Benoît Arbez
Gestionnaire de patrimoine at VYV 3 Bourgogne- Claim this Profile
Click to upgrade to our gold package
for the full feature experience.
-
English Professional working proficiency
-
Spanish Elementary proficiency
Topline Score
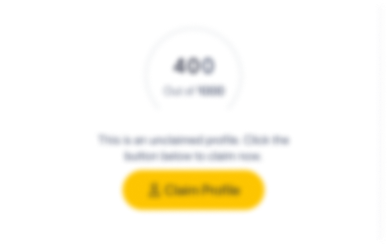
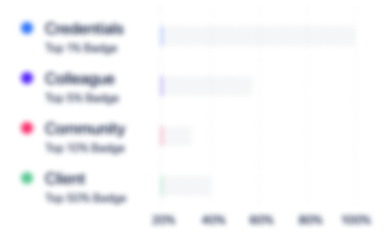
Bio


Experience
-
VYV 3 Bourgogne
-
France
-
Individual and Family Services
-
100 - 200 Employee
-
Gestionnaire de patrimoine
-
Sep 2022 - Present
-
-
-
Ville de Chenôve
-
France
-
Government Administration
-
1 - 100 Employee
-
Responsable pôle bâtiment
-
Oct 2020 - Present
-
-
-
Merck Group
-
Germany
-
Pharmaceutical Manufacturing
-
700 & Above Employee
-
Facilities Manager -Hard services
-
Jul 2015 - Jul 2017
Hard services and project management (building and utilities):Responsible of the facilities installations of the site (24/7), electricity, steam, chilled water, heating water, compress air, vacuum, sprinkler, fire detection system, access control system, HVAC (cleanrooms Class A)… Establish, manage and monitor performance and contracts of suppliers and providers performance through appropriates KPI’s and measure for all hard FM services.Energy monitoring and optimisation within the ISO 50001 certification.Ensuring that quality and safety procedures are respected as well as corporate guidelines and regulatory rules.Business partner for operation staff, and HSE services for the site engineering group.Responsible of the safety management of all subcontractors on site (1FTE dedicated).Managing a team of 5FTE. Manage the repair and maintenance OPEX budget.Hard FM contract awarded in sept 2016.Lead local capital projects: building optimisation, layout modification, new utilities systems, and energy saving… Show less
-
-
Project Manager site engineering
-
Sep 2013 - Jul 2015
Management of projects utilities and building: conception, quotation, scheduling, cost follow-up, construction management, and validation.Construction of 750 m2 of cleanrooms (Class A) for media plate production, 1500m2 of R&D offices and 700m2 of R&D Labs (L2)Refurbishment of 3 mezzanines in production area (600m2), and 1000m2 of office area, lockers etc.
-
-
-
Capsugel
-
United States
-
Pharmaceutical Manufacturing
-
400 - 500 Employee
-
Maintenance Manager (automatism, electricity and utilities)
-
2011 - Sep 2013
Responsible of development, optimisation and the maintenance of the automated systems of the site. Ensuring the availability of the utility systems of the site (24/7). Managing a team of 15 FTE (Engineers, technicians and sub-contractors). Management of hard FM contract and applying it to electricity services.Managing projects of energy conservation (- 6% energy cost of the site) and of automation across sites (US, Belgium, France).
-
-
Utilities Manager
-
2010 - 2011
In charge of infrastructure management for critical utilities (black and clean) for the production (Steam, electricity, compress air, Chilled water, process Air, process water). Managing a team of 3 technicians and sub-contractors.Development of hard FM contract, projects of reliability and energy efficiency of installations (green belt).
-
-
Project Manager
-
2008 - 2010
Project manager for process, utilities and building: conception, quotation, scheduling, cost follow-up construction management, and validation.Conception of centralised cleaning system (3 CIPs) and the associated building for the raw material preparation. Conception of distribution system and the associated building for the raw material preparation.
-
-
-
Merck Group
-
Germany
-
Pharmaceutical Manufacturing
-
700 & Above Employee
-
Qualification Engineer / Ingénieur qualification
-
2005 - 2008
In charge of new product launch: project management, planning and coordination, validation of products and parts (IQ, OQ, PQ, standards), FMEA organisation. Managing a team of 3 technicians.Key contact person liaising with other departments (purchasing, operations, and field services): after sales service, tools development for production and technical support for purchasing.FR:o Responsable de lancement nouveaux de produits : gestion, planification et animation de projets, validation de produits (qualitatif, fonctionnel, performances, normes,…), organisation FMEA et AMDEC, gestion d’une équipe de 3 techniciens.Support des services connexes : résolution de problème de conception, développement d’outil de production, et apport technique au service achat. Show less
-
-
Technical Expert / Expert technique
-
2003 - 2005
Management and training of operators. Performance management and improvement of a manufacturing cell: Monitor and control KPI’s (yield, quality, lead time, HSE), process flow improvement, creation of Kanban, coordinating the « Kaisen Event » and 6S activities.Project leader of industrialisation of new products.FR:o Management et formation des opérateurs.Suivi et amélioration des performances de l’atelier :Animation autour des indicateurs (productivité, qualité, délais, sécurité), amélioration des flux, mise en ilots, création de Kanban, animation de « Kaisen Event » et d’actions 5S.Gestion de la mise en production des nouveaux produits. Show less
-
-
Education
-
Ecole de Management de Normandie
Master 2 (M2) -
Ecole Nationale Supérieure d'Ingénieurs Sud Alsace ENSISA
Ingénieur, General Studies (option: automatisme) -
Lycée Gustave Eiffel
Prépa ATS, Ingénieur / technicien en technologie d''automatisation -
IUT Le creusot
DUT, GEII -
Lycée Gustave Eiffel
Bac F3, Electrotechnique
Community
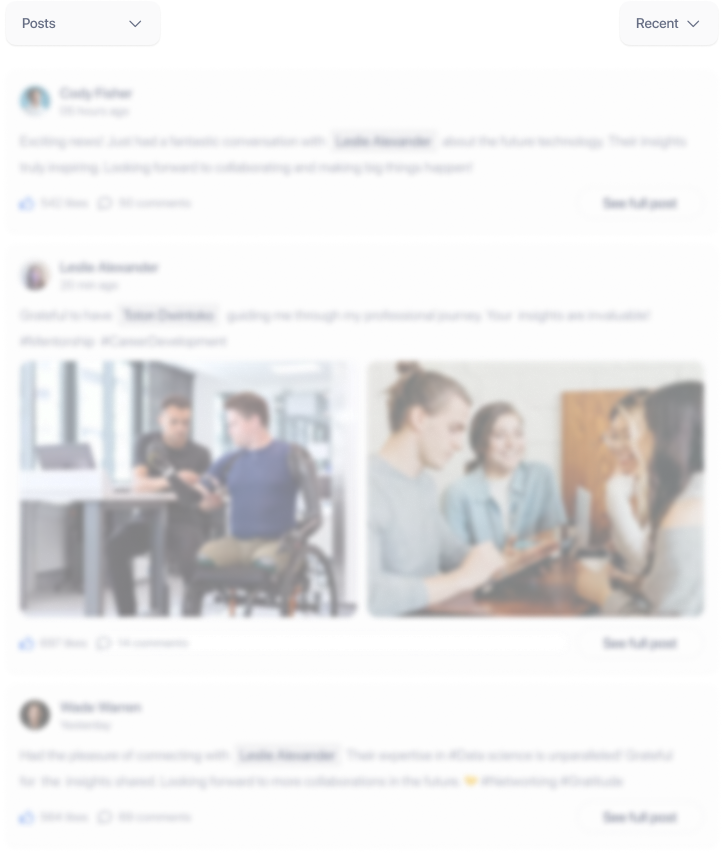