Annechris Sewards
Head Of Project Management Office at OMI Solutions (Pty) Ltd- Claim this Profile
Click to upgrade to our gold package
for the full feature experience.
-
English Native or bilingual proficiency
-
Afrikaans Native or bilingual proficiency
Topline Score
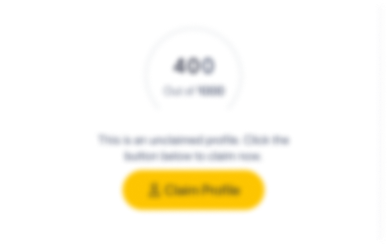
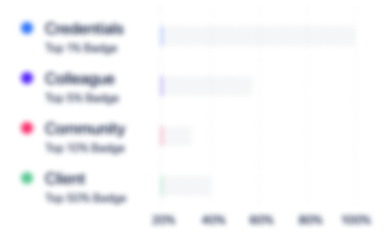
Bio

Angelika Ehrich
I was introduced to Annechris at Palabora Mining Company and got to know her as a highly effective IT Manager who managed her Department as well as her Service Providers extremely well. She understood the art of balancing day-to-day issues and requirements in view of the broader, longer term vision of her Department and the Company as a whole. Annechris was strict, but extremely fair and had a passion for the well being of her entire team. Her integrity and constant drive to improve service delivery have left a lasting impression. I would highly recommend Annechris and believe that she is a great asset to any company looking to employ her.

Paul Croney
I have known Annechris professionally for more than six years. She is a very able IT professional able to manage departments as well as to provide detailed technical advice in the areas of applications (both technical and SAP) and infrastructure.

Angelika Ehrich
I was introduced to Annechris at Palabora Mining Company and got to know her as a highly effective IT Manager who managed her Department as well as her Service Providers extremely well. She understood the art of balancing day-to-day issues and requirements in view of the broader, longer term vision of her Department and the Company as a whole. Annechris was strict, but extremely fair and had a passion for the well being of her entire team. Her integrity and constant drive to improve service delivery have left a lasting impression. I would highly recommend Annechris and believe that she is a great asset to any company looking to employ her.

Paul Croney
I have known Annechris professionally for more than six years. She is a very able IT professional able to manage departments as well as to provide detailed technical advice in the areas of applications (both technical and SAP) and infrastructure.

Angelika Ehrich
I was introduced to Annechris at Palabora Mining Company and got to know her as a highly effective IT Manager who managed her Department as well as her Service Providers extremely well. She understood the art of balancing day-to-day issues and requirements in view of the broader, longer term vision of her Department and the Company as a whole. Annechris was strict, but extremely fair and had a passion for the well being of her entire team. Her integrity and constant drive to improve service delivery have left a lasting impression. I would highly recommend Annechris and believe that she is a great asset to any company looking to employ her.

Paul Croney
I have known Annechris professionally for more than six years. She is a very able IT professional able to manage departments as well as to provide detailed technical advice in the areas of applications (both technical and SAP) and infrastructure.

Angelika Ehrich
I was introduced to Annechris at Palabora Mining Company and got to know her as a highly effective IT Manager who managed her Department as well as her Service Providers extremely well. She understood the art of balancing day-to-day issues and requirements in view of the broader, longer term vision of her Department and the Company as a whole. Annechris was strict, but extremely fair and had a passion for the well being of her entire team. Her integrity and constant drive to improve service delivery have left a lasting impression. I would highly recommend Annechris and believe that she is a great asset to any company looking to employ her.

Paul Croney
I have known Annechris professionally for more than six years. She is a very able IT professional able to manage departments as well as to provide detailed technical advice in the areas of applications (both technical and SAP) and infrastructure.

Experience
-
OMI Solutions (Pty) Ltd
-
South Africa
-
Environmental Services
-
1 - 100 Employee
-
Head Of Project Management Office
-
Sep 2021 - Present
-
-
Head of Research & Development at OMI Solutions (Pty) Ltd
-
Apr 2021 - Aug 2021
-
-
Process Engineer & Project Manager
-
Feb 2020 - Apr 2021
-
-
-
-
Project Manager & Independent Consultant
-
Aug 2007 - Jan 2020
Annechris has been working as an independent consultant since 2007, managing a variety of projects. Available for assignments as required in typically following areas:• Project Management: handling a variety of projects, from inception through scoping to planning and execution.• Business process design and implementation, in particular where humans and computers both play a role.• Change management, especially related to changes in business processes and implementation of new systems (electronic and other).• Access control / time & attendance, especially in the mining industry – assessment, scoping and implementation.• Maintenance improvement and planning.• Process improvement. Show less
-
-
Implementation of SAP Plant Maintenance
-
May 2018 - Jun 2019
Change Management Lead and Project Team Co-ordination. Included development of naming conventions, data clean-up from old system for upload to SAP, updating maintenance plans and development of formal planning processes. Caretaking planned maintenance co-ordinator role at Booysendal Platinum after PM go-live in October 2018: Embedding of SAP PM, continuing the development of maintenance plans, creating the functional location structure and task lists for BD South Mine, co-ordinating the maintenance planners from a functional point of view, liaising with engineers w.r.t. SAP PM use and issues, assisting planners with business process issues as well as SAP PM issues. Show less
-
-
Project Leader
-
Sep 2015 - Oct 2018
Project Leader for Gijima Technologies, working on a number of projects, the largest of which was an Application Support Contract for a Public Service Client: Overall management of the activities under the contract: contract negotiations, due diligence exercise at all client sites and transition management; Management of support team – developers, DBA and on-site support technicians; Planning and managing the deployment of updated versions of the application, Business improvement via user education and application improvement, change management and user training. Show less
-
-
Project Manager
-
May 2012 - Nov 2014
2014: Smelter and Acid Plant annual shutdowns: scoping, planning, resourcing and execution; 21-day shut, R25m budget, ±200 contractors involved. Completed on time and within budget, 2 minor injuries.2013: Smelter and Acid Plant annual shutdowns: scoping, planning, resourcing and execution; 21-day shut, R22m budget, ±200 contractors involved. Completed on time and within budget, 1 minor injury.2013: Various energy saving projects (in line with ESKOM SOP): verifying scope & budget, then planning and execution of projects in time to achieve projected energy savings and ESKOM funding2012: Smelter and Acid Plant annual shutdowns: scoping, planning, resourcing and execution; 3-month shut (included a Reverb hearth clean-out and partial wall rebuild), R31m budget, ±500 contractors involved. Completed on time and within budget, 1 minor injury. Show less
-
-
Project Manager - Time & Attendance projects
-
Sep 2007 - May 2012
2011-2012: Implementation of time-&-attendance system and processes at Nkomati Mine: Scoping and tender process, overseeing of implementation, troubleshooting, change management and support. Revision of related business processes.2010 – 2011: Project to interface SAP and Xtime (clocking system) at Xstrata Coal SA (now Glencore): including data preparation, management of technical activities, change management.2007 – 2009: Installation, commissioning and expansion of time-and-attendance system (SACO) at Two Rivers Platinum: work included project scoping, tender process, implementation management, change management, tender documentation, post-implementation support. Show less
-
-
Trackless Maintenance Improvement Project
-
Aug 2008 - May 2009
Leading an initiative to improve planning and execution of maintenance on TMM: including process re-design, SAP enhancements and training, improving maintenance planning processes, implementation of range of actions identified as improvement opportunities, feasibility and stocking of new trackless spares store.
-
-
-
Implats
-
Mining
-
700 & Above Employee
-
Group IT Infrastructure Manager
-
Dec 2005 - Jul 2007
IT Infrastructure for Implats Group – all sites: Rustenburg mines, Springs refineries, Head Office (Illovo), Pretoria central services office, Marula Platinum mine (Burgersfort), Zimbabwe Platinum mines (Harare, Selous and Ngezi); access control system at mining operations (Rustenburg, Marula & Zimplats); SAP Basis & authorisations; management of outsourced IT infrastructure support service providers; IT security, legal compliance and policies/procedures; implementation, maintenance and ongoing extension of IT strategy. IT budget of R32m p.a. Show less
-
-
Technical Manager
-
Sep 2004 - Nov 2005
Member of SAP and IT Infrastructure Refresh Project's management team; Integration and change management co-ordinator – ensuring the different projects mesh, and all requirements are met; Time and Attendance system upgrade project; Marula mine: IT infrastructure installation, SAP readiness, change management & time & attendance system upgrade
-
-
-
-
Laboratory & Copper Planning Superintendent
-
Jan 2004 - Aug 2004
Day-to-day running of chemical laboratory (34 staff, 7000 samples per month); metallurgical accounting and copper production planning
-
-
IT Manager
-
Feb 2002 - Dec 2003
IT infrastructure: network equipment, servers, desktops and peripherals. Maintenance, support and development of applications, including SAP and the company’s intranet and internet sites. maintenance of telephone system and administration of telecommunication – internal system, Telkom and company cellphones. IT budget of R17m p.a.In 2003, Annechris co-presented at SAPhila (held at Sun City, South Africa) on factors which ensure a successful SAP implementation.
-
-
Business Planning Manager
-
Jan 2001 - Jan 2002
Responsibilities:Production, maintenance and sales plans for industrial minerals: short, medium and long term. Sales administration, metallurgical accounting, business analysis. strategic planning. South African sales & marketing, and liaison with Japanese customers’ local offices. Achievements: Improved planning & forecasting accuracy by 8%. Creation of e-marketing web site to allow customers to place orders electronically, thereby reducing administration costs. Simplification and streamlining of metallurgical accounting systems. Improved accuracy of laboratory analyses of products by 5%. Reduced customer complaints by 9%. Show less
-
-
Maintenance Planning Superintendent
-
May 2000 - Dec 2000
Responsibilities: Maintenance planning for industrial minerals, asset management and mining: streamlining and improving the section’s service to these areas. Development of schedulers & planners. Implementing initiatives such as weekly master schedule. Capital Plan for 2001-2003. Achievements: Planning & progressing of 2 major annual plant shutdowns to completion on time and within budget. Increased planned vs unplanned maintenance by 15%. Developed and implemented new maintenance planning procedures. Show less
-
-
Continuous Improvement Superintendent
-
Mar 1999 - Apr 2000
Responsibilities: Condition monitoring, non-destructive testing and failure analysis. 8 specialists, 4 others. Ensuring a good service to the whole plant, including inspections of fabrications and repaired electrical motors, fault finding, promoting the service across site.Achievements: Extending services across site – NDE, vibration monitoring, failure analysis. Equipment failure rates reduced by average of 5%. Initiation of infra-red monitoring programme, especially on electrical installations and major equipment – failures reduced by 3% in first year. Using mechanical survey specialist to align major equipment to reduce failures – cost saving achieved >R2m in one year. Show less
-
-
Strategic Development Superintendent
-
Aug 1997 - Feb 1999
Responsibilities: Technical assistant to the General Manager, responsible for metallurgical accounting, monthly report on operations and annual production and mine business plan. Preparing ad hoc presentations for the General Manager, providing production data for internal and external queries, development of electronic database of mineral rights history.Achievements: Modernising, extending and simplifying production forecasting model. Simplifying the metallurgical accounting and reporting systems. Creation of shared source of production and other relevant data. Upgrade of Smelter process control system to “year 2000” compliance. Created electronic record of mineral rights data, history & legal requirements. Show less
-
-
Technical Supt, Smelter
-
Feb 1996 - Jul 1997
Responsibilities: Commissioning of smelter MIS system. Maintenance and upgrading of all computers in the division. Setting up of systems (computerised and manual) as required by the division. All IT-related issues. Monitoring of capital project expenditure. Achievements: Management Information System (MIS) made operational and improved. Acid plant DCS (distributed control system) upgraded. Improved the division’s capital expenditure performance against plan by 15%.
-
-
-
-
Production Controller
-
Oct 1990 - Feb 1992
Responsibilities: On-time delivery of orders. Programming of new orders into work schedules by means of capacity loading. Ensuring that casting and finishing shops achieve the weekly plan.Achievements: Reduced overdue orders from 20% (half of which was over 3 months overdue) to 5%, all less than 30 days overdue, and maintained below this level. Improved deliveries to a major customer from 30% late to 100% on time. Computerised daily production figures.
-
-
Finishing Shop Supervisor
-
Feb 1989 - Oct 1990
Responsibilities: Ensuring all processes carried out according to licensor’s specifications, all finished products meeting hardness, appearance and dimensional standards. Achieving delivery targets. Recruitment and training. Labour relations, discipline and health and safety.Achievements: 99% on-time delivery of orders. All operators in the shop multi-skilled. Customer rejects reduced from ±10% to 1%. Man-hours per tonne decreased from 20 to 15, mainly due to improvements in raw casting quality. Show less
-
-
-
Copalcor Rolling Mills
-
Wadeville, South Africa
-
Casting Plant Manager & Quality Assurance Manager
-
Jan 1987 - Mar 1988
Responsibilities: Continuous casting plant and slab foundry operations, quality control and warehouse. Recruitment and training of operators and quality control inspectors. Labour relations, discipline, health and safety. Formalising and restructuring the quality control department. Ensuring quality of products and packaging met customer requirements. Customer liaison. Achievements: Reduced customer returns from 5% to 1%. Chemical analyses in cast strip 100% within specifications. Improved overall quality standards. Show less
-
-
-
Impala Platinum Minerals Processes
-
Rustenburg, South Africa
-
Smelter Metallurgist
-
Nov 1984 - Dec 1986
A two-year graduate engineer-in-training programme was completed, which included acting as plant operator, foreman and superintendent in each department. Some metallurgical project work was done. Setting up and maintaining Lotus 1-2-3 spreadsheets for daily, weekly and monthly production figures. A two-year graduate engineer-in-training programme was completed, which included acting as plant operator, foreman and superintendent in each department. Some metallurgical project work was done. Setting up and maintaining Lotus 1-2-3 spreadsheets for daily, weekly and monthly production figures.
-
-
Education
-
The University of Manchester
MSc, Computer Science -
University of the Witwatersrand
BSc (Eng) (Met), Minerals Processing
Community
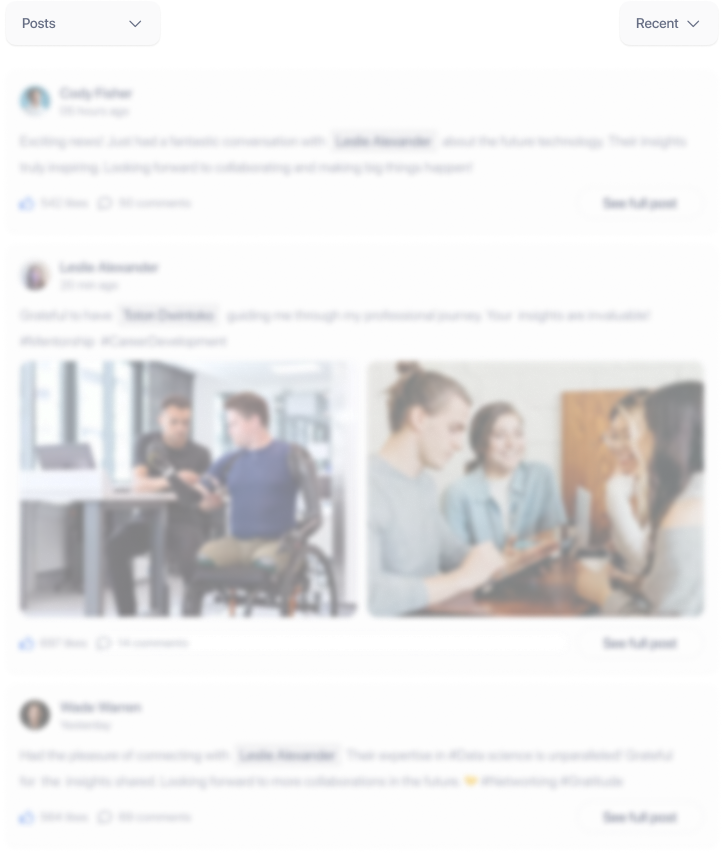