Jeanna Calhoun
Production Control Supply Chain and Parts Mgmt at Toyota Motor Manufacturing, Kentucky, Inc.- Claim this Profile
Click to upgrade to our gold package
for the full feature experience.
Topline Score
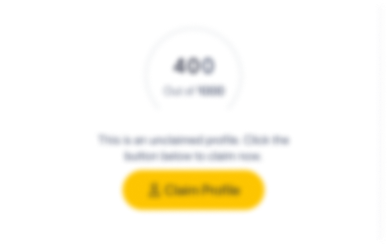
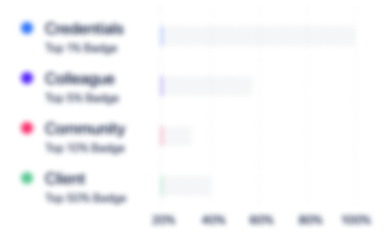
Bio


Experience
-
Toyota Motor Manufacturing, Kentucky, Inc.
-
United States
-
Business Consulting and Services
-
200 - 300 Employee
-
Production Control Supply Chain and Parts Mgmt
-
Sep 2022 - Present
Maintain parts inventory by utilizing Server eKanban System. Daily analysis of all abnormal conditions in the supply chain from North American parts Suppliers. Coordination with suppliers and internal groups for management of crisis situations minimizing impact to production. Develop, visualize & monitor KPI’s, Operating Procedures and Project Schedules. Manage inventory to meet Build Out and Start Up targets with zero impact to production. Partner with External & Internal Logistics groups to reduce internal part shortages and overflow. Request and monitor recovery of abnormal conditions that occur in the supply chain. Show less
-
-
-
Innovative Home Loans
-
United States
-
Financial Services
-
Mortgage Loan Coordinator
-
Jul 2020 - Sep 2022
Ownership of residential mortgage loan files after Origination. Fulfill all requirements to advance the loan to the closing table. This includes obtaining, reviewing, and assembling documentation, along with preparing and submitting files. I work closely with Customers, Loan Officers, and both internal and external partners providing a high level of service in a professional manner. Ownership of residential mortgage loan files after Origination. Fulfill all requirements to advance the loan to the closing table. This includes obtaining, reviewing, and assembling documentation, along with preparing and submitting files. I work closely with Customers, Loan Officers, and both internal and external partners providing a high level of service in a professional manner.
-
-
-
-
Team Operations Coordinator
-
Aug 2014 - Jun 2020
Oversee the daily operations of a fast-growth real estate team. Manage all administrative, marketing, listings and transaction coordination for the team. Implemented systems and procedures to enhance operations and increase sales. Managed the recruiting, hiring, training and ongoing leadership of all future administrative hires. Created business operations manual with Standard Operating Procedures for all processes. Oversee the daily operations of a fast-growth real estate team. Manage all administrative, marketing, listings and transaction coordination for the team. Implemented systems and procedures to enhance operations and increase sales. Managed the recruiting, hiring, training and ongoing leadership of all future administrative hires. Created business operations manual with Standard Operating Procedures for all processes.
-
-
-
-
Production Control and Supply Chain Management Specialist
-
Jul 2009 - Jun 2012
Service Parts Operations: • Responsible for Service Part quality, delivery and performance for over 250 suppliers. • Initiate and support supplier improvements to achieve quality targets. • Initiate actions to prevent the occurrence of any non-conformities relating to product, process, and quality system. • Developed, improved, and managed processes affecting supply to meet personal and departmental objectives. • Managed new model projects and coordinated timing with supply chain . • Project lead for development, implementation and management of Receiving Inspection Operations process. • Developed, coordinated and conducted training for North American suppliers in Toyota procedures, order management and shipping requirements. • Understand aspects of inventory, procurement and supply chain practices. Service Parts Engineering: • Responsible for the establishment, function and service structure for all North American built Toyota vehicles. • Develop and coordinate strategies relative to engineering change instructions (ECI's) and parts technical information with customer groups and external government regulatory agencies Parts Business Planning: • Monitor, analyze and report daily on competitor price changes. • Supplier Financial and Quality Crisis management • Analyze monthly reports and propose countermeasures for improvement through root cause analysis. • Analyze data to determine most cost effective solution for continued service parts supply. Show less
-
-
-
Toyota Motor Manufacturing Kentucky
-
United States
-
Business Consulting and Services
-
200 - 300 Employee
-
Quality Control Team Leader
-
Jun 2005 - Jul 2009
• Supervised, scheduled, and supported 20-25 team members to achieve departmental goals • Responsible for the facilitation of an efficient production operation. • Developed standardized work for processes in group • Trained all team members and ensured they understood all safety and quality keypoints necessary to successfully perform their processes • Entrusted to process confidential employee information and provide coaching to team members of all levels • Provide guidance to management to investigate and resolve group concerns and promote positive employee relations • Increased team and group efficiency by 20% by implementing countermeasures that reduced downtime, increased productivity, and improved quality • Led Kaizen activities that increased team member involvement in process and quality improvements Show less
-
-
-
-
Safety/ Ergonomics Project Lead
-
Jan 2001 - Jun 2005
• Performed accident and early symptoms investigations, posture confirmation and JT/SJT evaluations.• Collaborated with design and engineering to improve part and process workability • Provided direct support to production engineering design changes, new equipment kanbans and served as an ergonomic advisor to Pilot Teams for new model preparation. • Established strong departmental safety support through floor activities including team member involvement, shop audits and countermeasure identification. • Resolve unsafe conditions and establish system that maintains improvements in a constant changing work environment• Developed and conducted training curriculum using PowerPoint, Excel and Word.• Extensive experience of process evaluations and job ratings Show less
-
-
Production Team Member (Body Weld)
-
Nov 1997 - Jan 2001
• Learned all processes in team and rapidly gained a working knowledge of entire group• Participated in development of standardized work for processes in group• Assisted in training team members • Implemented countermeasures that improved production efficiency
-
-
Education
-
Northwood University
BA Business Management, Business Administration and Management -
Ashford University
Master's degree, Teaching and Learning with Technology
Community
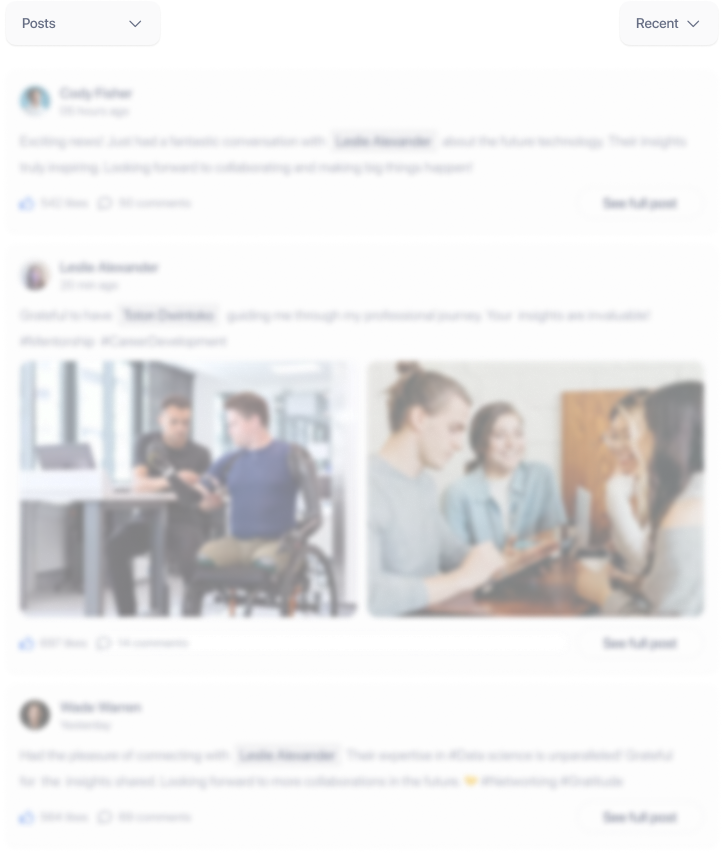