Ain Syuhada
Engineer at TDK (MALAYSIA) SDN BHD- Claim this Profile
Click to upgrade to our gold package
for the full feature experience.
Topline Score
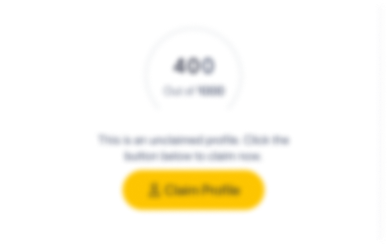
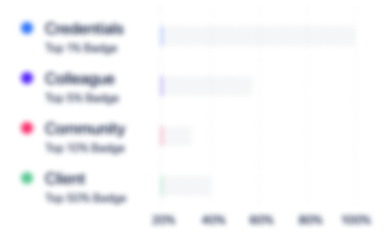
Bio


Experience
-
-
Engineer
-
-
PCA Group Sdn Bhd
-
Malaysia
-
Industrial Machinery Manufacturing
-
100 - 200 Employee
-
QA Engineer
-
Oct 2019 - Apr 2022
• Plan, arrange and monitor daily manpower activities • Contribute in New Product Development stage which are related to Quality scope. • Contribute in Product Certification (In-charge) for CE, UL, IEC 80079-34-2018 • Carry out internal audit for ISO9001:2015, ISO14001:2015, ISO 45001:2015 (OHSMS), all product certification. • Investigate and analyse customer complaints on cause root cause, corrections, corrective actions and action plan. • Liaise with supplier on the quality improvement plan under Vendor Development Program • Publish Monthly Quality Report to be review in the Monthly Management Meeting. • Plan, monitor and update Measuring Equipment Calibration Record. Show less
-
-
-
C.S Yap Engineering Sdn Bhd
-
Malaysia
-
Construction
-
1 - 100 Employee
-
QA Engineer
-
Jun 2016 - Dec 2017
• Respond to customer complaint by conducting Root-Cause Analysis and arrange for Immediate Action Plan for internal activity. • To achieve target of 5 working days or less in replying the 8D/Why why analysis report. • Handle Internal and Customer Audit. • SPC study, MSA & Familiar with 7 QC tools • KPI Monthly/Yearly Report Analysis • In-charge of handling Document Control Center (DCC) by ensuring all procedures comply to ISO 9001(QMS). • Create a ISO Documentation - Work Instruction (WI) and Standard of Procedure (SOP) • Coordinate and manage the overall preparation for supplier, internal and external ISO 9001 Audit. • Handle Management Review Meeting preparation by compiling data, final report, meeting agenda and monitor follow-up action of meeting outcome. • Provide training for knowledge enhancement program to all QC Inspector and Production staff. • Handling Internal and External (Outsource) Calibration activity such as QC testing equipment, Qc measuring tools (measuring tape, Digital Caliper, etc) and Jig/fixtures. Show less
-
-
-
Unisteel Technology Limited
-
Singapore
-
Appliances, Electrical, and Electronics Manufacturing
-
100 - 200 Employee
-
Customer Quality Engineer
-
Oct 2014 - Feb 2016
As a window for Toshiba customer (Philippine and Japan) regarding Quality/ Documentation support upon queries. •To assist customer to achieve ‘Supplier Quality Performance Rating > 90% • To achieve target of 7 working days or less in replying the 8D report. • To review and study about customer needs before explain to internal team. • To lead and manage internal team in order to meet customer requirements or technical issue. • To work together with internal team on continuous process improvement. • To coordinate/investigate the root cause and corrective action with respective team and reply the 8D report to customer between timeline. • To commit the periodical report to customer after verification from HOD. • To conduct internal audit prior to customer visit. • To closely collaborate with Supplier Quality Engineer, to ensure the supplier achieve the customer specification. • To quickly respond to customer enquiries beyond customer expectation. Show less
-
-
Education
-
Universiti Tun Hussein Onn Malaysia
Bachelor's degree, Mechanical Engineering
Community
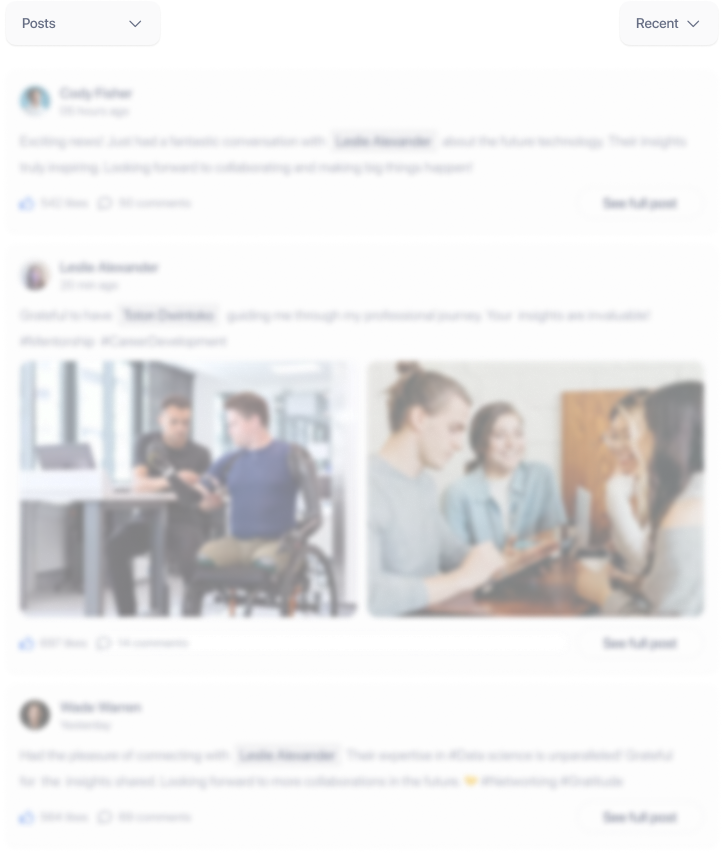