Irshad Patavekar
Consultant - Quality & Trasformation at WNS Denali- Claim this Profile
Click to upgrade to our gold package
for the full feature experience.
Topline Score
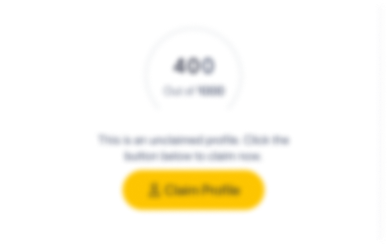
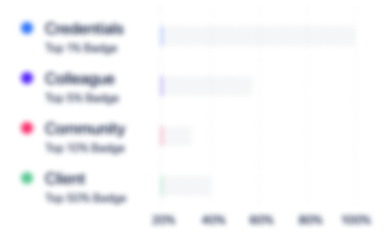
Bio


Experience
-
WNS Denali
-
United States
-
Business Consulting and Services
-
500 - 600 Employee
-
Consultant - Quality & Trasformation
-
Dec 2022 - Present
Pune, Maharashtra, India
-
-
-
Marsh McLennan Global Services India Private Limited (MMGS)
-
India
-
Insurance
-
700 & Above Employee
-
Deputy Manager- Buisness Tranformation Global Metrics
-
Jul 2022 - Dec 2022
Pune, Maharashtra, India
-
-
-
-
Supplier Quality Engineer
-
Jul 2021 - Jul 2022
Pune, Maharashtra, India
-
-
-
Catalydd
-
India
-
Engineering Services
-
1 - 100 Employee
-
SQA Process Improvement
-
Feb 2021 - Jul 2021
Pune, Maharashtra, India * Extensive background includes Quality Management, Quality Assurance, Process Improvement. * Highley skilled at SPC, PFMEA. Risk Analysis and Management, MSA, DMAIC-Lean Six Sigma Methodology. * Proficient in handling customer audits in line with ISO9001:2015/IATF16949:2016. * Able to Perform Process and Product audits in the Product lines and ensure compliance with the Quality Systems and Certification requirements. * Able to Drive team performance, efficiency, and… Show more * Extensive background includes Quality Management, Quality Assurance, Process Improvement. * Highley skilled at SPC, PFMEA. Risk Analysis and Management, MSA, DMAIC-Lean Six Sigma Methodology. * Proficient in handling customer audits in line with ISO9001:2015/IATF16949:2016. * Able to Perform Process and Product audits in the Product lines and ensure compliance with the Quality Systems and Certification requirements. * Able to Drive team performance, efficiency, and motivation support the effective daily operation of the business. * Proficient at overseeing customers escalations & bring the issues to resolution and properly communicating this to the stakeholders. * Able to Identify and drive process improvement opportunities, projects aligned with business initiatives and customer needs and expectations. * Adept to Serve as point of contact for all QA related queries and address the team's crises when they arise through conflict management. * Able to Analyze the Process and Product Concession/deviations and prepare an action plan to reduce the concessions or deviations. * Able to create an environment built on trust, open communication, creative thinking, and teamwork Prepare reports and interact with Operations and support groups regarding quality improvements * Able to Create improvement initiatives that add value to the business, Improve process capability from the SIX SIGMA Greenbelt programs. * Adept to Ensure the full understanding of the existing company policies among employees. * Adept to Minimize Customer issues and concerns proactively. * Adept to Actively contribute to customer visits in the presentation of the company. Show less
-
-
-
-
Jr.Manager-QA
-
Aug 2013 - Sep 2020
Pune Area, India * Responsible for Customer audits and follow-up of corrective actions for audit finding. * Manage and salvage Supplier Non-Conformance materials with the help of customers and suppliers. * Responsible for Conducting periodic MSA(Measurement System Analysis), SPC(Statistical Process Control), and PFMEA(Process Failure Mode and Effect Analysis) at the supplier end ensuring customer specific requirement. * Responsible for receiving customer complaints and initiate Corrective… Show more * Responsible for Customer audits and follow-up of corrective actions for audit finding. * Manage and salvage Supplier Non-Conformance materials with the help of customers and suppliers. * Responsible for Conducting periodic MSA(Measurement System Analysis), SPC(Statistical Process Control), and PFMEA(Process Failure Mode and Effect Analysis) at the supplier end ensuring customer specific requirement. * Responsible for receiving customer complaints and initiate Corrective and Preventive actions for customer quality concerns through 8D and problem-solving techniques. * Streamline the existing processes and establish Standard Operating Procedures(SOP) and Work Instructions and Train the associates on the New SOP'S. * Review of Non-Confirming Products and driving to identifying Root cause Analysis, Permanent Corrective and Preventive Actions, and check the effectiveness of CA and PA with the help of PFMEA and 7 Quality Control Tools. * Manage and Collaborate with suppliers and stakeholders to resolve quality issues. * Responsible for Quality Assurance Activities in Incoming, at supplier end PDI, and Inprocess-Online and Offline Inspection System. * Applied 3S/5s on the shop floor, analyzed inventory model, and trained operators in basic lean six sigma procedures. * Introduced a tagging system to correctly identify and quantify quarantined non confirming parts from the supplier which helped incorrectly evaluation of the cost of poor quality. * Implemented a parallel deployment of supplier rejection analysis to other different sections of the plant. Show less
-
-
-
POONA RADIATORS AND OILCOOLERS PVT LTD
-
Machinery Manufacturing
-
1 - 100 Employee
-
Sr.Engineer-Quality Control
-
Jul 2011 - Jul 2013
Pune, Maharashtra, India * Customer Complaint Handling, Preparing and closing of Non-Conformance ( NC ) reports. * Streamline the existing processes and establish Standard Operating Procedures(SOP) and Work Instructions and Train the associates on the New SOP'S. * Analyzed and took corrective and preventive actions on causes derived from SPC or Cp/Cpk (during Inprocess) and Pp/Ppk (during development) studies. * KPI target failure analysis and follow up through CAPA Reports. * Carry out Layout… Show more * Customer Complaint Handling, Preparing and closing of Non-Conformance ( NC ) reports. * Streamline the existing processes and establish Standard Operating Procedures(SOP) and Work Instructions and Train the associates on the New SOP'S. * Analyzed and took corrective and preventive actions on causes derived from SPC or Cp/Cpk (during Inprocess) and Pp/Ppk (during development) studies. * KPI target failure analysis and follow up through CAPA Reports. * Carry out Layout Inspections and Reporting. * Planning and conducting Internal Audits. * Responsible for the administration of the quality system, including implementation, Compliance, and maintenance of regulatory requirements and International standards. * Monitoring Customer' specific quality issues & initiate quality improvement projects through coordination with customers. * Responsible for leading the team and conduct the pilot run production and provide the pilot run report and get approval for the mass production from the customer. * Determine Supplier scorecards, analyze supplier performance. Identify opportunities for improvements by conducting periodic audits. * Conducting various quality function training for associates.
-
-
Quality Engineer
-
Jul 2010 - Jul 2011
Pune, Maharashtra, India * Review contracts, drawings, routings, purchase orders, shop instructions, and various related production and development plans for quality requirements. * Assist qualification of newly manufactured quality products. * Support and instruct as needed to Quality Inspectors. * Investigate all client complaints and issues. * Identify root cause and respond with corrective action. * Develop and execute plans for quality and control to ensure constant manufacturing continuity… Show more * Review contracts, drawings, routings, purchase orders, shop instructions, and various related production and development plans for quality requirements. * Assist qualification of newly manufactured quality products. * Support and instruct as needed to Quality Inspectors. * Investigate all client complaints and issues. * Identify root cause and respond with corrective action. * Develop and execute plans for quality and control to ensure constant manufacturing continuity and product conformance. * Review, supervise, and review quality documentation as needed. * Participate as Material Review Cross-Functional Team member to review and temper Non-Conforming Material as suitable. * Manage and oversee source inspection activities along with supervising quality documents. * Conduct audits of supplier quality system and approve new suppliers along with verifying ongoing supplier compliance. * Involve as an internal auditor for ISO:9001:2000 process audits of quality management systems. * Develop and execute statistical process controls utilizing apt quality tools plus statistical techniques. * Develop and maintain positive relations and effectual communication lines with all functions, vendors, and clients. * Prepare, supervise, and report suitable and effectual metrics monitoring assigned processes effectiveness. * Support quality goals and objectives along with activities to identify, explain, and resolve quality issues.
-
-
-
Garware Technical Fibres Limited
-
India
-
Textile Manufacturing
-
300 - 400 Employee
-
GET
-
Jul 2009 - Jun 2010
Pune, Maharashtra, India * Completing all tasks set by the Supervisor and assisting wherever possible. * Observing existing strategies and techniques and offering suggestions for improvement. * Conducting research and collating data. * Traveling to different sites and gaining practical experience in new work zones. * Working closely with staff to foster professional values and build good relationships. * Observing health and safety guidelines at all times. * Attending meetings and workshops. *… Show more * Completing all tasks set by the Supervisor and assisting wherever possible. * Observing existing strategies and techniques and offering suggestions for improvement. * Conducting research and collating data. * Traveling to different sites and gaining practical experience in new work zones. * Working closely with staff to foster professional values and build good relationships. * Observing health and safety guidelines at all times. * Attending meetings and workshops. * Submitting to all forms of evaluation during the traineeship. * Compiling reports and delivering presentations to staff members and other stakeholders. Show less
-
-
Education
-
Shivaji University, Kolhapur
Bachelor of Engineering (B.E.), Mechanical Engineering -
Govt. Polytechnic Ratnagiri
Diploma, Mechanical Engineering -
Alfred Gadney High School- Dapoli
SSC, SSC
Community
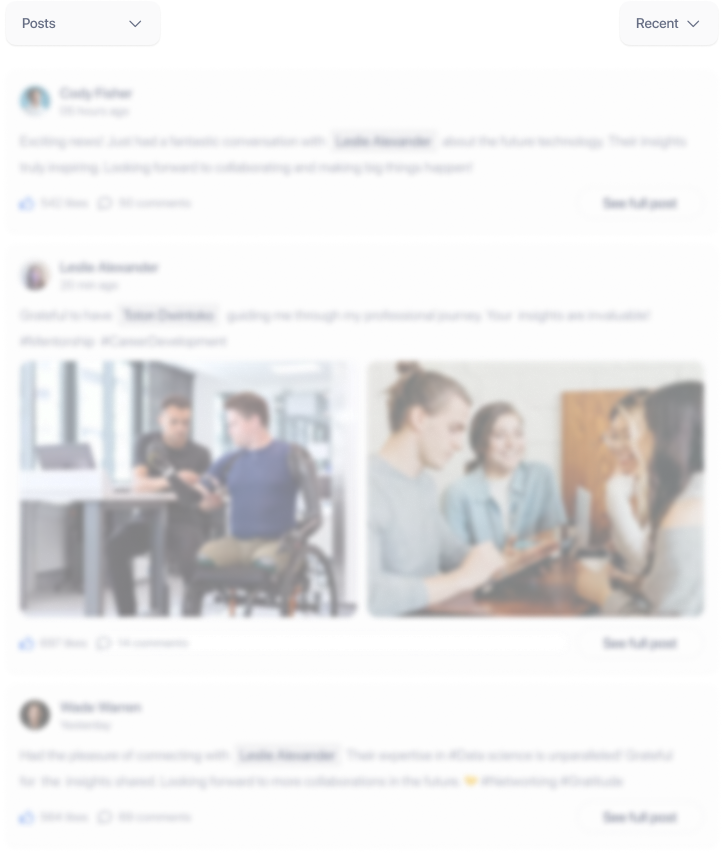