Alejandro Perales
Quality Manager at MacroFab- Claim this Profile
Click to upgrade to our gold package
for the full feature experience.
Topline Score
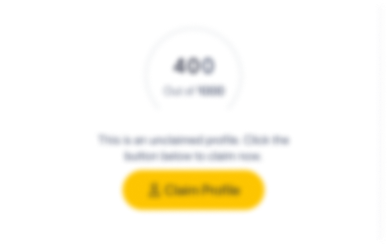
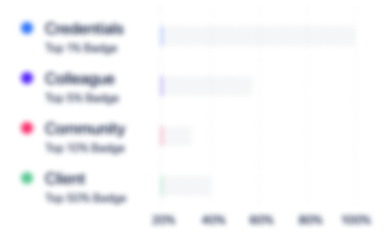
Bio


Experience
-
MacroFab
-
United States
-
Appliances, Electrical, and Electronics Manufacturing
-
100 - 200 Employee
-
Quality Manager
-
Mar 2023 - Present
- Establish key metrics for the evaluation of CM's. - Establish quality policy as well as objectives in terms of sigma level. - Development of early involvement with CM's and engineering supervision to ensure quality levels. - Establish process quality engineering, inspection systems and supplier management internally and with CM's. - Data analysis on a daily basis to measure KPI's. (DPPMs, Failure rate, top offenders, CM's failure trend, customer complaint and DPPM's with customer and final user) - Implementation of the 8D format to answer customer complaints and to handle complaints to CM's and or partner factories. -DPPM's failure trend 4Q implementation to measure and evaluate weekly basis performance and the effectiveness of the action plan. Show less
-
-
-
Flex
-
United States
-
Appliances, Electrical, and Electronics Manufacturing
-
700 & Above Employee
-
-
Apr 2022 - Mar 2023
Management and administration of resources for 4 clients.• Supervision of KPI's of 4 clients such as performance, scrap, client complaints, defective parts per million and material returned from the client.• Focus on continuous communication with the client.• Ensuring correct introduction of NPI's by monitoring procedures and key activities.• Ensure validation of project basics, as well as its APQP package.• Decision making for continuous production without affecting quality.• Standardize padlocks and systemic poka yokes.• Metric review of internal and external corrective actions.• Cost reduction projects through analysis of actions without added value using the VSM tool.• Training of quality engineers.Achievements through Kaizen methodology• Leader: Reduction of 12.5% of the assembly quality staff for a client.• Leader: Reduction of in process scrap by means of poka yoke for PCB's OSP – Savings of USD $5,200.00 per month.• Leader: Head count reduction for PTH adjustment. Savings of USD $600.00 per month. Show less
-
-
-
2018 - Mar 2023
Key CompetenciesData analysis / Management and communication with customer / Continuous improvement / Root cause approach / Problem solving / Operational controls / Metrics analysis / Leading improvement projects / Teamwork / Focus on automation / Staff growth / Report handlingActivities:• Lead daily and weekly meetings for the continuous improvement of the project metrics.• Follow-up to customer complaints and feedback.• Use and quarterly update of control plan and PFMEA based on customer requirements and improvements implemented in the process.• Follow-up to customer metrics such as scorecard, feedback from RMA’s and DPPM’s.• Constant involvement in KAIZEN and Lean activities for the implementation of systematic improvement activities.• Implementation of systems for traceability, measurement, poka yokes and controls through automation.• Direct customer service during complaints using 8D methodology with a focus on root cause analysis using Ishikawa and 5W.• Experience in new part number’s introduction, from local transfers, to transfers from the same site and / or customers sites.• Experience in development, creation, and involvement of deep analysis for problems that require decision making, both to improve internal metrics and / or customer’s metrics.• Involvement with CFT for reaction plans that do not affect neither OTD nor product quality.• Permeate a culture of quality, analysis, and improvement in the work team. Show less
-
-
Education
-
ITESO Universidad Jesuita de Guadalajara
Licentiate degree, Engineering/Industrial Management
Community
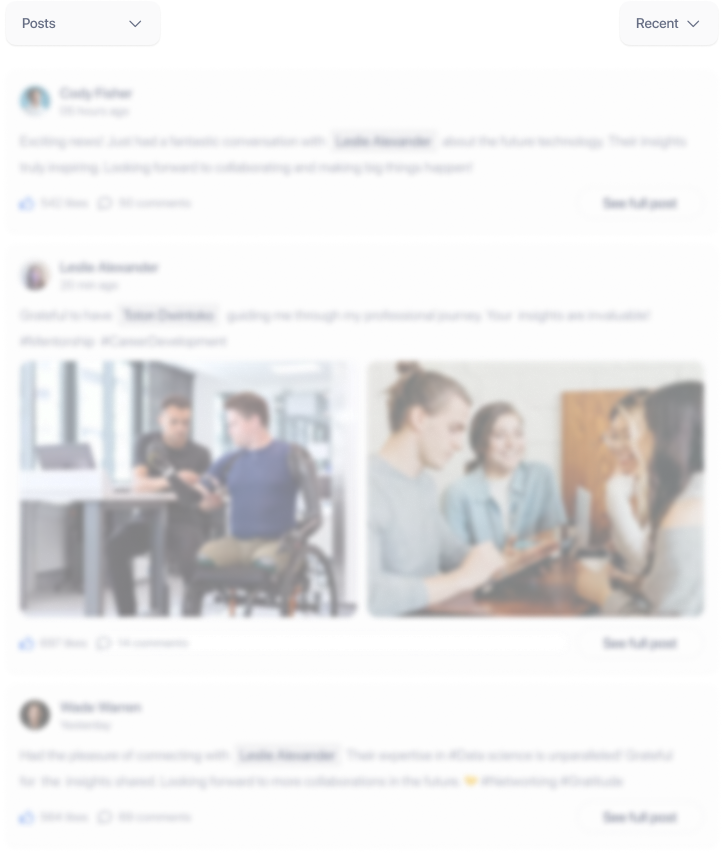