Brandon Brewer
Configuration Management Engineer at U.S. Army DEVCOM- Claim this Profile
Click to upgrade to our gold package
for the full feature experience.
Topline Score
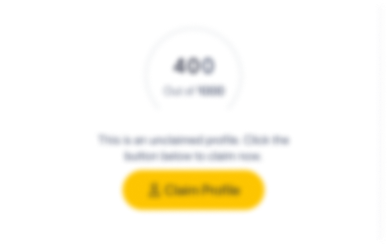
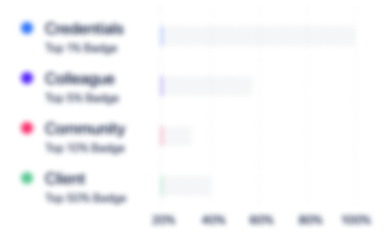
Bio


Experience
-
U.S. Army DEVCOM
-
United States
-
Government Relations Services
-
200 - 300 Employee
-
Configuration Management Engineer
-
Feb 2021 - Present
-
-
-
Niagara LaSalle Corporation
-
United States
-
Mining
-
1 - 100 Employee
-
Technical Sales Representative
-
Jan 2019 - Apr 2020
-
-
-
Corey Steel Company
-
United States
-
Mining
-
1 - 100 Employee
-
Outside Sales Trainee
-
Jun 2018 - Dec 2018
-
-
-
US Army
-
United States
-
Armed Forces
-
700 & Above Employee
-
Configuration Engineer
-
May 2017 - Jun 2018
• Managed the configuration of M4 carbine and M16 rifle weapon systems • Evaluate and processed engineering change proposals and request for variances • Developed knowledge of GD&T, 3D modeling in Creo Parametric • Represented the U.S. government professionally during contractor interactions • Managed the configuration of M4 carbine and M16 rifle weapon systems • Evaluate and processed engineering change proposals and request for variances • Developed knowledge of GD&T, 3D modeling in Creo Parametric • Represented the U.S. government professionally during contractor interactions
-
-
-
Driftwood Pub
-
Davenport, Iowa Area
-
Head Bartender
-
May 2016 - Jan 2018
Daily Job Tasks: Making cocktails, maintaining clean and orderly work environment, customer service and creating an enjoyable experience for patrons, maintaining and closing the cash drawer at night, shutting down the restaurant, and other management type activities. Daily Job Tasks: Making cocktails, maintaining clean and orderly work environment, customer service and creating an enjoyable experience for patrons, maintaining and closing the cash drawer at night, shutting down the restaurant, and other management type activities.
-
-
-
Trinity Supply Chain Solutions
-
United States
-
Transportation, Logistics, Supply Chain and Storage
-
1 - 100 Employee
-
Quality Engineer
-
Mar 2015 - Feb 2016
Daily Job Tasks: Creating ISIRs (Initial Sample Inspection Report) and PPAPs (Production Parts Approval Process) for customers and suppliers. These were completed on almost all fasteners, the most common of which being screws, bolts, nuts, pins and many other types of hardware. Common Tests Performed: Dimensional, Surface Hardness, Core Hardness, Radius Measurements, Angle Measurements, and Thread Gauging. Common Tools/Equipment Used: Caliper, Height Gage, Optical Comparator, Thread Pitch Micrometer, Go/No Go Thread Ring Gauges, Go/No Go Thread Gage, Go/No Go Plug Gauges, Radius Gauges, Angle Gauges, and Rockwell Hardness Tester. Attended Midwest Fastener Association (MWFA) Fastener Technology Workshop and MWFA Introduction to Fasteners Training Seminar. Show less
-
-
-
Quad City Manufacturing Lab
-
Moline, IL
-
Engineering Student Design Team Member
-
May 2014 - Dec 2014
Worked on a vision system for defect detection on manufacturing lines. Powered by MATLAB, this system was built from the ground up and contained many different algorithms to achieve desired results. These included a template matching feature that matched an ideal template of the part being scanned to the test subject anywhere within the view of the camera. An Arduino board was controlled via MATLAB to give commands to a stepper motor connected to a turntable with the test piece mounted on top. A graphical user interface was generated to give the user customization to the operation of the defect detection process. This included simply running the algorithm, rotating the turntable a specific number of degrees, adjusting the threshold to combat light fluctuations, and more. The coordinates of the defect were also found and stored in an array to be used in the future with tooling for removal and addition of material to correct the defects. A simple webcam produced tolerance results within 0.05" and could vastly be improved with a higher resolution camera and a smaller step rotation device. Supplementary tasks included using SolidWorks to design and create test parts, turntable top, and the mounting bracket by sending the files to a 3D plastic printer on campus. Weekly progress reports in the form of papers and presentations were also given to keep everyone up to date on the progress of the project. A final term paper was written and submitted along with a final presentation. Return on Investment analysis was also produced based on the intended use in manufacturing facilities and determined to be in the multi-million dollar range if the system if continued work was done to the system. Work based off of the project is being carried out to be implemented in a local business. This design was presented at the Illinois State Academy of Science Annual Research Conference and the Western Illinois University Student Research Conference in the Spring of 2015. Show less
-
-
-
John Deere
-
United States
-
Machinery Manufacturing
-
700 & Above Employee
-
Part Time Student Engineer
-
Sep 2013 - Apr 2014
While working for John Deere, I worked in the quality department assisting the engineers with their daily activities. This work included preparing presentations, recording data, and analyzing data. Much of my daily work was done in Microsoft Office Excel. I assisted in the launch of a major update to a product line by working with an engineer to help him analyze and present data. One of the projects I worked on was creating a digital automated final inspection checklist for one of the lines in the Davenport facility. the inspection form had over 100 tasks, where each step would include a photo of what was to be measured, a section that provided a tolerance for test values, a place to record the test values, and buttons to select whether the test passed or failed. Using macros, the checks were all stored and documented in an archive where failed tests were put into a real time graph which could be used to create a Pareto Chart to analyze these failures. Another project I was on was helping the Gage and Calibration Team create a training guide for incoming personnel. This was an in depth guide that would outline exactly how each gage was to be calibrated and how often. I also created an analysis of how many hours were spent running certain tasks in order to approximate the manpower needed. This project included checking calibration dates at work stations and ensuring that each station had the tools that they needed in order to perform their job tasks correctly. Show less
-
-
Education
-
Western Illinois University
Bachelor’s Degree, Engineering -
Sauk Valley Community College
Associate’s Degree, Engineering
Community
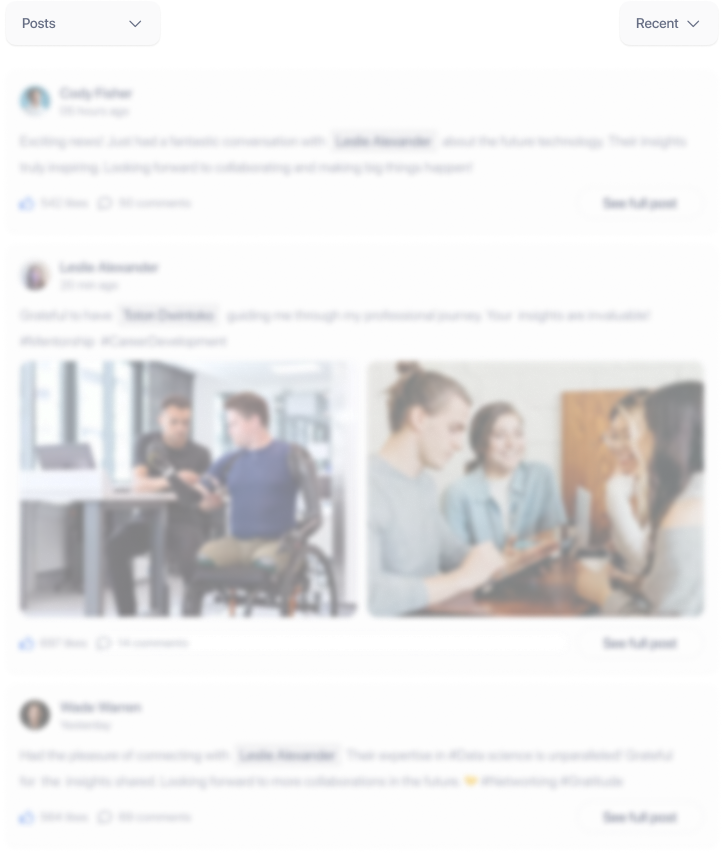