Ahmed Abdu
Supply Chain Manager at Al-Jazeera Factory For Paints Co.- Claim this Profile
Click to upgrade to our gold package
for the full feature experience.
Topline Score
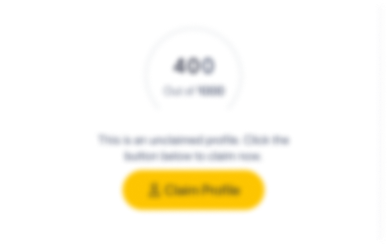
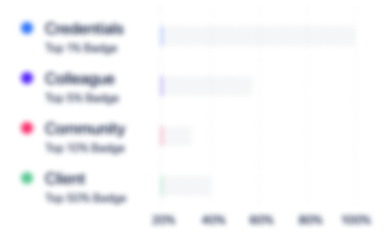
Bio


Credentials
-
Business Etiquette
American chamber of commerce of Egypt -
Business communication
American chamber of commerce of Egypt -
Business professional "Customer service"
American chamber of commerce of Egypt -
Business professional "Leadership"
American chamber of commerce of Egypt -
Business professional "Sales"
American chamber of commerce of Egypt -
Certified Manager Certification.
American chamber of commerce of Egypt -
Certified Supply Chain Professional (CSCP)
American chamber of commerce of Egypt -
Control of International work place hazards
NEBOSH -
Detailed scheduling & Planning
American chamber of commerce of Egypt -
Lean and six sigma certifications.
Symbyosys -
Management of international health and safety
NEBOSH -
NEBOSH international general certificate in occupational health
NEBOSH -
Presentation skills
LOGIC Consulting -
Production and inventory management
American chamber of commerce of Egypt -
Report writing
American chamber of commerce of Egypt
Experience
-
Al-Jazeera Factory For Paints Co.
-
1 - 100 Employee
-
Supply Chain Manager
-
Feb 2019 - Present
• Managed more than 300 employees. • Managed more than 13 warehouses in different locations. • Launched (AXAPTA) system as new ERP and MRP System inside the company. • Created Supply chain procedures, policies, work instructions, team job deception’s • Implemented schedule and policy changes and collaborated with management to formulated new policies and goals. • Increased profit margins by 10% and reduced expenses by 15%. • Increased supply efficiency by 15% through process improvement design and implementation. • Increased the production efficiency to be 95% through proper plan and reduced the changeover numbers. • reduced Customer Order Cycle Time by 10%. • Increased Inventory Turnover by 20%. • Reduce dead stock costs 32% through Saving projects. • Reduced warehouses operation cost 31%. • Increased area coverage by 50% through effective scheduling and detailed location monitoring. • Increased warehouse utilization efficiency to be 100%. • Increased dispatching efficiency 19% through process improvement and reviewing KPIs on a monthly basis. • Created and launched new stock levels of Finished goods and raw materials less than the previous levels by 15% through the implementations of shipping methods and new classifications of FG & RM items. • Increased utilization efficiency of forklifts to be 100% instead of 60% and introduced the latest technology of forklifts. • Saved $55K by eliminating constraints in the laminating process. • Created and launched supplier scorecard and supplier survey. • Created supplier stocking agreements with lead buyers to reduce time down to 5 days. • Reduced high-speed wrapping setups by 10% through changing pack quantity of raw stock. • Reduced costs in inventory and piece part price by 21% by identifying unnecessary tooling. Show less
-
-
-
Fine Solutions. A FHH Company
-
United Arab Emirates
-
Manufacturing
-
1 - 100 Employee
-
Supply Chain Manager
-
Jun 2008 - Jun 2018
• Managed more than 400 employees. • Managed more than 8 Stores of finished goods, Spare parts and Raw materials. And the required maintenance of all stores. • Managed More than 50 forklifts with required maintenance. • Launched (ORACLE) system as new ERP and MRP System inside the company. • Created Supply chain procedures, policies, work instructions, team job deception’s • Implemented schedule and policy changes and collaborated with management to formulated new policies and goals. • Increased profit margins by 16% and reduced expenses by 15%. • Increased supply efficiency by 19% through process improvement design and implementation. • Increased the production efficiency to be 95% through proper plan and reduced the changeover numbers. • reduced Customer Order Cycle Time by 18%. • Increased Inventory Turnover by 31%. • Reduce dead stock costs 32% through Saving projects. • Reduced warehouses operation cost 31%. • Increased area coverage by 92% through effective scheduling and detailed location monitoring. • Increased warehouse utilization efficiency to be 100% instead of 62%. • Increased dispatching efficiency 19% through process improvement and reviewing KPIs on a monthly basis. • Created and launched new stock levels of Finished goods and raw materials less than the previous levels by 9% through the implementations of shipping methods and new classifications of FG & RM items. • Increased utilization efficiency of forklifts to be 100% instead of 60% and introduced the latest technology of forklifts. • Saved $205K by eliminating constraints in the laminating process. • Led 5S project that reduced waste and searching time by 15%. • Created and launched supplier scorecard and supplier survey. • Created supplier stocking agreements with lead buyers to reduce time down to 2 days. Show less
-
-
-
Mobiserve Holding
-
United Arab Emirates
-
Telecommunications
-
700 & Above Employee
-
Warehouse and Planning Manager
-
Apr 2006 - Jun 2008
• Created warehouse and planning procedures, policies, work instructions, team job deception's, stores risk assessment and communicate this information to staff. • Managed more than 100 employees. • Managed more than 8 Stores of finished goods, Spare parts and Raw materials. And the required maintenance of all stores. • Managed More than 50 forklifts with required maintenance. • Increased utilization efficiency of warehouses to be 100% instead of 45%. • Increased utilization efficiency of forklifts to be 95% instead of 30% and introduced the latest technology of forklifts. • Increased utilization efficiency of forklifts to be 95% instead of 30% and introduced the latest technology of forklifts. • Reduced warehouses operation cost 65%. • Reduce dead stock costs 80% through Saving projects. • Reduced stock out to be 0% instead of 10%. • Increased dispatching efficiency by 40% through process improvement and reviewing KPIs on a monthly basis. • Reduce safety incident / accident to be Zero inside the stores. • Created and launched RFID System and reduced manpower cost 50%. • Launched (ORACLE) system as new ERP System inside the company. • Created and launched MRP System. • Implemented warehouse-wide Kanban system for FIFO management of all Finished goods, raw material and spare parts items. • Led 5S project that reduced waste and searching time by 15%. • Controlled stock balance and conducted stocktaking on a periodic basis following appropriate guidelines released by accounting and audit departments. And Keeping stock control systems up to date. • Reduced direct material costs 15% on formed metal products. • Created raw materials monthly and periodically purchase requests. • Maintained the availability of the optimal inventory level at all times. • Reduced shortage of raw materials to be Zero% instead of 21%. • Created cost saving projects and reduced 200,000$ annually. Show less
-
-
-
Procter & Gamble
-
United States
-
Manufacturing
-
700 & Above Employee
-
Warehouse team Leader
-
Apr 2004 - Apr 2006
• Created a staging area system that saved 3 hours a day per material handling. • Managed raw material team and SAP Key user team. • Switched all staff to the new barcode scanner system that saved 2 hours a day per material handler. • Managed and monitored raw material store team to record the transactions on the ERP system (SAP). • Ensure that all raw materials were delivered to the production lines on time, according to production plan received from the planning department. • Monitored the stock levels of Raw materials and re-fill the item stock which had reached the minimum level to ensure the availability of raw materials. • Reduced scrap quantities inside the warehouse to be .02 instead of .09. • Supervision of stock movements from stores and Shelf's locations to ensure they are recorded accurately for inventory integrity. • Controlled stock balance and conducted stocktaking on a periodic basis following appropriate guidelines released by accounting and audit departments. And Keeping stock control systems up to date. • Created analysis report of the Raw material losses and gain. • Set the plan of future requirements for Storage capacity and their equipment's. • Implemented the new bar-coding system in the raw materials store for receiving and delivery. • Participate in Modification of new SAP System version. • Created work plan, assign tasks appropriately and appraise the results. • Coordinate between the raw material department and other departments. Show less
-
-
Education
-
American Chamber of Commerce
Diploma of Education, Supply chain -
NEBOSH
Diploma of Education, Safety -
Cairo University
Bachelor's degree, Accounting
Community
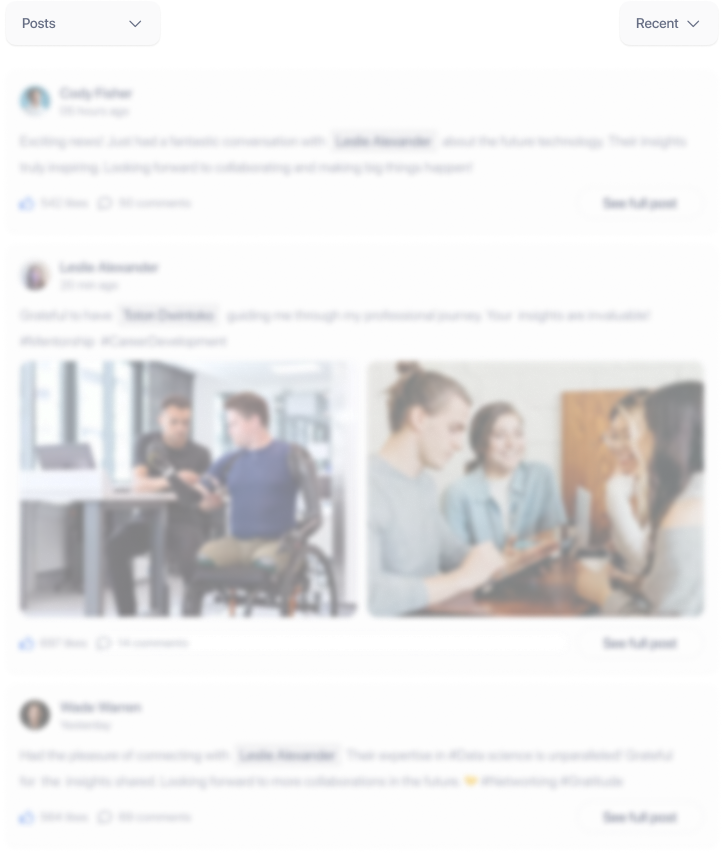