Allan Pichler
Military Operations Center Product Support Specialist at TRAINCROFT, INC.- Claim this Profile
Click to upgrade to our gold package
for the full feature experience.
Topline Score
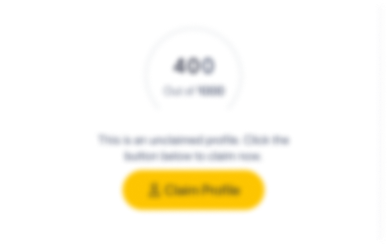
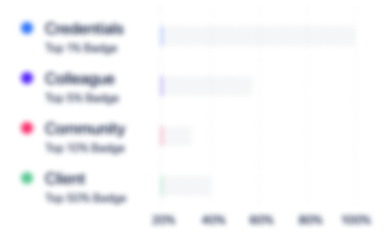
Bio


Experience
-
TRAINCROFT, INC.
-
Professional Training and Coaching
-
1 - 100 Employee
-
Military Operations Center Product Support Specialist
-
Aug 2021 - Present
-
-
-
Air Transport International, Inc.
-
United States
-
Aviation and Aerospace Component Manufacturing
-
500 - 600 Employee
-
Reliability Analyst
-
Apr 2021 - Aug 2021
ETOPS Reporting ETOPS Reporting
-
-
-
PSA Airlines, Inc.
-
United States
-
Airlines and Aviation
-
700 & Above Employee
-
Reliability Analyst
-
Jul 2016 - Oct 2020
Laid-off due to outsource reduction by PSA Complied data on aircraft delays, cancellations, and components, analyzed and evaluated performance for unsatisfactory trends or conditions. Provided corrective action proposals to maintenance programs in response to alerts and trends, contributing to an overall on time departure rate of 97.4 percent. Maintained the delay and cancellations spreadsheet the monthly reliability report, provided data to the FAA Reviewed Service Bulletins, generated cost proposals, and supplied recommendations to management. Show less
-
-
-
Belcan
-
United States
-
Information Technology & Services
-
700 & Above Employee
-
Compliance Engineer
-
Sep 2015 - Jan 2016
Laid-off due to outsource reduction by GE,Researched, identified, and verified hazardous materials for compliance for Registration, Evaluation, Authorization, and Restriction of Chemicals (REACH) and The European Chemicals Agency (ECHA) on Aero-derivative turbine components. Updated GE Marine and Industrial Engine manuals to incorporate hardware changes affected by new laws imposed by REACH and ECHA. Incorporation of this information helped GE meet its obligations on time and under budget.Generated conformity documentation designating the use/location of components containing hazardous materials/coatings for GE engines currently in service, thus meeting the governmental reporting requirements. Show less
-
-
Diagnostic Engineer group leader
-
Jul 2009 - Sep 2015
Managed team of 26 personnel, for 24 x 7 operations, $1.7 million yearly contract. Improved operational processes increasing alert completion by 20 percent with increased accuracy.
-
-
Engine Support Technician
-
Jul 2004 - Jul 2009
Performed diagnostic analysis, to identify performance and failure trends on GE engines. Provide worldwide customer technical repair and troubleshooting support. Assisted GE engineers in analyzing potential root cause analysis and developed improvement actions for engine faults and exceedances.
-
-
-
United States Air Force
-
United States
-
Defense and Space Manufacturing
-
700 & Above Employee
-
Ohio Reserve Maintenance Advisor
-
Mar 2001 - Mar 2004
Advised Air Force Reserve (AFR) unit directors on proficiency, readiness and welfare for eight Aircraft Battle Damage Repair (ABDR) Teams to ensure members were fully trained and ready for their duty requirements.Led quality reviews, squadron inspections, strategic/tactical planning, self-assessment inspections, and ABDR training for eight teams.Advised on unit programs and processes, identified compliance deficiencies, increasing evaluation pass ratings by 35%.Provided recommendations for process improvements to maintain a high level of readiness for the USAF Show less
-
-
Assistant Aircraft Maintenance Superintendent
-
Jul 2000 - Feb 2001
Managed a 65-person depot maintenance section for F-16/F-117A/A10 crash damage and ABDR repairPrepared daily briefings, scheduled work assignments, wrote operational policies/processes, created monthly history reports, and organized deployment field teams.Completed the section’s personnel performance reports on time and correctlySkilled in preparing cost estimates on all aspects of the teams duties and requirements ensuring section stayed under budget at all times Managed personnel availability while ensuring their training, both operational and safety training, was completed on time and to the highest standards ensuring the teams readiness and for the field Show less
-
-
Superintendent Aircraft Production Scheduling
-
Jun 1996 - Jul 2000
Developed, implemented, and managed a brand new production scheduling program on time and under budget.Authored all governing policy and operating documents used for properly utilizing the new production scheduling system. Coordinated depot maintenance, tracked man-hour expenditures, and engineering modification requests to ensure tasks were completed on time and under budgetResearched time compliance technical orders (TCTOs) and modification kits, for availability through supply and item/equipment managers to ensure section was always prepared.Managed production work control documents, blueprints, tooling and parts inventory for shipment as needed to meet the USAF requirements. Monitored time change items, updated aircraft configurations using the REMIS system. Input TCTO information, part /serial number changes. Conducted work control document maintenance record reviews and maintained aircraft historical documents. Coordinated aircraft functional check flights.Led 5-man maintenance team to deliver six F-16A aircraft to the Royal Jordanian Air Force for a special assignment which resulted in a service medal and accommodation for outstanding work and preparedness. During this operation supervised/ coordinated transient maintenance requirements while managing logistical movement of aircraft, personnel and equipment as neededEstablished cost estimates and transition flow plans for a 39 Million dollar regeneration project of twenty eight F-16A/B aircraft the US Navy. Researched and prepared a comprehensive list of aircraft TCTOs required for flight. Briefed US Navy Officers and Military contractors during program management reviews Show less
-
-
Tactical Aircraft Depot Maintenance Craftsman
-
Feb 1994 - May 1996
Appointed as lead military production scheduler for the presidential directed F-16A/B aircraft regeneration project supporting the Royal Jordanian Air Force. Managed time accounting and completed 331 TCTOs. Updated aircraft historical documents to ensure procedures were followed. This led to a promotion and accommodation medal.Developed parts inventory tracking database for managing over 5000 aircraft parts. Selected for inaugural F-16 regeneration project for twenty four F-16A/B aircraft (Peace Marble IV) to be delivered to the Israeli Air Force. Performed major aircraft inspections including: TCTOs, depot level upgrades, engine operation checks, component time changes, system servicing, document reviews and updated historical records. Received USAF medal and accommodation.Performed depot level TCTOs, aircraft modifications, crash damage evaluations, and cost estimates on all blocks of F-16 aircraft ensuring procedures completed on time and under budget Show less
-
-
Community
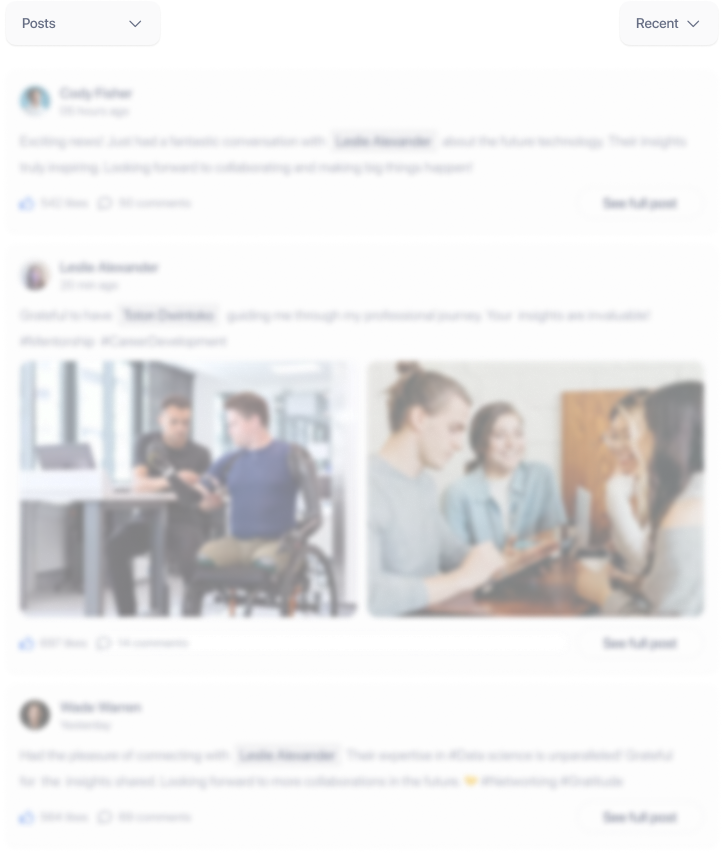