Carlon Plunk
Director of Supply Chain & Scheduling at ClockSpring|NRI- Claim this Profile
Click to upgrade to our gold package
for the full feature experience.
-
English Native or bilingual proficiency
-
Spanish Limited working proficiency
Topline Score
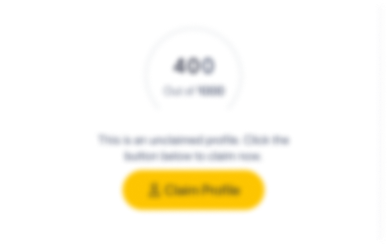
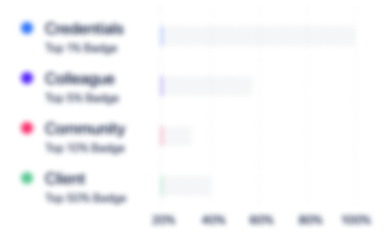
Bio

Faisal Humayun
I have been working with Carlon Plunk for last one year in material scheduling and inventory management at Goodman Manufacturing. Its a great learning opportunity. He is a friend , a coach , a leader. His analytical , innovative ,problem solving and proactive skills are matchless. In my 25years of career i have never met such a sound professional. Working with him is great blessing for me, he added a lot in my professional skills. i wish him all success in his career.

Richard Dye
I have known and worked with Carlon for over 5 years. We worked on a number of transitional projects: two in particular, the operations leadership of a 100 million $ divestiture of a complex product line. & transitioning a 240 person plant to profitability. Both of these projects impacted the same facility & which was a mixed blessing. The divestiture was fraught with errors when we became engaged. Through a lot of hard work and long days we became successful. Carlon did yeoman work and was key in reconciling bills of materials such that when the divestiture was complete which included facilities, tools, parts, materials, equipment & finish goods we had no redundant items. We transitioned ahead of plan and under budget. Carlons work in unloading from one enterprise system to another neither of which was very robust was exceptional. He was tireless in his pursuit of getting it right and he did. The other phase was to rebalance the remaining plant, working with the plant team he helped install robust systems and training that along with other operational activities improved the revenue line by 20% reduce headcount through attrition by 25%. He works hard, smart & remains very focused to deliver the strategic objective.

Faisal Humayun
I have been working with Carlon Plunk for last one year in material scheduling and inventory management at Goodman Manufacturing. Its a great learning opportunity. He is a friend , a coach , a leader. His analytical , innovative ,problem solving and proactive skills are matchless. In my 25years of career i have never met such a sound professional. Working with him is great blessing for me, he added a lot in my professional skills. i wish him all success in his career.

Richard Dye
I have known and worked with Carlon for over 5 years. We worked on a number of transitional projects: two in particular, the operations leadership of a 100 million $ divestiture of a complex product line. & transitioning a 240 person plant to profitability. Both of these projects impacted the same facility & which was a mixed blessing. The divestiture was fraught with errors when we became engaged. Through a lot of hard work and long days we became successful. Carlon did yeoman work and was key in reconciling bills of materials such that when the divestiture was complete which included facilities, tools, parts, materials, equipment & finish goods we had no redundant items. We transitioned ahead of plan and under budget. Carlons work in unloading from one enterprise system to another neither of which was very robust was exceptional. He was tireless in his pursuit of getting it right and he did. The other phase was to rebalance the remaining plant, working with the plant team he helped install robust systems and training that along with other operational activities improved the revenue line by 20% reduce headcount through attrition by 25%. He works hard, smart & remains very focused to deliver the strategic objective.

Faisal Humayun
I have been working with Carlon Plunk for last one year in material scheduling and inventory management at Goodman Manufacturing. Its a great learning opportunity. He is a friend , a coach , a leader. His analytical , innovative ,problem solving and proactive skills are matchless. In my 25years of career i have never met such a sound professional. Working with him is great blessing for me, he added a lot in my professional skills. i wish him all success in his career.

Richard Dye
I have known and worked with Carlon for over 5 years. We worked on a number of transitional projects: two in particular, the operations leadership of a 100 million $ divestiture of a complex product line. & transitioning a 240 person plant to profitability. Both of these projects impacted the same facility & which was a mixed blessing. The divestiture was fraught with errors when we became engaged. Through a lot of hard work and long days we became successful. Carlon did yeoman work and was key in reconciling bills of materials such that when the divestiture was complete which included facilities, tools, parts, materials, equipment & finish goods we had no redundant items. We transitioned ahead of plan and under budget. Carlons work in unloading from one enterprise system to another neither of which was very robust was exceptional. He was tireless in his pursuit of getting it right and he did. The other phase was to rebalance the remaining plant, working with the plant team he helped install robust systems and training that along with other operational activities improved the revenue line by 20% reduce headcount through attrition by 25%. He works hard, smart & remains very focused to deliver the strategic objective.

Faisal Humayun
I have been working with Carlon Plunk for last one year in material scheduling and inventory management at Goodman Manufacturing. Its a great learning opportunity. He is a friend , a coach , a leader. His analytical , innovative ,problem solving and proactive skills are matchless. In my 25years of career i have never met such a sound professional. Working with him is great blessing for me, he added a lot in my professional skills. i wish him all success in his career.

Richard Dye
I have known and worked with Carlon for over 5 years. We worked on a number of transitional projects: two in particular, the operations leadership of a 100 million $ divestiture of a complex product line. & transitioning a 240 person plant to profitability. Both of these projects impacted the same facility & which was a mixed blessing. The divestiture was fraught with errors when we became engaged. Through a lot of hard work and long days we became successful. Carlon did yeoman work and was key in reconciling bills of materials such that when the divestiture was complete which included facilities, tools, parts, materials, equipment & finish goods we had no redundant items. We transitioned ahead of plan and under budget. Carlons work in unloading from one enterprise system to another neither of which was very robust was exceptional. He was tireless in his pursuit of getting it right and he did. The other phase was to rebalance the remaining plant, working with the plant team he helped install robust systems and training that along with other operational activities improved the revenue line by 20% reduce headcount through attrition by 25%. He works hard, smart & remains very focused to deliver the strategic objective.

Credentials
-
Certified in Production and Inventory Management (CPIM)
APICS Supply Chain CouncilSep, 2002- Nov, 2024 -
Certified in Production and Inventory Management (CPIM)
APICS
Experience
-
CSNRI Composites
-
United States
-
Oil and Gas
-
1 - 100 Employee
-
Director of Supply Chain & Scheduling
-
Jun 2021 - Present
Responsible for leading supply chain, procurement, demand planning, warehouse operations, lean inventory control and vendor management. Responsible for leading supply chain, procurement, demand planning, warehouse operations, lean inventory control and vendor management.
-
-
-
Goodman Manufacturing
-
United States
-
Manufacturing
-
700 & Above Employee
-
Director of Procurement & Supply Chain
-
Sep 2015 - Jun 2021
Responsible for demand, supply & operations planning in high-mix/high-volume manufacturing. Managing 9 Buyers/Planners, $1B material spend. Maintaining MRP systems & leading lean supply chain strategies. • Developed supply team, through recruitment/training, supporting operations growth 3,000 to 20,000 daily units • Consolidated five sites into a single 4.2MM sf facility, developing strategic end to end supply chain systems • Reduced assembly stockouts by creating poka-yoke system for automated end of line scanning • Developed materials consolidation plan necessary to increase operations production efficiencies • Negotiated supplier agreement netting $2.8MM price reduction over 5 years • Ensured material availability to operations by creating automated exception reporting system • Developed/Implemented scheduling strategies, supporting customer demand, utilizing lean philosophy • Improved productivity of operations by developing, implementing, and tracking KPIs Show less
-
-
-
Gibson Brands, Inc.
-
United States
-
Music
-
500 - 600 Employee
-
Gibson Brands Director of Supply Chain & Procurement
-
Sep 2012 - Aug 2015
Responsible for Sourcing, Purchasing, Scheduling & Material Operations. In high-mix/high-volume manufacturing. Managed staff of 8 Buyers/Analysts/Warehouse Managers, $65MM material spend. Implementing lean production strategies. • Increased daily production from 250 to 750 units implementing MRP & lean inventory management systems • Consolidated global transportation spend, simplified supply chain, by negotiating companywide freight contract • Saved $6.5M, leading negotiations of lumber, hardware and electronics contracts • Reduced total inventory by $3.5MM, 32%, through implementation of MRP and JIT inventory practices • Saved $150K by negotiating VMI contract, increasing SKU/Location accuracy from 15% to 85% • Recovered $4M by developing "Government" series guitar product line to consume federally seized materials Show less
-
-
-
Cummins Inc.
-
United States
-
Motor Vehicle Manufacturing
-
700 & Above Employee
-
Global Supply Chain Manager
-
Sep 2008 - Sep 2012
Responsible for Development of Supply Chain Operations Solutions across eight sites in five countries. Service Distribution Inventory Planning. Managed staff of 8 Buyers/Analysts. Spend $50MM across 97K part numbers, 2,000 suppliers. • Increased operations distribution fill rate from 86% to 95.6% through forecast/stocking improvements & creation of a planner dashboard used to discover planning flaws and optimize planning system inputs • Achieved 80% late delivery improvement by matching customer demand to supplier capabilities • Ensured ISO-9001 compliance through maintenance and creation SOX compliant documents and procedures • Ensured International Traffic in Arms Regulations (ITAR) compliance through developing, implementing, and documenting operations procedures to match ISO-9001 standards • Saved $130K in labor through automating of customer service operations communication processes Show less
-
-
-
Ashley Furniture Industries
-
United States
-
Furniture and Home Furnishings Manufacturing
-
700 & Above Employee
-
Production And Inventory Control Manager
-
Sep 2002 - Apr 2008
Responsible for Development /Implementation of Capacity Planning, Schedule, Warehouse, Methodology. Implemented systems in Asia & US operations. Managed staff of 8 Buyer/Analysts. Spend $100MM. • Eliminated EOY physical WIP by creating & implementing an automated, virtual cycle counting program • Increased assembly operations efficiency, by developing scheduling systems considering, material availability, line efficiencies/capacity. Implemented globally as sales grew from $500M to $3.5B over 5 years • Ensured efficient operations during the start-up production of the Kunshan, China cut/sew facility by providing material management expertise to shop floor leadership & implementing operations lean practices • Reduced inventory variance by $100K per week through rollout of daily cycle count program Show less
-
-
-
The University of Southern Mississippi
-
United States
-
Higher Education
-
700 & Above Employee
-
Project Manager
-
Jan 2000 - Jan 2002
Managed non-profit convention center. Staff of 8 people. Responsible for maintaining building and equipment. Notable Achievements Include: *Managing facilities planning and scheduling Managed non-profit convention center. Staff of 8 people. Responsible for maintaining building and equipment. Notable Achievements Include: *Managing facilities planning and scheduling
-
-
-
Lone Star Steakhouse / Texas Land & Cattle
-
United States
-
Restaurants
-
100 - 200 Employee
-
Operations Manager
-
1996 - 2000
Managed daily operations of a $2-million annual business. Staff of 75 people. Responsible for inventory control, production and planning. Notable Achievements Include: *Experienced sales turnaround manager. Managed daily operations of a $2-million annual business. Staff of 75 people. Responsible for inventory control, production and planning. Notable Achievements Include: *Experienced sales turnaround manager.
-
-
-
UPS
-
United States
-
Truck Transportation
-
700 & Above Employee
-
Belt Leader
-
Aug 1993 - Jul 1996
-
-
Education
-
The University of Southern Mississippi
M.B.A, Business Administration, Management and Operations -
The University of Southern Mississippi
Bachelor's degree, Business Administration, Management and Operations -
University of Arkansas
Business -
Hinds Community College
Business Administration and Management, General
Community
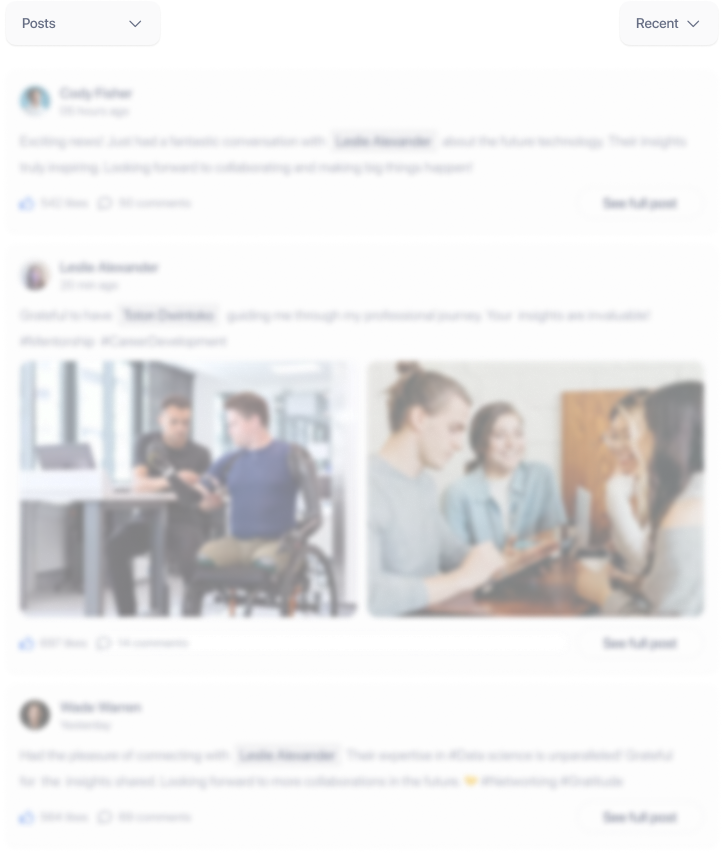