
Alex Blackhall
Project Manager at Northpower- Claim this Profile
Click to upgrade to our gold package
for the full feature experience.
Topline Score
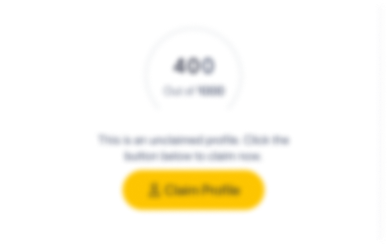
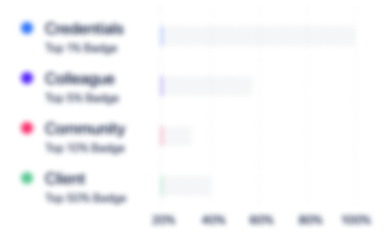
Bio


Experience
-
Northpower
-
New Zealand
-
Utilities
-
500 - 600 Employee
-
Project Manager
-
Sep 2022 - Present
Project manager of Volumetric Transmission Works on Transpowers Network, mainly re-insulation and Attachment Point replacement. Project manager of Volumetric Transmission Works on Transpowers Network, mainly re-insulation and Attachment Point replacement.
-
-
-
Electrix
-
New Zealand
-
Utilities
-
200 - 300 Employee
-
Contract Manager
-
May 2020 - Sep 2022
-
-
Estimator
-
Jan 2015 - May 2020
Preparing estimates in system for regional TP maintenance contract.Liaise with clients over defects and urgency.Work closely with planner in rolling four month program.Collating quotes from sub-contractors and suppliers.Monitor task productivity for accuracy of estimates.Preparation of invoicing sheets for administrators.Managing job variations with clients.Ensuring contractual invoicing dates are met.Coordinating with customers, field staff, management and sub-contractors to ensure project success.Ensuring all relevant HSEQ are priced for and achieved.Assist Contract Manager with month end reporting on job status and financials
-
-
Leading Hand
-
Oct 2013 - Dec 2014
I ran a field based crew of up to seven line mechanics. This meant doing any aspect of transmission de-energised field work anywhere in NZ. This included fault patrols, condition assessment, maintaining and upgrading for our client (Transpower) the 100/220kV assets, as well as assisting with substation builds for our PSD division.
-
-
-
-
Assembly and Erection Supervisor
-
Nov 2009 - Oct 2013
My role involved the supervision of assembly and erection field staff building transmission towers on various projects in Australia and NZ. These were divided into crews with cranes plus an aerial revision crew. I was tasked with the day to day running which included safety, crane selection (size, radius, etc), landowner entry in places, quality, site document compliance, steel delivery and basic HR whilst maintaining production rates with the best possible quality. Daily reporting was to my construction manager.Supervision of up to seven field crews including internal as well as Sub contractorsCommitment to the zero-harm philosophy Devised and implemented document and process changes saving approx. 160kProduced a cost benefit analysis for the NIGUP welfare facilitiesPart of the team responsible for writing and updating WI / JHA / SWMS / SHAOwnership of the work programSite set up ‘walk overs’ for enabling worksAssessing sites for crane sizeLiaising with Sub-contractors regarding crane costs, availabilityAmending work program as necessaryNominated for Star Award two years runningReduced working aloft time through assembly innovationCoaching and mentoring field staffEnsuring client specifications were metDaily supervision meetingsCompletion of all relevant paperwork Ensure land owner disruptions are kept to a minimum, through planningHonest and politeness to Landowners and client representativesSimplified lifting charts to make them easier to read and minimise weight errors
-
-
-
Electrix
-
New Zealand
-
Utilities
-
200 - 300 Employee
-
Supervisor
-
2006 - 2009
From the information gained from various sources such as the Condition Assessment reports, Patrol reports and product alerts I had to plan and program maintenance work for the work crews. Priority had to be given to faults that were imminent failures or in high risk areas such as road crossing. A rolling four month plan was required monthly by the client. Some issues captured required scoping. I had to input all the jobs into their system including an estimate for approval far enough ahead to ensure materials were ordered in time. I also had to order the materials and check them on delivery. Work had to be programmed to fit into existing outages if required and Live Line work had to have its own approval. Consideration had to be taken of the type of work and the seasons as well as the possible impact on the landowners businesses. Crews had to be assembled on a combination of factors such as, availability, skills, tickets, numbers and workload. This role required a lot of liaising with fellow office staff, field staff, subcontractors, client representatives, land owners and suppliers. Program maintenance schedule to keep to a four month rolling programWork within an annual budgetPrioritise defects as requiredRequest system outages were requiredPlan work including live line work to minimise outagesEnsure work teams have sufficient competencies to work safelyEstimate and enter defects into ours and the clients systemLiase with engineering to ensure correct materials are orderedComply with all current client specificationsAttend monthly client contract meetingAttend annual five and 10 year rolling asset management meetings with clientHave a full time emergency fault patrol plan for unscheduled outagesEnsure the fault patrol plan is activated in a timely fashionDeliver value for money for the client through reducing wasteComplete relevant paperwork on time
-
-
-
Balfour Beatty plc
-
United Kingdom
-
Construction
-
700 & Above Employee
-
LE1
-
2000 - 2006
• Hazard Identification Training• Safe Climbing Techniques• Tower Rescue Training• Emergency First Aid• Safe use of fire extinguishers• Tower erection and dismantling using a crane• Clear and receive permits• MEWP licence• Telescopic handler licence• Puller / tensioner licence• Sit in and sit on all terrain vehicle licences• Slinger signaller• Use of method statements, procedures and risk assessments• Installation of portable drain earths and DRESS schemes• De-spacing and spacing twin, triple and quad bundled conductors• Raising and lowering of working platforms• Replacement of suspension and tension insulator sets• Making mid span and dead end conductor joints on ACSR and AAAC conductors• Setting up equi-potential zones• Installation of anti climbing devices• Procedures for catching off conductors to ground anchors• Use of CCS system• Pulling pilot wires• Competent user of hand tools including chain saw, rotor broach, stihl saw, capstans, portable winches and hydraulic presses• Conductor removal and Tower demolition• Manual Handling
-
-
-
-
Mast Officer
-
1997 - 1998
Supervised the heightening of telecommunication and scientific masts during the summer maintenance whilst at Halley Base, Antarctica.• Planning summer works• Day to day running of a four man team• Annual stocktake• Submit the next year’s material requirements• Record keeping Supervised the heightening of telecommunication and scientific masts during the summer maintenance whilst at Halley Base, Antarctica.• Planning summer works• Day to day running of a four man team• Annual stocktake• Submit the next year’s material requirements• Record keeping
-
-
Education
-
Berwick upon Tweed
Community
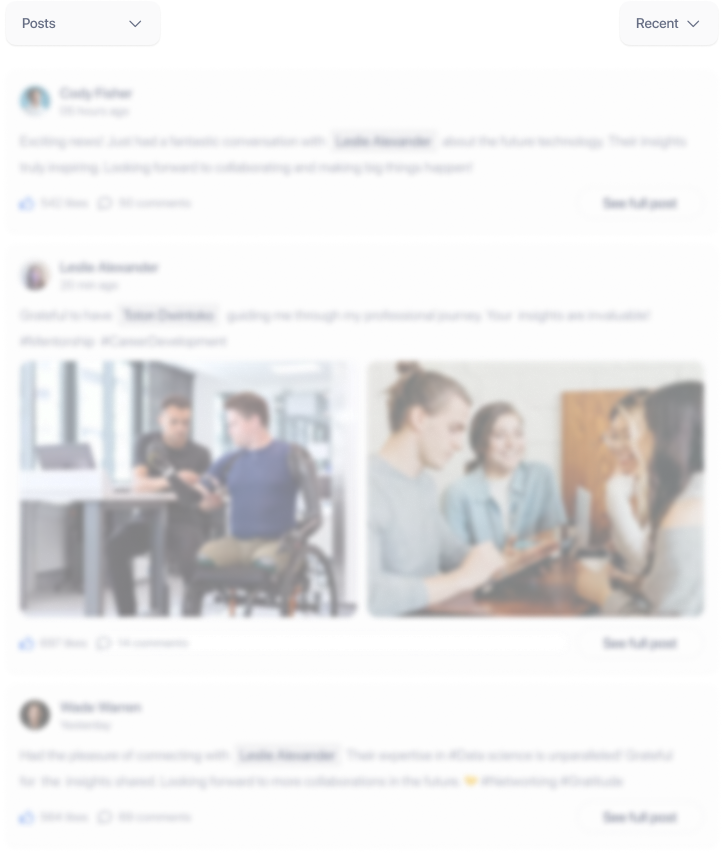