Allan Manning
Head of Technical Support at TurnKey Lender- Claim this Profile
Click to upgrade to our gold package
for the full feature experience.
Topline Score
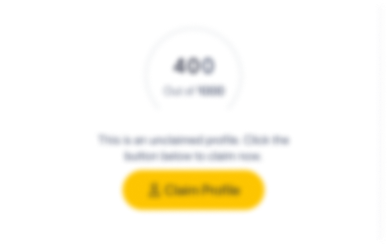
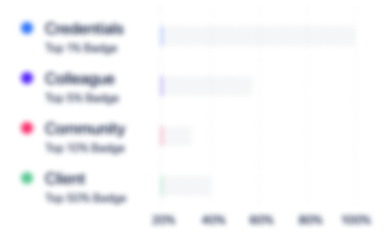
Bio


Experience
-
TurnKey Lender
-
United States
-
Software Development
-
100 - 200 Employee
-
Head of Technical Support
-
Sep 2022 - Present
-
-
-
MTech Mobility
-
United States
-
IT Services and IT Consulting
-
1 - 100 Employee
-
Director Of Support Services
-
Oct 2021 - Sep 2022
-
-
-
Telit IOT Platforms
-
Boca Raton Florida
-
Technical Support Manager
-
Mar 2014 - Jul 2021
Managed and improved a global team network and support engineers to provide outstanding technical support to global customers in the IOT industry. Accomplishments include achieving 99%+ SLA objectives, increased support staff 300%, managed customer escalations while improving the escalation process, became system administrator of Salesforce ™ CRM with many design improvements and implementations. Also provided detailed (MO, QTR, S1 S2) status reports to executive level management and tier 1… Show more Managed and improved a global team network and support engineers to provide outstanding technical support to global customers in the IOT industry. Accomplishments include achieving 99%+ SLA objectives, increased support staff 300%, managed customer escalations while improving the escalation process, became system administrator of Salesforce ™ CRM with many design improvements and implementations. Also provided detailed (MO, QTR, S1 S2) status reports to executive level management and tier 1 customers on support KPIs, escalations and project developments. Other outstanding accomplishments include primary contributor to successful ISO-270001 certification, designed and implemented RMA procedures and enhanced the overall support flow process. Show less Managed and improved a global team network and support engineers to provide outstanding technical support to global customers in the IOT industry. Accomplishments include achieving 99%+ SLA objectives, increased support staff 300%, managed customer escalations while improving the escalation process, became system administrator of Salesforce ™ CRM with many design improvements and implementations. Also provided detailed (MO, QTR, S1 S2) status reports to executive level management and tier 1… Show more Managed and improved a global team network and support engineers to provide outstanding technical support to global customers in the IOT industry. Accomplishments include achieving 99%+ SLA objectives, increased support staff 300%, managed customer escalations while improving the escalation process, became system administrator of Salesforce ™ CRM with many design improvements and implementations. Also provided detailed (MO, QTR, S1 S2) status reports to executive level management and tier 1 customers on support KPIs, escalations and project developments. Other outstanding accomplishments include primary contributor to successful ISO-270001 certification, designed and implemented RMA procedures and enhanced the overall support flow process. Show less
-
-
-
B2X Care Solutions
-
Germany
-
Transportation, Logistics, Supply Chain and Storage
-
300 - 400 Employee
-
Technical Project Manager
-
Jul 2012 - Mar 2014
Support B2X with project management activities globally including NA, EMEA, APAC, and LATAM with direct customer and supplier interactions; manage projects pertaining to site on-boarding, product quality, and process improvement; and identify project scope, risk analysis, mitigation strategies, develop project plans, identify stake holders, and produce progress reports. Support B2X with project management activities globally including NA, EMEA, APAC, and LATAM with direct customer and supplier interactions; manage projects pertaining to site on-boarding, product quality, and process improvement; and identify project scope, risk analysis, mitigation strategies, develop project plans, identify stake holders, and produce progress reports.
-
-
-
BlackBerry
-
Canada
-
Software Development
-
700 & Above Employee
-
Field Quality Project Manager
-
Mar 2011 - Jul 2012
Description: Implement issue management, development of support processes, data and device analysis, presentations, customer service, mentoring and project planning; develop several supporting areas such as device collections, device analysis, data analysis, stakeholder team meetings, and prioritization of issues; and support development activities with multiple presentations and extensive documentation. Description: Implement issue management, development of support processes, data and device analysis, presentations, customer service, mentoring and project planning; develop several supporting areas such as device collections, device analysis, data analysis, stakeholder team meetings, and prioritization of issues; and support development activities with multiple presentations and extensive documentation.
-
-
-
Texas Instruments
-
United States
-
Semiconductor Manufacturing
-
700 & Above Employee
-
Process & Equipment Engineering
-
Jan 2001 - Jun 2009
Description: Redefined the image testing process and developed a defect model; developed an automated optical inspection process and automated image inspection test station; reduced customer returns through deployment of automated test system; conducted and implemented documentation and technical writing; coordinated execution of changes to testing procedures; coordinated the creation, testing and release of any new device or new test variation; assisted in development of LAT process and… Show more Description: Redefined the image testing process and developed a defect model; developed an automated optical inspection process and automated image inspection test station; reduced customer returns through deployment of automated test system; conducted and implemented documentation and technical writing; coordinated execution of changes to testing procedures; coordinated the creation, testing and release of any new device or new test variation; assisted in development of LAT process and devised a latent acceptance test; and used statistical process control to identify defect excursions.
-
-
Process Engineering Technician
-
2000 - 2001
Primary duty was product return failure analysis which primarily consisted of image review, defect characterization and data analysis. Personally performed all image reviews using in house test equipment and supplemented findings with SEM (Scanning Electron Microscope) images and EDAX (Energy-Dispersive X-ray analysis) data. Kept samples of all defect types for comparisons and made defect libraries which were used in training and demonstrations. Defined defect classifications by assigning… Show more Primary duty was product return failure analysis which primarily consisted of image review, defect characterization and data analysis. Personally performed all image reviews using in house test equipment and supplemented findings with SEM (Scanning Electron Microscope) images and EDAX (Energy-Dispersive X-ray analysis) data. Kept samples of all defect types for comparisons and made defect libraries which were used in training and demonstrations. Defined defect classifications by assigning defect definitions and would accomplish this using multiple defect characteristics such as appearance, morphology and root cause. In addition, maintained a high level of symmetry between the manufacturing organization and the business organization by constantly communicating and comparing defect information with the customer quality engineers and technicians of the business group. Hosted weekly product returns team meeting consisting of the fab manager, manufacturing managers, process and equipment engineering managers, product engineers, quality assurance personnel and customer service representatives. Presented returns data at the weekly operations meeting and often fielded questions regarding data and defect characterization. Developed a training program for image inspection operators. Using the data collected performing returns analysis would give the operators training on high frequency defect types and methods on how best to detect them.
-
-
Equipment Systems Technician
-
1999 - 2000
Installation of FSI ™ brand surface conditioning equipment. Was assigned ownership of FSI brand wafer surface conditioning equipment. Coordinated and carried out troubleshooting and routine maintenance. Applied troubleshooting expertise to many other types of wafer conditioning equipment such as baths, hoods, etchers, sorters, ovens, etc. Provided operational training to engineers and operators and gave maintenance training to the other technicians.
-
-
-
TEL FSI
-
Semiconductors
-
100 - 200 Employee
-
Customer Service Engineer
-
Feb 1996 - Sep 1999
Installation of surface conditioning equipment. Installed FSI brand wafer surface conditioning equipment at semiconductor companies in the DFW and Houston area. Also performed installations in New Mexico and Japan. Approximately 30% travel was required for this job. Coordinated and performed equipment maintenance for several customers in the DFW area. Equipment maintenance was done on weekly, monthly, quarterly and yearly basis. This maintenance required basic hand tools along with… Show more Installation of surface conditioning equipment. Installed FSI brand wafer surface conditioning equipment at semiconductor companies in the DFW and Houston area. Also performed installations in New Mexico and Japan. Approximately 30% travel was required for this job. Coordinated and performed equipment maintenance for several customers in the DFW area. Equipment maintenance was done on weekly, monthly, quarterly and yearly basis. This maintenance required basic hand tools along with knowledge of handling hazardous chemicals such as HF, HCL, H2SO4, etc. Customer interaction and training. New installations often required training the customer’s engineers and operators on tool functions and operation. Troubleshooting. On numerous occasions would provide successful troubleshooting support to customers by being on site performing the work myself or by providing telephone support to the customer’s technicians. Inventoy control. Organized customer service inventory area in a secure environment where material could be found quickly and in good condition. Provided an inventory tracking system with Microsoft Excel to other CSEs that contained inventory amount, reorder period, lead time, cost and position in supply room along with training and system instructions. Show less Installation of surface conditioning equipment. Installed FSI brand wafer surface conditioning equipment at semiconductor companies in the DFW and Houston area. Also performed installations in New Mexico and Japan. Approximately 30% travel was required for this job. Coordinated and performed equipment maintenance for several customers in the DFW area. Equipment maintenance was done on weekly, monthly, quarterly and yearly basis. This maintenance required basic hand tools along with… Show more Installation of surface conditioning equipment. Installed FSI brand wafer surface conditioning equipment at semiconductor companies in the DFW and Houston area. Also performed installations in New Mexico and Japan. Approximately 30% travel was required for this job. Coordinated and performed equipment maintenance for several customers in the DFW area. Equipment maintenance was done on weekly, monthly, quarterly and yearly basis. This maintenance required basic hand tools along with knowledge of handling hazardous chemicals such as HF, HCL, H2SO4, etc. Customer interaction and training. New installations often required training the customer’s engineers and operators on tool functions and operation. Troubleshooting. On numerous occasions would provide successful troubleshooting support to customers by being on site performing the work myself or by providing telephone support to the customer’s technicians. Inventoy control. Organized customer service inventory area in a secure environment where material could be found quickly and in good condition. Provided an inventory tracking system with Microsoft Excel to other CSEs that contained inventory amount, reorder period, lead time, cost and position in supply room along with training and system instructions. Show less
-
-
Education
-
Kaplan College
BS, Information Technology -
Texas State Technical College
AA, Biomedical Equipment Engineering -
Mclennan Community College
AA, Ag. Production & Resource Management
Community
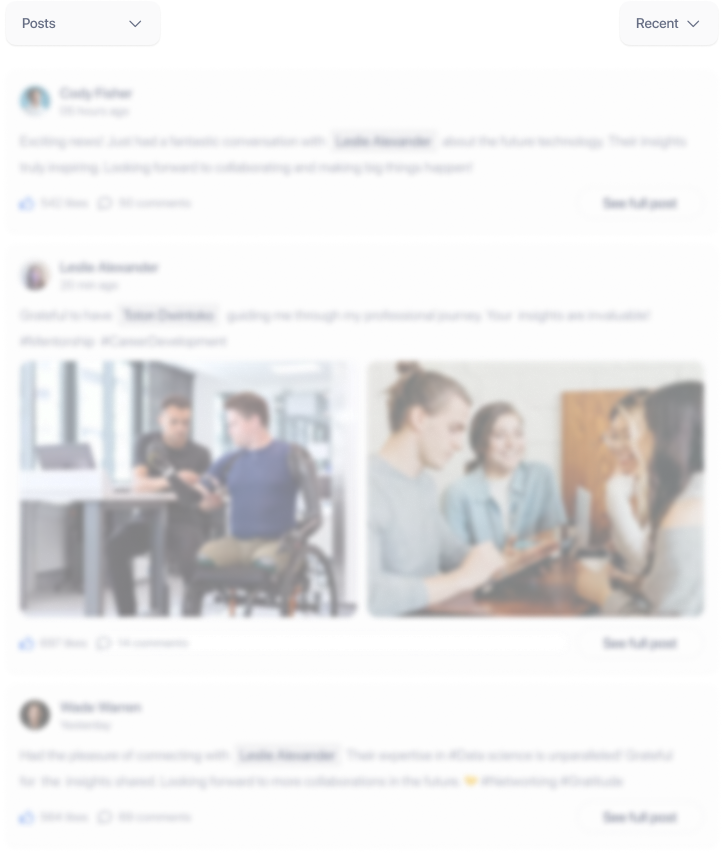