Alan McMillen, CSSGB
Manager - Disposables Production at Acutus Medical, Inc.- Claim this Profile
Click to upgrade to our gold package
for the full feature experience.
Topline Score
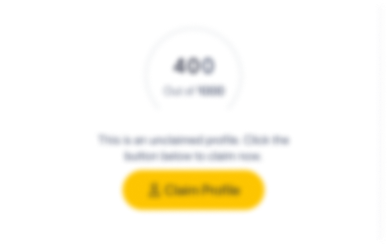
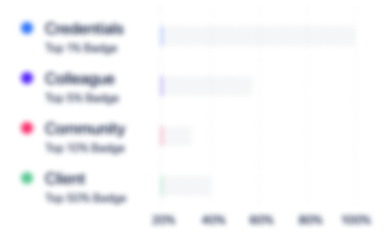
Bio
0
/5.0 / Based on 0 ratingsFilter reviews by:
Credentials
-
Six Sigma Green Belt (CSSGB)
ASQ - World HeadquartersAug, 2023- Sep, 2024
Experience
-
Acutus Medical, Inc.
-
United States
-
Medical Equipment Manufacturing
-
100 - 200 Employee
-
Manager - Disposables Production
-
Mar 2023 - Present
-
-
Associate Manager - Disposables Production
-
Feb 2022 - Mar 2023
-
-
Production Supervisor
-
Jun 2021 - Feb 2022
-
-
-
B. Braun Medical Inc. (US)
-
United States
-
Medical Equipment Manufacturing
-
700 & Above Employee
-
Production Supervisor
-
Sep 2020 - Mar 2021
Manage all operations of creating IV bag solutions from start to finish. Assemble film and caps together by plastic welding seals to manufacture the bag itself. Fill IV bags with various pharmaceutical solutions to ensure appropriate ratio of solution to air volume. Package bags into cardboard over cartons and ensure palatalization of delivery to warehouse. Ensure quality control through various leak tests, visual inspections, microbiology and chemistry testing, as well as monitoring machine setting. Following continuous improvement strategies to identify, implement, and improve all operations of the department. Utilize APQ to analyze performance and ensure various metric targets are being achieved on time. Collaborate with supply chain teams to ensure optimal scheduling in all three areas to meet demand. Develop a team of 54 team members to optimize process operations, output, and total costs. Ensure daily GMP, ISO, cleanroom, and EHS compliance while conducting daily GEMBA walks. Show less
-
-
-
Applied Medical
-
United States
-
Medical Equipment Manufacturing
-
700 & Above Employee
-
Production Supervisor
-
Sep 2016 - Sep 2020
Created a graphical aid project that was implemented by the company, and is now used in all manufacturing plants, which reduced the plants monthly scrap cost by over 50%. Lead a 5S and S.M.E.D. project that resulted in reducing overall plant downtime by 17%. Reduced WIP inventory by over $400,000. Reduced manufacturing costs on hundreds of components, some by over 75%. Recognized by the company for reducing manufacturing costs and increasing output of Alexis Laparoscopic Systems, as well as successfully graduating from Operations Leadership Level I and II development programs. Managed all plant operations including injection molding, liquid injection molding, metal injection molding, insert molding, pad printing, and all rework. Forecasted, planned, and scheduled components to run across various machine groups to minimize down time, while increasing efficiency and output. Identified and implemented process improvements across all operations of the plant to increase output and efficiency, while reducing scrap and overall cost. Worked with all cross functional teams such as engineering, quality, and clinical development on a daily basis to improve quality and ensure timely project completions. Developed a team of 24 team members, continuously enhancing their knowledge, skills, abilities, while strengthening team cohesion and ensuring individual professional growth and opportunities. Lead audits ensuring good manufacturing practices and ISO requirements were in compliance. Show less
-
-
-
ASI Inc.
-
Human Resources Services
-
1 - 100 Employee
-
Concert Technician
-
Apr 2014 - Dec 2015
Communicated with clients to ensure the stage was set up to exceed the needs and ensure safety of all performers. Designed and executed entertaining and technical audio and visual optimizations to produce the best show possible. Managed a team of five employees to ensure that individual and group tasks were assigned to best suit the clients needs and desires.
-
-
Rockwall Attendant
-
Aug 2014 - May 2015
Worked as a team player to help ensure that every client received the best and safest experience possible. Actively sought out and engaged potential clientele to improve the number of weekly/monthly clients. Continually taught new and existing clients the necessary skills and techniques needed to advance their rock climbing expertise. Maintained a safe environment for all clients, and ensured all equipment was in good working order to be safely utilized.
-
-
-
McMillen Builders Inc.
-
United States
-
Construction
-
1 - 100 Employee
-
Assistant Contractor
-
Jun 2007 - Aug 2015
Built custom homes to client specifications from framing to finish using various machinery and tools. Managed strict deadlines by subcontracting tasks out, and creating schedules for timely completion. Resolved problems with clients, designers, and engineers by communicating needs and restrictions. Built custom homes to client specifications from framing to finish using various machinery and tools. Managed strict deadlines by subcontracting tasks out, and creating schedules for timely completion. Resolved problems with clients, designers, and engineers by communicating needs and restrictions.
-
-
Education
-
California State University-Fullerton
Bachelor of Business Administration (B.B.A.), Business Administration and Management, General
Community
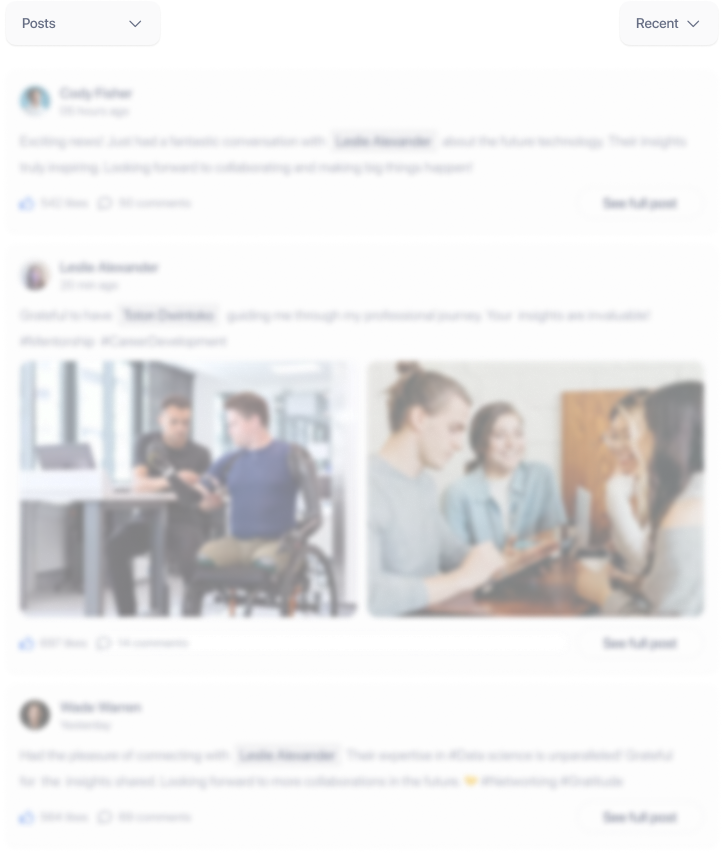