Alan Kuai
Senior Supplier Quality Engineer at Heraeus Materials Singapore Pte Ltd- Claim this Profile
Click to upgrade to our gold package
for the full feature experience.
Topline Score
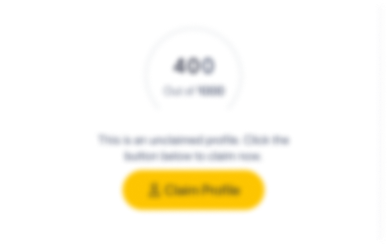
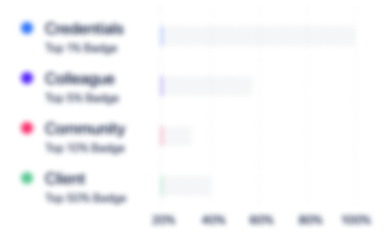
Bio


Experience
-
Heraeus Materials Singapore Pte Ltd
-
1 - 100 Employee
-
Senior Supplier Quality Engineer
-
Nov 2021 - Present
Led new suppliers qualification, system/process audits, established quality agreement and supplier advance product quality planning (APQP/PPAP) by assessing manufacturing/technology capabilities and Health, Safety and Environmental risks. Drove supplier quality issue, KPI, SCAR% and follow up on the action closure using 8D methodology. Support in new Product development processes to ensure supplier process capability is effective to meet product and process requirements. Key Accomplishments: • Qualified potential suppliers to achieve cost down and strengthen supply chain. • Maintained supplier performance complained rate at 0.3%. • Review and evaluate supplier quality data to identify improvement opportunities.
-
-
-
3D Systems Corporation
-
United States
-
Industrial Machinery Manufacturing
-
700 & Above Employee
-
Procurement Engineer
-
Feb 2020 - Dec 2020
Held overall responsibility for maintaining suppliers (CNC machining, sheet metal, plastic) key metrics to meet objectives related to cost, quality and delivery. Led cost savings initiatives with negotiation, alternate sourcing strategies and qualifying potential suppliers on offering competitive lead-time and pricing to obtain the maximum benefit for the company and satisfying customer. Serve as the technical liaison between suppliers and design team. Led root cause analyses to resolve supplier issues. Key Accomplishments • Resourced Asia suppliers mainly in Taiwan, Singapore and Malaysia to fend off tax tariff from China and achieved at least 20% cost saving. • Executed RFQ and submitted quote to customer (NA and EMEA) within 24 hours lead time. • Negotiated Pay Term moved from N45 to N60 for top spend suppliers.
-
-
-
Grand Venture Technology Limited
-
Singapore
-
Mechanical Or Industrial Engineering
-
1 - 100 Employee
-
Senior Supplier Quality Engineer
-
Aug 2019 - Feb 2020
Oversaw multiple suppliers (casting, machined part, surface finish treatment), ensuring quality standards achieved in all performance metrics. Prepared and presented supplier-related improvements at monthly plant meetings. Investigated and analyzed any manufacturing issues in regards to supplied components. Maintained optimized production levels and on-time customer deliveries. Key Accomplishments • Established and implemented Supplier quality management procedure (Suppler selection / qualification / scorecard). • Executed system audit to overseas suppliers mainly in China and Malaysia. • Led continuous improvement through regularly scheduled supplier assessments and closed loop 8D Supplier Corrective Action System.
-
-
-
Trend Technologies
-
United States
-
Industrial Machinery Manufacturing
-
300 - 400 Employee
-
Assistant Quality Assurance Manager
-
Dec 2018 - Jul 2019
Key Accomplishments • Developed and implemented corrective action to improve powder coating process for identifying problematic return issues resulting in prevention savings of $28,000. • Spearheaded customer focus team to implement customer satisfaction in fast response time within 24 hours. • Initiated with targeted suppliers on reducing non-conformances at below 1000 Dppm. Job Scope : • Led a group of Engineers on Incoming Inspection, In-process Inspection and Outgoing Inspection • Managed a group of Customer Focus Team Engineers – To support NPI (FAI / PPAP submission) and Handling of customer compliant / returned till corrective and preventive action taken (ie, 8D report), presenting to customer and following up internal on closure and monitoring the effectiveness. • Stood as the Company representative on following up all quality issues and product approvals during communications with vendors, customers and outside certification providers. • Drove continuous improvement on product quality performance to achieve all related company metrics (KPI). • Participated in audit from customer and ISO system certification and involved as internal auditor to assist team to achieve certification. • Reviewed FAI reports / PPAP submission and other periodic quality report as needed by customers and internal reporting. • Performed audit on suppliers, monitored the quality performance and assisted them in driving continuous improvement. • Attended 3rd parties and customer audit respectively, assisted in follow-up findings for corrective actions. • Reviewed quality procedures, instructions, checklist, control plan and quality related documents, and ensured they are followed accordingly and guiding in the interpretation of the quality plan to production team. • Ensured measuring equipment’s calibration as per master schedule. • Conducted all quality related training that include customer workmanship and specification. • Identified training needs for all QA staffs.
-
-
-
Xerox Corp
-
Business Supplies and Equipment
-
Senior Supplier QA/Procurement Engineer
-
Nov 2006 - Nov 2018
Key Accomplishments • Successfully led cost down activity to completion for combined annual savings of US$1.2M. • Optimized assembly fixtures, line balancing and poke-yoke processes at supplier site and led supplier improved daily output from 80 to 120 units. • Set quality performance improvement goal with problem suppliers and executed with them on reducing rejects to ensure they met target of 500 Dphm (Machine) / 1000Dppm (Parts). Job Scopes: • Supplier Selection – With joint effort of sourcing on aspect of quality, capability, pricing, delivery, etc • Supplier selection/qualification – Supplier self-assessment, Onsite system/process audit, • Part qualification (APQP) – Implement PPAP such as FAI, Process Capability study(CPK), Control Plan, FMEA, Process Parameter Sheet, Statistical Process Control chart(SPC), Measurement System Analysis(MSA/GR&R), RoHS / EHS compliance, COC, etc • Ensured incoming products from suppliers suitability for production and assembly • Investigated and followed-up quality issue with suppliers and ensure effectiveness closure on Corrective/preventive actions implementation to prevent recurrence (8D report) • Monitored suppliers monthly quality performance metrics such as Incoming/Outgoing Lot Acceptance rate, Production/Testing yield, Dppm, RMA, CAPAR, On-time delivery, etc • Provide training and guidance to suppliers such as SPC, MSA, etc. • Participated in development and launch of new products • Conducted Design For Manufacturing (DFM) prior to tool fabrication • Cost down initiatives - Reduced the UMC (Unit Machine Cost) of the parts, sub assemblies and modules thru engaging suppliers, discussion and share ideas.
-
-
-
Avaplas Ltd
-
Plastic Injection molding
-
Senior QA Engineer
-
Jun 2002 - Nov 2006
• Maintenance and Documentation of QS 9000 / ISO 9001:2000 / ISO 14001 System through electronic base system • Overseeing all Quality related problem in plastic molding products and assembly components • Managing the QA Clean Room Department (Mold Evaluation/First Article Submission/In-Process/Outgoing, Customer Complaint) • Initiated, replied and followed-up on effective corrective/preventive actions to customer • Interfaced with all relevant department in problem solving by effective used of failure analysis, problem solving, mistake-proofing and statistical techniques • Handled Customer complaints, returns and work with customers on special requirements • Performed Internal Quality Audit • Transferred knowledge and trained oversea plant for new project.
-
-
-
Minnesota Rubber Asia Pacific Pte Ltd
-
Rubber molding
-
Quality Assurance / Design Engineer
-
Jul 1996 - Jun 2002
• Managing the QA Department (Mold Evaluation/First Article Submission/Incoming /In-Process/Outgoing, Customer complaint) • Overseeing all Quality related problem in rubber molding products • Assisted Production in failure analysis and rectify mold problems • Supervising the Final Inspection Department (Sorting) • Maintenance of all Calibration Measuring Equipment • Aliasing with Customer/Supplier on Product Quality • Planned and Co-ordinated all Internal Quality Audit Program • Development, Maintenance and Documentation of QS 9000 System through electronic base system • Co-ordinated and established all Advance Product Quality Plan (APQP) documents: (Process Flow Chart, Control Plan, PFMEA, MSA, SPC, Cpk, etc) • Performed engineering work from design stage to final production • Liaised with Sales on developing finished product standards • Designed molds, jigs and fixtures and improve machine design • Planned and coordinated with tool room and mold vendors on new mold fabrication, tooling rework and tool maintenance
-
-
-
Sanyo Airconditioner Manufacturing (S) Pte Ltd
-
Aircon manufacturing
-
Quality Assurance Superintendent
-
May 1994 - Jul 1996
• Approval of First Article Sample • Liaising and Working with Supplier on Quality Improvement Programs • Assisting in areas of evaluating and qualifying alternative source components • Participated in Supplier Audit, Safety Audit, QCC and QAT • Maintenance of ISO 9002 • Approval of First Article Sample • Liaising and Working with Supplier on Quality Improvement Programs • Assisting in areas of evaluating and qualifying alternative source components • Participated in Supplier Audit, Safety Audit, QCC and QAT • Maintenance of ISO 9002
-
-
Education
-
University of Bradford
Bachelor of Science in Business and Management Studies -
Singapore Polytechnic
Diploma in Mechanical & Manufacturing Engineering
Community
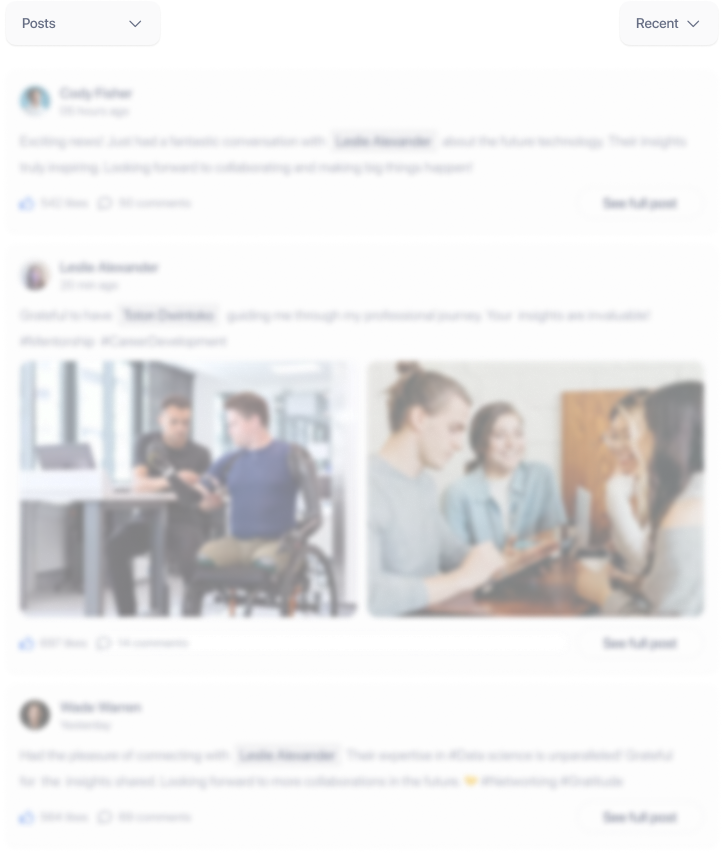