Mark Fuller
Senior Design Engineer at GE Additive- Claim this Profile
Click to upgrade to our gold package
for the full feature experience.
-
English -
Topline Score
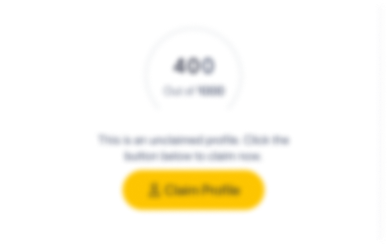
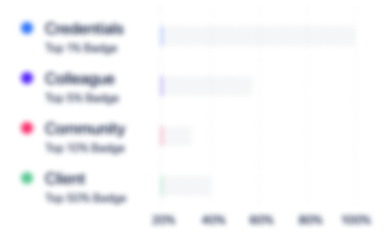
Bio

Ronald G "Greg" Young
Mark is a highly talented individual, extremely creative and able. Good conceptual knowledge extended through project execution and startup.

Ronald G "Greg" Young
Mark is a highly talented individual, extremely creative and able. Good conceptual knowledge extended through project execution and startup.

Ronald G "Greg" Young
Mark is a highly talented individual, extremely creative and able. Good conceptual knowledge extended through project execution and startup.

Ronald G "Greg" Young
Mark is a highly talented individual, extremely creative and able. Good conceptual knowledge extended through project execution and startup.

Credentials
-
The Six Morning Habits of High Performers
LinkedInSep, 2020- Nov, 2024 -
Sustainability Advisor Certificate
Georgia Southern UniversityOct, 2015- Nov, 2024
Experience
-
GE Additive
-
United States
-
Machinery Manufacturing
-
300 - 400 Employee
-
Senior Design Engineer
-
Aug 2017 - Present
• Support external customer on their metal additive journey • Teach level 1 & 2 design for metal additive (DFAM) • Lead designer for Pacer Edge Program between GE and US Airforce • Design aerospace additive heat exchangers using new and novel techniques • Developed and printed the largest powder bed additive part ever produced on the GE Additive Atlas machine, weighing over 300 pounds. • Support external customer on their metal additive journey • Teach level 1 & 2 design for metal additive (DFAM) • Lead designer for Pacer Edge Program between GE and US Airforce • Design aerospace additive heat exchangers using new and novel techniques • Developed and printed the largest powder bed additive part ever produced on the GE Additive Atlas machine, weighing over 300 pounds.
-
-
-
Gulfstream Aerospace
-
United States
-
Aviation & Aerospace
-
700 & Above Employee
-
Manufacturing Engineer II
-
Sep 2012 - Aug 2017
• Worked on a cross departmental team to established First Manufacturing 3D printer hub at Gulfstream. Reduced cycle time from 2-3 weeks to 1-2 days. • Designed and implemented over 50 3D printed tools saving $150,000 ( Examples: ergonomic hand tools, shop aids, tool organizers, FOD reductions tools, and Pre-tooling design evaluation fixtures) • Created tutorials and training about desktop additive manufacturing. • Optimizing and updating G650, G500 & G600 Manufacturing Models from Fibersim to CPD. Work directly with mechanics to improve ply stackup, reduce voids/ discrepancies and reduce cycle time. • Designed 12 new laser work cells to optimize working area and flexibility. Increased effective working area by over 30%, reduced dust collection areas over 50% and designed in the ability to chain lasers together to project a 15’ X 35’ tool • Identified issues with release sprays for antenna fairings and implemented alternative release agent (Total Cost savings Per year $55,000, Time savings 12 weeks a year, and green savings of 1 ton less PTFE in the atmosphere) • Manage continues improvement, 6S, and green team for composites since 2015 • Helped facilitate Composite Building expansions and redesign for new G500 & G600 parts • Designed and implemented Mobile Computer Workstations around technicians’ needs to increase work flow and reduce downtime (80 Mobile Computer Workstations implemented to date) • Project Manager of installation and Certification of new 10’ Diameter X 35’ long Autoclave that has increase curing capacity by over 100% • Designed, 3D printed and implemented ergonomic articulating vacuum cleaner attachment. This solution reduced cleaning time by 80%, Ergo Risk from 27 to 1 and 5,000’ less vertical steps per cleaning. Won first place at 2015 applied ergonomics conference. http://www.iise.org/Ergo/Conference/details.aspx?id=39622 (Patented)
-
-
-
EMS, Inc.
-
United States
-
Industrial Machinery Manufacturing
-
1 - 100 Employee
-
Regional Application Engineer
-
Jun 2010 - Sep 2012
• Product Support & training on 3D scanners & printers (3D systems, Rapidform, steinbeckler, Konica Minolta, Surphaser) • Reverse engineer customer’s part with scan data using Rapidform (XOR) • First Article inspections with Scan data using Rapidform (XOV) • Take Customers Idea to create 3D functional prototypes • Product Support & training on 3D scanners & printers (3D systems, Rapidform, steinbeckler, Konica Minolta, Surphaser) • Reverse engineer customer’s part with scan data using Rapidform (XOR) • First Article inspections with Scan data using Rapidform (XOV) • Take Customers Idea to create 3D functional prototypes
-
-
-
Flight Display Systems
-
Alpharetta Ga
-
Design & Manufacturing Engineer
-
Dec 2009 - Jun 2010
• Design 3D parts for Aerospace applications in SolidWorks (Sheet metal & machined parts) • Quality control & First Article Inspection for all new products • Optimize lean manufacturing techniques for all products • Designed 14” touch screen ( FD141CV-C-1) OEM replacements for Apache helicopter • Reduced size, added power filtering, & EMI shielding for the 7” LCD (FD70CV-M) • Created wire path fixtures for reducing wire length & EMI interference • Consult with Electrical Engineers to determine building constants • Perform FEA tests using SolidWorks to optimize design aspects & reduce production time
-
-
Education
-
Georgia Southern University
Bachelor of Science Mechanical Engineering Technology, Mechanical Engineering
Community
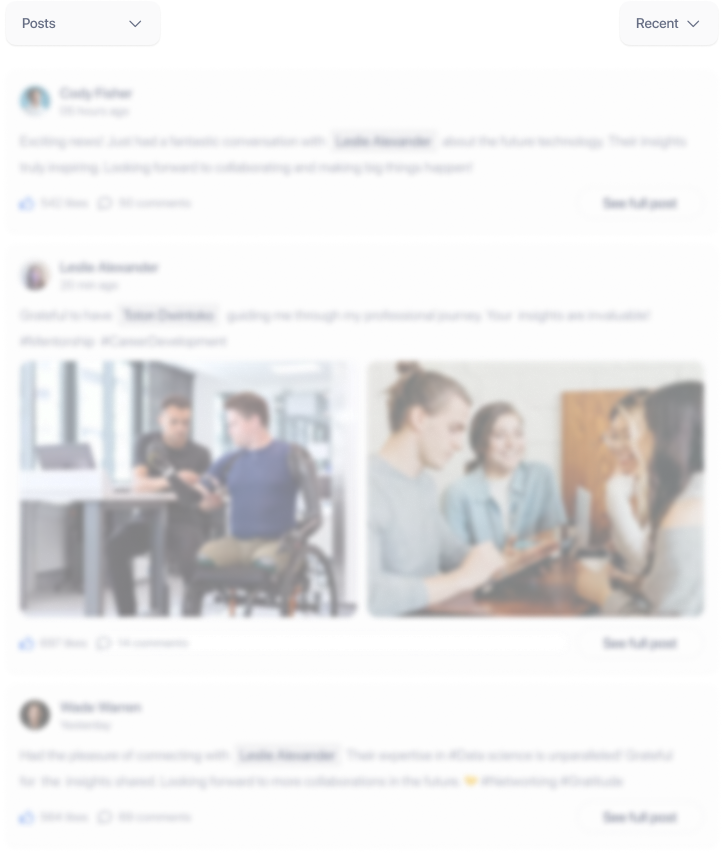