
David Chiang
Continuous Improvement Manager at Toyal America, Inc.- Claim this Profile
Click to upgrade to our gold package
for the full feature experience.
Topline Score
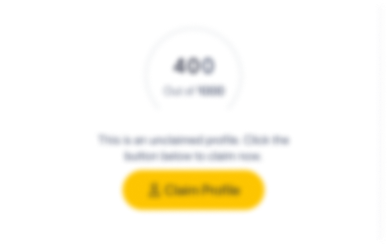
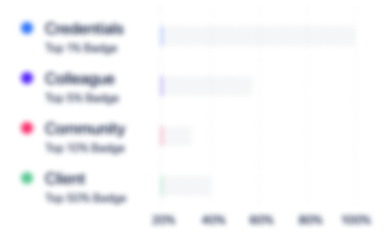
Bio


Credentials
-
Apollo Root Cause Analysis Faciltator
- -
TapRooT Root Cause Analysis Faciltator
-
Experience
-
Toyal Group
-
Japan
-
Chemical Manufacturing
-
1 - 100 Employee
-
Continuous Improvement Manager
-
Oct 2018 - Present
Areas of focus are eliminating root causes of poor quality with Paste production, making improvements to expand our Powders business, and implementing changes to improve operational excellence. Areas of focus are eliminating root causes of poor quality with Paste production, making improvements to expand our Powders business, and implementing changes to improve operational excellence.
-
-
-
Bunge Loders Croklaan
-
Netherlands
-
Food and Beverage Manufacturing
-
700 & Above Employee
-
Process Technology Manager
-
2018 - 2018
Provide regional expertise on processing technologies available to the organization in conjunction with global technology. Responsible for GMP pilot plant operation including pilot production/testing, personal and food safety, equipment maintenance and new capability development.Raised On Time In Full (OTIF) delivery of sample production to external customers from below 50% to 90% by installing daily visual production board with Key Performance Indicators to track performance, identify and correct barriers.
-
-
-
AkzoNobel
-
Netherlands
-
Chemical Manufacturing
-
700 & Above Employee
-
Technology Engineer
-
2017 - 2017
Directed process development and production optimization programs at ISO-9002 certified site which produced fatty amine derivatives from tallow for oil drilling, fuel/oil additives, asphalt, and fabric softener markets.Saved $500k/yr in nickel catalyst usage for hydrogenations by using a more economical catalyst already on site and finding optimum usage level without sacrificing productivity or product quality.Lead structured investigations to correctly identify root causes for major plant incidents including process fire causing a multiday outage, spills (loss of primary containment events) , employee injuries, significant equipment failures/downtime, and high value product & raw material losses.
-
-
-
AkzoNobel
-
Netherlands
-
Chemical Manufacturing
-
700 & Above Employee
-
Continuous Improvement Manager
-
2015 - 2016
Responsible for implementing a CI program at the 125 person Morris manufacturing site which produces a variety of fatty amines and their derivatives for many different end users including fabric softeners, fuel/oil additives, agrochemicals, asphalt, and oil drilling. Implemented AkzoNobel lean manufacturing systems aimed at increasing operational excellence and efficiency at Salisbury NC plant in 2015 and at Morris IL plant in 2016. The effort initially implemented visual short interval control boards, 5S, root cause & problem solving including a cycle time loss accounting system, and standardized work steps at the "factory floor" level. Responsible for managing and developing a portfolio of cost savings projects for the Morris site which included using Six Sigma as well as Lean Manufacturing. The site saved $5 million in 2015-2016 through product yield improvements, energy usage, transportation cost, and waste reduction. The employees achieved this sustainable savings with no or low capital investment.
-
-
-
AkzoNobel
-
Netherlands
-
Chemical Manufacturing
-
700 & Above Employee
-
Batch Hydro Production Leader
-
2014 - 2014
Executed production, coordinated / prioritized maintenance work, and drove improvement in hydrogenated fatty amines units (OSHA PSM covered unit). Accountable for EHS (including safety permitting), asset utilization, schedule compliance, and product quality. Managed inventory and process orders through SAP.Raised first pass quality production of Duomeen product from 50% to 100% by identifying and then properly controlling the quality critical parameters during the reaction step.Improved operational safety by implementing new corporate lockout-tagout system and safety permitting initiative. Worked with the operators and mechanics to to make the new system workable and understandable.
-
-
-
AkzoNobel
-
Netherlands
-
Chemical Manufacturing
-
700 & Above Employee
-
Arquad Production Leader
-
2010 - 2013
Managed a batch processing unit which made quaternary amines (OSHA PSM covered unit). Responsible for supervising production, coordinating maintenance, EHS, and troubleshooting. Led startup team to successfully commission a $3 million quaternization reactor installed to meet the growing demand from the oil and gas markets. Startup was completed on time, on budget, and most importantly--without incident. Managed a batch processing unit which made quaternary amines (OSHA PSM covered unit). Responsible for supervising production, coordinating maintenance, EHS, and troubleshooting. Led startup team to successfully commission a $3 million quaternization reactor installed to meet the growing demand from the oil and gas markets. Startup was completed on time, on budget, and most importantly--without incident.
-
-
-
Dow
-
United States
-
Chemical Manufacturing
-
700 & Above Employee
-
Senior Process Engineer and QC Lab Manager
-
2003 - 2010
Provided process engineering support for all phases of an acrylic and vinyl acetate batch emulsion plant. Supervised QC Lab operations including 5 technicians.Eliminated frequent reactor downtime by identifying root cause and re-designing feed line to greatly reduce the growth of disruptive in-pipe blockages. Used existing field instrumentation to measure the pipe resistance to create a feed line "cleanliness" meter on control room DCS screen for the operators to monitor any chemical build up.Solved chronic housekeeping eyesore while improving safety and productivity by overhauling the SWECO product filtration area with a $450k capital project. The success of the improved and simplified design relied heavily on input from the operators and mechanics to ensure operability, maintainability, and employee buy-in. Decreased reactor cleanout neutralization time by 75%. Procedure originally called for blind dilutions using acid to reach the target pH. Improvements made by involved QC Lab in performing sample titrations and calculating the target amount of acid for operations to use. Improved QC Lab productivity using 5S. Equipment was relocated to promote efficient work flow. Sample prep time was cut 50% by replacing expensive and large water bath with a small footprint freezer,
-
-
-
Rohm and Haas
-
Chemical Manufacturing
-
400 - 500 Employee
-
Louisville Plant Area 2 Technical Manager
-
1997 - 2003
Directed the technical and $6 million/yr capital program for Louisville Plant Area #2 which comprised of operating units for PARALOID polymer production, MMA distillation, and central plant utilities. Managed a 12-person department including process engineers, project engineers, electrical engineer, process control engineers, and analytical lab technician. Directed the technical and $6 million/yr capital program for Louisville Plant Area #2 which comprised of operating units for PARALOID polymer production, MMA distillation, and central plant utilities. Managed a 12-person department including process engineers, project engineers, electrical engineer, process control engineers, and analytical lab technician.
-
-
-
Rohm and Haas
-
Chemical Manufacturing
-
400 - 500 Employee
-
Bristol Pilot Plant Operations Manager
-
1992 - 1996
Managed $10 million/yr pilot plant facilities staffed with 32 personnel (engineers, operators, and mechanics) to provide batch scale-up support for processes producing emulsion/solution polymers, specialty monomers, plastics, and ag chemicals. Accountable for all aspects of operation including safety, customer satisfaction, and cost.
-
-
Process Engineer
-
1990 - 1992
Provided technical support to Multi Products Manufacturing Area which included batch processing of surfactants and agricultural chemicals.
-
-
Education
-
Caltech
Masters, Chemical Engineering -
Purdue University
Bachelors, Chemical Engineering
Community
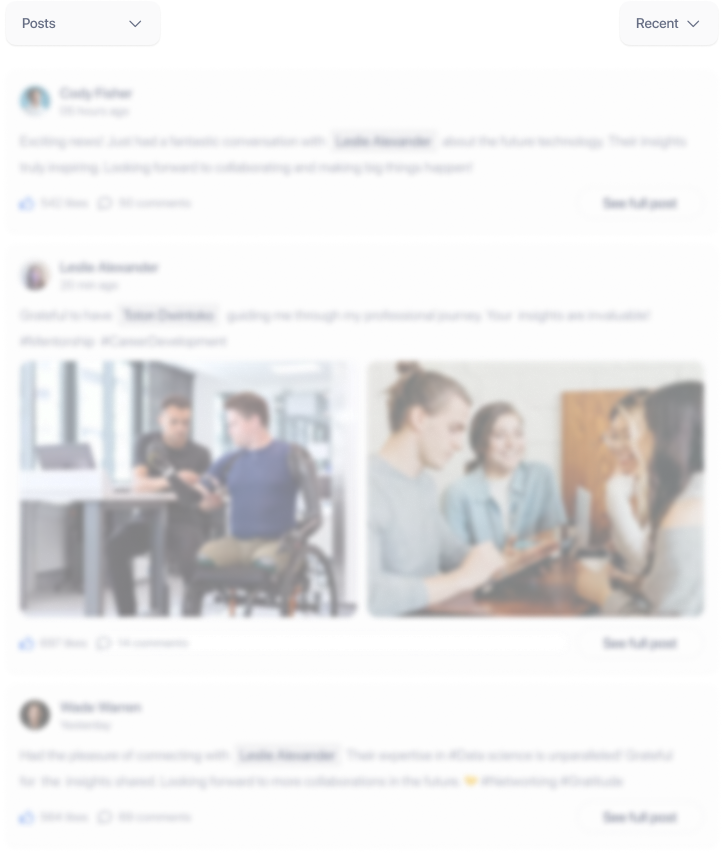