Phani kumar Kovi
Head Of Operations at Apicore US LLC- Claim this Profile
Click to upgrade to our gold package
for the full feature experience.
-
Telugu -
-
English -
-
Hindi -
Topline Score
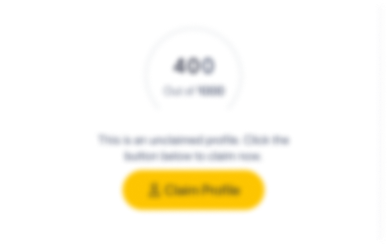
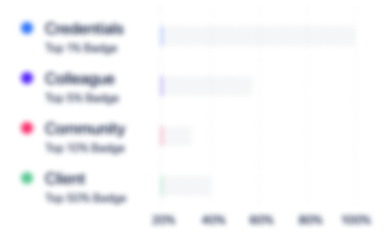
Bio

Prathap Borreddy
phani is good process engineer in pharma scale up or pharma technology transfer

Prathap Borreddy
phani is good process engineer in pharma scale up or pharma technology transfer

Prathap Borreddy
phani is good process engineer in pharma scale up or pharma technology transfer

Prathap Borreddy
phani is good process engineer in pharma scale up or pharma technology transfer

Experience
-
Apicore US LLC
-
Pharmaceutical Manufacturing
-
1 - 100 Employee
-
Head Of Operations
-
Apr 2019 - Present
-
-
Director Technical Operations
-
May 2011 - Present
Trouble Shooting and process robustness. Handling batch processing troubles raised in the plant which effects deliveries and delivery schedules Providing solutions for PSD requirement & crystallization problems. Calculate the Utility consumption in the batch. Cost Improvement Products implementation (Commercial batches ). New product Development monitoring from Lab Batches to Commercial batches in plant. 5 year plan implementation.
-
-
-
Dr. Reddy's Laboratories
-
India
-
Pharmaceutical Manufacturing
-
700 & Above Employee
-
Team leader
-
Jan 2007 - May 2011
Scale up of New Products Scaling up of New products from Lab scale to plant scale. Selection of equipments and Designing. What -if Study. Preparation of p&id and PFD for the process. Looking for options for the Automation of the process. Preparation of Mass balance, Energy Balance, ETP load, Utility load estimations. Product costing. Execution of trial and Validation with Technology Transfer to Manufacturing . Involved in Technology transfer document finalization. Execution of new drug validation as per c-GMP. Involved in modification of equipment as per process requirement. Preparation of Equipment list for new project with their Specification. 5 Year Plan (Capacity Enhancement) Played a key role in doubling the production capacity of 40 products in the existing facility. Fulfills the Market Demand , Business Requirements and Customer estimation Reaching. Capacity updation according to the marketing projections. Decoupling of products and Automation. Segregation of existing products into 3 categories.(Runner Repeater & Stranger). Preparing of basic engineering package for New clean Room. Batch Time cycle Reduction by simple Automation. Technical support to projects in designing the equipment for new blocks and for modern technologies. Separate planning and containment facility for all Steroids in the Unit. Trouble Shooting and process robustness. Handling batch processing troubles aroused in the plant affecting deliveries and delivery schedules . Providing solutions for PSD (particle size distribution) requirement & crystallization problems. Calculating all the Utility consumption in the batch . Leading all teams like manufacturing, R&D, Regulatory, Quality control, Maintenance etc. for addressing the troubles. Cost Improvement Products implementation has been done in plant (Commercial batches ). New product Development products monitoring from Lab Batches to Commercial batches in plant Show less
-
-
as Assistant Manager Technical Service Department
-
Jan 2007 - May 2011
Responsibilities in Dr Reddy'sScale up of New ProductsScaling up of New products from Lab scale to plant scale.Selection of equipments and Designing.What -if Study.Preparation of p&id and PFD for the process.Looking for options for the Automation of the process.Preparation of Mass balance, Energy Balance, ETP load, Utility load estimations.Product costing.Execution of trial and Validation with Technology Transfer to Manufacturing .Involved in Technology transfer document finalization.Execution of new drug validation as per c-GMP.Involved in modification of equipment as per process requirement.Preparation of Equipment list for new project with their Specification.5 Year Plan (Capacity Enhancement) Played a key role in doubling the production capacity of 40 products in the existing facility.Fulfills the Market Demand , Business Requirements and Customer estimation Reaching.Capacity updation according to the marketing projections.Decoupling of products and Automation.Segregation of existing products into 3 categories.(Runner Repeater & Stranger).Preparing of basic engineering package for New clean Room.Batch Time cycle Reduction by simple Automation.Technical support to projects in designing the equipment for new blocks and for modern technologies.Separate planning and containment facility for all Steroids in the Unit.Trouble Shooting and process robustness.Handling batch processing troubles aroused in the plant affecting deliveries and delivery schedules .Providing solutions for PSD (particle size distribution) requirement & crystallization problems.Calculating all the Utility consumption in the batch .Leading all teams like manufacturing, R&D, Regulatory, Quality control, Maintenance etc. for addressing the troubles.Cost Improvement Products implementation has been done in plant (Commercial batches ).New product Development products monitoring from Lab Batches to Commercial batches in plant. Show less
-
-
-
-
Executive - DISH
-
Mar 2006 - Jan 2007
Preparation of p&id and PFD for the process. Looking for options for the Automation of the process. Preparation of Mass balance, Energy Balance, ETP load, Utility load estimations. Product costing. Execution of the process batches in Manufacturing Preparation of p&id and PFD for the process. Looking for options for the Automation of the process. Preparation of Mass balance, Energy Balance, ETP load, Utility load estimations. Product costing. Execution of the process batches in Manufacturing
-
-
-
-
Executive
-
Mar 2006 - Dec 2006
Multipurpose plants designed and commissioned as per USFDA guidelines and also USFDA approved products And continuous process and distillation columns also handled. Commissioned "500 TPA" continuous Production of "Halothane" Liquid API Product. Complete DCS plant Responsibilities in Nicholas Piramal India Lmt. Execution of production planning. Responsible for monitoring and supervising the production operations batch movements and manpower allotment . Initiating process improvements for achieving cost reduction and reduction of time cycle. Show less
-
-
-
-
Executive - Process development
-
May 2004 - Feb 2006
Responsibilities in Vijayasri Organics Based on R& D process, Conducting used tests at R&D and observing the process. Responsibility of handling of GC Monitoring all quality control activities online Based on plant conditions, conducting What-if study experiments In some case carrying out Negative experiments Selection of Equipments Training People working with me. Maintain the QA documents and follow up sop's. Responsibilities in Vijayasri Organics Based on R& D process, Conducting used tests at R&D and observing the process. Responsibility of handling of GC Monitoring all quality control activities online Based on plant conditions, conducting What-if study experiments In some case carrying out Negative experiments Selection of Equipments Training People working with me. Maintain the QA documents and follow up sop's.
-
-
Education
-
Acharya Nagarjuna University
B Tech, Chemical Engineering -
RVR & JC College of Engineering
Bachelor of Technology, Chemical
Community
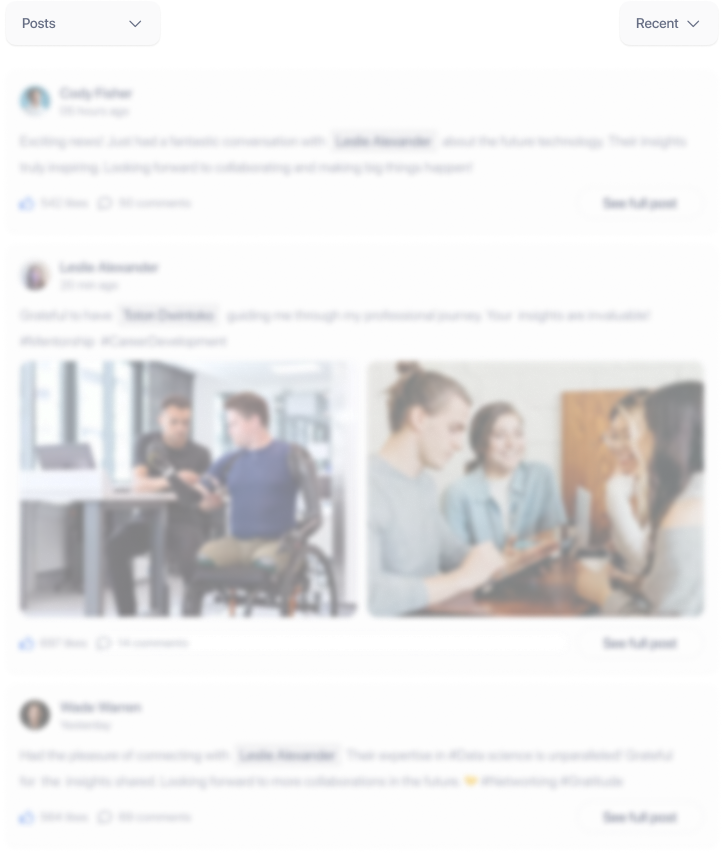