Alexander Logan
Director of Operations at AeroX Aviation Services- Claim this Profile
Click to upgrade to our gold package
for the full feature experience.
Topline Score
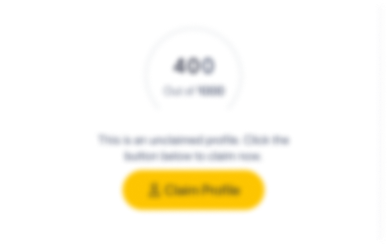
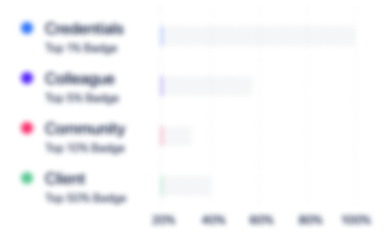
Bio


Credentials
-
FAA Airframes
Federal Aviation AdministrationOct, 2013- Sep, 2024 -
FAA Powerplant
Federal Aviation AdministrationOct, 2013- Sep, 2024 -
General Radiotelephone Operators License with Radar Endorsement
Federal Communications CommissionJul, 2013- Sep, 2024 -
Autodesk AutoCAD User Certification
Manchester Community College NHJan, 2012- Sep, 2024
Experience
-
AeroX Aviation Services
-
United States
-
Aviation and Aerospace Component Manufacturing
-
1 - 100 Employee
-
Director of Operations
-
Jan 2020 - Present
-
-
Project Manager, Maint. Supervisor & Head of Sales/Marketing - Aviation Maintenance & Modifications
-
Sep 2018 - Jan 2020
AeroX LLC was established as part of a merger/acquisition deal involving ARM International LLC.Duties & Responsibilities:Manage talent acquisition process, marketing campaigns, client sales & relations. Network within industry to secure technical & non-technical employees and/or MOD team members. Manage job postings, online presence, and compile data regarding current openings and recruitment metrics. Coordinate and facilitate interviews and travel as necessary.Act as a trusted advisor for Aircraft owners, operators, air agencies and other maintenance providers. Evaluate potential aircraft upgrades and modifications on a case-by-case basis to ensure customer needs are met and desired functionality is achieved.Perform major structural modifications and repairs as required per STCs, AMMs, SRMs, SBs, ADs, and other approved technical data on various aircraft worldwide. Maintain customer loyalty through quality workmanship. scheduling flexibility, and turn time efficiency. Works include: Wifi instialltions, SATCOM installations, Cabin phone systems, ADS-B solutions, Winglet installations, Skin replacement/repairs, ventral strake installations, ATG upgrades, custom cabin equipment mounting, cabin entertainment and management systems, and much more.
-
-
-
-
Director Of Marketing And Development
-
Jul 2017 - Mar 2019
Support Recruiting and Sales staff via web-based technical expertise; Create Graphics, Advertising Campaigns, Newsletters, and other original Web Content; Manage various social-media platforms; track database growth and maintain lead quality; increase name recognition of company and drive additional traffic to job postings. End result: Increase company outreach and stimulate growth. Accomplishments: Created original recruiting campaigns which allowed Matthews Aviation to attract and hire more than 120 experienced Aircraft Maintenance Professionals within two days for a single client location; practically doubling the Contractors on staff, significantly increasing company revenue.
-
-
Marketing Manager & Recruiter
-
Aug 2016 - Jun 2018
-
-
-
Self Employed
-
Real Estate
-
1 - 100 Employee
-
Project Manager - Major Alterations
-
Apr 2016 - Sep 2016
Organize and plan major modification projects on various aircraft in accordance with approved technical data. Source talent, oversee/supervise/and assist in physical completion of modification; including but not limited to the following:-Structural alterations/repairs-Skin alterations/repairs-Antenna Installation-Fuel line/system alterations-Installing/routing wire harnesses-Flight-control alterations-Aircraft Painting-Inspection-Updating aircraft logbooks-Material and Man-Hour tracking-Invoicing and other administrative duties.Projects include special missions STCs, Antenna Installations, Cabinet/Equipment shelf fabrication & Installation, Phone & Entertainment systems upgrades, basic and complex repairs on the following aircraft models:-Gulfstream GIV-Bombardier Challenger & Global-LearJet 35/35A-Cessna Citations, 206 & 208-Beechcraft King Air B200-Pilatus PC-12-Dassault Falcon 50, 900ex, 7x-Sikorsky S76
-
-
-
Pro Star Aviation
-
United States
-
Aviation and Aerospace Component Manufacturing
-
1 - 100 Employee
-
Lead Aircraft Structural Installation Technician
-
Oct 2013 - Jun 2016
Modify aircraft through fabrication and installation of sheet-metal parts. Fabricate parts utilizing blueprints, mechanical drawings, applicable manuals, hand held tools and large metal forming tools. Ensure accurate fabrication of parts using precision measuring devices. Apply chemical conversion coating and paint parts to match aircraft in immediate vicinity and to prevent corrosion. Remove aircraft interiors and obstructing structures to facilitate installation of new avionics equipment and fabricated parts.
-
-
-
Morgan Advanced Materials
-
United Kingdom
-
Glass, Ceramics and Concrete Manufacturing
-
700 & Above Employee
-
CNC Fabrication Technician
-
Oct 2011 - Apr 2013
Apply knowledge of mechanics, mathematics, metal properties, layout, and machining procedures to set up and operate a variety of machine tools to produce precision parts. Fabricate, modify, and repair parts and/or corresponding mechanical drawings. Calculate machine speed and feed ratios and the size and position of cuts. Insert control instructions into machine control units to start operation. Modify cutting programs to account for problems encountered during operation. Measure dimensions of finished work-pieces to ensure conformance to specifications, using precision measuring instruments, templates, and fixtures.
-
-
-
United States Marine Corps
-
United States
-
Armed Forces
-
700 & Above Employee
-
Work-Center Supervisor & Inspector / Aircraft Maintenance Technician
-
Nov 2006 - Nov 2011
Supervise a maintenance work-center of 15 mechanics. Determine schedules and assign work activities based on work priority, equipment availability, and skill of personnel. Monitor employees’ work levels and review worker performance. Develop, implement and evaluate maintenance policies and procedures. Coordinate and conduct worker training in safety, repair, maintenance techniques, operational procedures, and use of equipment. Counsel employees about work-related issues and assist employees to correct job-skill deficiencies. Establish lines of communication between maintenance work-center and administrative work-center.
-
-
Community
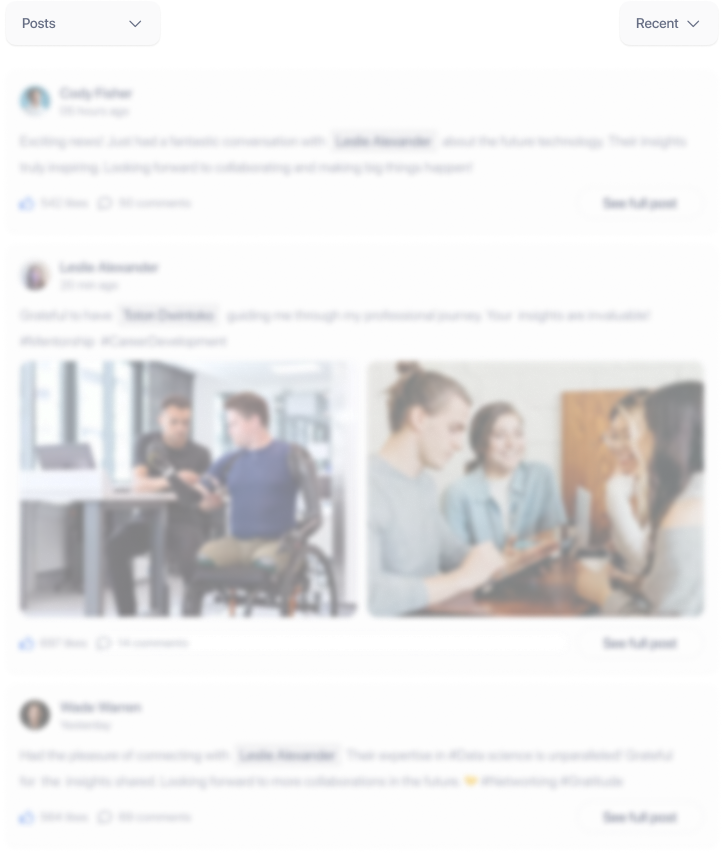