Anthony B.
Machine Shop Engineer at UConn School of Engineering- Claim this Profile
Click to upgrade to our gold package
for the full feature experience.
Topline Score
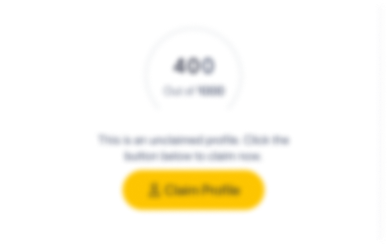
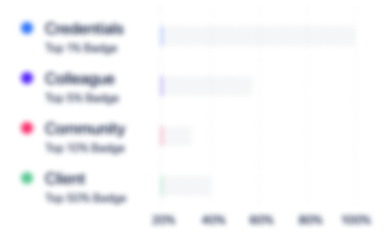
Bio

Sean Saint
I had the pleasure of working with Anthony for a year and a half. During that time I found to him to be a creative, out-of-the-box thinking engineer. He always proved capable of getting things done. Anthony is very capable of manageing vendors and all typical tasks of an engineer, but he excelled when asked to get something done NOW for no money. Here, his creativity allowed him to "McGyver" together solutions to problems that truly impressed me.

Gunther Becht
During my time at Datum3D, I experienced Anthony as a self-motivated, independent co-worker. He has a very solid knowledge required for various engineering task and was quick and interested in learning additional skills necessary in the field of product development and rapid prototyping (i.e. graphic and industrial design or machining).

Sean Saint
I had the pleasure of working with Anthony for a year and a half. During that time I found to him to be a creative, out-of-the-box thinking engineer. He always proved capable of getting things done. Anthony is very capable of manageing vendors and all typical tasks of an engineer, but he excelled when asked to get something done NOW for no money. Here, his creativity allowed him to "McGyver" together solutions to problems that truly impressed me.

Gunther Becht
During my time at Datum3D, I experienced Anthony as a self-motivated, independent co-worker. He has a very solid knowledge required for various engineering task and was quick and interested in learning additional skills necessary in the field of product development and rapid prototyping (i.e. graphic and industrial design or machining).

Sean Saint
I had the pleasure of working with Anthony for a year and a half. During that time I found to him to be a creative, out-of-the-box thinking engineer. He always proved capable of getting things done. Anthony is very capable of manageing vendors and all typical tasks of an engineer, but he excelled when asked to get something done NOW for no money. Here, his creativity allowed him to "McGyver" together solutions to problems that truly impressed me.

Gunther Becht
During my time at Datum3D, I experienced Anthony as a self-motivated, independent co-worker. He has a very solid knowledge required for various engineering task and was quick and interested in learning additional skills necessary in the field of product development and rapid prototyping (i.e. graphic and industrial design or machining).

Sean Saint
I had the pleasure of working with Anthony for a year and a half. During that time I found to him to be a creative, out-of-the-box thinking engineer. He always proved capable of getting things done. Anthony is very capable of manageing vendors and all typical tasks of an engineer, but he excelled when asked to get something done NOW for no money. Here, his creativity allowed him to "McGyver" together solutions to problems that truly impressed me.

Gunther Becht
During my time at Datum3D, I experienced Anthony as a self-motivated, independent co-worker. He has a very solid knowledge required for various engineering task and was quick and interested in learning additional skills necessary in the field of product development and rapid prototyping (i.e. graphic and industrial design or machining).

Experience
-
UConn School of Engineering
-
Storrs Mansfield, Connecticut, United States
-
Machine Shop Engineer
-
Mar 2023 - Present
-
-
-
Stryker
-
Shirley, Ma
-
Principal Mechanical Engineer
-
Feb 2020 - Aug 2022
• Designed, developed, prototyped, and tested accompanying tools to aid in Robotic Assisted Surgery (RAS) under FDA/ISO standards. These include the following: o Computed Tomography (CT) and Infrared (IR) trackable instruments and patient arrays. o Calibration fixtures and handheld surgical planning instrumentation. • Designed test fixtures to measure whole system accuracy. • Collaborated with marketing and surgeons in Voice of Customer (VOC) reviews to assess their needs and thoughts on the products that were being developed. This aided in product development for defining the User Needs that was integral to our Design and Development Plan (DDP). • Worked with global Stryker teams to align supporting design/project phases to meet the product launch schedule. • Collaborated with cross functional teams and outside design firms to create a product harmonization strategy for the Product Look and Feel (PLF). • Led the Design for Manufacturing (DFM) of a robotic arm used for RAS which led to improving the function, accuracy, and manufacturability. Show less
-
-
-
Flexion Therapeutics
-
Burlington, Ma
-
Medical Device Engineer
-
Jul 2018 - Feb 2020
• Supported the Lifecycle Management (LCM) of Zilretta® by designing and producing working conceptual prototypes for in-house evaluations which will be used to guide the next Zilretta® product image direction. • Leading the Design Control tasks in support of new indications for Zilretta® following under 21 CFR Part 820 and ISO 13485 Quality guidelines. • Traveled to overseas manufacturing plant to identify and mitigate design and process flaws within the drug filling line and was able to decrease vial rejections from 20% to 3% which recovers $250K of lost revenue per run. • Designed test fixtures and set up experiments for sterility and accelerated ageing tests. • Assisted in the development of a new product image, set to be released in 2026. • Jumpstarted the preliminary packaging designs to relay the conceptual direction for an outside design firm. Show less
-
-
-
Discover Echo Inc.
-
9530 Padgett St Suite 101, San Diego, CA 92126
-
Senior Product Development Engineer
-
Oct 2013 - May 2018
Starting in a spare bedroom, the Revolve Microscope was created. As part of the small founding team, we developed both an Upright and Inverted Microscope in one. We had also leveraged today’s technology to implement a tablet and cloud-based technology to an archaic realm. I led the ME team in the design and build of a robust and fully functional prototype which has now evolved into a viable, high precision product found in many prestigious Colleges and research facilities. The ability to prototype quickly, being budget conscience and designing for manufacturability has allowed our team to get to market as fast as we did. • Led the ME team to swiftly design and build the first Revolve microscope for validation and funding. • Validated subassemblies throughout the design phase with working prototypes which consisted of FDM, CNC, mill, lathe, general shop skills, optics, and electromechanical integration of motors, PCBs, sensors, LEDs and actuators. • Collaborated with the software, electrical and industrial design teams for seamless integration of subsystems. • Assisted in the conception of multiple patented designs (US20160238829A1). • Created all the drawings (GD&T) and documents (SOPs & Assembly Drawings) for my projects, sourced the hardware and machine shops, followed through on delivery and first article inspections, assembled and tested all pertaining systems, wrote ECOs to mitigate any issues and then transitioned it to manufacturing. • Diligently worked with customers, sales and manufacturing to find and correct flaws or issues in the system. • Worked creatively to reduce cost with DFM/A while on-boarding overseas manufacturers. • Created and fabricated test/assembly fixtures for manufacturing. • Designed a laser cut wooden microscope for trade show swag which turned into a popular aid for teachers to use in their introductory to biology classes. • Developed a remote electronic focusing controller for the Rebel microscope.1 Show less
-
-
-
Spinal Elements, Inc.
-
Carlsbad, CA
-
Senior Product Development Engineer
-
May 2009 - Aug 2013
At Spinal Elements, I was part of both the cervical and lumbar team. I was the sole engineer that brought to market the Sapphire Plate, Mercury MIS and the Controlled Delivery Systems. The Sapphire and Mercury MIS systems had featured implants and/or surgical instrumentation. Each product also complied with FDA/ISO regulations and standards. I was also involved in the training and clinical trials for these products. • Designed, developed and brought to market the Sapphire® Anterior Cervical Fixation Plate System which has been successful in the field • Designed and developed the Mercury® Classic MIS Tower and Controlled Delivery Systems • Completed ground-up designs of several implants, surgical instruments and system component trays • Collaborated with surgeons and marketing to define product specifications • Used rapid prototyping to prove out feasibility of initial concepts • Performed verification testing on mechanical and cadaveric specimens to FDA standards • Attended clinical studies with surgeons and used their feedback to hone in the design/procedure Show less
-
-
-
-
R&D Engineer
-
Oct 2007 - Feb 2009
At Alure Medical (Now Refine Medical), we developed a minimally invasive soft tissue support devices for mastopexy in the aesthetic surgery market. I was part of a four person Engineering team which developed multiple devices for soft tissue support. These devices were in compliance with FDA/ISO regulations that led to human clinical trials and a 510(k). • Collaborated in the design of a minimally-invasive aesthetic soft tissue system • Complied with FDA/ISO standards and regulations for design control and manufacturing processes • Turned novel ideas into working medical prototypes and filed record of invention for the company’s patent portfolio (US20100331612A1) • Selected materials to demonstrate proof of concept. Engineered and built test fixtures for acute and chronic FDA guideline in vitro testing • Supervised degreed engineering technician Show less
-
-
-
Breakaway Imaging, LLC
-
Littleton, MA
-
Mechanical Engineer
-
Jan 2004 - Aug 2007
At Breakaway Imaging (Now Medtronic Navigation) we were a small team of seven building a patient-centric mobile medical imaging system, the O-Arm, which provides 2D (fluoro) and 3D (volumetric) functionality. My role was to design, develop and prototype the base chassis (drive, positioning and lift/shift hydraulic system), rear cabinet (electrical packaging) and the outer skins. • Contributed to the design and build of a patient-centric mobile medical imaging system, the O-Arm®, which provides 2-D (fluoroscopy) and 3-D (volumetric) functionality • Designed and built the base cart of the O-Arm® consisting of a drive, positioning, and lift/shift hydraulic system • Assisted in the overall Industrial Design of prototype and final product • Primarily designed outer shells of the O-Arm® • Designed and built the rear cabinet of the O-Arm® Redesigned pre-existing generator Packaged electronic system within rear cabinet • Fabricated breadboard and prototype involving extensive CNC work and general machining skills Show less
-
-
-
-
Solidification Simulation Engineer
-
Feb 2003 - Dec 2003
At Wollaston Alloys, I used MagmaSoft and SolidWorks to conceptualize and simulate the casting process in order to alleviate all discrepancies in the final molded part. I also assisted in streamlining the casting system and finding the potential flaws at the production level. • Ran solidification simulations and established casting processes • Utilized MagmaSoft (casting simulation software) to alleviate all porosity, hot spots and discrepancies within the castings • Supervised the recognition and repair of system flaws at production level Show less
-
-
-
Diaphorm Technologies, LLC.
-
Salem, NH
-
Project Engineer
-
Mar 2000 - Nov 2002
As my first job out of College, I started as a Project Engineer designing and building various machines for the production of composite products. I also worked on the integration of electric and Hybrid electric power/drive systems into standard vehicles. I also maintained the role of DSA (Departmental Software Administrator) and graphics designer for manuals and brochures. • Designed and built a specialty automated binder applicator, which performs within precise pre-forming requirements • Fabricated equipment consisting of general machining, sheet metal enclosures, some electrical field wiring, welding (TIG, MIG, and stick) and painting • Aided in the design of the electrical packaging for the DC-DC Converter (DC 345) and various other prototypes • Utilized Photoshop to create graphics used in equipment operation manuals and logos for our division Show less
-
-
-
DaTum3d
-
Watertown, MA
-
Co-op Engineer
-
1999 - 1999
While in College, I had the opportunity to start cutting my teeth as an aspiring Engineer. At DaTum3D, I had worked on the development and build of test fixtures for the computer industry as well as some mechanical design on a prototype lamination machine. Here I had learned how to run CNC's and really hone in my machine shop abilities in prototyping. While in College, I had the opportunity to start cutting my teeth as an aspiring Engineer. At DaTum3D, I had worked on the development and build of test fixtures for the computer industry as well as some mechanical design on a prototype lamination machine. Here I had learned how to run CNC's and really hone in my machine shop abilities in prototyping.
-
-
Education
-
Tufts University
-
Wentworth Institute of Technology
BSME
Community
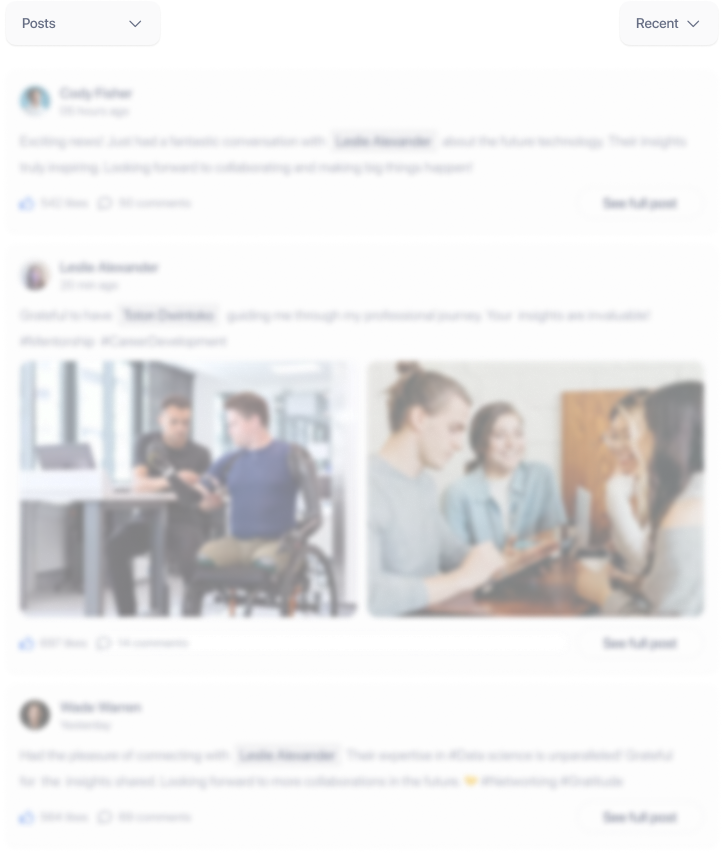