Adam Watson
Operations Manager at FRC Corp- Claim this Profile
Click to upgrade to our gold package
for the full feature experience.
Topline Score
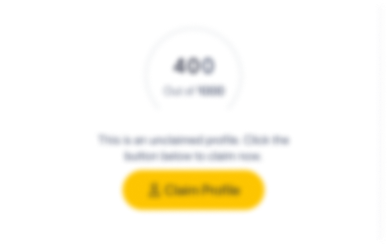
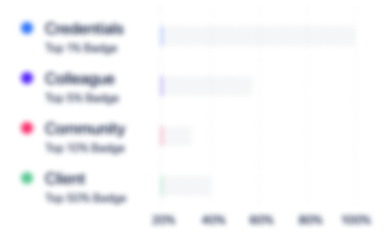
Bio

Thomas Williams
While working at HNI Corporation, Adam and I travelled to various plants within the corporation and conduction RCI training and events (Lean Kaizen events). Adam demonstrated not only knowledge of the tools and techniques used, but also an ability to lead and manage team members from all levels of the corporation. He also showed a willingness to do any job that was required, and work until the job was done. He has an ability to gain the trust of members of the shop floor while listening and responding to their needs, but also the ability to present persuasive proposals to higher management.

Thomas Williams
While working at HNI Corporation, Adam and I travelled to various plants within the corporation and conduction RCI training and events (Lean Kaizen events). Adam demonstrated not only knowledge of the tools and techniques used, but also an ability to lead and manage team members from all levels of the corporation. He also showed a willingness to do any job that was required, and work until the job was done. He has an ability to gain the trust of members of the shop floor while listening and responding to their needs, but also the ability to present persuasive proposals to higher management.

Thomas Williams
While working at HNI Corporation, Adam and I travelled to various plants within the corporation and conduction RCI training and events (Lean Kaizen events). Adam demonstrated not only knowledge of the tools and techniques used, but also an ability to lead and manage team members from all levels of the corporation. He also showed a willingness to do any job that was required, and work until the job was done. He has an ability to gain the trust of members of the shop floor while listening and responding to their needs, but also the ability to present persuasive proposals to higher management.

Thomas Williams
While working at HNI Corporation, Adam and I travelled to various plants within the corporation and conduction RCI training and events (Lean Kaizen events). Adam demonstrated not only knowledge of the tools and techniques used, but also an ability to lead and manage team members from all levels of the corporation. He also showed a willingness to do any job that was required, and work until the job was done. He has an ability to gain the trust of members of the shop floor while listening and responding to their needs, but also the ability to present persuasive proposals to higher management.

Experience
-
FRC Corp
-
United States
-
Telecommunications
-
1 - 100 Employee
-
Operations Manager
-
Jun 2021 - Present
-
-
-
Energy Manufacturing Company, Inc.
-
United States
-
1 - 100 Employee
-
Production Manager
-
Jan 2020 - Mar 2021
Responsible for 100+ employees across 3 shifts of hydraulic cylinder machining, welding, assembly, and shipping. Schedule daily production for individual machining and assembly work centers to optimize productivity while meeting goals in safety, on-time delivery, and quality. Responsible for 100+ employees across 3 shifts of hydraulic cylinder machining, welding, assembly, and shipping. Schedule daily production for individual machining and assembly work centers to optimize productivity while meeting goals in safety, on-time delivery, and quality.
-
-
-
Flexsteel Industries Inc.
-
United States
-
Furniture and Home Furnishings Manufacturing
-
300 - 400 Employee
-
Production Manager -Steel
-
Jan 2019 - Aug 2019
Responsible for all aspects of Steel Manufacturing process. Provide leadership of the manufacturing operation focusing on staffing and workload planning, managing operating expenses, and alignment through ongoing continuous improvement efforts to enhance safety, quality, productivity, and delivery. Develop and execute plans to meet operational objectives, KPIs, capital projects, and operating budgets.
-
-
Manufacturing Transition Lead
-
Oct 2018 - Jan 2019
Coordinate the relocation, start-up, and qualification of production equipment and processes from a facility being decommissioned to a newly-constructed facility with minimal interruptions to customers.
-
-
Business Track Owner - Plan to Manufacture
-
Feb 2017 - Oct 2018
Lead the Plan to Manufacture track in corporation-wide implementation of SAP. Responsible for development and cut-over of business and manufacturing processes from legacy to ERP software. Work with consultants to develop solutions to process gaps and create custom functionality for unique business processes. Participate in cross-functional teams to create system tools designed to meet changing business requirements.
-
-
Continuous Improvement, Engineering, & Maintenance Manager
-
Oct 2013 - Feb 2017
Lead the implementation of a Lean culture via associate training and conducting Kaizen events. Organize and design lean activities within location to impact key business initiatives. Drive performance improvements using 5S, visual management, standard work, value stream mapping, SMED, and other relevant lean tools. Plan, deploy, and lead lean activities that produce significant cost savings though productivity, quality, waste reduction improvements, and improving business processes. Provide mentoring and support to all production leads, managers and supervisors to bring about the necessary cultural change within the company Show less
-
-
-
Terex Corporation
-
United States
-
Machinery Manufacturing
-
700 & Above Employee
-
Manufacturing Engineer
-
Apr 2012 - Oct 2013
Manage production of 3 major value streams on 1 mixed-model assembly line. Develop, document, and improve manufacturing methods, utilizing knowledge of materials, fabrication processes, tooling and production equipment capabilities, assembly methods, and quality control standards. Evaluate equipment, processes, operations, and assembly to determine and implement safety, productivity and quality improvements. Analyze and plan labor utilization, layout of equipment and workspace, and workflow for maximum efficiency while meeting customer demand. Lead and participate in continuous process improvement initiatives. Show less
-
-
-
HNI Corporation
-
United States
-
Furniture and Home Furnishings Manufacturing
-
700 & Above Employee
-
Focus Factory Manager
-
Feb 2011 - Mar 2012
Manage operations of case goods manufacturing factory with a staff of 4 supervisors and 44 employees to meet production goals. Drive daily continuous improvement. Participate in product development process from concept through launch to full production. Set Policy Deployment goals and drive results for operations and growing the business. Work with limited administrative and financial resources, requiring creativity and flexibility. Participate in Lean Assessments at sister companies for benchmarking and strategic planning. Show less
-
-
Rapid Contiuous Improvement Engineer
-
Jan 2010 - Feb 2011
Lead the introduction of Kaizen and fostered a culture of change at HBF. Organize improvement projects and events around opportunities for improvement identified in manufacturing and business. Perform as an active change agent to eliminate waste and streamline flow using lean methodologies. Establish methods and metrics for tracking production efficiency and first-pass-yield. Implement MDI and drive visual management into all aspects of the manufacturing environment.
-
-
Process Engineer
-
May 2008 - Dec 2009
Lead and facilitate improvement teams at facilities throughout the organization as part of the Lean Leadership Development program. Study and develop Lean training curriculum and applications under the guidance of Shingijitsu consultants and the Director of Continuous improvement. Conduct lean training for members in positions ranging from executive management to shop floor operators.
-
-
-
Whirlpool Corporation
-
United States
-
Manufacturing
-
700 & Above Employee
-
Process Engineer Coop
-
2005 - 2005
-
-
Education
-
Iowa State University
BS, Industrial and Manufacturing Systems Engineering
Community
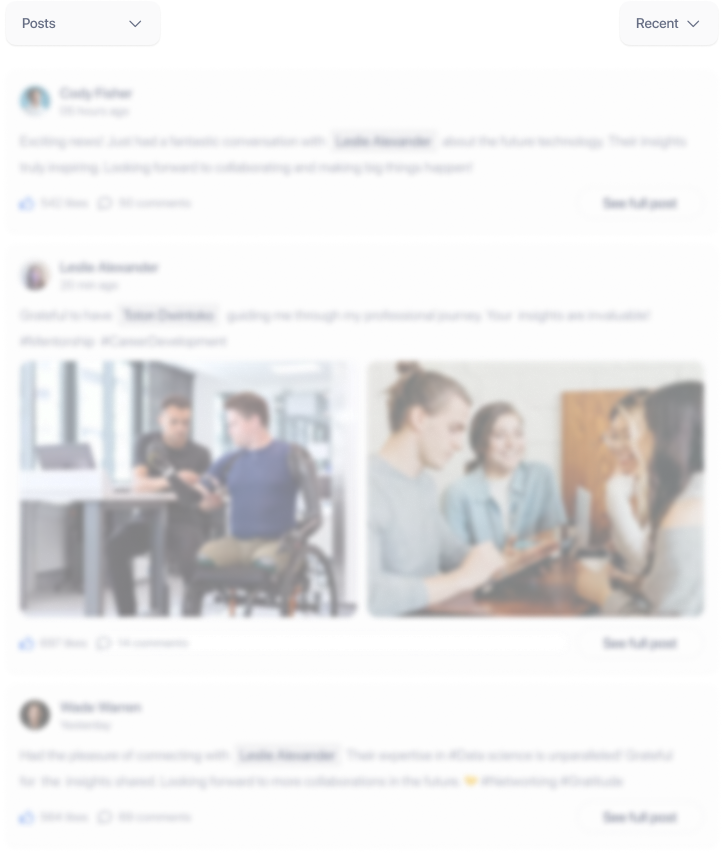