Paul Underwood
Supplier Quality Engineer, V at MC3 Cardiopulmonary- Claim this Profile
Click to upgrade to our gold package
for the full feature experience.
Topline Score
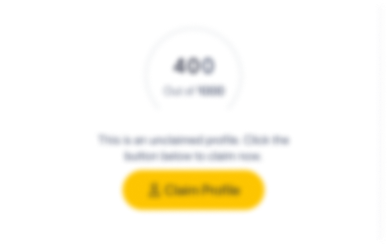
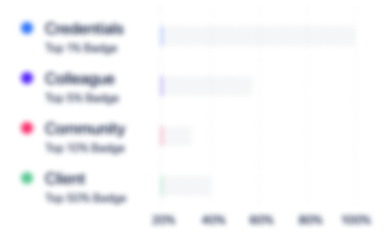
Bio

Alison Cassidy
I worked with Paul for a number of years at Apple. Back then, he was my go-to person when I needed detailed information on product quality and yields, and I regularly relied on him for information relating to our xServe product line. I always found Paul to be a diligent engineer, with a keen eye for process improvements. As a diagnostic developer, it was Paul who tended to be the person who came to me with suggestions for improvements. Rather than being a person who 'just did the job', he tended to go the extra distance to be proactively involved in the product life-cycle, from new product introduction/xVT to end-of-life. I'd highly recommend Paul for any position in quality engineering.

Alison Cassidy
I worked with Paul for a number of years at Apple. Back then, he was my go-to person when I needed detailed information on product quality and yields, and I regularly relied on him for information relating to our xServe product line. I always found Paul to be a diligent engineer, with a keen eye for process improvements. As a diagnostic developer, it was Paul who tended to be the person who came to me with suggestions for improvements. Rather than being a person who 'just did the job', he tended to go the extra distance to be proactively involved in the product life-cycle, from new product introduction/xVT to end-of-life. I'd highly recommend Paul for any position in quality engineering.

Alison Cassidy
I worked with Paul for a number of years at Apple. Back then, he was my go-to person when I needed detailed information on product quality and yields, and I regularly relied on him for information relating to our xServe product line. I always found Paul to be a diligent engineer, with a keen eye for process improvements. As a diagnostic developer, it was Paul who tended to be the person who came to me with suggestions for improvements. Rather than being a person who 'just did the job', he tended to go the extra distance to be proactively involved in the product life-cycle, from new product introduction/xVT to end-of-life. I'd highly recommend Paul for any position in quality engineering.

Alison Cassidy
I worked with Paul for a number of years at Apple. Back then, he was my go-to person when I needed detailed information on product quality and yields, and I regularly relied on him for information relating to our xServe product line. I always found Paul to be a diligent engineer, with a keen eye for process improvements. As a diagnostic developer, it was Paul who tended to be the person who came to me with suggestions for improvements. Rather than being a person who 'just did the job', he tended to go the extra distance to be proactively involved in the product life-cycle, from new product introduction/xVT to end-of-life. I'd highly recommend Paul for any position in quality engineering.

Credentials
-
Adult and Pediatric First Aid/CPR/AED
American Red CrossOct, 2022- Nov, 2024 -
Certified Quality Engineer (CQE)
ASQ - World HeadquartersDec, 2013- Nov, 2024
Experience
-
MC3 Cardiopulmonary
-
United States
-
Medical Equipment Manufacturing
-
1 - 100 Employee
-
Supplier Quality Engineer, V
-
Sep 2020 - Present
Key technical role responsible for the development, implementation, improvement and continuous reinforcement of established Quality Assurance fundamental practices. The role involves hands- on work with MC3 and our suppliers in the areas of design, design transfer, test method validation, manufacturing, distribution, and/or service. Key technical role responsible for the development, implementation, improvement and continuous reinforcement of established Quality Assurance fundamental practices. The role involves hands- on work with MC3 and our suppliers in the areas of design, design transfer, test method validation, manufacturing, distribution, and/or service.
-
-
-
Orchid Orthopedic Solutions
-
United States
-
Medical Equipment Manufacturing
-
500 - 600 Employee
-
Senior Quality Engineer
-
Sep 2016 - Aug 2020
• Work with Project Managers, Engineers, CNC Programmers, CMM Programmers, SPC administrators, and Manufacturing staff to ensure new product quality and improve existing product quality. • Responsible for new product introduction and APQP (Contract review, pFMEA, Process Flows, Control Plans, MSA, First Article Inspection etc.) • Develop test methods and procedures to support production. • Utilizes statistical analysis and SPC to determine process capability. • Coordinate with operators in determine best methods of measurement and testing of product. • Work with production and engineering to resolve internal quality issues and drive quality improvements. • Liaison with customers to resolve issues with both product and system quality. • Work with Lead Auditor on internal audits. Reviewed results of audits and develop corrective actions. • Record, log and report on CAPA metrics. • Facilitate CAPA review meetings including meeting agenda and scribe meeting minutes. • Provide guidance, training and leadership to CAPA Teams for development of CAPA investigation, root cause analysis, corrective action and plans. Show less
-
-
-
Terumo Cardiovascular
-
United States
-
Medical Equipment Manufacturing
-
500 - 600 Employee
-
Engineer II, CAPA
-
Jul 2014 - Sep 2016
* Served as a point of contact and assisted with investigating, planning, and implementing improvements to products and processes during the CAPA process. * Ensured that every activity performed in the CAPA process was accurately documented and that all time frames for reporting and resolution were met. * Identified appropriate representatives from affected departments while working in all stages of CAPA investigation, management and resolution. * Acted a project manager for all phases of the CAPA process including root cause investigation, plan development, implementation of action items and verification of effectiveness. * Assisted in generation of management review metrics for CAPA. Demonstrated commitment to patient safety and product quality by maintaining compliance to the Quality Policy and all other documented quality processes and procedures. Show less
-
-
-
Orchid Orthopedic Solutions
-
United States
-
Medical Equipment Manufacturing
-
500 - 600 Employee
-
Quality Engineer
-
Jan 2013 - Jul 2014
* Responsible for new product introduction and APQP (Contract review, pFMEA, Process Flows, Control Plans, Gage R+R, First Article Inspection etc) * Develop test methods and procedures to support production. * Utilizes statistical analysis and SPC to determine process capability. * Coordinate with operators in determine best methods of measurement and testing of product. * Performs root cause analysis, corrective action, review and reporting. * Work with production and engineering to resolve internal quality issues. * Liaison with customers to resolve issues with both product and system quality. * Worked with Lead Auditor on internal audits. reviewed results of audits and develop corrective actions. Show less
-
-
-
Venchurs, Inc.
-
Adrian, Michigan.
-
Quality Engineer
-
Jul 2011 - Dec 2012
* Responsible for managing and obtaining over 700 PPAP approvals from various manufactures including Chrysler, Ford, GM, Toyota and Nissan * Lead corrective action program for both internal and external customer, supplier quality issues utilizing quality tools including CARs, 8Ds, 3x5 Whys. etc * Participated in Kaizen events for lean manufacturing and process improvements. * Developed and introduced layer process audits. * Prepared standardized work instruction and inspection documentation for new program. * Managed RMA, MRB and quality hold material. * Supervised QA technicians. Show less
-
-
-
Boston Scientific
-
United States
-
Medical Equipment Manufacturing
-
700 & Above Employee
-
-
Jan 2011 - May 2011
● Development of production equipment and fixtures.● Generate 3D CAD models of concepts/ideas using Solidworks. ● Member of cross-function lean manufacturing/ continuous improvement team.● Working with Vendors from design, quotations, manufacturing to testing and installation.● Development and implementation of cGMP compliant documentation including functional and user specification, IVOT protocols/reports, equipment/gauge drawings.
-
-
-
Oct 2010 - Dec 2010
6 week work experience for my Medical Device Industrials Skills course.
-
-
-
-
Quality Manager
-
Jul 2008 - Nov 2009
• Responsible for resolving all factory and customer quality issues • Accountable for the management and supervision of all quality inspectors • Full autonomy for the ISO 9000 quality system and industry standards • Introduction of Return Material Authorisation (RMA) system for customers • Completion of inspections of finished products to verify conformance to requirements • Compiling appropriate documentation including inspection records and non-conformance reports as necessary • Ensuring all targets and deadlines are adhered to • Active member of Health & Safety Committee ensuring strict adherence to Health and Safety regulations and highlighting of any concerns in this area to relevant personnel • Responsible for highlighting any issues to supervisors and inform them of any areas of concern • Carry out all other duties as requested Role Achievements: • Reduced quality costs by 50% from 1% of turnover to 0.5% Show less
-
-
-
Apple
-
United States
-
Computers and Electronics Manufacturing
-
700 & Above Employee
-
Quality/Yield Engineer
-
Jul 2003 - Jul 2006
• Responsible for all quality issues relating to Xserve production line • Chair and drive Quality improvement action plans for Production and Functional groups (Test, Mfg and SQE) • Production and analyzing of Yield data extensively • Main interface for Yield and Quality reports, internally and with other manufacturing facilities • Participation in new product introductions including worldwide conference calls and coordinate Engineering/ Manufacturing/ Quality action plans • Recording and driving field issues to related departments • Responsible for the provision of training for customers audit testing Role Achievements: • Developed Failure Mode and Rework Fixes list for shop floor reporting system used worldwide. Show less
-
-
-
-
Product Engineer
-
Oct 2001 - Nov 2002
•Designed hardware for internet access device, provided working prototype, including custom cases. • Developed production systems, including automated hard drive format and system download. • Produced production procedures and documentation. •Designed hardware for internet access device, provided working prototype, including custom cases. • Developed production systems, including automated hard drive format and system download. • Produced production procedures and documentation.
-
-
-
-
CAD Draftsperson
-
Jan 1999 - Oct 2000
• Documentation of modifications and repairs to aircraft (OV-10A, S-2A, UH-1H) • Produced fabrication / installation drawings from workshop samples. • Introduced ANSI Y14.5 drafting standards and Engineering Change Order (ECO) system. • Documentation of modifications and repairs to aircraft (OV-10A, S-2A, UH-1H) • Produced fabrication / installation drawings from workshop samples. • Introduced ANSI Y14.5 drafting standards and Engineering Change Order (ECO) system.
-
-
-
-
Design Engineer / Quality Manger
-
1995 - 1998
Areas of responsibility: • Commenced employment as a CAD Drafter • Reverse-engineering and design of aviation components • Preparation of design packages for PMA (Parts Manufacturing Approval) Approval • Inspection of prototype, first article and production components • Introduction of 3-D modeling and analysis of components • Quality Manager of MIL-I-45208/ISO 9002 • Performing vendor inspections and quality audits • Responsible for the installation and maintenance of computer and phone systems • Technical support for all computer problems • Represented company at various trade shows Role Achievements: • Appointed Designated Manufacturing Inspection Representative (DMIR) by the Federal Aviation Administration (FAA) Show less
-
-
-
Reynaers Aluminium
-
Belgium
-
Wholesale Building Materials
-
500 - 600 Employee
-
Quality Manager / Design Engineer
-
1992 - 1995
• Managed projects from quotation and pricing, to manufacturing, delivery and installation. • Developed and designed new vertical sliding window system. • Produced construction, inspection, and profile die drawings for customers and suppliers. • Installed and coordinated ISO-9002 Quality Assurance system. • Introduced Statistical Process Control (SPC) on manufacturing operations. • Trained staff in Quality system and in use of measuring equipment. • Answering Customer technical enquires. Show less
-
-
Education
-
University of Limerick
B.Eng, Production Engineering -
Carlow Institute of Technology
National Diploma, Mechanical Engineering -
FÁS, in conjunction with Impact Training
Medical Devices Industrial Skills – FETAC Level 5
Community
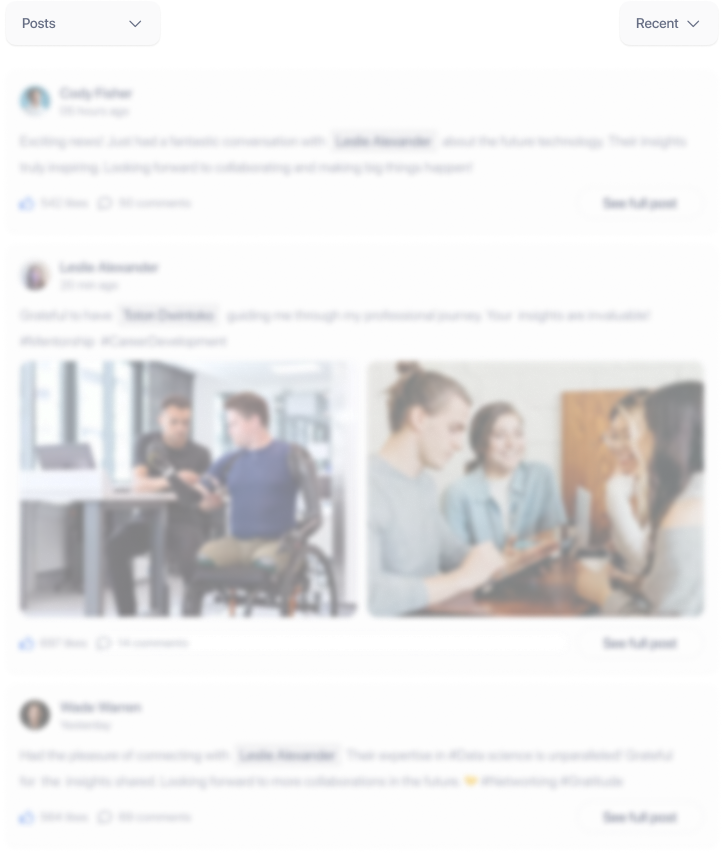