Martha M. Rollefson
Sales Associate & Instructor at Wild Birds Unlimited, Inc.- Claim this Profile
Click to upgrade to our gold package
for the full feature experience.
Topline Score
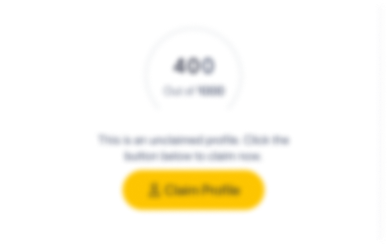
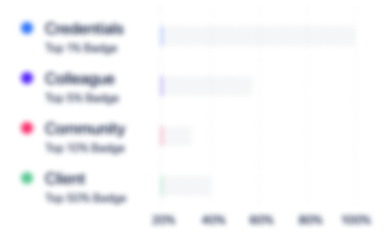
Bio

John Kiser
Martha is a real professional. We have been colleagues for over a decade. As a client she clearly communicated the results expected, then she worked with us to achieve success. Capable, reasonable, approachable and responsive, with a real understanding of what it takes to win in our business, Martha is a partner I would choose to work with any day. She helped us be winners!

Giovanna Lazzarotto
I worked with Martha for several years in Chemtura while she was the Mgr of Global Quality Assurance. Martha is a great team worker, a SAP expert and a professionist. Every issue was dealt taking care of any single detail and trying to find solutions which could work globally and which every single location could have benefit. Martha is a BIG plus for any organization who can benefit of her contribution, experience, knowledge and dedication. Giovanna Lazzarotto

John Kiser
Martha is a real professional. We have been colleagues for over a decade. As a client she clearly communicated the results expected, then she worked with us to achieve success. Capable, reasonable, approachable and responsive, with a real understanding of what it takes to win in our business, Martha is a partner I would choose to work with any day. She helped us be winners!

Giovanna Lazzarotto
I worked with Martha for several years in Chemtura while she was the Mgr of Global Quality Assurance. Martha is a great team worker, a SAP expert and a professionist. Every issue was dealt taking care of any single detail and trying to find solutions which could work globally and which every single location could have benefit. Martha is a BIG plus for any organization who can benefit of her contribution, experience, knowledge and dedication. Giovanna Lazzarotto

John Kiser
Martha is a real professional. We have been colleagues for over a decade. As a client she clearly communicated the results expected, then she worked with us to achieve success. Capable, reasonable, approachable and responsive, with a real understanding of what it takes to win in our business, Martha is a partner I would choose to work with any day. She helped us be winners!

Giovanna Lazzarotto
I worked with Martha for several years in Chemtura while she was the Mgr of Global Quality Assurance. Martha is a great team worker, a SAP expert and a professionist. Every issue was dealt taking care of any single detail and trying to find solutions which could work globally and which every single location could have benefit. Martha is a BIG plus for any organization who can benefit of her contribution, experience, knowledge and dedication. Giovanna Lazzarotto

John Kiser
Martha is a real professional. We have been colleagues for over a decade. As a client she clearly communicated the results expected, then she worked with us to achieve success. Capable, reasonable, approachable and responsive, with a real understanding of what it takes to win in our business, Martha is a partner I would choose to work with any day. She helped us be winners!

Giovanna Lazzarotto
I worked with Martha for several years in Chemtura while she was the Mgr of Global Quality Assurance. Martha is a great team worker, a SAP expert and a professionist. Every issue was dealt taking care of any single detail and trying to find solutions which could work globally and which every single location could have benefit. Martha is a BIG plus for any organization who can benefit of her contribution, experience, knowledge and dedication. Giovanna Lazzarotto

Credentials
-
formerly APICS certified (2002)
-
Experience
-
Wild Birds Unlimited, Inc.
-
United States
-
Retail
-
200 - 300 Employee
-
Sales Associate & Instructor
-
Mar 2016 - Present
-
-
-
Supply Chain Performance Improvement
-
Blue Ridge Mountain Region
-
Consulting / SAP Project Support / Temporary Coverage
-
Sep 2015 - Sep 2022
SAP/ERP implementation and assessment/performance improvement projects in Quality, Logistics, and Lean Manufacturing; temporary coverage for employees on leave from supply chain execution positions. Expertise in design and implementation, without committing clients to sustaining a permanent position. SAP/ERP implementation and assessment/performance improvement projects in Quality, Logistics, and Lean Manufacturing; temporary coverage for employees on leave from supply chain execution positions. Expertise in design and implementation, without committing clients to sustaining a permanent position.
-
-
-
LANXESS
-
Germany
-
Chemical Manufacturing
-
700 & Above Employee
-
Mgr Global Quality Assurance
-
Jan 2011 - May 2015
Strengthened the network among quality professionals scattered across sites and businesses and developed a set of shared performance expectations for improving Quality Practices.- Produced the first global platform for customer complaint management. The SharePoint system standardized entry, flow, and reporting processes, with extensive dashboards provided monthly for analysis of results and tools for real-time follow-up. Starting in 2010, used outcomes data to drive dramatic reductions in the time to resolve and close cases: reduced complaint rate, improved employee engagement and customer satisfaction with the process. - Established a global Quality Assessment & Scorecard based on complaint rates and external costs of poor quality to demonstrate impact of failures and improvements. - My small team also maintained the corporate ISO platform, SAP quality module, tools for specification management, and the vendor/material qualification process.- Led collaboration of R&D, Manufacturing, Commercial Team, and Master Data to reduce cycle time for establishing new SKUs for developmental products from weeks to days. Show less
-
-
Manager, 3rd-Party Warehousing Services
-
Jun 2001 - Dec 2010
Drove improved performance for over 2-dozen 3rd-party warehousing sites across the US, through multiple consolidations, transfers, and implementation of integrated transportation planning platform in SAP environment; provided global leadership on warehousing and logistics transaction processing to facilitate on-time delivery with short leadtimes. Provided SAP support & training for warehouse, purchasing, sales and customer service teams. Converted a fully manual system for managing distribution into an SAP/MRP–driven process. Instituted “Inventory CrossCheck” to improve batch-level accuracy while eliminating the need for costly full-scale physical inventories. Developed a battery of key performance indicators to support network rationalization and to focus negotiation and training efforts Show less
-
-
-
-
Mgr, Prodn & Inventory Planning
-
Jan 1997 - Mar 2001
Master scheduler for plant in Queretaro, Mexico producing small consumer appliances in lean, JIT environment. Focal point for manufacturing, marketing, sales and international distribution organization in balancing supply chain capability with both forecasted and real demand. Developed 12-month rolling production and inventory plans and monthly Master Production Schedule for manufacturing facility in Mexico producing Black & Decker irons, blenders, SpaceMaker coffeemakers, and Toast-R-Ovens. — Over a 3-year period, grew the job from master scheduling of 2 dozen US skus in 3 product lines to 170 skus across 12 product lines for both North and South America with sales value of over $330 million per year and average US inventory of $20 million in cost of goods sold. — Built an Excel-based advanced planning & scheduling system for negotiating production rates and setting future master production schedules while recognizing detailed constraints in mix, volume, and staffing adjustments; allocating capacity across regions; projecting inventory turns, units & dollars; comparing plan to budget, and estimating US warehouse space requirements. Increased inventory turns by >50% and reduced out-of-stocks by 30% while reducing development time from 25 days to 12 days for manufacturing’s daily shipment schedule & creating customized reports of planned shipments for each country’s commercial office. Show less
-
-
-
Rockwell Automotive
-
Troy, MI
-
Manager, Employee Development
-
Apr 1992 - Jan 1997
After several months facilitating JIT Bootcamp, shifted into HR Generalist plus Employee Development role responsible for yearly ethics & diversity seminars plus leadership development training. After several months facilitating JIT Bootcamp, shifted into HR Generalist plus Employee Development role responsible for yearly ethics & diversity seminars plus leadership development training.
-
-
-
-
Manager, Total Quality
-
Oct 1984 - Apr 1992
From 1987 to 1992, developed process documentation for fiber cable facility and transitioned into Total Quality System development, training, and internal consulting role. From 1984-1987, served as Plant Quality Manager in Fordyce, Arkansas with ~20 employees in test department and lab. Used SPC to improve confidence in finished goods quality. From 1987 to 1992, developed process documentation for fiber cable facility and transitioned into Total Quality System development, training, and internal consulting role. From 1984-1987, served as Plant Quality Manager in Fordyce, Arkansas with ~20 employees in test department and lab. Used SPC to improve confidence in finished goods quality.
-
-
-
Corning Glass Works
-
Big Flats, NY and Parkersburg, WV
-
Senior Process Engineer
-
Jun 1979 - Oct 1984
Used experiments and statistical analysis to improve quality and productivity in plants producing Pyrex tubing and laboratory glassware. Used experiments and statistical analysis to improve quality and productivity in plants producing Pyrex tubing and laboratory glassware.
-
-
Education
-
University of Wisconsin-Madison
Bachelor of Science (B.S.), Statistics -
Bellevue University
MA, Leadership -
Bellevue University
-
University of Wisconsin-Madison
Community
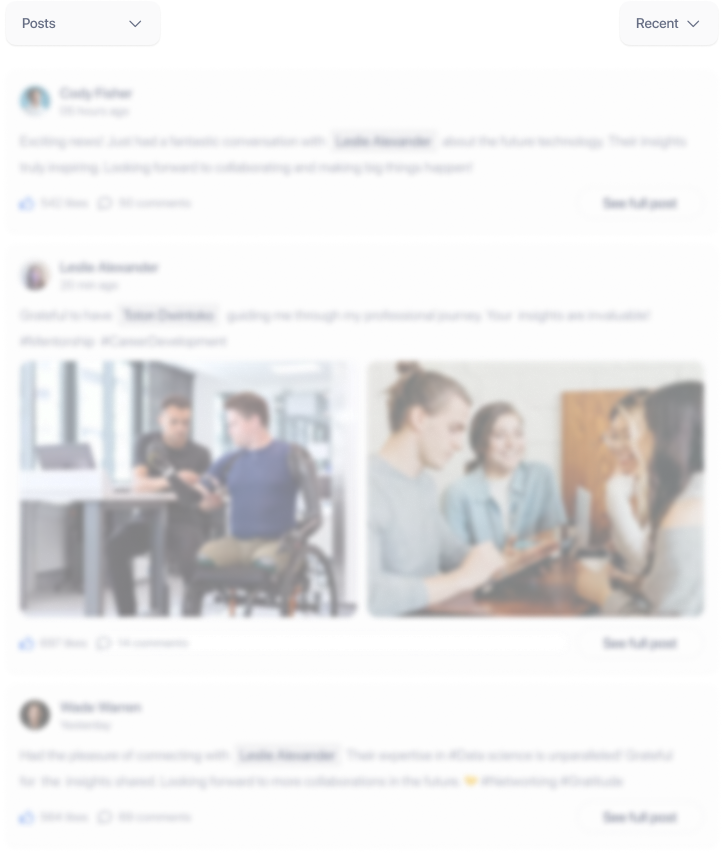