Ivan Wooldridge
Principal Consultant at ORBIZ- Claim this Profile
Click to upgrade to our gold package
for the full feature experience.
Topline Score
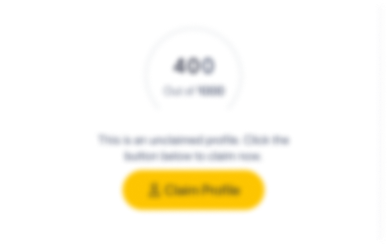
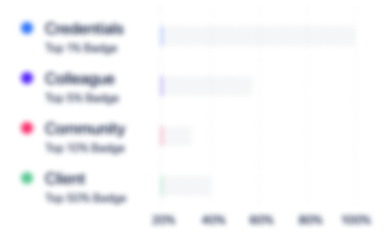
Bio

Chris Colbourne
Working with Ivan was excellent , his knowledge, expertise and leadership made achieving outstanding results easy.

Matthew Smith
I had the great pleasure of working for Ivan at the Toyota Manufacturing plant in the UK in his capacity and Senior Group Leader. I always found Ivan to be level headed, approachable and supportive in the development of all personnel in his charge. I would certainly be more than happy to work with Ivan again in the future and have no hesitation in extending my recommendation to others.

Chris Colbourne
Working with Ivan was excellent , his knowledge, expertise and leadership made achieving outstanding results easy.

Matthew Smith
I had the great pleasure of working for Ivan at the Toyota Manufacturing plant in the UK in his capacity and Senior Group Leader. I always found Ivan to be level headed, approachable and supportive in the development of all personnel in his charge. I would certainly be more than happy to work with Ivan again in the future and have no hesitation in extending my recommendation to others.

Chris Colbourne
Working with Ivan was excellent , his knowledge, expertise and leadership made achieving outstanding results easy.

Matthew Smith
I had the great pleasure of working for Ivan at the Toyota Manufacturing plant in the UK in his capacity and Senior Group Leader. I always found Ivan to be level headed, approachable and supportive in the development of all personnel in his charge. I would certainly be more than happy to work with Ivan again in the future and have no hesitation in extending my recommendation to others.

Chris Colbourne
Working with Ivan was excellent , his knowledge, expertise and leadership made achieving outstanding results easy.

Matthew Smith
I had the great pleasure of working for Ivan at the Toyota Manufacturing plant in the UK in his capacity and Senior Group Leader. I always found Ivan to be level headed, approachable and supportive in the development of all personnel in his charge. I would certainly be more than happy to work with Ivan again in the future and have no hesitation in extending my recommendation to others.

Experience
-
ORBIZ
-
Australia
-
Business Consulting and Services
-
1 - 100 Employee
-
Principal Consultant
-
Jul 2022 - Present
ORBIZ are a global consulting firm who facilitate the rapid delivery of significant and sustainable improvements in performance across a diversity of industries. We facilitate turnaround, transformation and strategic improvement programs through the development and implementation of a system and culture of Lean and continuous improvement. This enables our clients to increase the effectiveness of their organisations by making them easier to manage, more flexible, more competitive and overall more profitable. Our team of industry professionals have been selected based on their extensive experience from the highest performing industries and organisations around the world and their passion and enthusiasm for engaging with people to successfully transfer that knowledge and experience. Operating across a diversity of industries our services range from the optimisation of business development systems to deliver growth, through to operating system improvements that reduce cost through improvements in safety, quality and productivity. We have a strong reputation for delivering challenging projects and significant results and we enjoy being involved in change as we are passionate about working with people and organisations to help them sustainably improve their performance. ORBIZ brings together a network of highly knowledgeable performance improvement specialists who operate across Asia Pacific, Europe, Africa and the Americas to form a talented and flexible consulting and advisory team. Our consultants are experienced business professionals who have lived and breathed the philosophies of Lean and continuous improvement through successful careers with industry leading companies around the world. We have extensive experience of implementing sustainable improvement and change programs across a diversity of industries including Mining, Energy, Construction, Transport, Aerospace, Manufacturing and Healthcare. Show less
-
-
-
Boston Consulting Group (BCG)
-
United States
-
Business Consulting and Services
-
700 & Above Employee
-
Lean Master Coach
-
Jan 2022 - Jun 2022
• Engaged as a LEAN Master Coach for 6 BCG consultants, 10 Safe Production System (SPS) deployment teams • Engaged as a LEAN Master Coach for 6 BCG consultants, 10 Safe Production System (SPS) deployment teams
-
-
-
Mount Gibson Iron
-
Australia
-
Mining
-
100 - 200 Employee
-
Lean Consultant
-
Feb 2020 - Dec 2021
• Coached GM and 4 Managers to implement LEAN based systems and processes promoting stability and continuous Improvement • Established a simplified Project Management system (based on Project A3s) to introduce discipline and control into the project management • Promoted the identification and completion of improvement opportunities at team level through 10 Performance Centres • Coached GM and 4 Managers to implement LEAN based systems and processes promoting stability and continuous Improvement • Established a simplified Project Management system (based on Project A3s) to introduce discipline and control into the project management • Promoted the identification and completion of improvement opportunities at team level through 10 Performance Centres
-
-
-
BHP
-
Australia
-
Mining
-
700 & Above Employee
-
Manager
-
Apr 2017 - Dec 2019
• Refurbishes Haul Truck and Rail components to "as new" in line with the strategic reliability aspirations, 30 employees • Cultivated PRC's vision "Pursue Results through Culture" by engaging and empowering the front-line to problem solve and eliminate waste from processes increasing throughput by 40% • Refurbishes Haul Truck and Rail components to "as new" in line with the strategic reliability aspirations, 30 employees • Cultivated PRC's vision "Pursue Results through Culture" by engaging and empowering the front-line to problem solve and eliminate waste from processes increasing throughput by 40%
-
-
-
Origin Energy
-
Australia
-
Utilities
-
700 & Above Employee
-
Lean Consultant
-
Oct 2016 - Mar 2017
• Built a Management Operating System with associated 2-day training programme • Coached 10 improvement projects to develop internal continuous improvement capacity and improve performance • Built a Management Operating System with associated 2-day training programme • Coached 10 improvement projects to develop internal continuous improvement capacity and improve performance
-
-
-
Shell
-
United Kingdom
-
Oil and Gas
-
700 & Above Employee
-
Continuous Improvement Lead
-
Jan 2014 - Sep 2016
• Deployed the Shell Continuous Improvement program through a 8, 3 day training programmes with 80 associated improvement projects • Implemented Project Management approach to the Operational Readiness for Prelude FLNG based in South Korea involving 12 teams • Deployed the Shell Continuous Improvement program through a 8, 3 day training programmes with 80 associated improvement projects • Implemented Project Management approach to the Operational Readiness for Prelude FLNG based in South Korea involving 12 teams
-
-
-
Woodside Energy
-
Australia
-
Oil and Gas
-
700 & Above Employee
-
Lean Consultant
-
Jul 2013 - Dec 2013
• Ran the Continuous Improvement programme at Pluto and the Karratha Gas Plant with 24 improvement projects, coached 20 project leaders and 15 Sponsors • Ran the Continuous Improvement programme at Pluto and the Karratha Gas Plant with 24 improvement projects, coached 20 project leaders and 15 Sponsors
-
-
-
Alacer Gold Corp.
-
Mining
-
1 - 100 Employee
-
Business Excellence Manager
-
Jan 2012 - Jun 2013
• Project managed teams of Business Improvement Consultants (up to 16) in Australia and Turkey running improvement projects and the culture programme • Created and established 20 stand up performance meetings to promote High Performing Teams and "Leaders Standard Work" to create High Performing Leaders • Project managed teams of Business Improvement Consultants (up to 16) in Australia and Turkey running improvement projects and the culture programme • Created and established 20 stand up performance meetings to promote High Performing Teams and "Leaders Standard Work" to create High Performing Leaders
-
-
-
Newcrest Mining
-
Australia
-
Mining
-
700 & Above Employee
-
Principal Business Excellence Advisor
-
Dec 2008 - Dec 2011
• Part of the Corporate Business Excellence team developed, and change managed a Management Operating System (MOS) across Newcrest’s 7 sites • Part of the Corporate Business Excellence team developed, and change managed a Management Operating System (MOS) across Newcrest’s 7 sites
-
-
-
Rio Tinto
-
United Kingdom
-
Mining
-
700 & Above Employee
-
Lean Manufacturing Resourcing - Lean Management Consultant
-
Jul 2006 - Nov 2008
Hope Downs • Guided the Operational readiness team with 8 departments and weekly progress meetings using LEAN project management techniques • Introduced LEAN tools during the first year of operations to establish RTIO’s flagship model for LEAN Mining with monthly visits form other teams HiSmelt • An experimental Smelter, plagued with operational issues. Introduced "LEAN" stability tools which moved production levels from 50% nameplate capacity to 80% Hope Downs • Guided the Operational readiness team with 8 departments and weekly progress meetings using LEAN project management techniques • Introduced LEAN tools during the first year of operations to establish RTIO’s flagship model for LEAN Mining with monthly visits form other teams HiSmelt • An experimental Smelter, plagued with operational issues. Introduced "LEAN" stability tools which moved production levels from 50% nameplate capacity to 80%
-
-
-
Newcrest Mining
-
Australia
-
Mining
-
700 & Above Employee
-
Lean Manufacturing Resourcing - Lean Management Consultant
-
Jul 2005 - Jun 2006
• LEAN techniques used to gained operational efficiencies which resulted in the reduction of the Truck fleet from 13 to 11 • LEAN techniques used to gained operational efficiencies which resulted in the reduction of the Truck fleet from 13 to 11
-
-
-
Toyota Motor Manufacturing UK
-
United Kingdom
-
Motor Vehicle Manufacturing
-
700 & Above Employee
-
Senior Group Leader
-
Jun 2000 - Jun 2005
• 12-month training programme on TPS with coaching from Japanese experts • Ran sections of the assembly line with up to 5 Group Leaders, 20 Team Leaders and 100 Team Members • 12-month training programme on TPS with coaching from Japanese experts • Ran sections of the assembly line with up to 5 Group Leaders, 20 Team Leaders and 100 Team Members
-
-
-
Michelin
-
France
-
Motor Vehicle Manufacturing
-
700 & Above Employee
-
Production Manager
-
Dec 1997 - May 2000
• Initiated a culture change programme to bring about a step change in productivity of 30% over two years • Initiated a culture change programme to bring about a step change in productivity of 30% over two years
-
-
-
Nissan Motor Corporation
-
Japan
-
Motor Vehicle Manufacturing
-
700 & Above Employee
-
Process Supply Chain Specialist
-
Feb 1995 - Nov 1997
• Supply chain of 10 first tier automotive European suppliers • Supply chain of 10 first tier automotive European suppliers
-
-
-
British Steel
-
United Kingdom
-
Mining
-
700 & Above Employee
-
Operations Manager
-
Sep 1987 - Jan 1995
• Progressed from Operations graduate trainee to Operations Manager with 85 reports, reporting to the General Manager • Progressed from Operations graduate trainee to Operations Manager with 85 reports, reporting to the General Manager
-
-
Education
-
The Victoria University of Manchester
BSc Hons, Aeronautical Engineering -
The Grove School
3 Advanced Level Certificates: Mathematics, Physics and Chemistry
Community
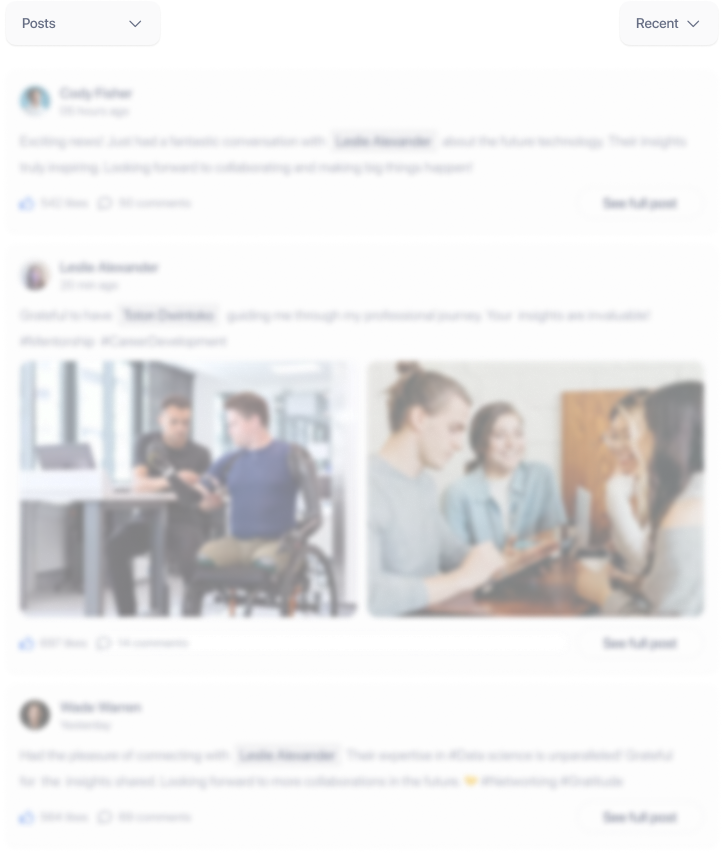