Aaron Suever
Controls Engineer at Central Process Engineering- Claim this Profile
Click to upgrade to our gold package
for the full feature experience.
-
German Limited working proficiency
Topline Score
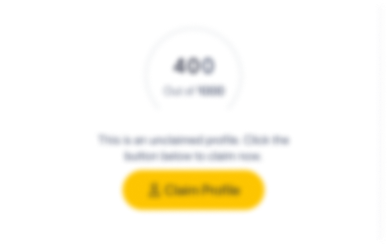
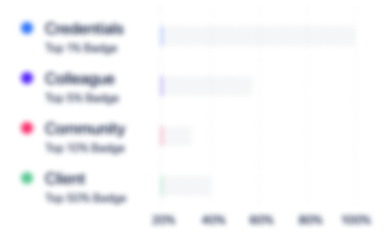
Bio


Experience
-
Central Process Engineering
-
United States
-
Motor Vehicle Manufacturing
-
1 - 100 Employee
-
Controls Engineer
-
Nov 2017 - Present
-
-
-
Shick Esteve
-
United States
-
Automation Machinery Manufacturing
-
100 - 200 Employee
-
Controls Engineer
-
May 2014 - Nov 2017
Provider of Dry and Liquid Ingredient Handling Systems, primarily for the baking industry. • Design electrical controls for dry/liquid ingredient-handling systems. • Controls support for in-house Test Lab/Product R&D. • Projects range from small service contracts/modifications, to controls upgrades from PLC-5/SLC-500/RSView, to system expansions/new production lines. • Involvement with projects ranging from sales quote phase, through Bill of Materials/purchasing, panel checkout, system simulation and testing, startup on-site, and support. But strongest focus on PLC/HMI development, and on-site startup or remote startup support for projects. • In-House Test Lab/R&D support includes testing vendor products for use in sold systems, as well as developing custom products in-house for use on systems, and implementing Test Lab system changes/re-configurations to test specific process scenarios. • Served as interim Controls Quote resource, until a permanent resource could be hired (approximately 5 months). Show less
-
-
-
W+D North America Inc.
-
Overland Park, KS
-
Electrical Service/Support
-
Apr 1997 - May 2014
High-speed paper-converting/printing equipment OEM • Electrical Department service/support for all equipment manufactured or sold by 100+ year-old German parent company. Due to high quality/long life of equipment, a wide range of technologies and designs supported, from relay control up to ControlLogix, with many different vendor sub-systems. • Technical support to in-house, parent company, and customer end-users. Experienced at supporting a wide variety of customer skill levels, backgrounds, language proficiencies, and personalities. • On-call support after normal business hours. • Supported international customers during parent-company “after-hours” times, and coordinated service/support with parent company (when necessary). • Performed “ExpertOnline” remote online troubleshooting/diagnostics support for new or upgraded equipment. • Emergency and planned service trips when required; mostly domestic travel, but also some international travel. • Installation and start-up of equipment in the field. • Equipment moves and upgrades/updates/retro-fits. • Trained customer operators, and customer maintenance personnel, either on-site, over the phone, or in-house. • Prepared procedures and other documents for various audiences. • Customer and in-house special projects. • Assisted customers with identification/procurement of original or suitable replacement parts. Provided instructions or assistance for non-direct replacements. • Configured, tested, and/or programmed spare parts and replacement parts before stocking or shipping to customers, as required. Pre-fabricated electrical assemblies, as required. • Repaired various equipment components, or arranged for repairs from vendor suppliers. • In-house troubleshooting/support of test equipment and capital equipment related to OEM parts manufacturing operations and Electrical Department operations. • In-house computer and software support for Electrical Department. Show less
-
-
Education
-
University of Michigan
B.S., B.S.E., Biology, Electrical Engineering
Community
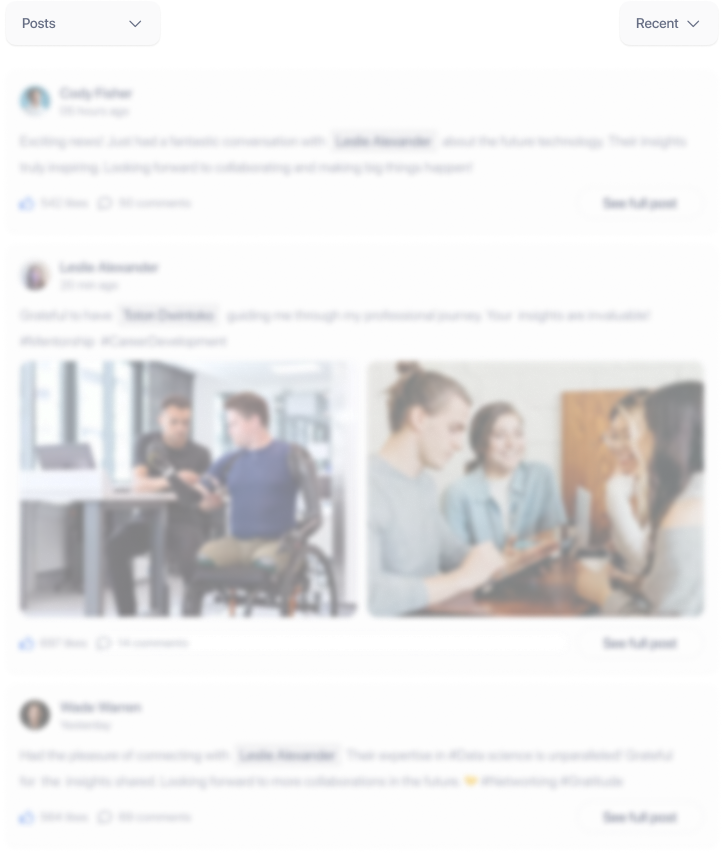