Alan Murray
Director Of Engineering at Red Mesa Science & Refining- Claim this Profile
Click to upgrade to our gold package
for the full feature experience.
Topline Score
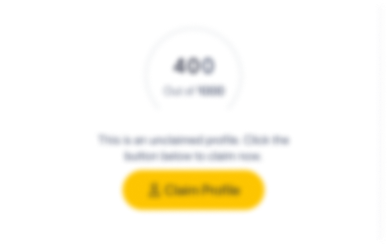
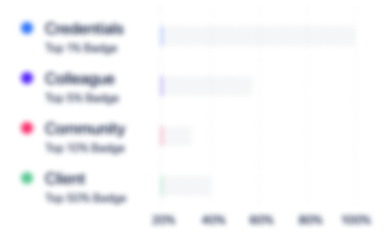
Bio


Credentials
-
ISO9000 Quality Auditor
Det Norske Veitas
Experience
-
Red Mesa Science & Refining
-
United States
-
Biotechnology Research
-
1 - 100 Employee
-
Director Of Engineering
-
Mar 2022 - Present
-
-
-
First Solar
-
United States
-
Renewable Energy Semiconductor Manufacturing
-
700 & Above Employee
-
Global Replication Manager
-
May 2017 - Mar 2022
Responsible for managing the global replication engineering team to implement new equipment and processes. Manage the process of capital equipment acquisition, fabrication, installation, start-up, and production ramp. Responsible for the overall project management, execution to timeline and the key interface with tool vendors. Lead troubleshooting activities, develop continuous improvement roadmaps to ramp equipment and process performance to achieve production output goals. Define project… Show more Responsible for managing the global replication engineering team to implement new equipment and processes. Manage the process of capital equipment acquisition, fabrication, installation, start-up, and production ramp. Responsible for the overall project management, execution to timeline and the key interface with tool vendors. Lead troubleshooting activities, develop continuous improvement roadmaps to ramp equipment and process performance to achieve production output goals. Define project requirements, develop specifications, and develop robust manufacturing equipment and processes. Partner closely with development Engineering, Sustaining Manufacturing engineering and Facilities Engineering teams
-
-
Global Replication Manager
-
May 2017 - Mar 2022
-
-
Manufacturing Engineer, Manufacturing Capital Equipment
-
Aug 2010 - Jun 2017
Lead teams and collaborate with Development Engineering in development of robust, manufacturable processes. Define requirements, evaluate, install, and qualify new process equipment. Managed projects ranging in duration from a month to a year and costing between $100K to $100M. Rolled out projects in US, Germany and Malaysia. Troubleshoot day-to-day manufacturing issues on production line. Identify and implement continuous improvements that contribute to achievement of throughput… Show more Lead teams and collaborate with Development Engineering in development of robust, manufacturable processes. Define requirements, evaluate, install, and qualify new process equipment. Managed projects ranging in duration from a month to a year and costing between $100K to $100M. Rolled out projects in US, Germany and Malaysia. Troubleshoot day-to-day manufacturing issues on production line. Identify and implement continuous improvements that contribute to achievement of throughput, yield, and product performance goals. Develop, continually improve, and document manufacturing processes to achieve product performance. Inject manufacturing requirements to new process developments. Design and execute planned process experiments, collect and analyze data and report results. Leads task forces and communicate status updates to stakeholders. Champion continuous improvement activities using Six Sigma and other statistical problem-solving methods. Resolve day-to-day production, equipment, and process problems. Identify training needs and provide training to other engineers, techs and associates. Develop Process Control Plans and Preventive Maintenance Plans. Replicate capital equipment into factory expansions, retrofitting current equipment to meet “copy smart” requirements, and provide continuous improvement of equipment performance. Evaluate manufacturing processes by designing and conducting equipment testing, applying knowledge of product design, fabrication, assembly tooling and materials. Collaborate with equipment vendors from concept design, to build, to completion of pre-delivery demonstration of equipment prior to implementation. Design, develop and implement engineering changes (ECRET’s/ECO). Collaborate with purchasing and tool vendors for capital acquisition. Track tool changes and tool performance to determine future areas of focus for improvement. Follow FMEA principles for continuous improvement and risk mitigation.
-
-
-
Acelity
-
United States
-
Medical Equipment Manufacturing
-
700 & Above Employee
-
Field Repair Technician
-
Sep 2009 - Aug 2010
Provided corrective and preventative maintenance of KCI’s Frame products in Utah, Idaho and Montana. Offered remote resolution and onsite support to service centers within the region. Supervised bed refurbishment project for three-state region. Managed spare parts inventory for four service centers. Trained service consultants onsite for simple repairs and maintenance. Worked directly with customers to provide support and troubleshooting. Documented all repairs, tracking of… Show more Provided corrective and preventative maintenance of KCI’s Frame products in Utah, Idaho and Montana. Offered remote resolution and onsite support to service centers within the region. Supervised bed refurbishment project for three-state region. Managed spare parts inventory for four service centers. Trained service consultants onsite for simple repairs and maintenance. Worked directly with customers to provide support and troubleshooting. Documented all repairs, tracking of retrofits, and trending of issues. Managed medical device equipment configuration to maintain regulatory compliance. Implemented “Copy Smart” program to improve equipment performance and reliability. Show less Provided corrective and preventative maintenance of KCI’s Frame products in Utah, Idaho and Montana. Offered remote resolution and onsite support to service centers within the region. Supervised bed refurbishment project for three-state region. Managed spare parts inventory for four service centers. Trained service consultants onsite for simple repairs and maintenance. Worked directly with customers to provide support and troubleshooting. Documented all repairs, tracking of… Show more Provided corrective and preventative maintenance of KCI’s Frame products in Utah, Idaho and Montana. Offered remote resolution and onsite support to service centers within the region. Supervised bed refurbishment project for three-state region. Managed spare parts inventory for four service centers. Trained service consultants onsite for simple repairs and maintenance. Worked directly with customers to provide support and troubleshooting. Documented all repairs, tracking of retrofits, and trending of issues. Managed medical device equipment configuration to maintain regulatory compliance. Implemented “Copy Smart” program to improve equipment performance and reliability. Show less
-
-
-
Applied Materials
-
United States
-
Semiconductor Manufacturing
-
700 & Above Employee
-
Operations Manager
-
Jun 2006 - Jan 2009
Oversaw successful start-up of a new field support operation at an Intel-Micron green field site. Hired, trained, and developed team of 26 employees in fewer than six months. Served as interface between customer and Applied Materials Engineering teams, as well as local safety manager to ensure all safety regulations were met. Planned and implemented site readiness activities to intercept customer first production start date. Managed equipment Installation projects of 57 tools and three… Show more Oversaw successful start-up of a new field support operation at an Intel-Micron green field site. Hired, trained, and developed team of 26 employees in fewer than six months. Served as interface between customer and Applied Materials Engineering teams, as well as local safety manager to ensure all safety regulations were met. Planned and implemented site readiness activities to intercept customer first production start date. Managed equipment Installation projects of 57 tools and three different product types in less than 15 months, as well as installation of 1st and 2nd of a kind tools on time for initial production. Strived for customer satisfaction and successful report card, which encompassed areas of Safety, Cost, Equipment Installation, Equipment Performance, Quality, Spares and Engineering CIP (Continuous Improvement Programs). Responsible for successful customer quarterly business reviews. Worked with customer and engineering to maintain “Copy Smart” program on all tools coming in to fabrication facility. Conducted tool configuration meetings with the customer. Conducted pre-installation meetings to manage customer’s critical timelines and schedules. Managed capital equipment installation and warranty budgets to maintain financial targets. Led CIP activities in CVD, Etch and RTP teams. Ramped successful equipment output performance to 11K WSPM (Wafer starts per month) ahead of schedule. Drove improvements in quality, spares support, and customer satisfaction, which resulted in customer scorecard improvements over 6Q by a total of 19% points.
-
-
Operations Manager
-
Oct 2004 - Jun 2006
Managed of all aspects of strategic and tactical activities of both an R&D center, as well as three production facilities at Micron headquarters in Boise, ID, as well as managed installation and warranty budgets of over 30 tools to meet budget requirements. Hired, trained, and developed team of 15 employees. Planned and implemented readiness activities for installation and warranty support of over 30 production tools in two-year span. Took on customer-facing role managing new tool… Show more Managed of all aspects of strategic and tactical activities of both an R&D center, as well as three production facilities at Micron headquarters in Boise, ID, as well as managed installation and warranty budgets of over 30 tools to meet budget requirements. Hired, trained, and developed team of 15 employees. Planned and implemented readiness activities for installation and warranty support of over 30 production tools in two-year span. Took on customer-facing role managing new tool introductions through evaluation period to achieve final selection for high volume manufacturing (HVM). Handled formulation of product improvement and cost of ownership roadmaps to ensure tool performance specifications were met. Directed transfer of technology from development facilities to HVM sites. Negotiated successful service contracts into production fabs. Improved tool performance metrics by over 10% in availability and utilization.
-
-
Lead Customer Engineer
-
Oct 1994 - Oct 2004
Field Service Engineer responsible for start up and warranty support of advanced semiconductor manufacturing equipment. Conducted all Preventative and Corrective maintenance on the systems during the warranty periods. Built solid relations with the customer. Used advanced troubleshooting techniques to resolve complex issues.
-
-
Quality Manager
-
Feb 2002 - Oct 2003
Tracked and verified all closed loop corrective actions for all system non-conformances at Boise site. Gained ISO-9001 certification and implemented business processes into Quality Management System(QMS). Completed external DNV audit of site to complete ISO9001 certification with zero findings, as well as completed Det Norske Veritas (DNV) auditor certification Developed and implemented over 50 QMS procedures for local office and loaded into corporate QMS database.
-
-
Education
-
DeVry University Phoenix, AZ
Bachelor of Science EET, Electrical and Electronics Engineering -
DeVry Institute of Technology
BSEET
Community
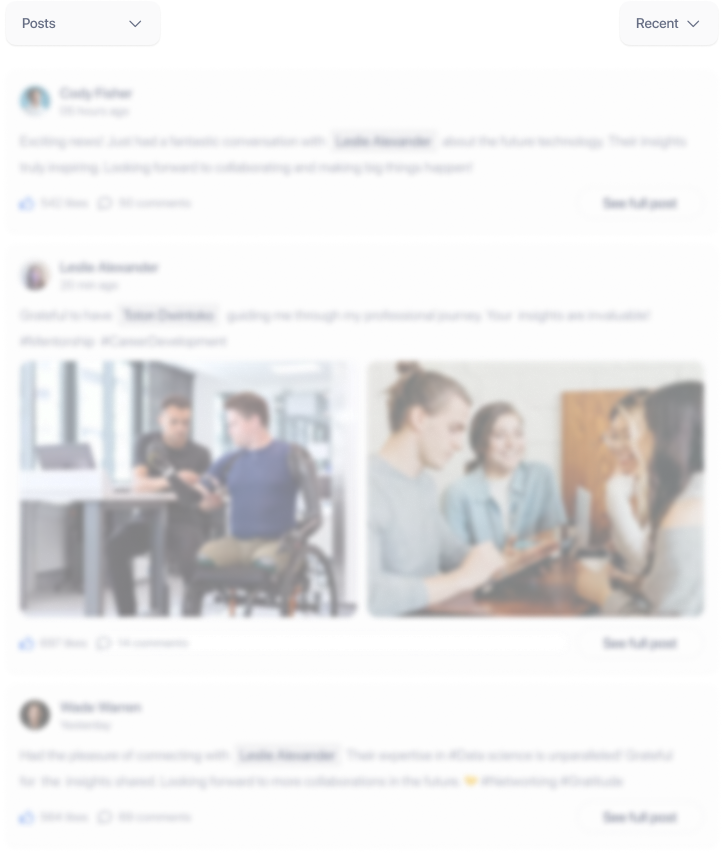