Aaron Martz
General Manager at interVac Design- Claim this Profile
Click to upgrade to our gold package
for the full feature experience.
Topline Score
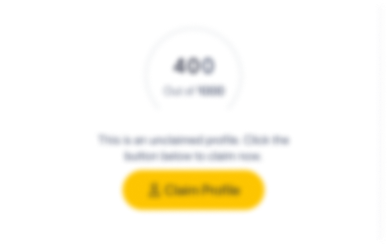
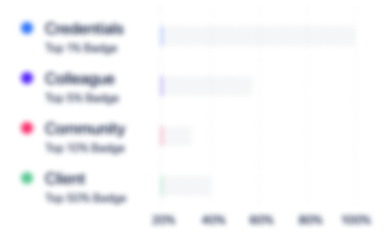
Bio


Experience
-
interVac Design
-
United States
-
Manufacturing
-
1 - 100 Employee
-
General Manager
-
Oct 2021 - Present
-
-
-
Interplex
-
Singapore
-
Appliances, Electrical, and Electronics Manufacturing
-
700 & Above Employee
-
Molding Manager
-
Oct 2019 - Oct 2021
At Inter plex I am responsible for two different molding plants; one automotive and one medical. We run each plant 24 hours a day 6 days per week. My tasks have been to reduce overtime, improve safety, reduce IDL costs, launch new programs, scrap reduction, 5S, and improve our over all OEE. Together as a team we have reduced overtime by nearly $275,000 annually (26 DL and IDL employees) reduced $200,000 in IDL personnel as well as improved our medical plants OEE from 72% to 87% and automotive from 48% to 75%. My responsibility also includes taking over an existing cell from another plant. The OEE at the other plant was 62%. We have successfully brought that product line to 96.5% and reduced the cycle time from 58 seconds to 42.5 seconds. Develop and maintain a monthly budget Responsible for department KPI Responsible for two (2) different plants; automotive and medical Responsible for new product launches Ensured all appropriate documentation is submitted and followed Developed several work instructions Reel – to – Reel insert micro-molding APQP Process Scrap reduction from 35% to 2% Improve the departments overall OEE from 58% to 79% in 8 months Reduce overtime from $20,000 per month to $1,000 and reduced the headcount from 32 to 20 (IDL and DL) Implemented eDarts on two machines Redesigned the molding floor for 5S and workflow to reduce waste Installed safety devices on all molding machines to make them OSHA compliant Successfully submitted Capital Expense requests to corporate to receive a total of $750,000 in 12 months Developed new processes from Vertical to Horizontal machines Show less
-
-
-
National Molding, LLC.
-
United States
-
Plastics Manufacturing
-
1 - 100 Employee
-
Process Engineering Manager (Leadership Team)
-
Jan 2019 - Oct 2019
PROCESS ENGINEERING MANAGER—NATIONAL MOLDINGIn April we eliminated the position of Plant Manager. The COO named five of the department managers as a unit to oversee the plant and its daily operations. I now have 1/5 of the roll of plant manager as well as my other processengineer duties. I have a total of 18 direct reports including process engineers and process technicians. As a teamwe have restructured the process technicians' duties and responsibilities allowing us to focus on decreasing ourmachine downtime. During this time, we have also taken the responsibility to merge another entire plant within ourown. PPAP and re-validations are also underway and my responsibility to see them through in a timely manner.Part of the Plant Leadership TeamResponsible for terminating, hiring, disciplining, training employeesReduce Scrap by 10% plant wideReview molds and develop a plan to obtain full cavitation/optimizationDevelop a plan to best optimize the Hetero cavity / core system Develop the maintenance staff to successfully maintain / troubleshoot 105 molding machinesResponsible for Scheduling Technicians to maintain a 24/7 operationResponsible for 24 IDLInstall and develop processes on 16 eDartsImplement Decoupled Molding plant wideTwo shot molding machines Show less
-
-
Process Engineering Manager
-
Dec 2018 - Jan 2019
In December I was quickly promoted to the Processing Engineering Manager. My duties remained the same as well as attending KPI meetings, overseeing the other 3 process engineers. My new focus was also to begin training allthe process technicians and getting all 12 eDART's on-line and functioning. I obtained my RJG Train the Trainer during this time.
-
-
SR. Process Engineer
-
Sep 2018 - Dec 2018
At National Molding I began as a SR. Process Engineer. Starting with validating new molds with gate seal, fill flow, load sensitivity, check ring, dynamic cavity imbalance, locating sensors (RJG), documenting process changes,supporting production with process and troubleshooting needs, as well as cycle time and scrap reduction. Also didcurrent production job transfers in between different molding machines utilizing machine outputs.
-
-
-
Burnt Offerings LLC
-
United States
-
Business Owner
-
May 2016 - Oct 2019
Owner and Operator of a Food Truck based in Northern Michigan serving up BBQ. We do weddings, corporate parties, graduations, rally’s and many more. Contact us to book your special day! If you are looking for something tasty that is grilled or smoked, I’m positive we can do it! Owner and Operator of a Food Truck based in Northern Michigan serving up BBQ. We do weddings, corporate parties, graduations, rally’s and many more. Contact us to book your special day! If you are looking for something tasty that is grilled or smoked, I’m positive we can do it!
-
-
-
Harbor Light Community Chapel
-
United States
-
Religious Institutions
-
1 - 100 Employee
-
Facilities Director
-
Dec 2016 - Aug 2018
At Harbor light I was responsible to implement several cost saving actives throughout the church and the school. Some of the projects was to replace all the lighting in nearly 65,000 square foot buildings with an ROI of 9 months, remodeling projects estimated at $250,000, also implemented and updated several safety violations brining the building back up to code. I also supervised 3 direct reports and nearly 50 volunteers at one time. At Harbor light I was responsible to implement several cost saving actives throughout the church and the school. Some of the projects was to replace all the lighting in nearly 65,000 square foot buildings with an ROI of 9 months, remodeling projects estimated at $250,000, also implemented and updated several safety violations brining the building back up to code. I also supervised 3 direct reports and nearly 50 volunteers at one time.
-
-
-
LexaMar
-
Motor Vehicle Manufacturing
-
1 - 100 Employee
-
Continuous Improvement Engineer (RJG implementation)
-
Mar 2014 - May 2016
CONTINUOUS IMPROVEMENT ENGINEER—MAGNA EXTERIORS At Lexmark my main duty was to implement RJG (eDART's) thought out the facility. Other responsibilities were documenting and improving processing conditions by reducing scrap, cycle times and removing some secondary operations. I also lead root cause analyses on several post molding operations saving nearly $5000, 000 over 1.5 years. Also, was involved in training employees on the scientific molding strategies, traveled for new tool launches. Secondary operation reduction Root cause post molding part issues New tool launches Training employees on scientific molding strategies Started/Completed implementation and training of eDART’s plant wide Build EOAT’s Mold design signoff Performed DOE’s on existing programs to reduce cycle time and scrap Implemented several cost reductions to total $1.5 million per year APQP Process Show less
-
-
-
Village of Mesick
-
United States
-
Elected Trustee
-
Aug 2007 - Mar 2014
-
-
-
Spencer Plastics
-
United States
-
Motor Vehicle Manufacturing
-
1 - 100 Employee
-
Process Engineer
-
Jan 1999 - Mar 2014
During my time at SPI, I started at the bottom and worked my way up. My responsibilities were ordering materials, ordering capital equipment, starting up new equipment, mold design reviews, setting molds, two different plant layouts and start-ups, mold troubleshooting, scrap and cycle reductions, new mold start-ups, shipping and receiving, launch RJG (ed Arts), train new employees, machine testing, safety coordinator, perform DOE's, and performed tooling maintenance. Responsible for all processing of plastic molds Responsible for all maintenance of facilities and equipment Semi/Annual machine testing and validation Process testing Implementing and monitoring process parameters Mold maintenance Safety Coordinator DOE’s Purchase machines and auxiliary equipment Two plant start-ups Developing processes for prototypes; leading to production Show less
-
-
Education
-
Indiana Wesleyan University
Master's degree, Substance Abuse/Addiction Counseling -
RJG inc
Train the Trainer Certification, Scientific Molding -
Indiana Wesleyan University
Bachelor of Science (B.S.), Substance Abuse/Addiction Counseling -
Indiana Wesleyan University
Associate of Science (A.S.), Christian Studies -
RJG
Master Molder 2, Injection Molding -
RJG
Advanced eDART -
RJG
Master Molder 1 -
Medical First Responder
-
RJG
Systematic Molding 1 -
Fire Fighter One
Community
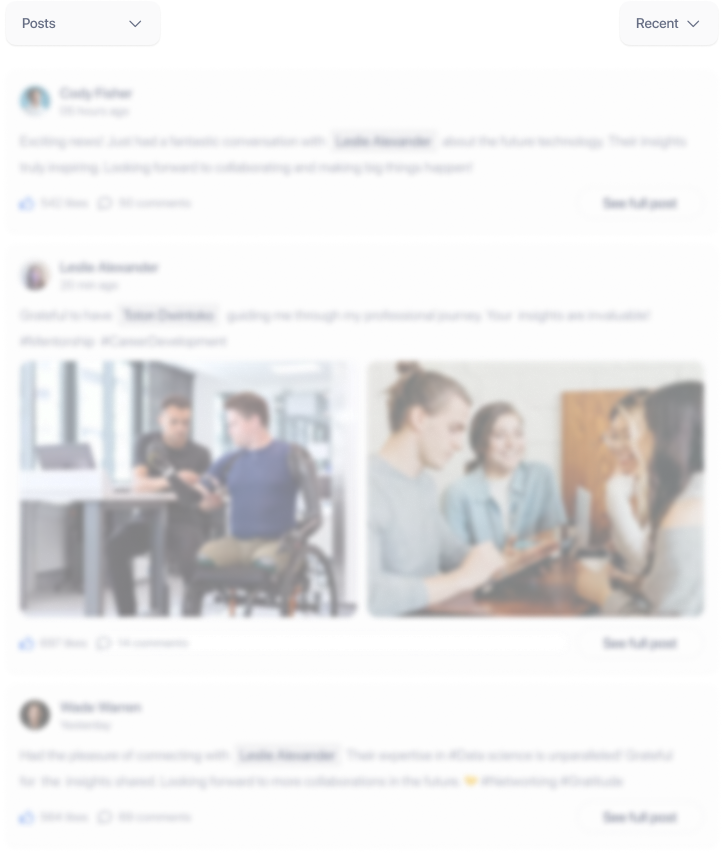