Adam Westwood
Designer at Engenera Renewables Group- Claim this Profile
Click to upgrade to our gold package
for the full feature experience.
Topline Score
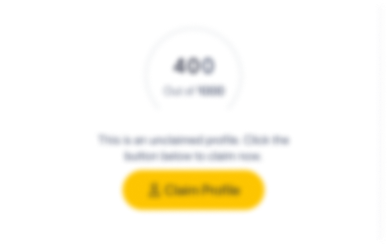
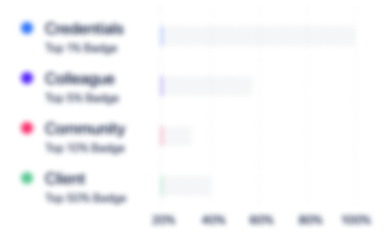
Bio


Experience
-
Engenera Renewables Group
-
United Kingdom
-
Renewables & Environment
-
1 - 100 Employee
-
Designer
-
Sep 2022 - Present
-
-
-
Greggs
-
Food & Beverages
-
700 & Above Employee
-
Maintenance Planner
-
Jan 2022 - Aug 2022
-
-
-
Wyndham Primary School
-
New Zealand
-
Primary and Secondary Education
-
Facilities Manager
-
Mar 2021 - Dec 2021
Provided solutions to property maintenance issues. Liaised with 3rd party contractors to ensure work was carried out correctly whilst safeguarding the pupils. Received safeguarding training. Managed the cleaning team to ensure the school was fit for use. Carried out periodic inspections. Ensured the school was a safe and secure environment. Provided solutions to property maintenance issues. Liaised with 3rd party contractors to ensure work was carried out correctly whilst safeguarding the pupils. Received safeguarding training. Managed the cleaning team to ensure the school was fit for use. Carried out periodic inspections. Ensured the school was a safe and secure environment.
-
-
-
Hitachi Rail
-
United Kingdom
-
Truck Transportation
-
700 & Above Employee
-
Production team member and site safety representative
-
Mar 2016 - Mar 2020
Improved assembly process by writing work procedures. Build jigs and fittings to aid the assembly process. Undertook workshop training. Undertook assembly task training. Performed assembly tasks to site standards. Took responsibility of quality standards for my own work. Member of the site safety committee. Carried out workplace safety inspections. Improved assembly process by writing work procedures. Build jigs and fittings to aid the assembly process. Undertook workshop training. Undertook assembly task training. Performed assembly tasks to site standards. Took responsibility of quality standards for my own work. Member of the site safety committee. Carried out workplace safety inspections.
-
-
-
BTG plc
-
United States
-
Medical Device
-
200 - 300 Employee
-
Site Engineer
-
Sep 2014 - Mar 2016
I was responsible for all engineering activities on the entire site. The previous site owner had gone into liquidation and the site was in complete disarray. All engineering had been reduced to minimum cost and the maintenance systems on site had failed. I had to set up a complete maintenance system for the site to restore the site to a fully working process. This entailed all of the following; Developed and managed the site maintenance plan by assessing and planning all maintenance and calibration activities in order to minimise plant downtime. Carried out reactive and proactive maintenance to maximise asset availability and avoid production disruption. Developed a framework of site maintenance contracts, ensuring the maintenance requirements of the assets were fulfilled and complied with cGMP. All contracts were competitively priced and complied with cGMP good engineering practices. Ensured all work was carried out in a timely manner causing minimal disruption to the site. Operated the permit to work system and ensured risk assessments were in place prior to execution of tasks. Prepared engineering documentation for the quality management system and ensured it was fit for purpose. Ensured all appropriate documentation associated with work carried out on site and materials supplied to site satisfied regulatory standards and was filed appropriately for potential regulatory inspection. Reviewed completed work orders and service reports for GMP compliance and analysed the report to develop action plans to prevent reoccurrence. Conducted root cause investigations into equipment and process breakdowns and failures. Implemented corrective and preventive actions in order to quickly resolve outstanding issues and prevent further occurrences of a similar nature. Developed a site maintenance stock scheme and liased with suppliers to organise site stock. Show less
-
-
-
FUJIFILM Diosynth Biotechnologies
-
United Kingdom
-
Biotechnology Research
-
700 & Above Employee
-
Project Engineer
-
Aug 2008 - Apr 2014
I was brought in on an initial 3 month project to prepare for an F.D.A inspection. My work impressed the maintenance manager who then gave me further projects that ran for almost 6 years. I assisted the maintenance manager in running the maintenance section if the following ways. Provided support to maintenance personnel to ensure tasks were completed in a timely manner causing minimal disruption to the site. Ensuring the maintenance requirements of the assets were fulfilled and to complied with cGMP and good engineering practices Reviewed the site maintenance scheme and developed a proactive maintenance schedule to maximise asset availability and avoid production disruption. Compiled work instructions for equipment that conformed to the manufacturers maintenance requirements. Undertook plant reliability centred maintenance study (R.C.M.) Analysed both production steams to individual component level, determined means of failure and put in appropriate pro-active maintenance to prevent component failure. Compiled a plant maintenance and instrumentation schedule. Trained to Lean Six Sigma yellow belt standard. Under took good manufacturing practice (cG.M.P.) training. Ensured Documentation Compliance. Show less
-
-
-
-
Project Engineer
-
May 2006 - Jul 2008
V fuels were a new company who were converting the previous G.S.K site to a site that produced biodiesel using used cooking oil. This entailed designing and installing a new process and returning previously redundant equipment to service. The development of this process was ongoing. Co-ordinated engineering staff throughout the plant. Co-ordinated the upkeep of essential site services and plant. Organised the repair of faults on equipment to maintain the plant operational. Compiled maintenance schedules and routines for plant equipment. Co-ordinated engineering staff throughout the plant. Co-ordinated the upkeep of essential site services and plant. Organised the repair of faults on equipment to maintain the plant operational. Set up equipment register and associated maintenance tasks in a CMMS system. Liaised with suppliers to organise spares, equipment and services. Liaised with contractors to organise services supplied to the site. Returned previously unserviceable equipment to a serviceable state. Co-ordinated mandatory inspections and testing of plant. Budgetary control and financial management. Show less
-
-
-
Shell
-
Oil and Gas
-
1 - 100 Employee
-
Engineer
-
Jul 2000 - Aug 2001
Shell Exploration Aberdeen Shell Exploration Aberdeen
-
-
-
British Army
-
Armed Forces
-
700 & Above Employee
-
Aircraft Maintenance Technician
-
May 1990 - Sep 1995
Carried out daily and technical servicing of aircraft, assessing the airworthiness of the aircraft and ensuring that the aircraft met recognised standards. Tested the aircrafts to asses the aircraft was at an airworthy standard. Co-ordinated maintenance teams. Carried out scheduled maintenance tasks and repaired faults on aircraft, following documented maintenance routines. Ensured the aircraft were repaired in a correct manner and all documentation was correctly completed and submitted. Spent 6 months working in the Vehicle Repair Section carrying out fault diagnosis and repairs to the regimental fleet of vehicles. Trained in first aid techniques. Completed aircraft technicians training at Army School of Aeronautical Engineering. Show less
-
-
Community
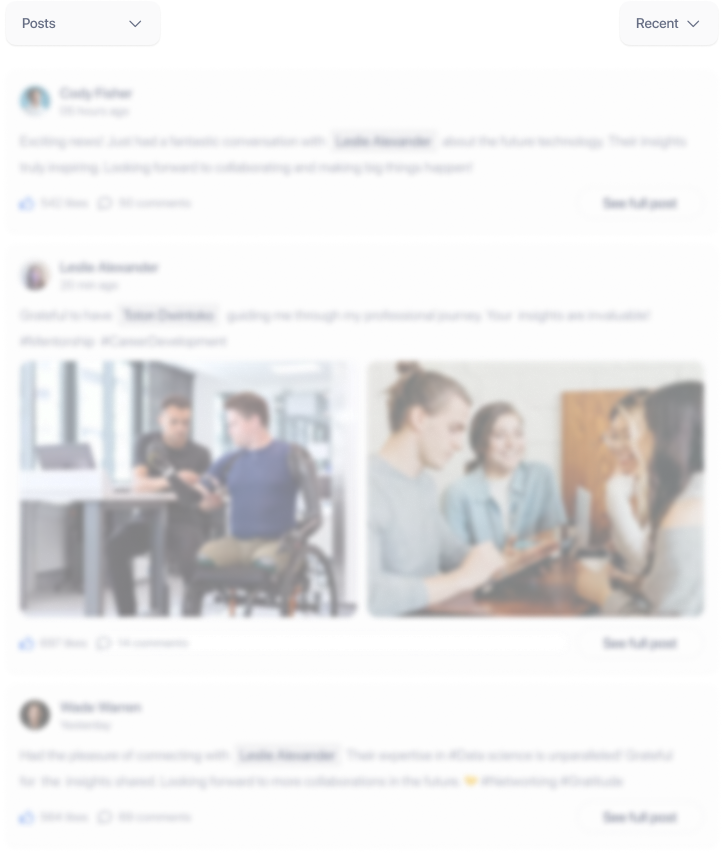