT’s, URS’s, FDS's, Validation protocols, Deviations, CAPA's and more. • Liaison with client QA Director to ensure project quality needs are met in consent decree remediation. • Ensure adherence to Quality Management System. • As Project Quality Manager, review & approve all documents, i.e., SOP’s, FAT/SAT’s, URS’s, FDS's, Validation protocols, Deviations, CAPA's and more. • Liaison with client QA Director to ensure project quality needs are met in consent decree remediation. • Ensure adherence to Quality Management System.
-
-
-
-
Consultant / Project Quality Manager
-
Jun 2015 - Jul 2016
- As Project Quality Manager, review & approve all documents, i.e., SOP’s, FAT/SAT’s, URS’s, FDS's, Validation protocols, Deviations, CAPA's, and more. Liaison with client QA Director to ensure project quality needs are met in consent decree remediation. Ensure adherence to Quality Management System. - Revise existing manufacturing batch records for Animal Health manufacturing client, and develop new batch records in granulation, blending, final blending, tabletting, and packaging for solid dose, liquid fill, cream fill and extrusion products.
-
-
-
Quality Compliance Partners
-
United States
-
Pharmaceutical Manufacturing
-
1 - 100 Employee
-
Quality Compliance Consultant
-
Sep 2013 - May 2015
• Provide regulatory compliance consulting, and auditing to clients including Parexel and Sanofi-Pasteur Ltd. • Responsible for vaccine manufacturing batch record certification to allow clients with an FDA hold on product release, to release product. Write narratives/summaries for quality data reviews. • Responsible for deviation and CAPA investigation and remediation; and aseptic process failure investigations. • Performing environmental monitoring trend analyses, and reviewing/approving environmental sampling results. • Performing License Conformance verification to ensure vaccine drug licenses and submittals to FDA and European agencies are consistent with internal Batch Production Records and procedures. Performing gap analyses, providing updates to client to assist them in meeting regulatory commitments.
-
-
-
PAREXEL
-
United States
-
Pharmaceutical Manufacturing
-
700 & Above Employee
-
Quality Compliance Consultant
-
Sep 2013 - May 2015
• Provide regulatory compliance consulting, and auditing to clients including Parexel and Sanofi-Pasteur Ltd. • Responsible for vaccine manufacturing batch record certification to allow clients with an FDA hold on product release, to release product. Write narratives/summaries for quality data reviews. • Responsible for deviation and CAPA investigation and remediation; and aseptic process failure investigations. • Performing environmental monitoring trend analyses, and reviewing/approving environmental sampling results. • Performing License Conformance verification to ensure vaccine drug licenses and submittals to FDA and European agencies are consistent with internal Batch Production Records and procedures. Performing gap analyses, providing updates to client to assist them in meeting regulatory commitments.
-
-
-
Sanofi Pasteur Ltd.
-
China
-
Personal Care Product Manufacturing
-
1 - 100 Employee
-
Quality Compliance Consultant
-
Sep 2013 - May 2015
• Provide regulatory compliance consulting, and auditing to clients including Parexel and Sanofi-Pasteur Ltd. • Responsible for vaccine manufacturing batch record certification to allow clients with an FDA hold on product release, to release product. Write narratives/summaries for quality data reviews. • Responsible for deviation and CAPA investigation and remediation; and aseptic process failure investigations. • Performing environmental monitoring trend analyses, and reviewing/approving environmental sampling results. • Performing License Conformance verification to ensure vaccine drug licenses and submittals to FDA and European agencies are consistent with internal Batch Production Records and procedures. Performing gap analyses, providing updates to client to assist them in meeting regulatory commitments.
-
-
-
Regeneron
-
United States
-
Biotechnology
-
700 & Above Employee
-
Validation Consultant
-
Jun 2011 - Sep 2013
Develop/Execute validation protocols (IQ, OQ, PQ) for three automated CIP systems, WFI stills, purification/chromatography systems, Perform SIP validation of BioReactors and other process vessels and transfer lines. Execute OQ protocol for manufacturing area Data Historian. Perform CIP Clean Hold studies. Develop Periodic Evaluation Reports, Continuing Qualification Assessments, Equipment Qualification Assessments, System Impact Assessments and Part 11/Annex 11 Assessments for automated manufacturing and lab equipment, and utilities.
-
-
-
Bristol-Myers Squibb
-
United States
-
Pharmaceutical Manufacturing
-
1 - 100 Employee
-
Validation Consultant
-
Oct 2009 - Apr 2010
Provide Validation and CIP/SIP Engineering services in start-up biologics facility; performing both CIP and SIP cycles using Delta V, including troubleshooting, fine-tuning and documenting cycles. Provide Validation and CIP/SIP Engineering services in start-up biologics facility; performing both CIP and SIP cycles using Delta V, including troubleshooting, fine-tuning and documenting cycles.
-
-
-
Validation, Inc.
-
United States
-
Pharmaceutical Manufacturing
-
1 - 100 Employee
-
Senior Validation Engineer
-
Dec 2009 - Mar 2010
Provide Validation and CIP/SIP Engineering services in start-up biologics facility; performing both CIP and SIP cycles using Delta V, including troubleshooting, fine-tuning and documenting cycles. Provide Validation and CIP/SIP Engineering services in start-up biologics facility; performing both CIP and SIP cycles using Delta V, including troubleshooting, fine-tuning and documenting cycles.
-
-
-
-
Validation Consultant
-
2009 - 2010
Develop/execute Commissioning and validation protocols (IQ, OQ & PQ) for autoclaves, fillers, sterilizing ovens & tunnels, WFI system, CTU thermal studies, USP Purified Water systems, Clean Steam systems, Building Management System, laboratory equipment, clean steam; with summary report preparation. Develop/execute Commissioning and validation protocols (IQ, OQ & PQ) for autoclaves, fillers, sterilizing ovens & tunnels, WFI system, CTU thermal studies, USP Purified Water systems, Clean Steam systems, Building Management System, laboratory equipment, clean steam; with summary report preparation.
-
-
-
Compli LLC
-
United States
-
Software Development
-
Senior Validation Consultant
-
Dec 2008 - Dec 2009
• Provide regulatory compliance & validation consulting to clients including Ben Venue Labs/Boehringer-Ingelheim, Sharp Corp., Pfizer Animal Health, Leiner Health Products, Adhesives Research, Inc., AppTec, Inc., INO Therapeutics/Ikaria, more. • Review/approve aseptic processing equipment validation protocols, cleaning validation protocols, aseptic processing, completed validation packages and Manufacturing/Batch Records for content and Good Documentation Practices. • Develop/execute Factory Acceptance Test (FAT), CQV protocols (Commissioning, IQ, OQ & PQ) for a packaging, sterilizing and manufacturing equipment with summary report preparation. • Develop/execute CQV protocols (Commissioning, IQ, OQ & PQ) for autoclaves, depyrogenation ovens, isolators, lyophilizers, CTU’s, MF/UF systems; ultrasonic washers, compressed gases, medical gas manufacturing systems, and cleaning validation cycle development; with summary report preparation. • Execute IQ, OQ & PQ protocols for solid dosage packaging lines including tablet fillers, cottoners, induction heat sealers and heat tunnels, cappers, labelers, vision systems, cartoners, overwrappers, and blister packaging systems. • Perform vendor audits, and GMP audits, as well as providing validation, cGMP and GDP training to clients.
-
-
-
-
Validation Consultant
-
Dec 2008 - Aug 2009
Develop/execute Factory Acceptance Test (FAT), commissioning & validation protocols (IQ, OQ & PQ) for a Nikka Densok high voltage vial inspection system, an ICOS Terminal Sterilization system; Newman Labelers and other pharmaceutical packaging equipment, Shrinkwrap system, with summary report preparation. Develop/execute Factory Acceptance Test (FAT), commissioning & validation protocols (IQ, OQ & PQ) for a Nikka Densok high voltage vial inspection system, an ICOS Terminal Sterilization system; Newman Labelers and other pharmaceutical packaging equipment, Shrinkwrap system, with summary report preparation.
-
-
-
-
Validation Consultant
-
2009 - 2009
Developed/executed IQ, OQ and PQ validation protcols at FDA's Rockville testing facility for lyophilizers, autoclaves, biosafety cabinets, incubators, refrigerators. Revised facility validation master plan. Developed/executed IQ, OQ and PQ validation protcols at FDA's Rockville testing facility for lyophilizers, autoclaves, biosafety cabinets, incubators, refrigerators. Revised facility validation master plan.
-
-
-
Ikaria
-
United States
-
Wellness and Fitness Services
-
1 - 100 Employee
-
Validation Consultant
-
2007 - 2009
Develop/execute FAT and validation protocols (IQ, OQ & PQ) for a start-up medical gas production facility, with summary reports. preparation. Systems included the Compressor and Fill Manifold systems, Reactor/Scrubber system, Vacuum system, Cylinder inverters, shrink wrap systems, blowdown/bakeout systems, and the automated control system. Develop/execute FAT and validation protocols (IQ, OQ & PQ) for a start-up medical gas production facility, with summary reports. preparation. Systems included the Compressor and Fill Manifold systems, Reactor/Scrubber system, Vacuum system, Cylinder inverters, shrink wrap systems, blowdown/bakeout systems, and the automated control system.
-
-
-
Siemens Healthcare
-
Italy
-
Medical Device
-
1 - 100 Employee
-
Validation Consultant
-
May 2008 - Dec 2008
Developed Process Validation protocols for the production of wetcake and reagents using an automated Buffer/Dilution system. Developed Performance Qualification Test Plan for facility CIP System Developed Process Validation protocols for the production of wetcake and reagents using an automated Buffer/Dilution system. Developed Performance Qualification Test Plan for facility CIP System
-
-
-
Compli, LLC
-
United States
-
Pharmaceutical Manufacturing
-
1 - 100 Employee
-
Senior Validation Consultant,
-
Feb 2006 - May 2008
Provide regulatory compliance, auditing, Quality Assurance, validation project management and consulting service to clients including Regeneron, Cardinal Health, Stryker Biotech, R. Donnelly & Associates, VTS Consultants, Inc., Biosan, Akorn Inc., AppTec, Sharp Corp., Intracom LLC, Integrated Project Services (IPS), Validation Inc., and Validation Plus, Inc. (VPI). Develop/execute FAT, commissioning and validation protocols (IQ, OQ & PQ) for autoclaves, fillers, cappers, vial washers, stopper processors, sterilizing ovens & tunnels, CIP Systems, WFI Stills, CTU thermal studies, USP Purified Water systems, Clean Steam systems, Building Management System, Microfiltration systems; laboratory equipment, packaging lines, aseptic isolators, vial and powder filling lines, controlled temperature units, compressed gas, clean steam, and cleaning validation/clean hold studies; with summary report preparation. Provide Validation and CIP/SIP Engineering services in start-up biologics facility; performing both CIP and SIP cycles using Delta V, including troubleshooting, fine-tuning and documenting cycles. Perform vendor audits, and GMP / Validation audits. Review and approve equipment validation protocols, cleaning validation protocols and completed validation packages.
-
-
-
cGMP Validation
-
United States
-
Pharmaceutical Manufacturing
-
1 - 100 Employee
-
Director
-
2008 - 2008
• Directed validation activities for projects in the New England region. • Provide regulatory compliance and validation consulting service to pharmaceutical, biological and medical device clients including Siemens Healthcare Diagnostics, FDA (CBER), Medimmune, and others. • Developed Process Validation protocols for the production of wetcake and reagents using an automated Buffer/Dilution system. • Developed Performance Qualification Test Plan for facility CIP System. • Responsible for Business development in New England and other areas, to include proposals and presentations. • Perform vendor audits, and GMP / Validation audits.
-
-
-
MedImmune
-
United States
-
Biotechnology Research
-
700 & Above Employee
-
Validation Consultant
-
2008 - 2008
-
-
-
-
Validation Consultant
-
2007 - 2008
Develop/execute FAT and validation protocols (IQ, OQ & PQ) for a start-up medical gas production facility, with summary reports. preparation. Systems included the Compressor and Fill Manifold systems, Reactor/Scrubber system, Vacuum system, Cylinder inverters, shrink wrap systems, blowdown/bakeout systems, and the automated control system. Develop/execute FAT and validation protocols (IQ, OQ & PQ) for a start-up medical gas production facility, with summary reports. preparation. Systems included the Compressor and Fill Manifold systems, Reactor/Scrubber system, Vacuum system, Cylinder inverters, shrink wrap systems, blowdown/bakeout systems, and the automated control system.
-
-
-
-
Validation Consultant
-
2006 - 2007
Develop/execute commissioning and validation protocols (IQ, OQ & PQ) for autoclaves, depyrogenation ovens, lyophilizers, CTU’s, MF/UF systems; ultrasonic washers, ; with summary report preparation. Develop/execute commissioning and validation protocols (IQ, OQ & PQ) for autoclaves, depyrogenation ovens, lyophilizers, CTU’s, MF/UF systems; ultrasonic washers, ; with summary report preparation.
-
-
-
Adhesives Research, Inc.
-
United States
-
Chemical Manufacturing
-
100 - 200 Employee
-
Validation Consultant
-
2006 - 2006
Developed Commissioning, and Installation/Operational Qualification Protocols for Intermediate Bulk Tanks, Compressed Air system, HVAC, and Spray Coater in a facility that manufactured dissolvable, medicated strips. Developed Commissioning, and Installation/Operational Qualification Protocols for Intermediate Bulk Tanks, Compressed Air system, HVAC, and Spray Coater in a facility that manufactured dissolvable, medicated strips.
-
-
-
AppTec
-
Chile
-
IT Services and IT Consulting
-
1 - 100 Employee
-
Validation Consultant
-
2005 - 2006
Develop and execute IQ and OQ protocols for Enguard Aseptic Isolator. Develop and execute IQ and OQ protocols for Enguard Aseptic Isolator.
-
-
-
Sharp
-
Japan
-
Consumer Electronics
-
200 - 300 Employee
-
Validation Consultant
-
2001 - 2006
Developed IQ, OQ & PQ protocols for automated manufacturing and packaging equipment. Developed IQ, OQ & PQ protocols for automated manufacturing and packaging equipment.
-
-
-
-
Cleaning Validation Consultant
-
Dec 2004 - May 2005
Performed audit of facility, particularly regarding cleaning validation, developed audit report. Developed Cleaning Validation Master Plan for facility with emphasis on chromatography resin and buffer tanks. Performed audit of facility, particularly regarding cleaning validation, developed audit report. Developed Cleaning Validation Master Plan for facility with emphasis on chromatography resin and buffer tanks.
-
-
-
VTS Consultants
-
United States
-
Pharmaceutical Manufacturing
-
1 - 100 Employee
-
Director
-
Aug 2001 - Apr 2005
• Directed validation activities for projects in US and Puerto Rico. • Performed quality, regulatory & cleaning validation audits, cGMP compliance inspections, vendor audits, quality audits, and validation consulting to pharmaceutical, biological, and medical device manufacturing clients in Puerto Rico and US, including Eli Lilly, Pharmacia, Alkermes, TEI Biosciences, Biosan, Applied Biosystems, Schering Plough LPO, RP Scherer North America, Bausch & Lomb, and others. • Performed as Quality-Over-Validation in Start-Up of new Biologics facility, reviewing/approving validation protocols and reports. • Functioned as 3rd Party oversight in new Biologics facility in remediating 600+ deviations including CAPAs/NOEs. • Developed Facilities Validation, and Cleaning Validation, Master Plans. • Developed IQ, OQ & PQ SAT protocols for automated USP Purified Water systems, manufacturing and packaging equipment (parenteral, solid dosage, biologics), isolators, an automated conveyor and inspections system, and for QC Microbiology and Analytical Chemistry Laboratory equipment. • Wrote Periodic Qualification Evaluations (PQEs) for Freeze Dryers, aseptic Filling Lines, and Utilities. • Performed CIP and SIP studies of Bio-Reactors, Media & Buffer tanks, and chromatography resin tanks. • Review/approve equipment validation protocols, cleaning validation protocols, completed validation packages and Manufacturing/Batch Records for content and Good Documentation Practices. • Responsible for Business development in Northeastern US to include proposals and presentations.
-
-
-
-
Validation Consultant
-
2005 - 2005
Develop/execute validation protocols (IQ, OQ & PQ) for autoclaves, fillers, cappers, vial washers, stopper processors, sterilizing ovens; with summary report preparation. Develop/execute validation protocols (IQ, OQ & PQ) for autoclaves, fillers, cappers, vial washers, stopper processors, sterilizing ovens; with summary report preparation.
-
-
-
-
Validation Consultant - Cleaning Validation
-
2004 - 2005
Developed validation protocols for sanitization of bioreactors, in both empty and half-full state for nutraceutical facility. Developed validation protocols for sanitization of bioreactors, in both empty and half-full state for nutraceutical facility.
-
-
-
-
Validation Consultant
-
Mar 2002 - Jun 2002
Developed Installation and Operational Qualification of the WW Sampling Booth & Conveyor System installed in the warehouse area of the St Petersburg, FL facility. Developed Installation and Operational Qualification of the WW Sampling Booth & Conveyor System installed in the warehouse area of the St Petersburg, FL facility.
-
-
-
TEI Biosciences Inc.
-
Medical Device
-
1 - 100 Employee
-
Validation Consultant
-
Mar 2002 - Apr 2002
Developed IQ and OQ protocols for automated laboratory instrumentation including Perkin-Elmer Differential Scanning Calorimeter, and others. Developed IQ and OQ protocols for automated laboratory instrumentation including Perkin-Elmer Differential Scanning Calorimeter, and others.
-
-
-
Schering-Plough Pharmaceuticals
-
IT Services and IT Consulting
-
1 - 100 Employee
-
Validation Consultant/Project Manager
-
Apr 2000 - Aug 2001
Project Manager for two major validation projects at Las Piedras and Manati, Puerto Rico in consent decree remediations. Review and approved validation protocols and completed validation packages. Consent decree remediation. Oversee up to 20 validation staff. Project Manager for two major validation projects at Las Piedras and Manati, Puerto Rico in consent decree remediations. Review and approved validation protocols and completed validation packages. Consent decree remediation. Oversee up to 20 validation staff.
-
-
-
The Validation Group
-
United States
-
Regional Manager - Puerto Rico
-
Mar 1997 - Aug 2001
• Provided Validation Consulting and Project Management services to pharmaceutical and medical device clients, including, MOVA Pharmaceuticals; Dupont Pharma; Ares Serono, Schering Plough Products; Schering Plough LPO; SmithKline Beecham; Eli Lilly del Caribe; St. Jude Medical; Merck, Sharpe & Dohme; and others. • Provided technical, quality and regulatory expertise, and auditing functions to clients. • Perform vendor audits, and GMP audits. • Provided cGMP training to staff and clients. • Performing aseptic process failure investigations in both pharmaceutical and biologics manufacturing. • Worked with aseptic manufacturing clients under FDA Consent Decree to bring them into compliance. • Responsible for remediating deviations, including review of CAPA’s, NCR’s and NOE’s. • Oversaw all projects in Puerto Rico, including managing up to 15 Puerto Rican staff as well as stateside personnel assigned to projects, including direct project management of three multi-million dollar projects. • Involved in the validation of a start-up biotechnology facility. • Developed Facilities Validation, Computer Validation and Cleaning Validation Master Plans. • Developed/executed protocols for automated tablet press, autoclaves, bioreactors, fermentors, dry heat ovens, IR tunnels, filling/capping machines, lyophilizers, packaging lines, aseptic processes, CIP, SIP and temperature mapping and more; developed validation reports. • Developed Design Controls for medical (cardiac) devices. • Review/approve equipment validation protocols, cleaning validation protocols, completed validation packages and Manufacturing/Batch Records for content and Good Documentation Practices. • Responsible for Business development in Puerto Rico. Developed new business for TVG-PR; grew headcount in region by 260% in three years.
-
-
-
St Jude Medical
-
United States
-
Medical Equipment Manufacturing
-
700 & Above Employee
-
Validation Consultant
-
1997 - 2001
Performed Validation audit. Developed Design Controls for cardiac devices in a medical device facility. Developed Cleaning Validation protocols. Performed Validation audit. Developed Design Controls for cardiac devices in a medical device facility. Developed Cleaning Validation protocols.
-
-
-
ValSource, LLC
-
United States
-
1 - 100 Employee
-
Validation Specialist/Project Manager
-
1996 - 1997
• Provided validation and regulatory input to project core teams, management steering committees and validation staff in a start-up biotechnology manufacturing facility. • Reviewed Validation Master Plans, Automation Quality Assurance Plans, IQ, OQ & PQ protocols and reports. • Provided validation and regulatory input to project core teams, management steering committees and validation staff in a start-up biotechnology manufacturing facility. • Reviewed Validation Master Plans, Automation Quality Assurance Plans, IQ, OQ & PQ protocols and reports. • Reviewed Functional Requirement Specifications, Factory Acceptance Test procedures, Software Detailed Design Specifications and Software Test Plans for automated systems. • Developed facilities Validation Master Plan. • Developed IOQ and PQ protocols for Water For Injection and Purified Water Systems, and Autoclaves.
-
-
-
-
Validation Consultant
-
1995 - 1997
As a Project Manager, provided validation and regulatory input to project core teams, management steering committees and validation staff in a start-up biotechnology manufacturing facility. Reviewed Validation Master Plans, Automation Quality Assurance Plans, IQ, OQ & PQ protocols and reports. Reviewed Functional Requirement Specifications, Factory Acceptance Test procedures, Software Detailed Design Specifications and Software Test Plans for automated systems. Review and approve equipment validation protocols, cleaning validation protocols and completed validation packages. Develop/Execute validation protocols (IQ, OQ, PQ) for CIP systems, Biowaste system, WFI stills, purification/chromatography systems, UF/DF systems,
-
-
-
-
Validation Project Manager
-
1995 - 1997
• Provided validation and regulatory input to project core teams, management steering committees and validation staff in a start-up biotechnology manufacturing facility. • Reviewed Validation Master Plans, Automation Quality Assurance Plans, IQ, OQ & PQ protocols and reports. • Reviewed Functional Requirement Specifications, Factory Acceptance Test procedures, Software Detailed Design Specifications and Software Test Plans for automated systems. • Developed facilities Validation Master Plan.
-
-
-
-
Validation Scientist
-
1995 - 1996
Responsible for developing cleaning validation master plan for Mayaguez facility encompassing all business units, including oncologics, steroidal and non-steroidal pharmaceuticals in solid dosage, liquid dose, parenterals and powder-filled products. Performed CIP of tanks and reactor vessels, and a non-liquid CIP of a dry-powder manufacturing system. Responsible for Equipment and Process change controls. Responsible for development of Performance Qualification protocols and reports.
-
-
-
SmithKline Beecham
-
United Kingdom
-
Financial Services
-
Validation Engineer
-
Apr 1992 - Oct 1995
Responsible for design and implementation of validation programs for Biopharmaceutical Manufacturing Facilities. Performed CIP and SIP studies of Bio-Bioreactors, Media & Buffer tanks; and CIP of chromatography skids, and thermal studies for autoclaves, and temperature controlled units.. Responsible for development, review & approval of validation procedures; evaluating test results, and final reports. Monitored validation control programs to ensure that process, process control, and utility systems maintain validated status, including maintenance of validation and engineering change control programs. Interfaced with QA, QC, Manufacturing, Engineering and Maintenance with respect to validation activities. Responsible for ensuring validation programs are conducted appropriately, within established budgets and schedules. Developed Cleaning Validation Strategy and Protocols for Biologics. Developed Computer Validation Master Plan. Performed as member of SmithKline Beecham Corporate Validation Task Force incorporating sites in US, UK and Puerto Rico. Supervised contract validation staff.
-
-
-
-
Validation Specialist
-
1989 - 1992
• Developed IQ, OQ & PQ Protocols for Client's Validation Projects for equipment to include tanks, Bioreactors, purification equipment, glassware washers, autoclaves, depyrogenation ovens, LN2 freezers, warm/cold rooms, refrigerators/freezers, blenders & granulation equipment, PW/WFI systems, Clean/Plant steam systems, glycol chiller, packaging equipment. • Validated a liquid filling line (IQ/OQ/PQ) including internal and external vial washers, IR tunnel, filler, capper, inspection machines, label printer and trayloaders. • Responsible for execution of IQ, OQ and PQ Protocols, including the performance of thermal validation studies; air, compressed gas, water, clean steam, and environmental sampling. • Performed CIP’s and SIP’s for Bioreactors, Media & Buffer tanks, Purified Water & WFI tanks & distribution loops, and more. • Developed Standard Operating Procedures for Client's Systems, Processes and Utilities. • Interacted with System Operators, Engineers, QC, and QA Personnel on a daily basis in Client's facilities (Ortho Biologics, Manati, PR; Lederle Parenterals, Carolina, PR; Eli Lilly & Co., Indianapolis, IN). • Involved in the validation of a start-up biotechnology facility from ground breaking to validation. • Compiled Validation Test and QC Assay results and developed reports for Client's submission to the FDA. • Responsible for training other Validation staff in Current Good Manufacturing Practices (cGMP's).
-
-
-
-
Validation Consultant / Team Lead
-
Jun 1990 - Nov 1990
Validated a liquid filling line (IQ/OQ/PQ) including internal and external vial washers, IR depyrogenation tunnel, filler, capper, inspection machines, label printer and tray loaders. Validated a liquid filling line (IQ/OQ/PQ) including internal and external vial washers, IR depyrogenation tunnel, filler, capper, inspection machines, label printer and tray loaders.
-
-
-
Ortho Biotech
-
Pharmaceutical Manufacturing
-
1 - 100 Employee
-
Validation Consultant
-
Oct 1989 - Jun 1990
In a start-up Biotech manufacturing facility, developed IQ, OQ & PQ Protocols for equipment to include tanks, Bioreactors, purification equipment, glassware washers, autoclaves, depyrogenation ovens, LN2 freezers, warm/cold rooms, refrigerators/freezers, blenders & granulation equipment, PW/WFI systems, Clean/Plant steam systems, glycol chiller, packaging equipment. Responsible for execution of IQ, OQ and PQ Protocols, including the performance of thermal validation studies; air, compressed gas, water, clean steam, and environmental sampling. Performed CIP’s and SIP’s for Bioreactors, Media & Buffer tanks, Purified Water & WFI tanks & distribution loops, and more. Developed Standard Operating Procedures for Client's Systems, Processes and Utilities.
-
-
-
Verax Corporation
-
United States
-
Printing Services
-
Microbiology Lab Manager, QC Micro Lab Tech, Production Shift Supervisor
-
Apr 1985 - Oct 1989
3 Postions Held:Microbiology Lab Supervisor (1988-1989) During start-up of Verax's GMP Bio-processing facility, responsibilities included:• Performing as a member of the Verax Validation Task Force.• Specifying and purchasing equipment & materials for microbiology, analytical chemistry and metrology laboratories.• Preparing schedules for in-process and final release assay and QC testing.• Developing protocols for the bio-pharmaceutical production operation. • Perform audits of vendors and testing agencies.• Providing cGMP training to staff.Quality Control/Microbiology Lab Technician (1987-1988)• Performed Endotoxin (LAL) and Sterility testing per USP and 21 CFR on daily in-process and final product samples.• Performed initial and routine Environmental testing of clean rooms, water, gasses, as well as biological indicator testing.• Performed Sterility, Shrinkage, Collagen, LOD, and Destructive testing on Verax Microspheres.• Performed microbial identification testing.• Wrote SOP’s for QC-Microbiology laboratory. Production Shift Supervisor (1985-1987)• Responsible for supervising and training up to eight technicians on rotating shifts in a biological Research & Development / Contract Manufacturing facility.• Responsible for technology transfer assignments in client facilities, with regard to Verax’ System 2000™ bio-reactors.• Operated and troubleshot a Verax Pilot Plant containing mammalian cell bio-reactors including CIP and SIP.• Operated Microfiltration and Ultrafiltration skids to purify mammalian cell products.• Responsible for writing SOP's, training operators, and for performing Cell Culture/Medium Optimization research and Toxicity Testing.• Responsible for writing and reviewing production batch records.
-
-
Microbiology Lab Supervisor
-
1987 - 1989
During start-up of Verax's GMP Bio-processing facility, responsibilities included:• Performing as a member of the Verax Validation Task Force.• Specifying and purchasing equipment & materials for microbiology, analytical chemistry and metrology laboratories.• Preparing schedules for in-process and final release assay and QC testing.• Developing protocols for the bio-pharmaceutical production operation. • Perform audits of vendors and testing agencies.• Providing cGMP training to staff.
-
-
Production shift supervisor
-
1985 - 1987
Responsible for supervising and training up to eight technicians on rotating shifts in a biological Research & Development / Contract Manufacturing facility.Responsible for technology transfer assignments in client facilities, with regard to Verax’ System 2000™ bio-reactors.Operated and troubleshot a Verax Pilot Plant containing mammalian cell bio-reactors including CIP and SIP.Developed Batch records. Review/approve completed batch records.Operated Microfiltration and Ultrafiltration skids to purify mammalian cell products.Responsible for writing SOP's, and performing Cell Culture/Medium Optimization research and Toxicity Testing.
-
-
Education
-
Keene State College
BS, Bio-Chem -
Bellows Falls Union High School
Diploma, General Studies
Community
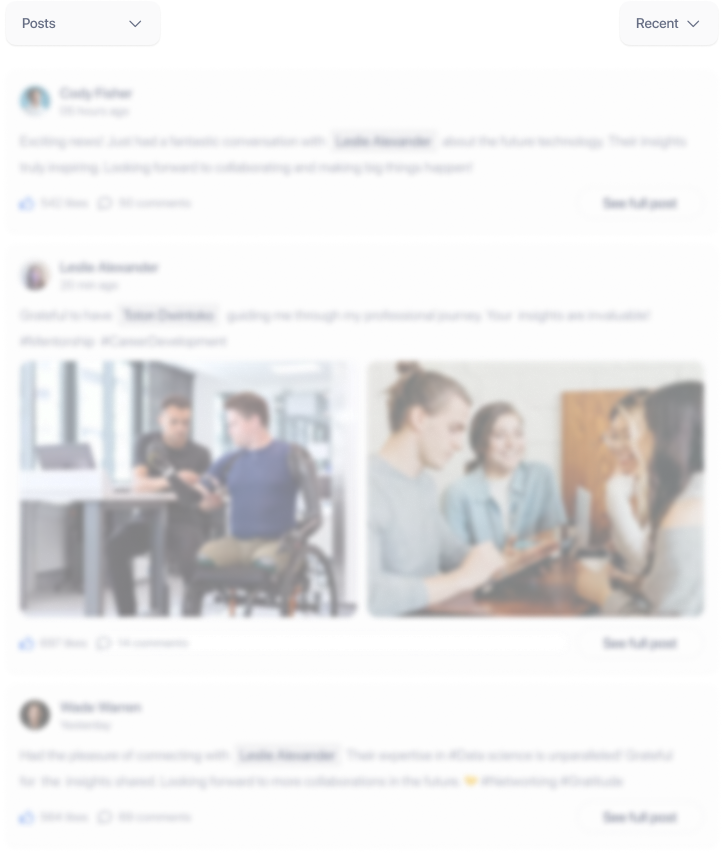