Aaron Deter
Director Cost Accounting & Continuous Improvement at Bolthouse Farms- Claim this Profile
Click to upgrade to our gold package
for the full feature experience.
Topline Score
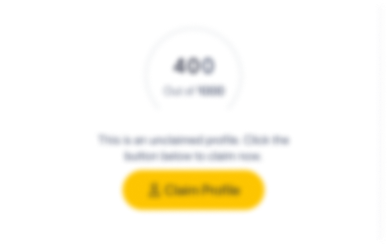
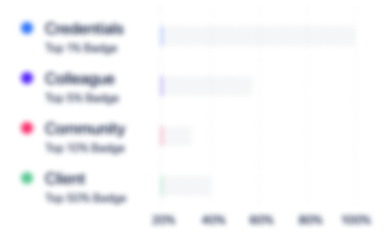
Bio

Joseph D Aschwanden
I have had the privilege of working with and taking instruction from Aaron Deter for the last 5 plus years. I have always found Aaron to be a great leader and someone that will see projects and tasks through to their logical conclusion. Having worked with Aaron on a number of tasks and projects, I have found Aaron’s leadership to be top-notch. Aaron provides a very clear picture of what is needed up front with clear and concise communication. In my experience, Aaron rarely misses the mark and is always able to achieve results, even in the most unlikely of situations. Aaron’s diverse background allows him to execute on a wide range of projects, both Finance and IT related. I would HIGHLY recommend Aaron Deter to any organization seeking a proven leader who is dynamic and results oriented! Joe Aschwanden IT Business Analyst/SAP COE Support

Leslie Henriquez-Cano
Aaron is a great supervisor and co-worker. I have work with Aaron for 15 years he is very detailed and straight forward. He has taught me quite a bit over the years which encouraged me to pursue a career with Cost Accounting.

Joseph D Aschwanden
I have had the privilege of working with and taking instruction from Aaron Deter for the last 5 plus years. I have always found Aaron to be a great leader and someone that will see projects and tasks through to their logical conclusion. Having worked with Aaron on a number of tasks and projects, I have found Aaron’s leadership to be top-notch. Aaron provides a very clear picture of what is needed up front with clear and concise communication. In my experience, Aaron rarely misses the mark and is always able to achieve results, even in the most unlikely of situations. Aaron’s diverse background allows him to execute on a wide range of projects, both Finance and IT related. I would HIGHLY recommend Aaron Deter to any organization seeking a proven leader who is dynamic and results oriented! Joe Aschwanden IT Business Analyst/SAP COE Support

Leslie Henriquez-Cano
Aaron is a great supervisor and co-worker. I have work with Aaron for 15 years he is very detailed and straight forward. He has taught me quite a bit over the years which encouraged me to pursue a career with Cost Accounting.

Joseph D Aschwanden
I have had the privilege of working with and taking instruction from Aaron Deter for the last 5 plus years. I have always found Aaron to be a great leader and someone that will see projects and tasks through to their logical conclusion. Having worked with Aaron on a number of tasks and projects, I have found Aaron’s leadership to be top-notch. Aaron provides a very clear picture of what is needed up front with clear and concise communication. In my experience, Aaron rarely misses the mark and is always able to achieve results, even in the most unlikely of situations. Aaron’s diverse background allows him to execute on a wide range of projects, both Finance and IT related. I would HIGHLY recommend Aaron Deter to any organization seeking a proven leader who is dynamic and results oriented! Joe Aschwanden IT Business Analyst/SAP COE Support

Leslie Henriquez-Cano
Aaron is a great supervisor and co-worker. I have work with Aaron for 15 years he is very detailed and straight forward. He has taught me quite a bit over the years which encouraged me to pursue a career with Cost Accounting.

Joseph D Aschwanden
I have had the privilege of working with and taking instruction from Aaron Deter for the last 5 plus years. I have always found Aaron to be a great leader and someone that will see projects and tasks through to their logical conclusion. Having worked with Aaron on a number of tasks and projects, I have found Aaron’s leadership to be top-notch. Aaron provides a very clear picture of what is needed up front with clear and concise communication. In my experience, Aaron rarely misses the mark and is always able to achieve results, even in the most unlikely of situations. Aaron’s diverse background allows him to execute on a wide range of projects, both Finance and IT related. I would HIGHLY recommend Aaron Deter to any organization seeking a proven leader who is dynamic and results oriented! Joe Aschwanden IT Business Analyst/SAP COE Support

Leslie Henriquez-Cano
Aaron is a great supervisor and co-worker. I have work with Aaron for 15 years he is very detailed and straight forward. He has taught me quite a bit over the years which encouraged me to pursue a career with Cost Accounting.

Experience
-
Bolthouse Farms
-
United States
-
Food and Beverage Services
-
500 - 600 Employee
-
Director Cost Accounting & Continuous Improvement
-
Nov 2019 - Present
-
-
-
Blue Diamond Growers
-
United States
-
Food and Beverage Services
-
700 & Above Employee
-
Manager Operations Finance
-
Sep 2015 - Nov 2019
• Manage the ERP cost accounting system for 3 manufacturing plants, 9 sub-contracting plants, and 8 distribution warehouses. Developed and streamlined processes for creating and maintaining Standards. • Identified and resolved integration gaps between Time & Attendance system, Payroll and General Ledger, improving Labor reporting and analysis. • Developed Annual Planning process for Operations group. Delivered Standards and Overhead budgets on schedule for first time in 5… Show more • Manage the ERP cost accounting system for 3 manufacturing plants, 9 sub-contracting plants, and 8 distribution warehouses. Developed and streamlined processes for creating and maintaining Standards. • Identified and resolved integration gaps between Time & Attendance system, Payroll and General Ledger, improving Labor reporting and analysis. • Developed Annual Planning process for Operations group. Delivered Standards and Overhead budgets on schedule for first time in 5 years. • Manage Capital Project accounting; eliminated 1 year backlog of completed, but uncapitalized projects. Developed processes and reporting tools to drive timely capitalization. • Assess and value cost reduction projects of over $20 million. Show less • Manage the ERP cost accounting system for 3 manufacturing plants, 9 sub-contracting plants, and 8 distribution warehouses. Developed and streamlined processes for creating and maintaining Standards. • Identified and resolved integration gaps between Time & Attendance system, Payroll and General Ledger, improving Labor reporting and analysis. • Developed Annual Planning process for Operations group. Delivered Standards and Overhead budgets on schedule for first time in 5… Show more • Manage the ERP cost accounting system for 3 manufacturing plants, 9 sub-contracting plants, and 8 distribution warehouses. Developed and streamlined processes for creating and maintaining Standards. • Identified and resolved integration gaps between Time & Attendance system, Payroll and General Ledger, improving Labor reporting and analysis. • Developed Annual Planning process for Operations group. Delivered Standards and Overhead budgets on schedule for first time in 5 years. • Manage Capital Project accounting; eliminated 1 year backlog of completed, but uncapitalized projects. Developed processes and reporting tools to drive timely capitalization. • Assess and value cost reduction projects of over $20 million. Show less
-
-
-
Raley's
-
United States
-
Retail
-
700 & Above Employee
-
Accounting Manager
-
Apr 2013 - Aug 2015
• Developed processes to analyze purchasing cost and reduce vendor over payments. • Coordinated the development of structures and procedures, establishing the foundation for ERP “procure to pay” process. • Managed the Electronic Data Interchange (EDI) upgrade and transition with objective of leveraging additional functionality to streamline business processes. • Developed processes to analyze purchasing cost and reduce vendor over payments. • Coordinated the development of structures and procedures, establishing the foundation for ERP “procure to pay” process. • Managed the Electronic Data Interchange (EDI) upgrade and transition with objective of leveraging additional functionality to streamline business processes.
-
-
-
The Coca-Cola Company
-
United States
-
Food and Beverage Services
-
700 & Above Employee
-
Senior Accounting & Systems Integration Manager
-
Sep 2009 - Apr 2013
• Managed Operations Accounting teams, including Sales Accounting, Cost / Inventory Accounting, Accounts Payable, Accounts Receivable and Financial Reporting. • Developed and optimized policies and procedures that insured the integrity of information flow and the coordination of the accounting teams with the business units. • Coordinated operations section of annual audit. Reduced related audit time by 50%. • Streamlined period end close processes, balance sheet reconciliations, and… Show more • Managed Operations Accounting teams, including Sales Accounting, Cost / Inventory Accounting, Accounts Payable, Accounts Receivable and Financial Reporting. • Developed and optimized policies and procedures that insured the integrity of information flow and the coordination of the accounting teams with the business units. • Coordinated operations section of annual audit. Reduced related audit time by 50%. • Streamlined period end close processes, balance sheet reconciliations, and financial reporting. Reduced period end close from 15 days to 3 days. • Performed Financial Analysis for finished product produce vs. buy decisions, machinery & equipment purchases, and technology improvement projects. Show less • Managed Operations Accounting teams, including Sales Accounting, Cost / Inventory Accounting, Accounts Payable, Accounts Receivable and Financial Reporting. • Developed and optimized policies and procedures that insured the integrity of information flow and the coordination of the accounting teams with the business units. • Coordinated operations section of annual audit. Reduced related audit time by 50%. • Streamlined period end close processes, balance sheet reconciliations, and… Show more • Managed Operations Accounting teams, including Sales Accounting, Cost / Inventory Accounting, Accounts Payable, Accounts Receivable and Financial Reporting. • Developed and optimized policies and procedures that insured the integrity of information flow and the coordination of the accounting teams with the business units. • Coordinated operations section of annual audit. Reduced related audit time by 50%. • Streamlined period end close processes, balance sheet reconciliations, and financial reporting. Reduced period end close from 15 days to 3 days. • Performed Financial Analysis for finished product produce vs. buy decisions, machinery & equipment purchases, and technology improvement projects. Show less
-
-
-
Sacramento Coca-Cola Bottling Co., Inc.
-
Sacramento, California Area
-
Cost Manager
-
Oct 2006 - Sep 2009
Cost Manager, October 2006 – September 2009 • Analyzed cost injection points and streamlined financial flow into business activity reducing variances and eliminating all unexplained production variances. • Identified gaps in Master Data structures and procedures; streamlined the organization and process flow, improving efficiency and effectiveness and reducing variances. • Successfully developed and implemented annual budget process that incorporated business manager involvement and… Show more Cost Manager, October 2006 – September 2009 • Analyzed cost injection points and streamlined financial flow into business activity reducing variances and eliminating all unexplained production variances. • Identified gaps in Master Data structures and procedures; streamlined the organization and process flow, improving efficiency and effectiveness and reducing variances. • Successfully developed and implemented annual budget process that incorporated business manager involvement and responsibility. Show less Cost Manager, October 2006 – September 2009 • Analyzed cost injection points and streamlined financial flow into business activity reducing variances and eliminating all unexplained production variances. • Identified gaps in Master Data structures and procedures; streamlined the organization and process flow, improving efficiency and effectiveness and reducing variances. • Successfully developed and implemented annual budget process that incorporated business manager involvement and… Show more Cost Manager, October 2006 – September 2009 • Analyzed cost injection points and streamlined financial flow into business activity reducing variances and eliminating all unexplained production variances. • Identified gaps in Master Data structures and procedures; streamlined the organization and process flow, improving efficiency and effectiveness and reducing variances. • Successfully developed and implemented annual budget process that incorporated business manager involvement and responsibility. Show less
-
-
-
Team Zapata
-
Sacramento, California Area
-
Administration Director
-
Aug 2005 - Oct 2006
• Directed and managed all administrative and financial activities of a small business focusing on Cash Flow Management. • Directed and managed all administrative and financial activities of a small business focusing on Cash Flow Management.
-
-
-
Pacific Coast Building Products
-
Wholesale Building Materials
-
100 - 200 Employee
-
Assistant Plant Manager, Anderson Wall
-
2004 - Aug 2005
• Analyzed statistical data to develop production and shipping capacities. • Developed labor and material tracking processes; analyzed usage and costs leading to improved margins. • Supervised plant Payroll, Human Resources and Safety functions. • Analyzed statistical data to develop production and shipping capacities. • Developed labor and material tracking processes; analyzed usage and costs leading to improved margins. • Supervised plant Payroll, Human Resources and Safety functions.
-
-
-
Pacific Coast Building Products
-
Wholesale Building Materials
-
100 - 200 Employee
-
Division Controller
-
2001 - 2003
• Managed division accounting and finance functions. • Presented and discussed financial information with senior and executive management. • Developed and recommended practices, policies and procedures that improve financial reliability and analysis. • Member of extended SAP implementation team. Duties included: advising project team on business needs, documenting system transactions and staff training. • Member of plant acquisition and closure team. • Managed division accounting and finance functions. • Presented and discussed financial information with senior and executive management. • Developed and recommended practices, policies and procedures that improve financial reliability and analysis. • Member of extended SAP implementation team. Duties included: advising project team on business needs, documenting system transactions and staff training. • Member of plant acquisition and closure team.
-
-
-
Pacific Coast Building Products
-
Wholesale Building Materials
-
100 - 200 Employee
-
Assistant Division Controller
-
1999 - 2000
• Streamlined monthly close process of over 30 retail / distribution locations while training staff of new junior accountants and accounting clerks. Reduced monthly close process from 10 to 8 days. • Streamlined monthly close process of over 30 retail / distribution locations while training staff of new junior accountants and accounting clerks. Reduced monthly close process from 10 to 8 days.
-
-
Education
-
University of California, Santa Barbara
Bachelor of Arts (B.A.), Business Economics -
California State University-Sacramento
Economics
Community
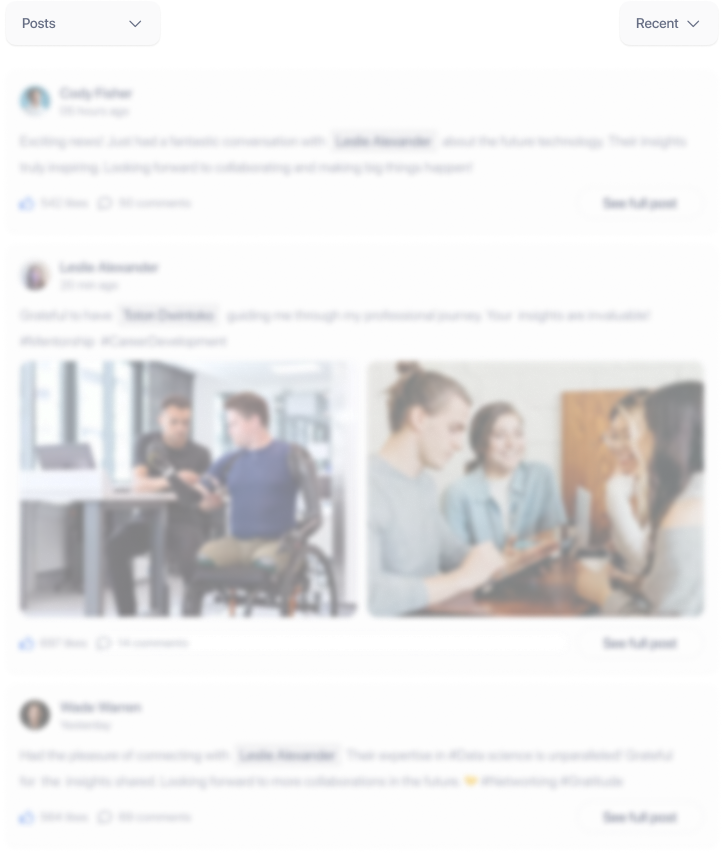