Alex Howard
Logistics Manager at Fun Outdoor Living- Claim this Profile
Click to upgrade to our gold package
for the full feature experience.
Topline Score
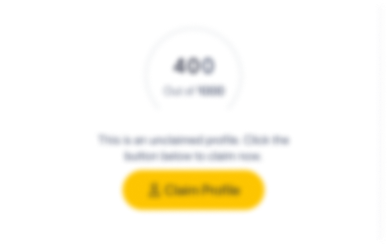
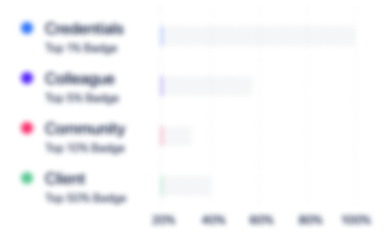
Bio

Mark Janeczko, MBA
Alex does a great job breaking down complex problems into actionable solutions. He has a vast understanding of lean logistical flows and excels at eliminating waste from processes. He is very lean focused and can eliminate process waste from any organization.

TANNER GALECKI
Alex works with tactical measure and choices driven by data. He digs deep into issues to find the root cause and then provides a solution for his team. I enjoyed working with Alex and learned a number of tips and life lessons from him while working together or sharing a conversation over lunch at the food truck. He takes his work very seriously and doesn't accept failure to be an option.

Mark Janeczko, MBA
Alex does a great job breaking down complex problems into actionable solutions. He has a vast understanding of lean logistical flows and excels at eliminating waste from processes. He is very lean focused and can eliminate process waste from any organization.

TANNER GALECKI
Alex works with tactical measure and choices driven by data. He digs deep into issues to find the root cause and then provides a solution for his team. I enjoyed working with Alex and learned a number of tips and life lessons from him while working together or sharing a conversation over lunch at the food truck. He takes his work very seriously and doesn't accept failure to be an option.

Mark Janeczko, MBA
Alex does a great job breaking down complex problems into actionable solutions. He has a vast understanding of lean logistical flows and excels at eliminating waste from processes. He is very lean focused and can eliminate process waste from any organization.

TANNER GALECKI
Alex works with tactical measure and choices driven by data. He digs deep into issues to find the root cause and then provides a solution for his team. I enjoyed working with Alex and learned a number of tips and life lessons from him while working together or sharing a conversation over lunch at the food truck. He takes his work very seriously and doesn't accept failure to be an option.

Mark Janeczko, MBA
Alex does a great job breaking down complex problems into actionable solutions. He has a vast understanding of lean logistical flows and excels at eliminating waste from processes. He is very lean focused and can eliminate process waste from any organization.

TANNER GALECKI
Alex works with tactical measure and choices driven by data. He digs deep into issues to find the root cause and then provides a solution for his team. I enjoyed working with Alex and learned a number of tips and life lessons from him while working together or sharing a conversation over lunch at the food truck. He takes his work very seriously and doesn't accept failure to be an option.

Experience
-
Fun Outdoor Living
-
United States
-
Facilities Services
-
1 - 100 Employee
-
Logistics Manager
-
Jul 2021 - Present
-
-
Operations Manager
-
Jul 2021 - Present
-
-
-
Kooks
-
United States
-
Motor Vehicle Manufacturing
-
1 - 100 Employee
-
Operations Excellence Manager
-
Jun 2020 - Aug 2021
-
-
Materials Manager
-
Jun 2020 - Aug 2021
-
-
-
Kapco Metal Stamping
-
United States
-
Mechanical Or Industrial Engineering
-
100 - 200 Employee
-
Production Planner
-
Jul 2019 - Dec 2019
Coordinating production workflow for one or multiple products. Planning and prioritizing operations to ensure maximum performance and minimum delay. Determining manpower, equipment and raw materials needed to cover production demand. Coordinating production workflow for one or multiple products. Planning and prioritizing operations to ensure maximum performance and minimum delay. Determining manpower, equipment and raw materials needed to cover production demand.
-
-
-
Wacker Neuson Group
-
Germany
-
Machinery Manufacturing
-
700 & Above Employee
-
Logistics Engineer
-
Jul 2018 - Jul 2019
Internal Logistics Engineer Logistics Engineering, Operations and Coordination. As a Logistics Engineer responsible for supporting the material strategy and optimization of inventory storage and flow of parts through the production facility. Working hand in hand with Material Control, Planning, Production, and Manufacturing Engineering, ensuring that processes are implemented to achieving warehousing and production support processes. Functioned as the Logistics Engineer responsible for documentation and optimization of current processes within Internal Logistics. In addition, also responsible for optimizing parts packaging to support PFEP (plan for every part) and optimization of parts presentation to production. • Warehouse and internal logistics design, planning and setup • 2800 Unique parts set up for storage and replenishment using internal warehouses. • 25,000. Ft of warehouse designed and implemented • Advanced logistics functions including kit by order and JIT sequencing based on lean manufacturing. • Capital investment and installation of $200,000 value racking setup and operations with Rapid Implementation time of 2 months. • Key player in the development of SAP WMS system, warehouse design, and logic building • Worked with supervisors to strengthen, develop, and support the daily process. • Wrote, updated, and controlled OMS and logistics work instruction database • Managed and generated tests based off of WI's and processes within the department. • Initiated a hands-on test to reassure department employees are trained appropriately. • Worked with manufacturing engineers to map and layout material flow, material storage, and labor requirements for the Material Control Department. • Support the development of warehousing strategy • Packaging optimizations in line with PFEP (plan for every part) strategy. • Trained and directed staff ensuring they understand their responsibilities and adhere to company policies and procedures. Show less
-
-
-
US Army
-
United States
-
Armed Forces
-
700 & Above Employee
-
Operations and Logistics Manager
-
Jan 2015 - Jan 2018
Logistics, Operations and Coordination, Responsible for the planning, coordination and execution of company mission and goals. Initiated programs to change logistic processes, culture and standard operating procedures to increase operational results and better company esprit de corps. Personally managed a fleet of over 40 vehicles in addition to 25 Million Dollars’ worth of company assets with zero losses. Increased company training and was in charge of over 200 personnel across multiple sites and locations. -Oversee all functions of purchasing; sourcing vendors, competitive quotes, receiving. -Research products, and negotiate cost effective purchase agreements. -Maintain excellent relationship with vendors. -Create and maintain database showing competitive pricing on all raw materials and purchase orders. -Train and direct staff ensuring they understand their responsibilities and adhere to company policies and procedures. -Managed large fleet of vehicles in excess of 4 million dollars. -Manage major shipping requirements regarding machinery, international shipments. Show less
-
-
-
US Army
-
United States
-
Armed Forces
-
700 & Above Employee
-
Medical Supply Warehouse Kuwait, Shipping & Receiving Manager
-
Nov 2013 - Oct 2014
Purchasing, Shipping, 2013 to 2014 As Shipping and Receiving, responsible for all policies, procedures and operations of the shipping and receiving department. Worked closely with each individual department, across multiple locations in order to ensure that the product was packed, and shipped in accordance to the customer's requirements. Checked and received all incoming orders. Maximized efficiency of the shipping and receiving departments by personally training all personnel. Administrative responsibilities included OSHA compliance, customer service, accounts payable, invoice all orders, audit and authorize freight invoices. -98% accuracy in shipments -100% accuracy in invoicing -Forklift certified trainer -Negotiated a 20% cost savings on small package shipments. -Achieved reduction in overtime, by efficient management of labor. -Decreased freight cost by negotiating freight rates -Worked on an on-going basis to keep our company in OSHA compliance. -Created and implemented paperless file management and distribution system, saving the government $60,500 quarterly a 96 percent savings. Show less
-
-
Education
-
Southern New Hampshire University
Bachelor's degree, Business, Management, Marketing, and Related Support Services
Community
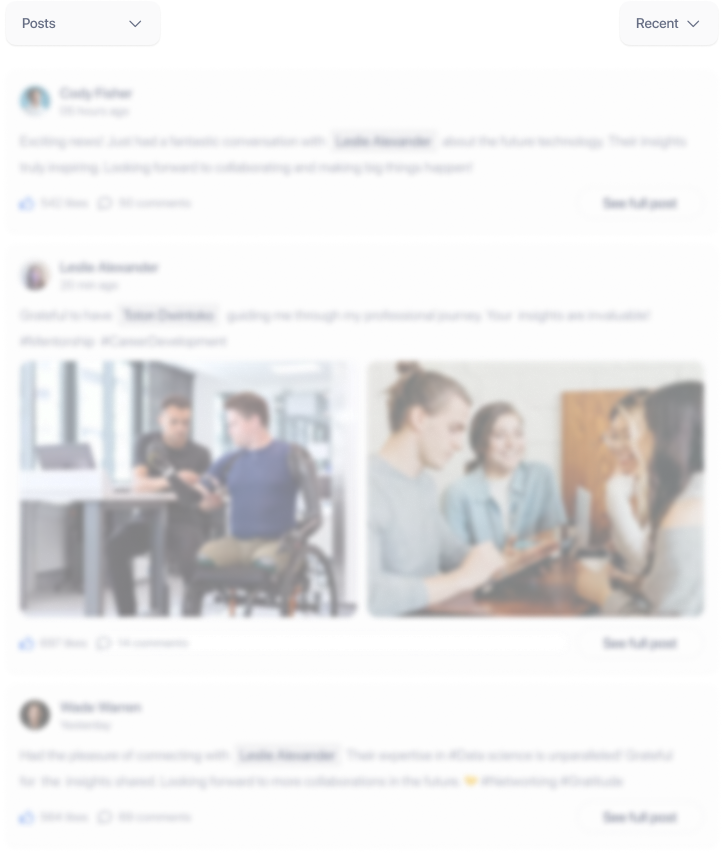