Alison Rusul
Manufacturing System Manager at Carbon Revolution- Claim this Profile
Click to upgrade to our gold package
for the full feature experience.
Topline Score
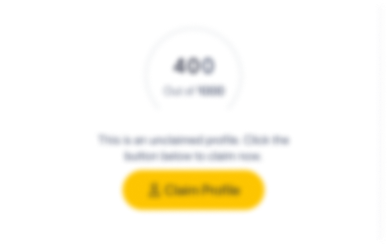
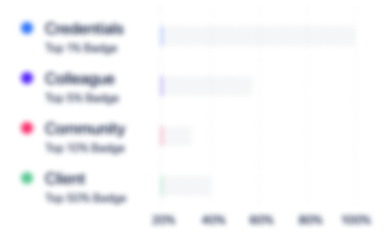
Bio


Experience
-
Carbon Revolution
-
Australia
-
Motor Vehicle Parts Manufacturing
-
100 - 200 Employee
-
Manufacturing System Manager
-
Jul 2019 - Present
Develop and implement a Lean Manufacturing System for Carbon Revolution that include 86 statements. Lead the Manufacturing scheduling process through a Sales & Operational Planning (S&OP). Liaise with Program Managers and Customers to ensure all programs receive the appropriate level of support. Manage the workforce growth within Manufacturing at Carbon Revolution through recruitment, on-boarding, training and upskilling programs. Identify and drive continuous improvement of the manufacturing process using Lean principles. Improves knowledge, capability and implementation ability of the current workforce with lean tools including; Workplace Organisation, Status at a Glance, Short Interval Control, Constraints Analysis, Standardisation, FIFO, 5S, Kanban, People Involvement, Predictive and Reliability Centred Maintenance, Practical Problem Solving, One Piece Flow, Value Stream Mapping, Workflow balancing, Capability based training development and assessment, Continuous Improvement. Develop and implement capacity expansion steps in conjunction with the Industrialisation Director / team.
-
-
-
VINFAST
-
Vietnam
-
Motor Vehicle Manufacturing
-
700 & Above Employee
-
Manufacturing System and Technical Manager
-
Dec 2017 - Jun 2019
Accountable for the manufacturing systems and Industrial Engineering activities across VinFast assembly operations. Guide, support and coach operation’s personnel in Lean Manufacturing Systems so they are able to achieve all aspects of the business in the areas of safety, people, quality, responsiveness and cost. Provide Industrial Engineering technical support to Area Managers, making production waste visible, measurable and ultimately eliminated Created the Lean Manufacturing System in VinFast – VinFast Excellent System Designed and Implemented a Simulated Work Environment to train all employees at all levels of the organisation. Manufacturing Lead for implementing the PLM (Product Lifecycle Management) System (Manufacturing Bill of Materials – Bill of Process – Standardised Work). Manufacturing Lead for creating and overseeing the Manufacturing Change Control. Demonstrated ability to perform successfully in multi-national company.
-
-
-
Schiavello
-
Australia
-
Leasing Non-residential Real Estate
-
300 - 400 Employee
-
Quality Manager
-
Feb 2017 - Nov 2017
Quality Manager for Schiavello Manufacturing. Encourage and support senior and operations management to develop and implement Customer Focussed quality and continual improvement. Promote quality achievement and performance improvement throughout the organization. Promote and facilitate the implementation, maintenance and compliance to AS/NZS ISO9001. Work collaboratively with the business units and corporate groups such as Product Development Group and IT to provide solutions to manufacturing problems. Liaise with external auditors on all manufacturing quality related matters and ensure that any nonconformities identified during audits are communicated and addressed by the respective.
-
-
-
Holden
-
Australia
-
Motor Vehicle Manufacturing
-
200 - 300 Employee
-
Industrial Engineer & Global Manufacturing Systems Coordinator
-
May 2014 - Nov 2016
Support the implementation and maintenance of GMS (Global Manufacturing System) and IE (Industrial Engineering) activities/systems to identify areas for elimination of waste (incl. labour, process etc), together with development of cost efficient process’ to improve the overall operating efficiency/effectiveness of the site. Develop strategies to implement the recommended improvements in workplace layout, material flow, labour allocation, line balance to maximise safety, quality & overall operational efficiencies of the site.
-
-
Quality Coordinator
-
Sep 2013 - May 2014
- Monitor compliance with ISO9001, ISO14001 & TS16949 standards.- Perform daily layered audits - Plastic representative for GMS Built in Quality Basket weave- Train/Coach individuals in Built in Quality- Analyse GSIP data - Manage Plastic PSR (Problem Solving Report) database & chair weekly reviews- Manage Plastic Control Change Process- Report out on Plastic GCA (Global Customer Audit) result weekly- Chairperson of Quality on Level 2 BPD (Business Plan Deployment) Board- Champion for Plastic DRR (Direct Run Rate) Issues & Chair meetings- Perform, record & distribute findings for Internal audits- Perform weekly Procedure and Work Instruction reviews- Participate in PFMEA (Process Failure Mode & Effect Analysis)- Respond/Communicate to GA Alarm Escalations
-
-
Production Supervisor
-
Jun 2006 - Sep 2013
- Supervise and allocate work to 4 - 6 teams – 50+ personnel.- Implement annual business plan incorporating Safety, People, Quality, Responsiveness & Cost- Develop processes and audit compliance to ensure Holden’s Vision & Mission Statements are upheld.- Lead a team to implement standard engineering based timing for every job within General Assembly.- Key member of the Cruze launch team.- Develop and deliver information pertaining to Holden’s Core Values.- Set targets and metrics for the year to ensure business goals are met.- Performance review annual plan every 6 months using Commitment Accountability Partnership (CAP) process.- Develop Team Leader's skills and effectiveness in the workplace.- Improved efficiency of Group with line balance/head reduction- Perform daily layered audits - Closing out finding - Conduct safety audits, evaluation & continuous improvement plans.- Created & Delivered Safety Induction for Holden’s Production Plant. - Monitor quality & efficiency via General Assembly Business Plan Board.- Conduct new employee inductions and allocate ongoing training.- Maintain company policies and workplace safety compliance.
-
-
Team Leader
-
Sep 1997 - Jun 2006
• Lead a work group of between 7-9 personnel• Liaise with the Maintenance, Materials, Mechanics, Engineering and Supervision• Facilitate and perform TPM (Total Production Maintenance) & Safety Tours daily. Launch Team member for the VE
-
-
Production Operator
-
May 1995 - Sep 1997
-
-
Education
-
SAI Global
Certificate, Implementing a Quality Management System ISO 9001:2015 -
General Motors University
DFSS Green Belt Certification, Six Sigma -
TAFE SA
Advanced Diploma, Human Resources -
TAFE SA
Advanced Diploma, Management -
Lloyd's Register Quality Assurance LTD
Auditor Training Course, Internal QMS -
Lloyd's Register Quality Assurance LTD
Auditor Transition Training Course, ISO/TS16949 -
GM Holden
Certificate III, Competitive Manufacturing -
TAFE SA
Certificate IV, Business (Frontline Management) -
Gladstone High School
High School, Sace - Year 12
Community
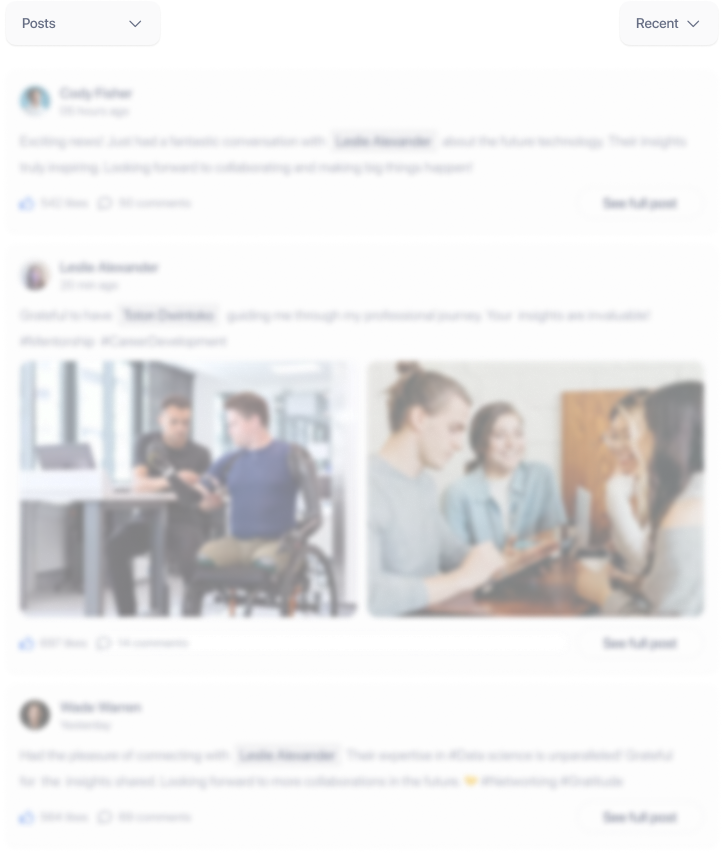