Alan Lamy
Director of Manufacturing at Kopin Corporation- Claim this Profile
Click to upgrade to our gold package
for the full feature experience.
Topline Score
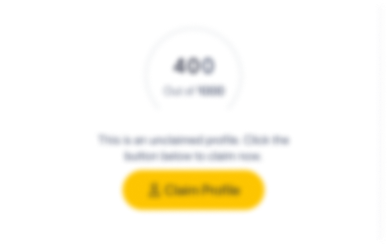
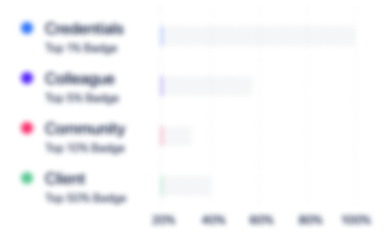
Bio


Experience
-
Kopin Corporation
-
United States
-
Semiconductor Manufacturing
-
100 - 200 Employee
-
Director of Manufacturing
-
Jun 2022 - Present
-
-
Sr. Manager, Manufacturing
-
Nov 2021 - Jun 2022
-
-
-
Skyworks Solutions, Inc.
-
United States
-
Semiconductor Manufacturing
-
700 & Above Employee
-
Section Manager 2, Operations
-
May 2018 - Oct 2021
Manage the day-to-day production activities in accordance with company policy and product quality standards. Generates and maintains records, metrics, and reports to communicate work cell goals and performance against such goals on a daily basis. Effectively utilizes labor hours to maximize line efficiencies, product yields and minimize non-value added activity. Identify and resolve production related problems by working closely with direct labor work force and support… Show more Manage the day-to-day production activities in accordance with company policy and product quality standards. Generates and maintains records, metrics, and reports to communicate work cell goals and performance against such goals on a daily basis. Effectively utilizes labor hours to maximize line efficiencies, product yields and minimize non-value added activity. Identify and resolve production related problems by working closely with direct labor work force and support personnel to provide constant focus on continuous improvement efforts on existing and new products and processes. Ensures adequate staffing, direction and disciplines are in place on a day-to-day basis. Evaluate employees through performance appraisals and take the necessary steps to reward or correct employee performance. Currently managing two of four compressed shifts. Show less Manage the day-to-day production activities in accordance with company policy and product quality standards. Generates and maintains records, metrics, and reports to communicate work cell goals and performance against such goals on a daily basis. Effectively utilizes labor hours to maximize line efficiencies, product yields and minimize non-value added activity. Identify and resolve production related problems by working closely with direct labor work force and support… Show more Manage the day-to-day production activities in accordance with company policy and product quality standards. Generates and maintains records, metrics, and reports to communicate work cell goals and performance against such goals on a daily basis. Effectively utilizes labor hours to maximize line efficiencies, product yields and minimize non-value added activity. Identify and resolve production related problems by working closely with direct labor work force and support personnel to provide constant focus on continuous improvement efforts on existing and new products and processes. Ensures adequate staffing, direction and disciplines are in place on a day-to-day basis. Evaluate employees through performance appraisals and take the necessary steps to reward or correct employee performance. Currently managing two of four compressed shifts. Show less
-
-
-
GlobalFoundries
-
United States
-
Semiconductor Manufacturing
-
700 & Above Employee
-
Sr. Section Manager Module Engineering
-
Nov 2017 - May 2018
Operations Manager responsible for the Wet Cleans module in a four shift compressed work week environment. Lead a team of 4 shift managers, 4 shift engineers and 58 manufacturing and process technicians; providing day-to-day operations support, direction and prioritization for the assigned module. An active leader in safety programs to help ensure compliance with EHS rules by visitors, contractors and employees at GLOBALFOUNDRIES Fab8. Closely interface with contractors and… Show more Operations Manager responsible for the Wet Cleans module in a four shift compressed work week environment. Lead a team of 4 shift managers, 4 shift engineers and 58 manufacturing and process technicians; providing day-to-day operations support, direction and prioritization for the assigned module. An active leader in safety programs to help ensure compliance with EHS rules by visitors, contractors and employees at GLOBALFOUNDRIES Fab8. Closely interface with contractors and service providers and vendors who provide specific maintenance or job functions as well as with the production staff to ensure key deliverables are being met (cycle time, line yield, and equipment availability metrics) Established training plans, including documentation and L3 certification packages, in order for the organization to be self-sustaining and reduce cost by eliminating vendor headcount. Lead a talent acquisition team to hire over 20 manufacturing technicians to achieve year end goal of eliminating vendor contracts. Support Fab8’s efforts in building a world class organization, achieving manufacturing excellence and establishing a team based collaborative culture based on mutual trust and respect, open and honest communications, teamwork and a passion for winning.
-
-
Sr. Section Manager/Wet Cleans
-
Mar 2015 - Nov 2017
G LOBALFOUNDRIES , Malta, NY Sr. Section Manager/Wet Clean 2015-Nov 2017 Lead a team of 16 manufacturing technicians in a compressed workweek environment. Responsible for effectively hiring, training, developing, leading, and managing the team, including development of employees’ skills and teamwork through coaching, mentoring, facilitating, and performance management. Ensured operational excellence in all aspects of factory performance, including Safety, Quality,… Show more G LOBALFOUNDRIES , Malta, NY Sr. Section Manager/Wet Clean 2015-Nov 2017 Lead a team of 16 manufacturing technicians in a compressed workweek environment. Responsible for effectively hiring, training, developing, leading, and managing the team, including development of employees’ skills and teamwork through coaching, mentoring, facilitating, and performance management. Ensured operational excellence in all aspects of factory performance, including Safety, Quality, Output, and Cost. Responsible for tool health across a fleet of 130 Wet Etch tools; prioritizing repair and preventive maintenance to meet factory output goals. Mentor to shift managers across organization to enable their development and that of their respective teams. Established training plans, including documentation and L2 certification packages, in order for the organization to be self-sustaining and reduce cost by reducing vendor headcount.
-
-
-
Intel Corporation
-
United States
-
Semiconductor Manufacturing
-
700 & Above Employee
-
Operations Manager
-
Nov 2004 - Mar 2015
November 2004 – Present (8 years 11 months)Operations manager responsible for leading a team of 28 manufacturing technicians. As an Operations Manager he is responsible for effectively hiring, training, developing, leading, and managing a team of manufacturing technicians in a compressed work week environment. He is also part of an Operations manager team responsible for achieving operational excellence in all aspects of factory performance, including Safety, Quality, Output and Cost. This… Show more November 2004 – Present (8 years 11 months)Operations manager responsible for leading a team of 28 manufacturing technicians. As an Operations Manager he is responsible for effectively hiring, training, developing, leading, and managing a team of manufacturing technicians in a compressed work week environment. He is also part of an Operations manager team responsible for achieving operational excellence in all aspects of factory performance, including Safety, Quality, Output and Cost. This includes partnering with the Module Team Leaders, Fab OMs, and shift managers. As a people manager, he owns developing his employee’s skills and teamwork, through coaching, mentoring, facilitating, leading and performance management. In addition, he is expected to role model the Fab 17 Operational Philosophy as well as the Fab 17 cultural attributes and norms. Show less November 2004 – Present (8 years 11 months)Operations manager responsible for leading a team of 28 manufacturing technicians. As an Operations Manager he is responsible for effectively hiring, training, developing, leading, and managing a team of manufacturing technicians in a compressed work week environment. He is also part of an Operations manager team responsible for achieving operational excellence in all aspects of factory performance, including Safety, Quality, Output and Cost. This… Show more November 2004 – Present (8 years 11 months)Operations manager responsible for leading a team of 28 manufacturing technicians. As an Operations Manager he is responsible for effectively hiring, training, developing, leading, and managing a team of manufacturing technicians in a compressed work week environment. He is also part of an Operations manager team responsible for achieving operational excellence in all aspects of factory performance, including Safety, Quality, Output and Cost. This includes partnering with the Module Team Leaders, Fab OMs, and shift managers. As a people manager, he owns developing his employee’s skills and teamwork, through coaching, mentoring, facilitating, leading and performance management. In addition, he is expected to role model the Fab 17 Operational Philosophy as well as the Fab 17 cultural attributes and norms. Show less
-
-
Education
-
Framingham State College
Bachelor of Arts (B.A.), Political Science and Government
Community
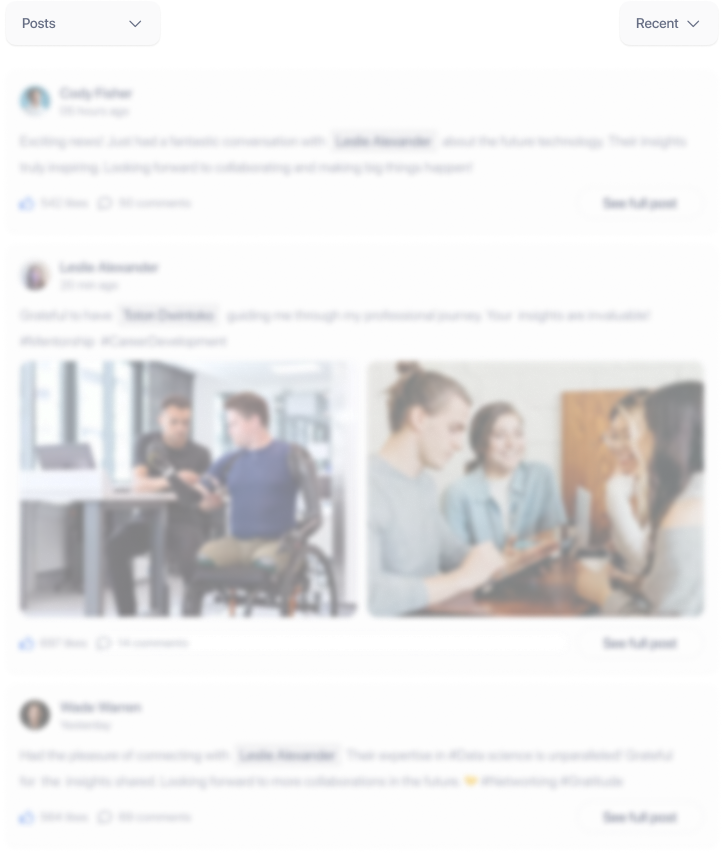