Alkesh Sharma
Director and General Manager at Eden Valley Foods Limited- Claim this Profile
Click to upgrade to our gold package
for the full feature experience.
Topline Score
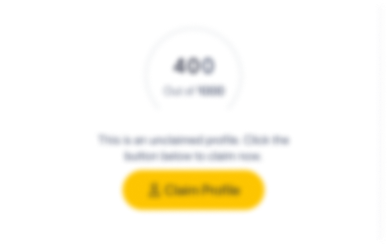
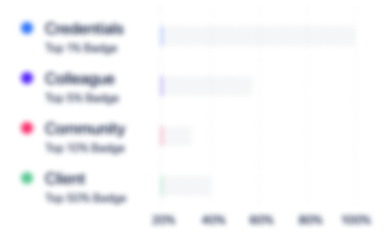
Bio


Experience
-
Eden Valley Foods Limited
-
New Zealand
-
Food and Beverage Services
-
1 - 100 Employee
-
Director and General Manager
-
Jan 2019 - Present
-
-
-
Brooke Holdings Ltd
-
United Kingdom
-
Business Consulting and Services
-
Food Consultant (Quality Systems Manager & Trader)
-
2012 - Oct 2018
Role involved developing and maintaining a QA system for the company along with day-to-day support in developing policies, procedures and dealing with corrective action for internal and third-party audits. In addition to this, I managed sales to retail stores and food ingredient customers. I was also responsible for the supplier approval programme for the business and procurement of high volume food ingredients from global vendors.-Co-ordinated compliance of QA systems at the 3PL warehouse and repack facility-Completed audit of international suppliers in China and India-Successfully exceeded the budgeted gross profit of $600K within one year-Recognised viable opportunities and added 30 new accounts nationally -Maintained strict credit controls to keep accounts within credit limits without affecting sales-Introduced 11 new supply sources for existing and new products
-
-
-
-
Key Account Manager
-
Apr 2007 - Sep 2012
This role was created to fulfil a sales gap in the market for owner-operated retail stores. Responsibilities included identifying opportunities, recommending and sourcing food ingredients to meet the customer requirements. -Identified new opportunities for accelerated growth in the small business market, increasing the number of accounts from 27 to 224-Retained and increased sales with existing customers, achieving 10 times growth in the sales volume -Established new supply sources for key ingredients and products from India, generating business worth $3mil per annum-Increased gross profit from $5K to $60K within two years. -Provided market information, feedback and reports on customers, competitor activity, and opportunities to benefit the business
-
-
Quality Systems Manager
-
Aug 2001 - Apr 2009
Responsible for developing, implementing and maintaining new methods to improve food quality systems and processes. In addition to this, coordinated with MAF/MPI for incoming container inspections, managed customer complaints and NCR process with suppliers.-Developed the first formal HACCP based Food Safety Programme for the businessDeveloped specific processes aimed at ensuring labelling compliance of imported and locally packed products in accordance to FSANZ-Implemented Food Safety policies and procedures at the blending and re-pack facility-Conducted due diligence of stock quality for the acquisition of Marsanta Foods-Completed auditing of international suppliers and vendors in Iran, India and China-Generated new product ideas and modified existing products and processes-Trained internal staff with issues relating to food safety and HACCP-Additionally, continued to source products internationally due to existing relationships with suppliers
-
-
Purchasing Officer & Food Safety Co-ordinator
-
Jul 2000 - Aug 2001
Responsible for sourcing local food ingredients and setup of food safety practices within the business.-Provide accurate and timely stock reporting and control all stock movements-Reduce the overall cost of purchases-Oversee, maintain, improve and report on the setup of the company’s quality system -Assist the sales staff with technical representation of food quality issues.
-
-
-
-
Production Manager
-
Dec 1999 - Mar 2000
Responsible for the management of a Production Plant (60 staff) which produced cupcakes, layer cakes and bakery products. This included management of new product development, production scheduling, maintenance and engineering personnel.-Successfully conducted plant trials for bakery products such as swiss rolls and cupcakes-Recipes were modified to increase shelf life by 30%-Production wastage was minimised by 10% Responsible for the management of a Production Plant (60 staff) which produced cupcakes, layer cakes and bakery products. This included management of new product development, production scheduling, maintenance and engineering personnel.-Successfully conducted plant trials for bakery products such as swiss rolls and cupcakes-Recipes were modified to increase shelf life by 30%-Production wastage was minimised by 10%
-
-
-
-
Production Manager
-
Sep 1993 - Dec 1999
Responsible for the management of a Production Plant (200 staff) which produced cakes, potato chips, rusks, chocolate products. This included management of new product development, production scheduling, maintenance and engineering personnel.-Improvement in plant efficiencies through new working methods and tighter waste control. -Installation & running of a multi-purpose cake production line from Sasib (manufacturer of the plant). -Development of new recipes and product range-Major refurbishment of cake production hall. No production losses were incurred during this period. -Achievement of MRP2 Class A in manufacturing procedures. -Major technical study conducted as part of due diligence for acquisition of leading cake manufacturer in Egypt.
-
-
Education
-
Meerut University
Master of Science, Organic Chemistry -
Nagpur University
Master of Food Technology
Community
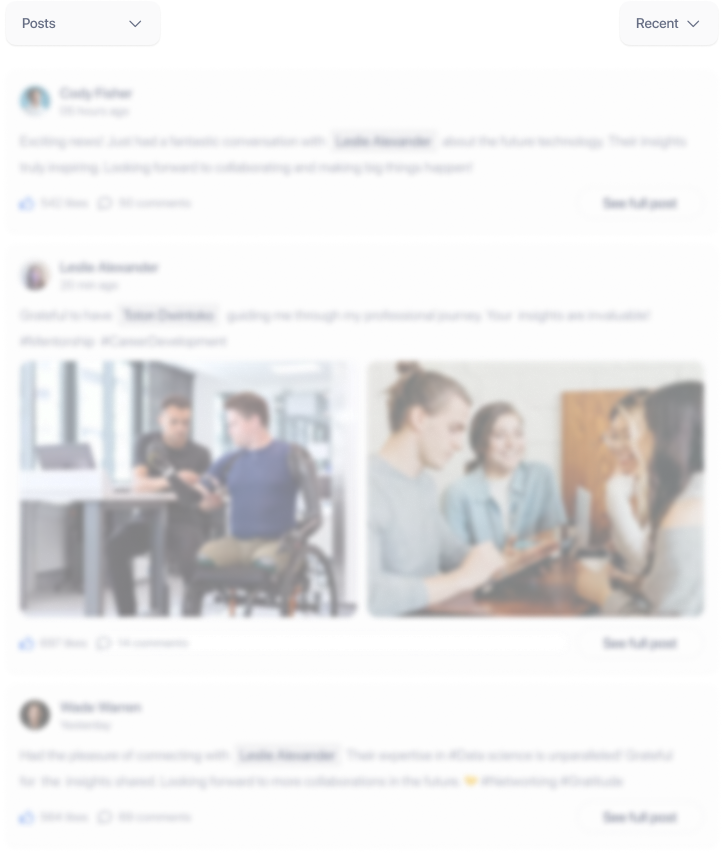