
Carmine Iuliano
Director of Safety at Rhoads Industries- Claim this Profile
Click to upgrade to our gold package
for the full feature experience.
-
Italian Native or bilingual proficiency
-
Command Spanish Limited working proficiency
Topline Score
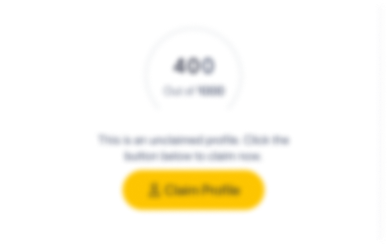
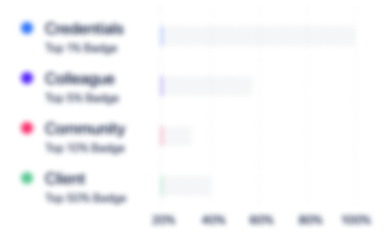
Bio

LinkedIn User
It was a true privilege to have the opportunity to work with Carmine Iuliano as a business partner and peer. Carmine has a genuine concern for employee safety and an unrelenting enthusiasm for the EH&S discipline, on display every day through his positive reinforcement of all things safety. Carmine built a well-earned reputation with his extensive knowledge and expertise, earning the trust and respect of everyone that he interfaced with. Even though Carmine is always in high demand, with responsibilities across numerous production and distribution sites, he has always made time to offer his support and imparted some sorely needed expertise to our logistics teams on fleet & warehouse safety programs. Carmine is a consummate professional, an EH&S expert, a valuable addition for any organization, and a great person to have the opportunity to work with and know.

Leonard Booth
It was a pleasure to have had the opportunity to work with Carmine, who is such an amazing safety leader. His knowledge of safety is second to none. His hands-on approach coupled with a can-do attitude allows him to quickly engage others at all levels of an organization and lead them on a safer path. I was thankful to have had such a strong partner in safety, one whose dedication to the safety of the employees inspired a shift in safety culture, moving us to what others aspired to be. I would highly recommend Carmine to any organization seeking a strong safety leader to develop and lead a national safety program.

LinkedIn User
It was a true privilege to have the opportunity to work with Carmine Iuliano as a business partner and peer. Carmine has a genuine concern for employee safety and an unrelenting enthusiasm for the EH&S discipline, on display every day through his positive reinforcement of all things safety. Carmine built a well-earned reputation with his extensive knowledge and expertise, earning the trust and respect of everyone that he interfaced with. Even though Carmine is always in high demand, with responsibilities across numerous production and distribution sites, he has always made time to offer his support and imparted some sorely needed expertise to our logistics teams on fleet & warehouse safety programs. Carmine is a consummate professional, an EH&S expert, a valuable addition for any organization, and a great person to have the opportunity to work with and know.

Leonard Booth
It was a pleasure to have had the opportunity to work with Carmine, who is such an amazing safety leader. His knowledge of safety is second to none. His hands-on approach coupled with a can-do attitude allows him to quickly engage others at all levels of an organization and lead them on a safer path. I was thankful to have had such a strong partner in safety, one whose dedication to the safety of the employees inspired a shift in safety culture, moving us to what others aspired to be. I would highly recommend Carmine to any organization seeking a strong safety leader to develop and lead a national safety program.

LinkedIn User
It was a true privilege to have the opportunity to work with Carmine Iuliano as a business partner and peer. Carmine has a genuine concern for employee safety and an unrelenting enthusiasm for the EH&S discipline, on display every day through his positive reinforcement of all things safety. Carmine built a well-earned reputation with his extensive knowledge and expertise, earning the trust and respect of everyone that he interfaced with. Even though Carmine is always in high demand, with responsibilities across numerous production and distribution sites, he has always made time to offer his support and imparted some sorely needed expertise to our logistics teams on fleet & warehouse safety programs. Carmine is a consummate professional, an EH&S expert, a valuable addition for any organization, and a great person to have the opportunity to work with and know.

Leonard Booth
It was a pleasure to have had the opportunity to work with Carmine, who is such an amazing safety leader. His knowledge of safety is second to none. His hands-on approach coupled with a can-do attitude allows him to quickly engage others at all levels of an organization and lead them on a safer path. I was thankful to have had such a strong partner in safety, one whose dedication to the safety of the employees inspired a shift in safety culture, moving us to what others aspired to be. I would highly recommend Carmine to any organization seeking a strong safety leader to develop and lead a national safety program.

LinkedIn User
It was a true privilege to have the opportunity to work with Carmine Iuliano as a business partner and peer. Carmine has a genuine concern for employee safety and an unrelenting enthusiasm for the EH&S discipline, on display every day through his positive reinforcement of all things safety. Carmine built a well-earned reputation with his extensive knowledge and expertise, earning the trust and respect of everyone that he interfaced with. Even though Carmine is always in high demand, with responsibilities across numerous production and distribution sites, he has always made time to offer his support and imparted some sorely needed expertise to our logistics teams on fleet & warehouse safety programs. Carmine is a consummate professional, an EH&S expert, a valuable addition for any organization, and a great person to have the opportunity to work with and know.

Leonard Booth
It was a pleasure to have had the opportunity to work with Carmine, who is such an amazing safety leader. His knowledge of safety is second to none. His hands-on approach coupled with a can-do attitude allows him to quickly engage others at all levels of an organization and lead them on a safer path. I was thankful to have had such a strong partner in safety, one whose dedication to the safety of the employees inspired a shift in safety culture, moving us to what others aspired to be. I would highly recommend Carmine to any organization seeking a strong safety leader to develop and lead a national safety program.

Credentials
-
Construction Management: Managing Risk
LinkedInJul, 2020- Nov, 2024 -
lead awareness training
Criterion labratories
Experience
-
Rhoads Industries
-
United States
-
Construction
-
1 - 100 Employee
-
Director of Safety
-
Jun 2022 - Present
As the Director of Safety I am responsible for every aspect of safety required by the federal, state and local governments. This requires me to have complete knowledge or know where to look for the rules and regulations governing safety in the workplace. It was my responsibility to develop and implement safety procedures for every aspect of the company, for our maritime, general industry, DOD or construction. While at Rhoads, I implemented a new confined space entry procedure, assisted Rhoads through a OSHA SST visit, that ended up with no violations or fines, and only 6 recommendations for improvement. I assist the risk manager with new hire training on all new employees plus periodic safety training with existing employees to keep them updated on the new safety procedures and changes. As Director of Safety, I have gathered and put together all reporting procedures outlined by the federal and state governing bodies. I also advise management of all safety rules and regulations on new or unfamiliar procedures. I discuss all accidents investigation findings to each supervisor and upper management per incident with corrective action suggestions, including recommendations from supervisors and management input. I also manage all safety training requirements. I conducted periodic safety inspection on all areas of Rhoads business lines, manufacturing procedures and employee safety. These inspections would include documenting any hazards found, equipment defects and whether employees are following the safety guidelines
-
-
-
Stuffed Puffs® Filled Marshmallows
-
United States
-
Food and Beverage Services
-
1 - 100 Employee
-
Environment, Health and Safety Manager
-
Feb 2022 - Jun 2022
-
-
-
Northeast Building Products
-
United States
-
Wholesale Building Materials
-
100 - 200 Employee
-
Environment, Health and Safety Manager
-
Dec 2021 - Feb 2022
Covered Chew ave site only Covered Chew ave site only
-
-
-
Puratos
-
Belgium
-
Food and Beverage Manufacturing
-
700 & Above Employee
-
National EHS Manager
-
Jun 2016 - Dec 2021
As National EHS Manager I had oversight for the following areas: All equipment processes before being implemented. I handled all WC issues and communicate with Occupational Health facilities depending on the severity of the cases , Overall monitoring of all environmental permits and forms for each site across the US. I ensure DOT compliance and new DOT Clearinghouse regulations for all distribution sites, Ensured that each site had a working knowledge of all safety regulations affecting the procedures at the site. Handle all safety concerns as needed for each site, I ensured there was a corporate procedure that was implemented and then modified to each site as needed. Do site visits with inspections and recommendations for improvement and upgrades as needed. I am constantly working on the implementation or modifications of standards to ensure compliance with cost savings initiatives. My chief goal is to get the employees, management, and unions to work together as one team to protect each other, our customers, and the environment.
-
-
-
Morgan Truck Body
-
United States
-
Truck Transportation
-
500 - 600 Employee
-
Northeast Regional Safety Engineer
-
May 2014 - Jun 2016
As Safety Engineer I was tasked with developing and implementing safety program to prevent or correct unsafe behaviors and environmental Issues. To develop human behavior working thinking that instituted safe work practices and conditions, utilizing knowledge of industrial processes, mechanics, chemistry, psychology, and industrial health and safety laws: I examined plans and specifications for new machinery or equipment to determine if all safety precautions have been included, I assisted in the design, installation and build of safety devices on machinery. I Conducted and coordinate safety and first aid training to educate workers about safety policies, laws, and practices. Investigates industrial accidents to minimize recurrence and prepares accident reports. I am responsible for keeping people free from danger, risk, or injury in the workplace.
-
-
-
Rhoads Industries
-
United States
-
Construction
-
1 - 100 Employee
-
Safety Manager
-
Jun 2011 - May 2014
As the Safety Manager I was responsible for every aspect of safety required by the federal, state and local governments. This required me to have complete knowledge or know where to look for the rules and regulations governing safety in the workplace. It was my responsibility to develop and implement safety procedures for every aspect of the company, for our maritime, general industry or construction. While at Rhoads, I implemented a new confined space entry procedure, assisted Rhoads through a OSHA SST visit, that ended up with no violations or fines, and only 6 recommendations for improvement. As part of my duties I took corrective actions when I noticed safety hazards and corrected these violations on the spot with the assistance of the appropriate supervisor. I performed new hire training on all new employees plus periodic safety training with existing employees to keep them updated on the new safety procedures and changes. As safety manager I complied will all reporting procedures outlined by the federal and state governing bodies. I also advise management of all safety rules and regulations on new or unfamiliar procedures. I discussed all accidents investigation findings to each supervisor and upper management per incident with corrective action suggestions, including recommendations from supervisors and management input. I also must manage all safety training requirements. I conducted periodic safety inspection on all areas of Rhoads business lines, manufacturing procedures and employee safety. These inspections would include documenting any hazards found, equipment defects and whether employees are following the safety guidelines.
-
-
-
Philly Shipyard, Inc.
-
United States
-
Shipbuilding
-
200 - 300 Employee
-
Environmental Health & Safety Coordinator
-
Dec 1999 - Jun 2011
Responsible for developing, and managing as well as coordinating and advising on all Shipyard wide EHS Programs in accordance with regulatory requirements in order to reduce the number and severity of injuries, violations and ensure compliance above all applicable government standards. Consults with Department Heads and Senior Managers of all departments and staff to provide direction on all EHS issues. Consulted with Safety Committees members and utilized their trade knowledge to come up with recommendations for solutions concerning safety and training. Facilitated sessions with user groups to determine needs for facility design. Develops course and training materials as well as promotes the program on site. Performed assessments of ergonomic risk factors and recommends control measures. Trained designated management staff, safety committee members and office staff to conduct field inspections. I was responsible for managing the Office Ergonomics Representatives Program involving training of designated management staff or alternatives to conduct office ergonomics assessments within their departments, as well as coordinating activities for the Office Ergonomics Representatives. Provided advice in facilitating the return of injured workers to full duty.
-
-
-
-
Steel fitter
-
Apr 1998 - Dec 1999
As a Structural Steel Fabricators I worked primarily in the shop, there were many occasions where I assisted in the overhaul or alteration of equipment at field locations. Assignments are usually oral and accompanied by structural blueprints and sketches. However, the layout, fabrication, and assembly were my responsibility. I had to utilize many pieces of heavy machinery and in handling steel members and had to be vigilant to prevent accidents. I was segregated from the class of Iron worker by the fact that the former is normally responsible for the shop fabrication and preparation of steel members for field installation and by the fact I had to work to much closer tolerances.
-
-
-
Undisdisclosed Fabricator
-
Oil and Gas
-
1 - 100 Employee
-
Metal Fitter
-
Oct 1997 - Apr 1998
Although Structural Steel Fabricators workprimarily in a shop, I assited in many overhauls or alteration ofequipment at field locations. Assignments are usually oral andaccompanied by structural blueprints and sketches. However, the layout, fabrication, and assembly were my responsibility I was assigned many duties in the operation of heavy machinery and in handling heavy steel members. The class of Structural Steel Fabricator is distinguished from the class of Iron worker by the fact that the former is normally responsible for the shop fabrication and preparation of steel members for field installation and by the fact I had to work to much closer tolerances.
-
-
-
-
Shipbuilder
-
Jul 1996 - Sep 1997
Lays out and fabricates metal structural parts, such as plates, bulkheads, and frames, and braces them in position within hull of ship for riveting or welding: Lays out position of parts on metal, working from blueprints or templates and using scribe and hand tools. Locates and marks reference lines, such as center, buttock, and frame lines. Positions parts in hull of ship, assisted by RIGGER (ship-boat mfg.). Aligns parts in relation to each other, using jacks, turnbuckles, clips, wedges, and mauls. Marks location of holes to be drilled and Installs temporary fasteners to hold part in place for welding or riveting. Installs packing, gaskets, liners, and structural accessories and members, such as doors, hatches, brackets, and clips. May prepare molds and templates for fabrication of nonstandard parts. May tack weld clips and brackets in place prior to permanent welding. May roll, bend, flange, cut, and shape plates, beams, and other heavy metal parts, using shop machinery, such as plate rolls, presses, bending brakes, and joggle machines.
-
-
-
-
Shipfittter than Leadman
-
Jul 1995 - Aug 1997
As a 2nd shift lead man I was assigned to ensure all workers completed the below task per night. Lays out and fabricates metal structural parts, such as plates, bulkheads, and frames, and braces them in position within hull of ship for riveting or welding: Lays out position of parts on metal, working from blueprints or templates and using scribe and hand tools.Locates and marks reference lines, such as center, buttock, and frame lines. Positions parts in hull of ship, assisted by RIGGER (ship-boat mfg.). Aligns parts in relation to each other, using jacks, turnbuckles, clips, wedges, and mauls. Marks location of holes to be drilled and Installs temporary fasteners to hold part in place for welding or riveting. Installs packing, gaskets, liners, and structural accessories and members, such as doors, hatches, brackets, and clips. May prepare molds and templates for fabrication of nonstandard parts. May tack weld clips and brackets in place prior to permanent welding. May roll, bend, flange, cut, and shape plates, beams, and other heavy metal parts, using shop machinery, such as plate rolls, presses, bending brakes, and joggle machines.
-
-
-
US Navy
-
United States
-
Armed Forces
-
700 & Above Employee
-
HT1 (SW) Surface Warfare
-
Aug 1983 - Jul 1995
Different Areas worked: Shipfitters shop, pipe shop, Sheet metal Shop, Galley, Naval HospitalMaintenance & Officer QuartersLast Command: USS Frank Cable AS-40Hull Maintenance Technicians are responsible for maintaining ships' hulls, fittings, piping systems and machinery. They install and maintain all shipboard and shore based plumbing and piping systems. They look after a vessel's safety and survival equipment and perform many tasks related to damage control, Ship board Fire fighting and Safety features.Mess Management specialists operate and manage US Navy messes and living quarters established to subsist and accommodate naval personnel in addition to many other duties including but not limited to: Estimate quantities and kinds of foodstuffs required.Assist supply officers in ordering and storage of subsistence items and procurement of equipment and mess gear.Check delivery for quantity and assist medical personnel in inspection for quality.Prepare menus and plan, prepare, and serve meals.Maintain food service spaces and associated equipment in a clean and sanitary condition, including storerooms and refrigerated spaces.Maintain records of financial transactions and submit required reports.Maintain, oversee, and manage quarters afloat and ashore.Navy Mess Management specialists run the White House mess for the President of the United States.
-
-
Education
-
Community College of Philadelphia
Associates Degree, Fire science -
Scotia-glenville High school
HS Diploma, General Studies
Community
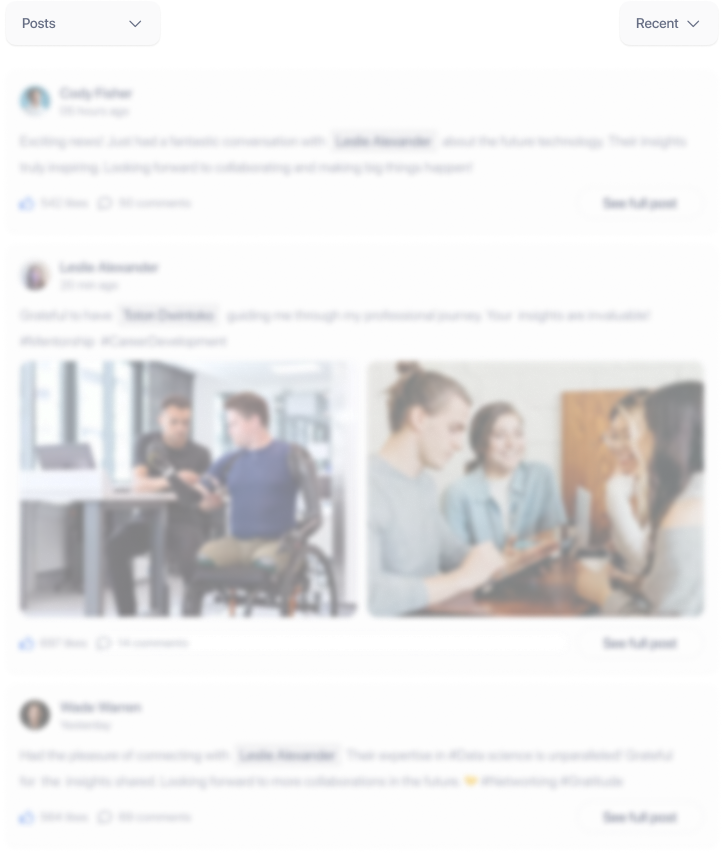