Miguel R.
Maintenance Supervisor at Yasunaga- Claim this Profile
Click to upgrade to our gold package
for the full feature experience.
-
English Professional working proficiency
-
French Limited working proficiency
-
Spanish Native or bilingual proficiency
Topline Score
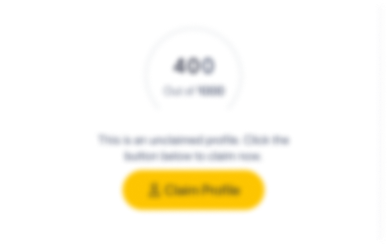
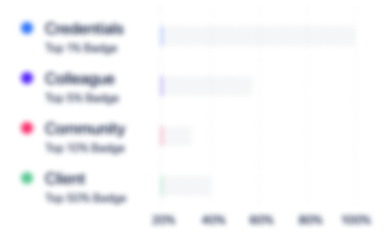
Bio


Experience
-
Yasunaga
-
Motor Vehicle Manufacturing
-
1 - 100 Employee
-
Maintenance Supervisor
-
Jan 2019 - Present
• • Diagnosed and troubleshot electrical malfunctions in CNC machines with the PLC ladder and/or electrical schematics. • Diagnosed and troubleshot electrical malfunctions in servomotors, air compressors, inductive and infrared sensors.• Performed preventative maintenance activities to the air compressors and CNC machines. (Grease lubrication, oil level check, change or cleaning of oil/coolant filters, spindle clamping pressure check, work seating pressure adjustment, residual magnetism test).• Diagnosed and troubleshot pneumatic and hydraulic systems in the CNC machines. (Clamping pressure, identified damaged directional valve and damaged pneumatic hoses)• Performed continues-improvement-works in the production processes. (Manufactured inspection tables, conveyors, raw material loading carts, etc) Using MIG and stick welding machines.• Performed CNC and PLC backups, and some ladder modifications in the Fanuc and Mitsubishi PLCs• Programmed vision system cameras (Keyence)• Performed a follow-up report of repetitive failures per month, reducing more than 60% of them.• Gained knowledge installing machinery, performing activities such as levelling and installation of auxiliary equipment.
-
-
-
Winkelmann Group
-
Germany
-
Fabricated Metal Products
-
100 - 200 Employee
-
Industrial Mechanic
-
May 2018 - Dec 2018
• Detected and troubleshot mechanical and pneumatic malfunctions in the leak-testing machines and washing machines.• Detected and troubleshot electrical irregularities and malfunctions in the laser-welding robots. (Replaced damaged inductive and photoelectric sensors; changed damaged actuators and adjusted safety curtains, etc.)• Performed preventative maintenance activities to the different types of equipment. (General cleaning, lubrication, change of filters, oil level check, etc.)• Developed a critical spare parts list for all the new equipment of the plant. Reducing downtimes by up to 60% when purchased them.
-
-
-
Woco Group
-
Germany
-
Motor Vehicle Manufacturing
-
200 - 300 Employee
-
Industrial Mechanic
-
May 2017 - May 2018
• Diagnosed and troubleshot mechanical and hydraulic faults in the rubber injection machines. (Changed damaged hydraulic pressure sensors; repaired or changed transmission chains; changed damaged hydraulic packing)• Diagnosed and troubleshot electrical faults. (Changed damaged power supply devices, electrical main switches and safety relays; tested and changed different types of fuses).• Performed preventative maintenance activities to the rubber injection machines. (General cleaning, lubrication, change of filters, oil level check).• Helped to install machinery, assembling and connecting the hydraulic and electrical systems.• Supported the start-up of the spare parts warehouse from scratch in just three months.• Developed my oral communication supporting in the attention to the German suppliers, at the beginning of the plant, translating from English to Spanish and vice versa.
-
-
-
Alucaps mexicana
-
1 - 100 Employee
-
Industrial Mechanic
-
Aug 2016 - Feb 2017
• Diagnosed and troubleshot mechanical, hydraulic and pneumatic systems in the plastic injection machines. (Changed damaged hydraulic hoses; adjusted pressure in the proportional valves as required; changed damaged transmission belts)• Diagnosed and troubleshot electrical faults in the plastic injection machines. (Tested and repaired gear-motors; tested and changed damaged heaters; adjusted or changed inductive, photoelectric and optical fiber sensors; tested and changed temperature sensors (PT100, thermocouple type J); programmed speed driver devices)• Performed preventative maintenance activities to the plastic injection machines and electrical boards. (Cleaned electrical contactors; re-tightened electrical terminals; lubricated injection machine joints with food-grade grease; checked oil levels)• Performed an automatic control for the water filling of a cooling tower’s tank. Reducing by 100% of the failures caused by this condition. (24Vdc / 480Vac).
-
-
-
-
Self Defense Instructor
-
Oct 2014 - Aug 2016
• Performed self-defence and fitness classes to more than 25 students per day. Achieving their goals monthly by 70%• Learned a lot about leadership, self-motivation and discipline.
-
-
-
Swissmex Rapid SA de CV
-
Mexico
-
Farming
-
1 - 100 Employee
-
Industrial Mechanic
-
Jan 2012 - Oct 2014
• Performed preventive maintenance activities to plastic moulding machines, air compressors, conveyors, CNC machines and hydraulic presses. Always keeping machine downtimes within the standard.• Took part of the Health and Safety commission, getting the position of secretary.
-
-
-
Alucaps mexicana
-
1 - 100 Employee
-
Industrial Mechanic
-
Oct 2008 - Jan 2012
• Troubleshot and repaired mechanical, electrical, hydraulic and pneumatic systems in the plastic injection machines, plastic compression machines, coating and sheet cutting machines. • Performed preventative maintenance activities to the plastic injection machines and electrical boards.• Developed a preventive maintenance plan for more than 300 motors in the plant. Reducing up to 70% of the downtime impact in the production operations, due to damaged motors.
-
-
Education
-
Conalep Jalisco
High School Diploma, Electrical Mechanic
Community
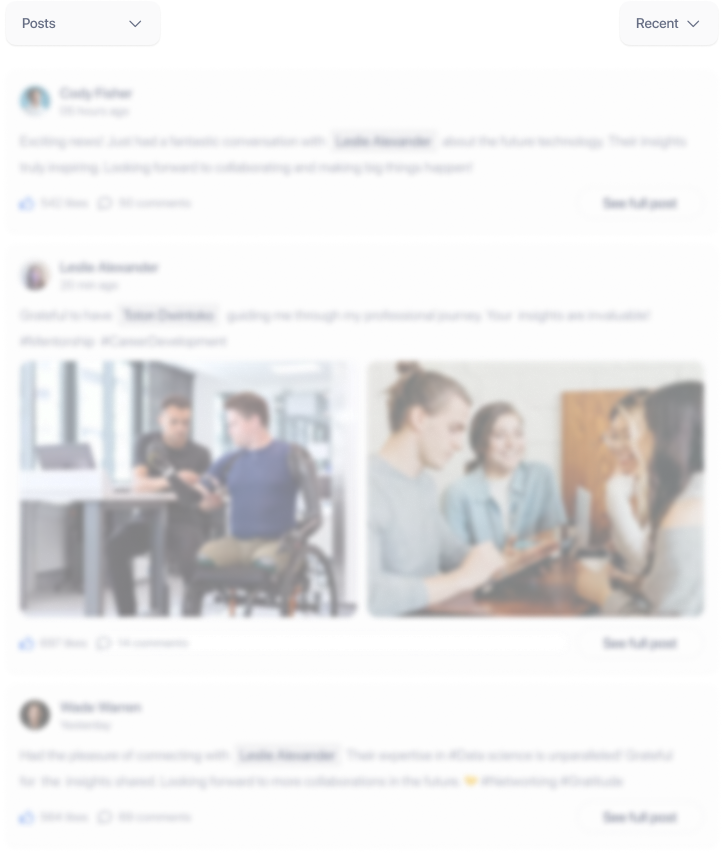