Ahmed Ezzat
DCS Operator at شركة البترول الوطنية الكويتية Kuwait National Petroleum Company- Claim this Profile
Click to upgrade to our gold package
for the full feature experience.
-
English -
Topline Score
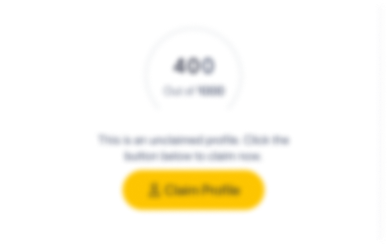
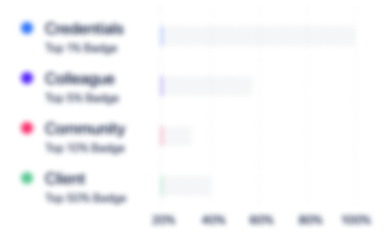
Bio


Experience
-
شركة البترول الوطنية الكويتية Kuwait National Petroleum Company
-
Kuwait
-
Oil and Gas
-
700 & Above Employee
-
DCS Operator
-
Jul 2012 - Present
DCS Operator ( CDU) ° I am working in KNPC ( Clean Fuel Project) at1- Crude Distillation Unit ( CDU).Capacity 264,000 BPSD The Technology Licensors for CDU are Open Art-Fluor Technology. • Monitors and operates equipment and processes in the assigned area inaccordancewith operating instructions. • Operate DCS control to coordinate and regulate process variables and to direct flowrates of various process and utility streams according to schedules. • Pre-heat train to increase Temperature gradually from 130 F° to 560 F° to decreaseViscosity.Increasing temperature using hightemperature Products to decrease Heat Duty atHeater H-101.•Removing Chloride Salts and water content by 1st and 2nd stage Desalters Temperature 300 F°& Pressures 362.5 psig)Under Electro magnetic field (about 20 to 30 KV).•Flash Drum to remove Vapours to reduce load at Heater. •Crude Heater, H-111-101A/B, is configured as a box type heater with horizontal tubes.two identical heaters are specified to accomplish the required duty. Each of these two heaters consists of two parallel radiant sections and a single convection section. Asingle Air Preheat System and a common stack serves both heaters.Heater works with balanced Draft FD and ID .•The Crude Distillation Column (V-111-101) Products. -Low pressure off-gas-Naphtha-Kerosene-Heavy Diesel-Light Diesel-Atmospheric Residue- Experience in Pre-commissioning, Commissioning and Initial Start-up. activities like:-- Final inspection of the plant. - Flushing of lines and equipments.- DCS Functioning check, Loop check.- Pump Mechanical Run test, Motor Solo Run test. - GALT ( Gas Air Leak Teat), PSSR- Heater Dryout. Show less
-
-
DCS Operator
-
Jul 2012 - Present
-Vacuum Distillation Unit VDU-213.The Technology Licensors for VDU is Chevron Lummus Global Technology. -The VDU-213 unit has been designed to treat 50000 BPSD of LSAR received from bothunits ARDS 112/212.-VDU consist of feed surge drum, motor driven charge pump, Heater with velocity steam.Main vacuum column is operating with 3-pumps around& produces VGO[ LVGO LightVacuum Gas Oil + HVGO Heavy Vacuum Gas Oil], TGO [ Trim Gas Oil] and VR [VacResidue] as a feed for D/S units.Slop wax is recycled back to the heater. - The Vacuum Distillation Unit (VDU-213) is composed one Heater H-101 with two identicalradiant cells. Each cell is having 8 burners in the center and tubes on the wall, in thehorizontal orientation. The heater has his convection section above and in between thetwo radiant cells. Tubes in convection section are arranged horizontally. 3.08 MW(design).-The convection section also has IP/MP steam superheating coils to augment the waste. - Vacuum Distillation Column V-101 consists of six sections:- The flash zone- The wash oil section- TGO section- HVGO heat removal section- LVGO and condensing section- Bottoms stripping section- VRU-213 will comprise the following sections:° Surge Drum and Pump. ° Feed Heat Recovery Train. ° Vacuum Heater. ° Vacuum Column. ° Liquid Ring Compressor° Products Cooling with Steam Generation. ° Ejector Package. ° Flare KOD. ° Flushing Oil System. -Experience in Startup and Shutdown procedures. - Experience in Pre-commissioning, Commissioning and Initial Start-up. activities like:-- Final inspection of the plant. - Flushing of lines and equipments. - Mechanical run-in Test of Pumps and Compressors MRT. - Motor Solo Run MSR. - Loop Check & Functional Test. - Dry out of fired Heaters. - Gas Air Leak test GALT- Pre-Startup Safety Review (PSSR). - Preparing Punch Lists. - Good reading of P&ID. Show less
-
-
-
-
Senior DCS&Field Operator
-
2009 - Jul 2012
•Experience with Natural Gas Sulfur removing by Hydro Desulfurization Unit. •Removing inorganic Sulfur from Natural Gas by Amine Gas Treatment (mono-ethanol amine) unit. •Responsible for the operation of different units of the Urea/ammonia plant including many units as synthesis (stripper, high pressure condenser, scrubber) and Reactors (low pressure condenser, rectifying column), evaporation System. •Gas Flare System to remove Ammonia Pollution. •Experience in Gas Compression with Centrifugal and Reciprocating Compressors •Experience with HP steam Turbines. •Monitors and operates equipment and processes in the assigned area in accordance with operating instructions. •Operate DCS control to coordinate and regulate process variables and to direct flow rates of various process and utility streams according to prescribed schedules. Read processing schedules, operating logs. •DCS experience with Foxboro IA Series V8.8 Fox View 10.4.4. • Test results of samples, and lab recommendations to determine changes in equipment controls required to produce specified quality and quantity of product. •Set controls to adjust process variables, such as flows, temperatures and pressures. • Participate in the turnaround with PIC 2009, 2012 and 2014. •Pre-commissioning and commissioning activities. •confirm all control valves and interlock system and emergency shutdown are working as per process requirements. •NG, process air, compressors associated lube oil and seal oil system, Woodward Governor, dry seal system, driven by Steam turbine. •Informs the Supervisor about any abnormal noises, vibrations, leaks etc. Records details of the plant operations. •Experience in Sour Water treatment system (Hydrolysis Unit) to remove (CO2&NH3&UREA) components. Show less
-
-
-
Ideal Standard MENA
-
United Arab Emirates
-
Consumer Goods
-
100 - 200 Employee
-
Shift Supervisor
-
Jan 2000 - Mar 2009
Supervisor in Ideal Standard Egypt - Petro chemical Acrylic Sheet Plant - (an American standard co), 10th of Ramadan City, Egypt (Previous Work) since 1/01/2000 Supervision · Responsible of the production line of Acrylic sheet(poly methylmetha acrylate), including many sections; Additives preparation area, pouring, inspection, washing sheets, curing in water bath and air bath , and other utilities like boilers, water treatment station, air compressors and chillers. · Coordination of work tasks between the shift employees - about 30 persons distributed between all sections · Supervision and control of free radical polymerisation process using bulk reactor ( 1 ton batch ) using DCS system · Using the laboratory instruments to check the raw material and final product is one of my job resposibiliteis. · Control of free radical polymerization process to produce PMMA(Poly methyl metha acrylate) using bulk reactor ( 1 ton batch ) using DCS system. · Using the laboratory instruments to check the raw material and final product is one of my job resposibiliteis. (GC,GPC,Karl fisher Titrator,Vicat Softening Point,spectro Photometer) · Control of Waste Recovery process to produce MMA from waste using cracking in reactor with Lead at high Temp (550 c) then condensing vapour in crude tank after that making distillation under vacuum to produce DMMA. Show less
-
-
Education
-
Zagazig University
Bachelor of Applied Science (B.A.Sc.), Chemistry
Community
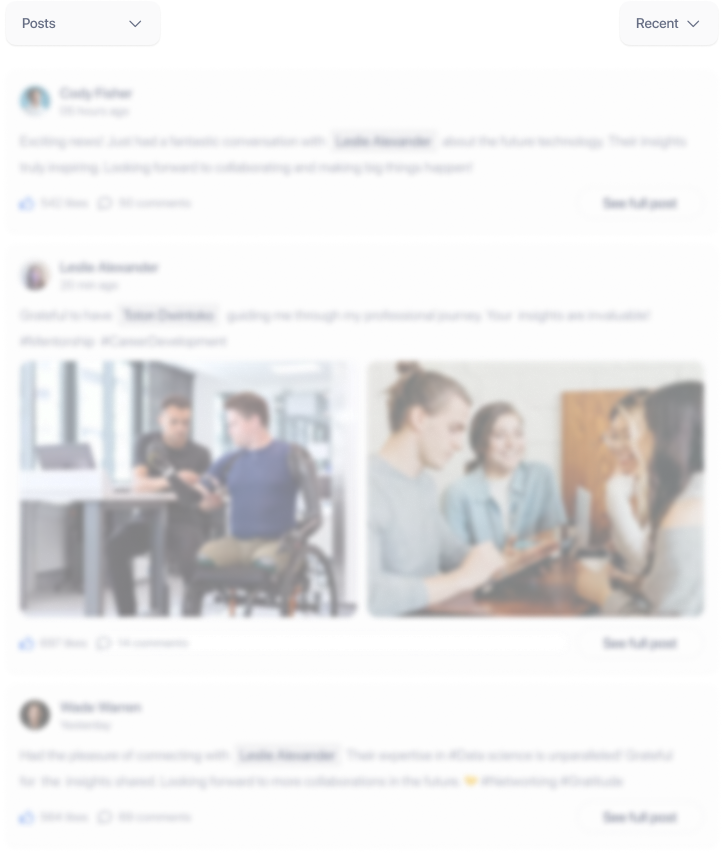