
Adam Turner
Plant Manager at Bissinger's Handcrafted Chocolatier- Claim this Profile
Click to upgrade to our gold package
for the full feature experience.
Topline Score
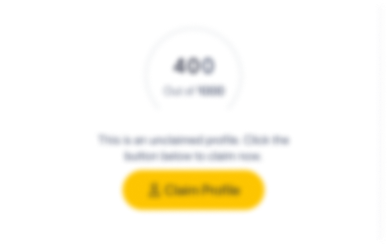
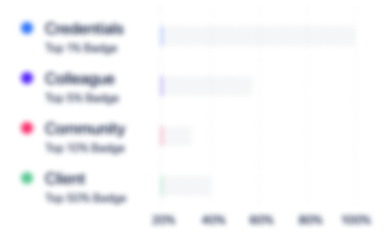
Bio


Experience
-
Bissinger's Handcrafted Chocolatier
-
United States
-
Food & Beverages
-
1 - 100 Employee
-
Plant Manager
-
Feb 2018 - Present
• Facilitate all manufacturing and plant operations; develop and manage 70+ production and warehouse team members• Oversee production planning and scheduling, labor and material management, inventory, shipping, and receiving• Develop continuous improvement activities that drive increased capacity and efficiency while reducing costs• Create, lead, maintain, and measure effectiveness of relevant continuous improvement opportunities• Quickly became ERP and MRP subject matter expert
-
-
Sales Operations Manager
-
May 2017 - Feb 2018
• Managed sales and operations coordination while leading both the wholesale and direct-to-consumer customer service teams• Facilitated successful communication between operations and sales departments• Ensured accurate sales forecasting was established and operations was properly executing to meet current and projected demands• Developed and managed measurements for sales velocity, forecast accuracy, and effective order fulfillment• Created processes and tools for effective management of peak season demand spikes• Tracked and cross-checked broker commissions ensuring accounting accuracy
-
-
Production Support Manager
-
Feb 2015 - May 2017
• Supervised all warehouse, inventory, shipping, and receiving teams; managed logistic contacts for in/outbound materials• Managed, developed, and oversaw warehouse, order fulfillment, inventory control, shipping, and receiving team members• Developed a process for inventory controls and material movement; implemented the Kanban Method for inventory rotation• Planned and executed the annual Physical Inventory; introduced a cycle count audit program• Created processes and metrics that saw an inventory accuracy improvement• Modernized inventory methods which yielded an improvement of on-time shipping
-
-
Efficiency Engineer
-
Apr 2013 - Feb 2015
• Project Manager for all continuous improvement activities• Redesigned the order fulfillment process and improved efficiency for enrobing processes• Analyzed data and developed metrics to monitor production efficiency, labor goals, and material consumption• Integral in ERP implementation, data migration, and process development• Increased shipping capacity from 800 to 1200 per shift
-
-
-
Boeing
-
United States
-
Aviation and Aerospace Component Manufacturing
-
1 - 100 Employee
-
Supply Chain Specialist
-
Apr 2010 - Apr 2013
• Managed the support contract supply chain for the United Kingdom RAF fleet of AV8B Harriers• Created, monitored, and updated the supply forecast
-
-
Procurement Coordinator
-
Jul 2009 - Mar 2010
-
-
-
Heidemann Associates
-
United States
-
Accounting
-
Engineering Intern
-
Jun 2007 - Aug 2007
•Assisted with consolidation of Springfield branch and merging it with the St. Louis office by preparing, organizing and transferring necessary electronic data•Provided support for various legal obligations such as arranging necessary documentation in regards to ongoing legal matters•Provided additional support to the accounting division, such as interpreting account information and readying accounts for payment. •Assisted with consolidation of Springfield branch and merging it with the St. Louis office by preparing, organizing and transferring necessary electronic data•Provided support for various legal obligations such as arranging necessary documentation in regards to ongoing legal matters•Provided additional support to the accounting division, such as interpreting account information and readying accounts for payment.
-
-
-
Hubbell Power Systems
-
United States
-
Appliances, Electrical, and Electronics Manufacturing
-
700 & Above Employee
-
Engineering Co-op
-
Jan 2006 - Aug 2006
•Completed an Industrial Engineering Co-op program, which involved performing various engineering tasks, such as statistical analysis and preventative equipment maintenance•Created and implemented new belt drive for synthetic fuse tube carts to improve the life span of the drive belts•Designed and implemented new assembly racks and overhead tool suspension system to be used in the anchor extension assembly work station, which reduced the risk of worker injury due to repetitive stress activities and improved productivity •Tracked data and performed statistical analysis regarding equipment reliability and availability•Scheduled various maintenance and tooling jobs in order to prevent equipment malfunction
-
-
Education
-
University of Missouri Trulaske College of Business
Masters, Business Administration -
University of Missouri-Columbia
Bachelors, Industirial and Manufacturing Systems Engineering
Community
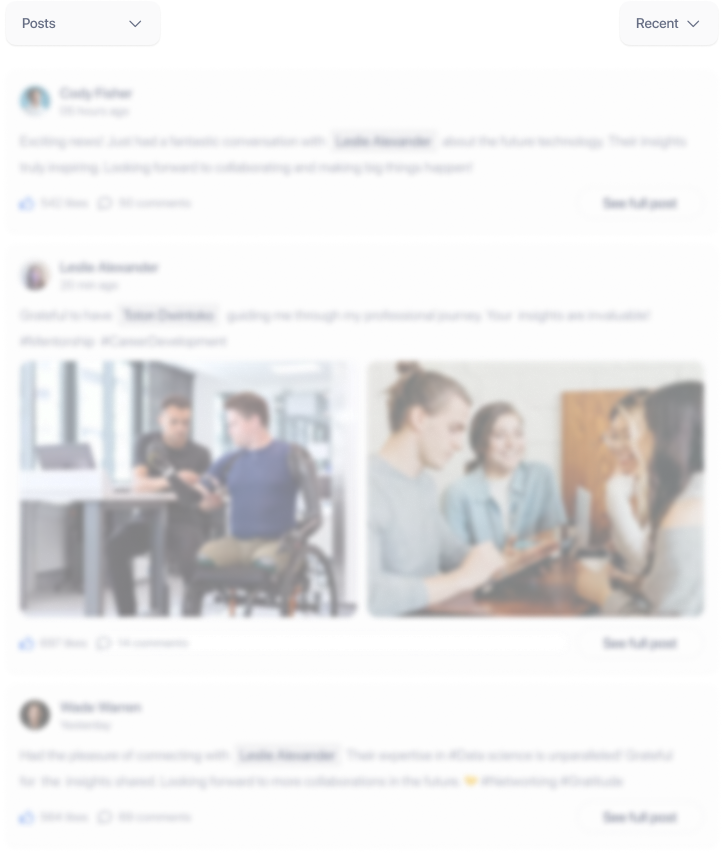