Fred Ullrich
Application Engineer at Dürr Group- Claim this Profile
Click to upgrade to our gold package
for the full feature experience.
Topline Score
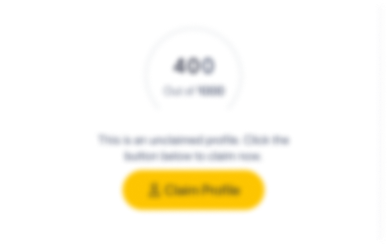
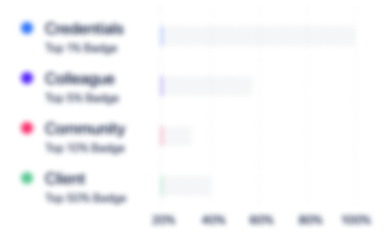
Bio


Experience
-
Dürr Group
-
Germany
-
Machinery Manufacturing
-
1 - 100 Employee
-
Application Engineer
-
Jun 2021 - Present
-
-
-
AkzoNobel
-
Netherlands
-
Chemical Manufacturing
-
700 & Above Employee
-
Project Manager - Projects & Engineering
-
Jan 2013 - Feb 2021
• Engineered a state-of-the-art VOC recovery system for a new manufacturing plant in China. This concentrator and recovery system was a step-change in the control technology, allowing the plant to recover VOC emissions for reuse instead of incinerating them. Made a detailed technical evaluation of the process to prove feasibility, and brought together team members in Asia, Europe, and North America to detail and execute the installation.• Engineered and managed a project to automate and improve capacity of a critical milling system. Result of the project is an eight-fold increase in throughput.• Engineered and managed the installation of a new resin pilot plant.• Engineered and managed manyconstruction and improvement projects, including a raw material warehouse, R&D lab, administrative office, and cold storage warehouse.• Installed spray booth upgrades, resulting in improved operator safety and industrial hygiene, and application quality.
-
-
VOC Expert Group Leader - Operational Eco-Efficiency Programs
-
Nov 2010 - Dec 2012
• Modeled VOC emissions at manufacturing sites around the world, resulting in a 30% reduction in company-wide VOC emissions. These reductions helped AkzoNobel to achieve its goal of being #1 on the Dow Jones Sustainability Index.• Researched and compiled best manufacturing practices and VOC control methods, and summarized their impact on emissions, and their relative cost and applicability to AkzoNobel operations.• Developed the technical competency of engineering and operations peers by sharing these best practices globally, in workshops and webinars.
-
-
Regional Engineering Manager - Industrial Finishes, Europe
-
2004 - Nov 2010
• Developed and implemented a global automated capital approval process using a Sharepoint workflow. With the workflow, reviewer feedback was instantaneous and most approvals were made the same day.• Developed master site plans for our European sites. Evaluated and prioritized their capital projects based on strategic, financial, technical, and safety merits.• Evaluated merger, acquisition, and consolidation opportunities throughout Europe. Insured that capacity, safety, and building and fire code issues were accounted for in the M&A project proposals. • Worked with the corporate Communities of Practice to develop and share mixing, milling, and filling innovations.• Developed, implemented, and maintained an intranet website to share technical standards and best practices with the engineering and operations community.
-
-
Site Consolidation Project Manager
-
2001 - 2004
• Proposed and developed a consolidation project to bring two separate manufacturing operations and an R&D lab together on a single campus. Managed in-house and third-party engineers to develop project scope, site plans, preliminary engineering designs and budgets, and the funding request.• Partnered with state, county, and local regulators to secure approvals and grants. Partnered with neighbors to ensure that their needs and interests were addressed during project development.
-
-
Senior Process Engineer
-
1995 - 2004
• Introduced innovative manufacturing processes to the business: automated bulk dosing systems to improve formulation accuracy; sealed portable tank designs to reduce process emissions and improve operator safety; VOC concentrator technology to reduce the operating cost of traditional VOC control; and a manufacturing cell for safe handling of hazardous pigments.• Engineered and commissioned greenfield coatings manufacturing plants.
-
-
-
Benjamin Moore & Co.
-
United States
-
Manufacturing
-
200 - 300 Employee
-
Project Engineer
-
1990 - 1995
Corporate project and process engineering department. Notable projects: alkyd resin plant in Burlington, Ontario, Canada; emulsion polymer plant in Johnstown, NY; paint plants in Mesquite, Texas, and Vancouver, BC, Canada.--Process design, plant layout, equipment specification, installation and commissioning.--Plant and laboratory air permitting--Industry support and via representation on the National Paint and Coatings Association, Air Quality Committee--Design of innovative tank ventilation systems that were later patented--Computing systems for the engineering group; introduction of AutoCad and AutoPlant Piping software and other design tools.
-
-
Resin Plant Manager
-
1986 - 1990
Alkyd and latex manufacturing plant in Pell City, Alabama, serving 7-8 Benjamin Moore paint plants.-- Management of production personnel and material handlers.-- Production planning.-- Logistics of inbound and outbound freight.-- Plant engineering and maintenance.
-
-
Quality Control Chemist
-
1985 - 1986
-
-
Education
-
University of Michigan
BS, Chemical Engineering -
Fairleigh Dickinson University
MBA, Management
Community
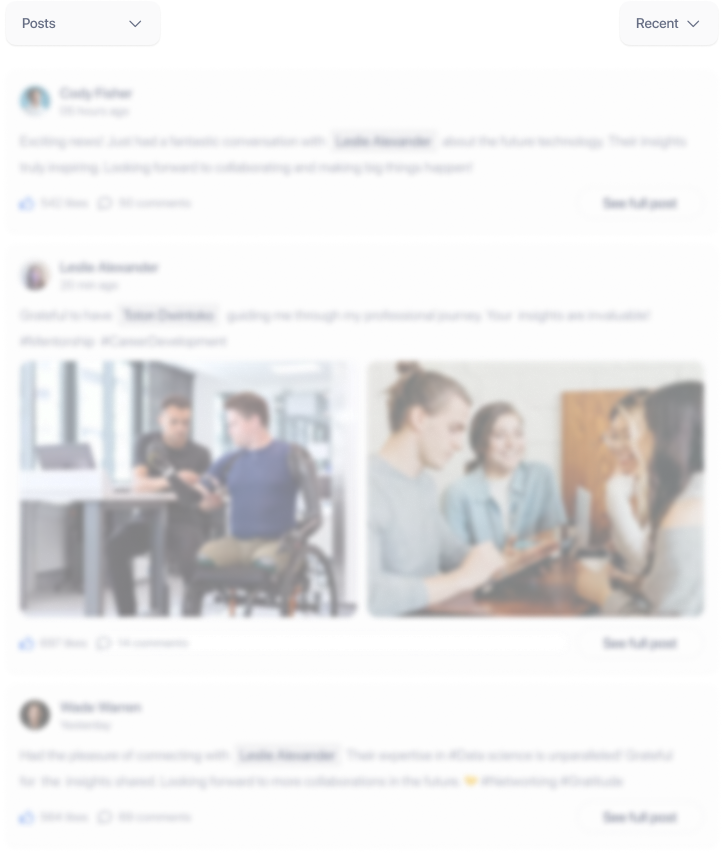