Ajie Revy Priambudi
Head of Quality Assurance Department at PT. Menara Terus Makmur- Claim this Profile
Click to upgrade to our gold package
for the full feature experience.
-
English Professional working proficiency
-
Indonesian Native or bilingual proficiency
-
German Elementary proficiency
-
Japanese Elementary proficiency
Topline Score
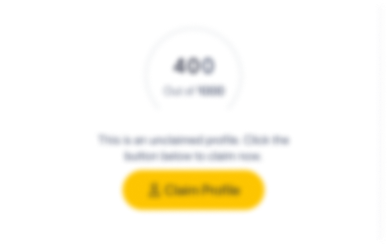
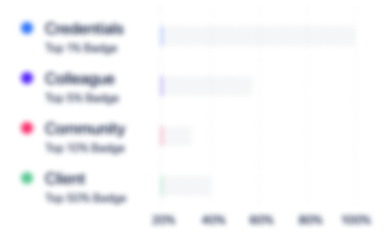
Bio


Experience
-
PT. Menara Terus Makmur
-
Motor Vehicle Manufacturing
-
1 - 100 Employee
-
Head of Quality Assurance Department
-
Feb 2022 - Present
Responsibilities : • Control supplier quality performances for mass production parts and control new product development in terms of quality by using PPAP approach • Control site quality performances for mass production parts and control new product development in terms of quality by using PPAP approach • Control calibration laboratory operational and performances • Ensure product quality management Responsibilities : • Control supplier quality performances for mass production parts and control new product development in terms of quality by using PPAP approach • Control site quality performances for mass production parts and control new product development in terms of quality by using PPAP approach • Control calibration laboratory operational and performances • Ensure product quality management
-
-
-
PT. Inti Ganda Perdana
-
Motor Vehicle Manufacturing
-
200 - 300 Employee
-
Head Of Quality Assurance Department
-
Jan 2021 - Feb 2022
Responsibilities :• Control supplier quality performances for mass production parts and control new product development in terms of quality by using PPAP approach• Control Quality Management System (ISO 9001 and IATF 16949) implementation• Control calibration laboratory operational and performances
-
-
Assistant Manager of Quality Engineering
-
Jun 2016 - Dec 2020
Responsibilities :• Develop quality management system (ISO 9001 and IATF 16949) • Develop supplier quality assurance system• Increase supplier quality performances for mass production parts and control supplier new product development in terms of quality by using PPAP approach • Ensure calibration laboratory operational and performances Achievements :• Established changing point management (henkaten kanri) tools for shop floor• Developed new product audit tools for the company and supplier• Developed supplier quality assurance manual• Developed new quality performance criteria for supplier • Led quality task force to avoid supplier upcoming issues• Initiated and established massive supplier quality audit system, process, and product• Developed virtual supplier quality audit scheme • Initiated quarterly quality appreciation for supplier• Developed new method to use and check FMEA and PPAP document• Initiated KPI for new product development projects in terms of quality• Initiated training measurement system analysis for supplier• Initiated voice of supplier (stakeholder) program• Led transition from ISO TS 16949 to IATF 16949• Developed new internal audit and review finding scheme• Developed sharing ISO 9001 and IATF 16949 material for shop floor• Led internal audit program• Led certification body audit program and achieved no major finding with minimum minor finding only• Developed company procedure manual with related department• Developed company system manual
-
-
Head of Quality Engineering Section
-
Mar 2016 - Jun 2016
Responsibilities:• Develop supplier new products in order to conform with schedule, drawing, and both IGP and customer requirements by using PPAP approach • Develop supplier in terms of quality performance for mass production parts Achievements:• Established process audit tools for supplier• Established process audit tools for IGP
-
-
Head of Research and Development Engineering Section
-
Jun 2013 - Mar 2016
Responsibilities:• Lead New Product Development projects by using APQP approach • Develop supplier new products in order to conform with schedule, drawing, and both IGP and customer requirements by using PPAP approach Achievements:• Propose and implement Unique Carrier Differential Machining Line layout for automation handling process (cost reduction)• Propose and implement Cover Differential check method in order to make improvement in casting supplier side• Propose and implement new Differential Parts design for easiness of machining process• Leader of Flywheel Parts development for Daihatsu passenger car• Develop casting supplier in term of Flywheel Parts for Daihatsu passenger car• Propose and implement new Flywheel design for easiness of casting and machining process• Propose and implement Flywheel check method in order to get correct measurement result of machining process• Propose and implement a Better Flywheel machining process to get good capability process• Leader of Ring Gear Part development for Toyota passenger car• Develop supplier regarding to Ring Gear Part for Toyota passenger car• Propose and implement Ring Gear check method in order to get correct measurement result of raw material process (in supplier side)• Leader of Hub Front Part localization for Suzuki passenger and commercial car• Develop forging supplier in respect of Hub Front Part for Suzuki passenger and commercial car• Propose and implement New Hub Front design for easiness of forging and machining process• Leader of Side Bearing Nut development Part for Toyota passenger car• Develop stamping supplier in term of Side Bearing Nut for Toyota passenger car• Propose and implement Side Bearing Nut stamping process to get good part
-
-
Head Of Application Engineering Section
-
Jun 2012 - Jun 2013
Responsibilities:• Lead new product development projects by using APQP approach • Develop supplier new products in order to conform with schedule, drawing and both IGP and customer requirements by using PPAP approach Achievements:• Leader of Differential Parts localization project for Mitsubishi commercial car• Develop casting supplier in term of Differential Parts for Mitsubishi commercial car• Save cost during development activity of Differential Parts for Mitsubishi commercial car around IDR 750 million• Leader of Hub Front Parts development for Suzuki passenger car• Develop forging supplier in respect of Hub Front Parts for Suzuki passenger car• Leader of Knuckle Parts localization project for Hino Small Truck• Develop forging supplier in term of Knuckle Parts for Hino Small Truck• Leader of Differential Parts development for Hino Medium Truck• Develop casting supplier regarding to Differential Parts for Hino Medium Truck
-
-
Head of Testing and Validating Engineering Section
-
Jun 2011 - Jun 2012
Responsibilities:• Conduct test and validate products in order to conform with drawing or other customer requirements• Product failure analysisAchievements:• Design test method and jig for Rear Axle (Housing) of Daihatsu passenger car• Develop and design Center Bearing Support for Propeller Shaft of Toyota passenger car• Contribute as a leader of Rear Axle Assy Durability Test for Toyota passenger car• Contribute as a leader of Propeller Shaft Assy Noise Test for General Motor passenger car• Able to prove broken Axle Shaft of Hino Truck due to end customer usage with failure analysis method
-
-
Education
-
Institut Teknologi Bandung (ITB)
Bachelor's Degree, Mechanical Engineering
Community
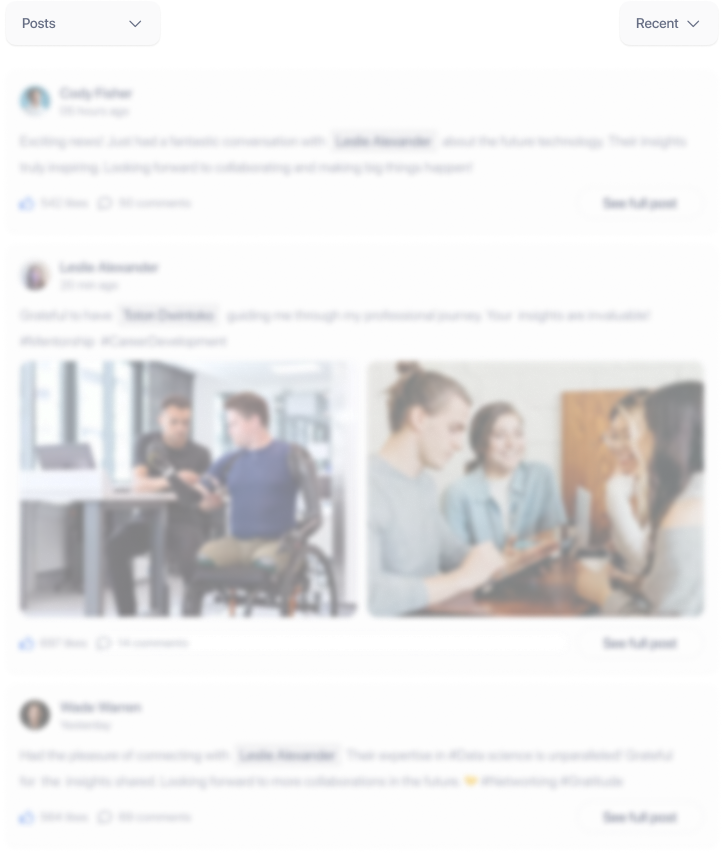