Aline Queiroz Pereira
Senior Supply Chain Analyst at Diva International Inc. "DivaCup"- Claim this Profile
Click to upgrade to our gold package
for the full feature experience.
-
Portuguese Native or bilingual proficiency
-
Spanish Full professional proficiency
-
English Native or bilingual proficiency
Topline Score
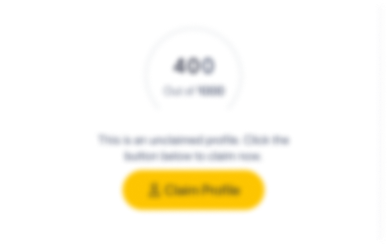
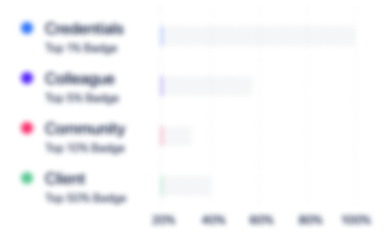
Bio

Alejandro Celis
I had the pleasure of studying with Aline for one year, she is a very efficient and responsible person. She is dedicated, self-motivated and very capable. Aline is also a great team player.

Robert Hillcoat
Aline is very detailed and would be a definite asset to any company.

Alejandro Celis
I had the pleasure of studying with Aline for one year, she is a very efficient and responsible person. She is dedicated, self-motivated and very capable. Aline is also a great team player.

Robert Hillcoat
Aline is very detailed and would be a definite asset to any company.

Alejandro Celis
I had the pleasure of studying with Aline for one year, she is a very efficient and responsible person. She is dedicated, self-motivated and very capable. Aline is also a great team player.

Robert Hillcoat
Aline is very detailed and would be a definite asset to any company.

Alejandro Celis
I had the pleasure of studying with Aline for one year, she is a very efficient and responsible person. She is dedicated, self-motivated and very capable. Aline is also a great team player.

Robert Hillcoat
Aline is very detailed and would be a definite asset to any company.

Experience
-
DIVA
-
Canada
-
Retail Health and Personal Care Products
-
1 - 100 Employee
-
Senior Supply Chain Analyst
-
May 2022 - Present
-
-
Supply Chain Analyst
-
May 2021 - Apr 2022
-
-
-
Penske Logistics
-
United States
-
Truck Transportation
-
700 & Above Employee
-
Logistics Planner
-
Mar 2020 - May 2021
- Develop the logistics plan for North American inbound supply chain network and cross-dock, managing material transfers between two Toyota plants; - Investigate forecast deviation for trailer cube outs, finding the root cause and proposing countermeasures; - Optimize cross-dock schedules and design to meet production timing; - Generate unload door schedules for over 200 different routes per day; - Provide data on departmental performance to support data-driven decisions; - Support the coordination of the logistics plan implementation with the customer, suppliers, transportation suppliers, and team members; Show less
-
-
-
Linamar Corporation
-
Canada
-
Motor Vehicle Manufacturing
-
700 & Above Employee
-
Materials Coordinator
-
Apr 2018 - Mar 2020
- Planned and placed vendor orders for high volume lines, created production requirements and monitored abnormal costs, quantities, and outstanding orders; - Monitored scheduled jobs on the MRP system and updated entries upon necessity; - Performed inventory management activities, ensuring material arrival, inventory accuracy, analyzing discrepancies, adjusting min and max inventory level, re-order point, set up new items, ensuring the inventory reduction target was being met; - Coordinated activities with different departments in new product development projects, month-end reconciliation, BOM or quality issues; - Supplier and customer management: communicated on a regular basis to review forecast and ensure production and shipping plan are up to date; - Updated monthly customer and supplier performance reports; - Communicated coverage concerns and timing of replenishment to stakeholders and implemented and followed up corrective actions; Show less
-
-
-
Penske Truck Leasing
-
United States
-
Truck Transportation
-
700 & Above Employee
-
Rental Representative
-
Dec 2017 - Apr 2018
• Managed and oversaw large fleet of vehicles • Matched vehicle demand with availability • Handled inbound and outbound sales process • Maintained existing customer relationship and coordinate customer accounts • Generated new business leads • Ensured excellent service in a fast-paced environment • Developed a smart vehicle choice spreadsheet, maximizing profit for all trucks; • Managed and oversaw large fleet of vehicles • Matched vehicle demand with availability • Handled inbound and outbound sales process • Maintained existing customer relationship and coordinate customer accounts • Generated new business leads • Ensured excellent service in a fast-paced environment • Developed a smart vehicle choice spreadsheet, maximizing profit for all trucks;
-
-
-
FedEx Office
-
United States
-
Printing Services
-
700 & Above Employee
-
Customer Consultant
-
Mar 2017 - Sep 2017
• Customer service activities and assist in sales, twice on the quarterly top 10 product sales • Provide necessary documentation for shipments • Used editing software to format printing documents • Identify customers’ needs to achieve satisfaction by providing adapted solutions • Customer service activities and assist in sales, twice on the quarterly top 10 product sales • Provide necessary documentation for shipments • Used editing software to format printing documents • Identify customers’ needs to achieve satisfaction by providing adapted solutions
-
-
-
Bosch
-
Germany
-
Software Development
-
700 & Above Employee
-
Project Coordinator- PMO
-
Mar 2015 - Dec 2016
• Supported project teams, from 5 different areas, to follow the product development process requirements • Developed and applied training for personnel regarding process changes; • Organized, performed and facilitated 20 project kick-off workshops within one year • Mapped product development flow of information in order to improve and integrate product development process • Updated performance indicators and developed an indicator for follow-up project activities and measure delays • Supported project teams, from 5 different areas, to follow the product development process requirements • Developed and applied training for personnel regarding process changes; • Organized, performed and facilitated 20 project kick-off workshops within one year • Mapped product development flow of information in order to improve and integrate product development process • Updated performance indicators and developed an indicator for follow-up project activities and measure delays
-
-
-
Continental
-
Germany
-
Motor Vehicle Manufacturing
-
700 & Above Employee
-
Continuous Improvement Intern
-
Mar 2013 - Mar 2015
• Updated production indicators • Performed weekly audits on 5S and ESD (Electrostatic discharge) control • Responsible for the Lessons Learned implementation, completing all of the pendent actions • Developed a training program regarding ESD (Electrostatic discharge) safety measures, as well as internal audit points • Performed budget control and budget reports of the division, as well as created purchase orders • Developed Problem Solving 8D Template for production problems • Updated production indicators • Performed weekly audits on 5S and ESD (Electrostatic discharge) control • Responsible for the Lessons Learned implementation, completing all of the pendent actions • Developed a training program regarding ESD (Electrostatic discharge) safety measures, as well as internal audit points • Performed budget control and budget reports of the division, as well as created purchase orders • Developed Problem Solving 8D Template for production problems
-
-
Education
-
Rochester Institute of Technology
Data Analytics and Visualization in Health Care, Health/Health Care Administration/Management -
Conestoga College
Post-Graduate Certificate Program, Supply Chain Management - Global -
Conestoga College
Post-Graduate Certificate Program, Global Business Management -
Universidade São Francisco
Engineer's degree, Production Engineering
Community
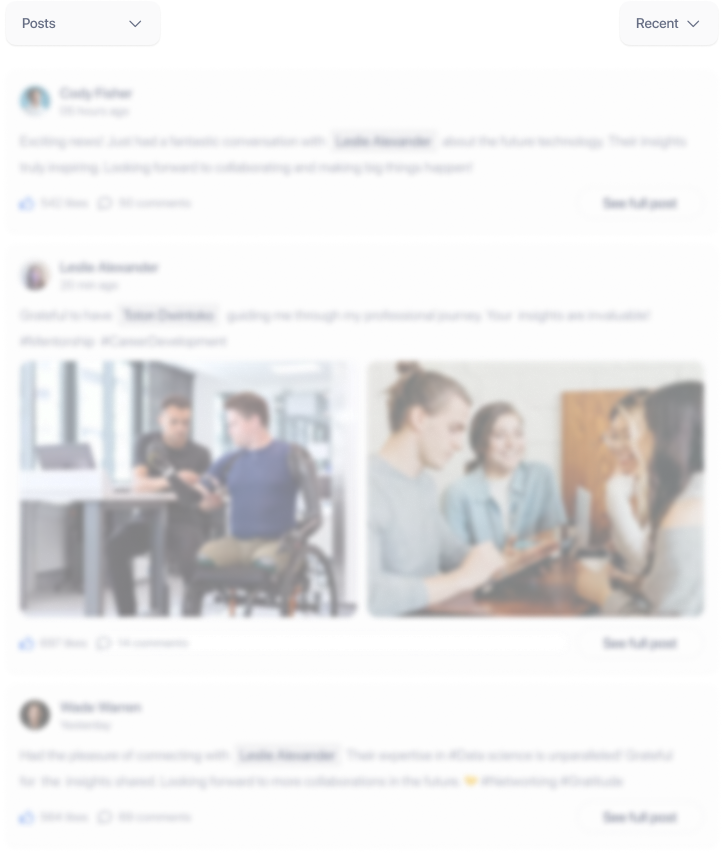