Adrian Hall
Supply Chain Consultant at Mr Fothergill's Seeds Ltd- Claim this Profile
Click to upgrade to our gold package
for the full feature experience.
Topline Score
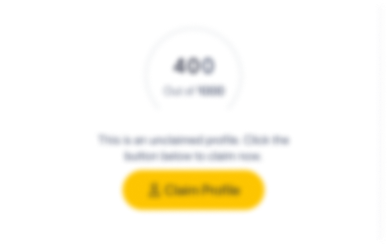
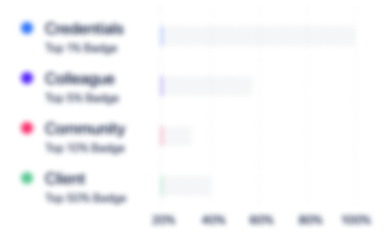
Bio

Richard Hall
I have worked with Adrian for several years and find him to be a enthusiastic motivated and committed individual. He has excellent attention to detail and his business process and systems knowledge is second to none. He has been key in implementing major projects into the business such as S&OP, and is an effective change agent who delivers process improvements consistently. Adrian is very adept at sifting through figures, balance sheets, charts etc and focussing in on the pertinent metrics. I have enjoy working with Adrian on several teams and find him to be an effective and adaptable team player.

Frans Visser
I have no hesitation in recommending Adrian. He is one of the brightest, adaptable, calm and organised people I have ever had the privilege to work with. He is quite capable of developing and implementing strategic and operational plans and would be an asset to any organisation he joins.

Richard Hall
I have worked with Adrian for several years and find him to be a enthusiastic motivated and committed individual. He has excellent attention to detail and his business process and systems knowledge is second to none. He has been key in implementing major projects into the business such as S&OP, and is an effective change agent who delivers process improvements consistently. Adrian is very adept at sifting through figures, balance sheets, charts etc and focussing in on the pertinent metrics. I have enjoy working with Adrian on several teams and find him to be an effective and adaptable team player.

Frans Visser
I have no hesitation in recommending Adrian. He is one of the brightest, adaptable, calm and organised people I have ever had the privilege to work with. He is quite capable of developing and implementing strategic and operational plans and would be an asset to any organisation he joins.

Richard Hall
I have worked with Adrian for several years and find him to be a enthusiastic motivated and committed individual. He has excellent attention to detail and his business process and systems knowledge is second to none. He has been key in implementing major projects into the business such as S&OP, and is an effective change agent who delivers process improvements consistently. Adrian is very adept at sifting through figures, balance sheets, charts etc and focussing in on the pertinent metrics. I have enjoy working with Adrian on several teams and find him to be an effective and adaptable team player.

Frans Visser
I have no hesitation in recommending Adrian. He is one of the brightest, adaptable, calm and organised people I have ever had the privilege to work with. He is quite capable of developing and implementing strategic and operational plans and would be an asset to any organisation he joins.

Richard Hall
I have worked with Adrian for several years and find him to be a enthusiastic motivated and committed individual. He has excellent attention to detail and his business process and systems knowledge is second to none. He has been key in implementing major projects into the business such as S&OP, and is an effective change agent who delivers process improvements consistently. Adrian is very adept at sifting through figures, balance sheets, charts etc and focussing in on the pertinent metrics. I have enjoy working with Adrian on several teams and find him to be an effective and adaptable team player.

Frans Visser
I have no hesitation in recommending Adrian. He is one of the brightest, adaptable, calm and organised people I have ever had the privilege to work with. He is quite capable of developing and implementing strategic and operational plans and would be an asset to any organisation he joins.

Experience
-
Mr Fothergill's Seeds Ltd
-
United Kingdom
-
Retail
-
1 - 100 Employee
-
Supply Chain Consultant
-
Jan 2023 - Present
-
-
-
Vibrant Foods
-
United Kingdom
-
Food and Beverage Manufacturing
-
100 - 200 Employee
-
Interim Supply Chain Planning Manager
-
Jun 2022 - Present
-
-
-
Titon
-
United Kingdom
-
Appliances, Electrical, and Electronics Manufacturing
-
1 - 100 Employee
-
Interim Supply Chain manager
-
Jan 2022 - Dec 2022
-
-
-
Nomad Foods
-
United Kingdom
-
Food and Beverage Manufacturing
-
700 & Above Employee
-
Interim Supply Chain Manager
-
Jul 2021 - Jan 2022
-
-
-
Elvie
-
United Kingdom
-
Wellness and Fitness Services
-
100 - 200 Employee
-
Interim Global Sales & Operations Manager
-
Oct 2020 - Apr 2021
-
-
-
East End Foods Limited
-
Food and Beverage Manufacturing
-
1 - 100 Employee
-
Interim Planning Manager
-
Mar 2020 - Sep 2020
-
-
-
TRS WHOLESALE CO. LIMITED
-
United Kingdom
-
Wholesale
-
1 - 100 Employee
-
Interim Planning Manager
-
Nov 2019 - Sep 2020
-
-
-
Autoglym
-
United Kingdom
-
Motor Vehicle Manufacturing
-
1 - 100 Employee
-
Interim Supply Chain Manager
-
Jun 2018 - Dec 2019
Development and implementation of an integrated operational planning process including capacity planning, demand planning and inventory management. Development and implementation of an integrated operational planning process including capacity planning, demand planning and inventory management.
-
-
-
Zip Water UK
-
United Kingdom
-
Appliances, Electrical, and Electronics Manufacturing
-
100 - 200 Employee
-
Interim Inventory Planning Manager
-
Jan 2018 - Jun 2018
Demand and Supply Planning system & process development and Inventory management. Demand and Supply Planning system & process development and Inventory management.
-
-
-
Bernard Matthews
-
Food and Beverage Manufacturing
-
300 - 400 Employee
-
Interim Planning Manager
-
Oct 2017 - Dec 2017
Support delivery of the Christmas fresh turkey programme. Support delivery of the Christmas fresh turkey programme.
-
-
-
Highland Spring Ltd
-
United Kingdom
-
Food and Beverage Services
-
100 - 200 Employee
-
Interim Supply Chain Manager
-
Feb 2017 - Sep 2017
Supply Chain system & process development. Supply Chain system & process development.
-
-
-
Kerry
-
Ireland
-
Food and Beverage Services
-
700 & Above Employee
-
Interim Planning Manager
-
Feb 2016 - Oct 2016
Manage and develop Supply Planning process in advance of Infor AP implementation. Manage and develop Supply Planning process in advance of Infor AP implementation.
-
-
-
Mondelēz International
-
United States
-
Food and Beverage Manufacturing
-
700 & Above Employee
-
Interim Supply Planning Platform Manager
-
Sep 2015 - Nov 2015
Management of Supply Planning and Materials Control teams responsible for planning operations of 6 manufacturing facilities across Europe, during the transition from local to central planning hub utilising SAP AP solution. Management of Supply Planning and Materials Control teams responsible for planning operations of 6 manufacturing facilities across Europe, during the transition from local to central planning hub utilising SAP AP solution.
-
-
-
Sensient Technologies Corporation
-
United States
-
Chemical Manufacturing
-
700 & Above Employee
-
Interim Supply Chain Consultant
-
Jun 2015 - Aug 2015
Review Supply Chain systems and processes with a view to cleansing and updating master data and transitioning manual tasks to incumbent Prism MRP solution in advance of JDE development and implementation. Review Supply Chain systems and processes with a view to cleansing and updating master data and transitioning manual tasks to incumbent Prism MRP solution in advance of JDE development and implementation.
-
-
-
KP Snacks
-
United Kingdom
-
Food and Beverage Manufacturing
-
500 - 600 Employee
-
Interim Supply Chain Manager
-
Dec 2014 - May 2015
Manage the Supply Chain team and 3PL operations during a site closure and production relocation project. Manage the Supply Chain team and 3PL operations during a site closure and production relocation project.
-
-
-
Kerry
-
Ireland
-
Food and Beverage Services
-
700 & Above Employee
-
Interim Supply Planning Manager
-
Feb 2013 - Nov 2014
Contract initially for 6 months to design, develop and implement time sequenced production planning, forward scheduling and line level capacity systems covering rolling 12 month horizon. Contract extended a further 5 months to source and implement customer demand management software to forecast 45k tns. To develop integrated MRP systems at daily and weekly level and to implement cross functional best practice. Further contract extension to support development of departmental processes and cross functional best practice in readiness for system migration to SAP. Development of stock management and reporting systems to reduce material and finished goods stock value to business targets.
-
-
-
Vion Food Group
-
Netherlands
-
Food and Beverage Manufacturing
-
700 & Above Employee
-
National Portion Supply Specialist - 6 month Contract
-
Jun 2012 - Dec 2012
• Managing demand and material supply for 2 production facilities processing 1.7m chickens per week supplying chilled and frozen portions to major retailers. • Approval of sales activity in-line with resource availability and factory capacities. • Development of factory utilisation models to provide business reports on operational capacities, leading to long term view of commercial opportunity. • Managing demand and material supply for 2 production facilities processing 1.7m chickens per week supplying chilled and frozen portions to major retailers. • Approval of sales activity in-line with resource availability and factory capacities. • Development of factory utilisation models to provide business reports on operational capacities, leading to long term view of commercial opportunity.
-
-
-
Bernard Matthews
-
Food and Beverage Manufacturing
-
300 - 400 Employee
-
Demand Planning Manager
-
Oct 2007 - Jun 2012
Management of sales forecast and promotional activity volumes in-line with commercial strategy. • Management of multi-category business forecast over rolling two year horizon • Accuracy of short term demand forecast to improve operational efficiency • Order fulfilment service level and product wastage • Factory and production line capacities across three manufacturing sites • Accountable for inventory levels within stock cover policy and financial KPI’s Management of sales forecast and promotional activity volumes in-line with commercial strategy. • Management of multi-category business forecast over rolling two year horizon • Accuracy of short term demand forecast to improve operational efficiency • Order fulfilment service level and product wastage • Factory and production line capacities across three manufacturing sites • Accountable for inventory levels within stock cover policy and financial KPI’s
-
-
-
Marlow Foods (part of Premier Foods)
-
Methwold, Norfolk
-
Planning and Logistics Manager
-
Feb 2007 - Oct 2007
Management of site supply chain functions. • Factory capacity planning and material availability for multi-category production unit. • Internal warehousing and 3PL operations. • Service levels and factory efficiency through effective production planning. • Implemented supply chain infrastructure to improve operational efficiency, data capture and stock control. • Developed Excel based planning, scheduling and material control systems for daily operation and long term capacity planning systems to run along-side SAP MRP system.
-
-
-
Bernard Matthews
-
Food and Beverage Manufacturing
-
300 - 400 Employee
-
Production Planning Manager
-
Sep 1999 - Feb 2007
Capacity planning and primary resource availability for 7 UK based factories across 3 locations. • Factory capacity planning and primary resource availability. • Production scheduling and availability of chilled and frozen products within logistics network. • Strategic supply planning with account teams and category directors. • Purchase of primary resources from European subsidiary to meet promotional demand. • Planning systems development and integration with MRP. • Developed and implemented labour planning system that reduced non-utilised labour and provided longer term view of agency requirements. • Implemented planning process that reduced waste without affecting service levels. • Joint managed development and implementation of advanced planning system.
-
-
Education
-
The Open University
Community
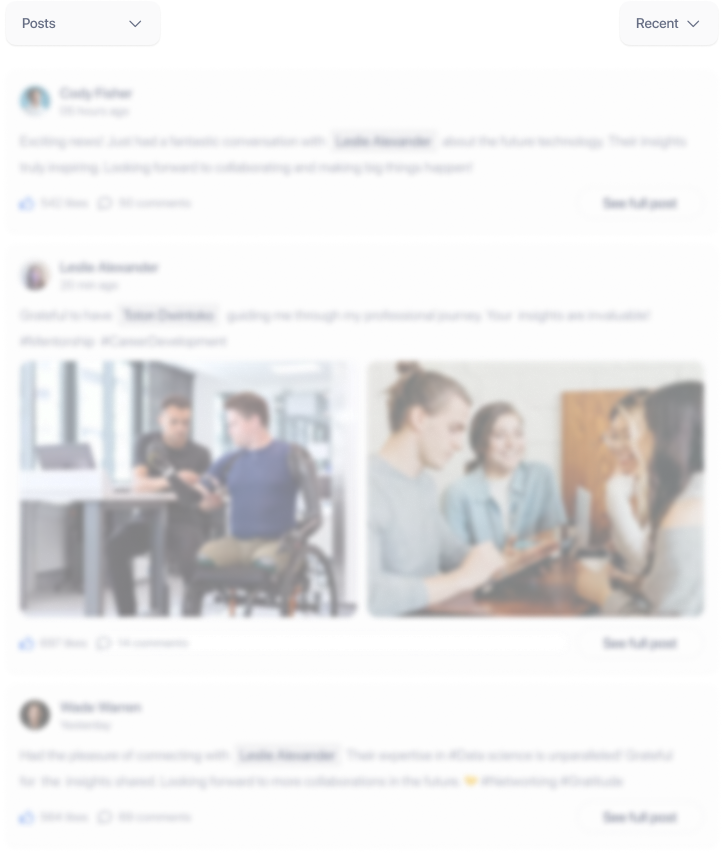