
Dave Fordy MCIPS
Interim Global Category Manager (Electronics) at Ultra Electronics Group- Claim this Profile
Click to upgrade to our gold package
for the full feature experience.
Topline Score
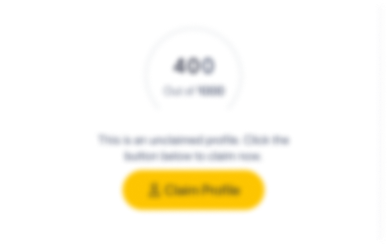
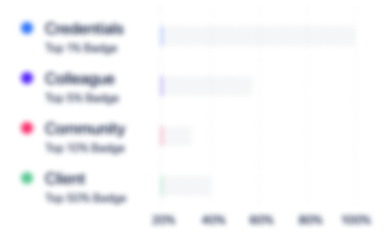
Bio


Experience
-
Ultra Electronics Group
-
Defense & Space
-
700 & Above Employee
-
Interim Global Category Manager (Electronics)
-
Jan 2021 - Present
• Engaged by the client to develop and implement a new Category Framework and Sourcing Strategy for electronic components across the global group. • Accountable to the client lead, SVP Procurement for review and acceptance of deliverables.• Maximize the collaborative benefits across the group to leverage the spend on the lowest “Total Cost of Ownership (TC0), including cost savings, compliance, risk, service levels and quality.• Develop a supply chain model utilizing franchised distributors, catalogue suppliers and brokers. • Select “strategic suppliers” and negotiate appropriate legal agreements. e.g. LTAs.• Review tail spend and identify and implement plans for vendor reduction and cost savings.• Conduct “Value Engineering and Value Analysis” across the category. Working with engineering to optimize opportunities around non branded and alternative parts, specification reviews, BOM costing exercises and “open book” pricing negotiations with vendors. • Ensure plans are in place for delivery of category benefits and savings pipeline for 2021 onwards. • Conduct risk assessments on supply chain models, resources, processes and global suppliers.• Create and manage a “risk register”, developing appropriate mitigations. • Stakeholder Management – mapping key stakeholders across the group, ensuring the category plans are developed and implemented with constructive feedback and “approval reviews”.
-
-
-
-
Interim Project Procurement Manager
-
Mar 2018 - Aug 2020
• Leading supply chain activity for the refurbishment and rebranding of Desiro 350/444/450 trains. 444/450 fleet size of 172 trains, £60m contract. Desiro 350 – fleet size of 50 trains, value £30m.• Sourcing activity and "total cost of ownership" negotiation.• Resolving key supplier tasks across categories including machining, seats and OEM systems.• Attending project and materials related face to face meetings and conference calls.• Provide material and service costing data to commercial and project teams.• Procurement subject matter expert to Commercial, Engineering and the wider project team.• Commercial and contract reviews plus resolving supplier performance issues.• Managing supply chain risk, escalating issues to senior management together with mitigating actions.• Supplier visits to determine capabilities, capacity and performance expectations.• Open order book management and expediting high risk deliveries, dealing with directors and account managers to ensure the "supply chain" critical path is adhered to.• Ensuring Siemens procurement policies and regulations are maintained.
-
-
-
ABP
-
United Kingdom
-
Defense and Space Manufacturing
-
1 - 100 Employee
-
Head Of Supply Chain
-
Sep 2017 - Dec 2017
• Head of Supply Chain responsible for £7m of direct materials and indirect categories. • Developing category management on low volume, high mix parts for bespoke military projects.• Contract management, drafting legal documents and resolving commercial issues.
-
-
-
AIM Altitude
-
United Kingdom
-
Airlines and Aviation
-
100 - 200 Employee
-
Group Head of Procurement
-
Apr 2017 - Jul 2017
• UK Group Head of Procurement managing 3 UK based teams with delivery into 4 sites. Spend £22M.• Development and ownership of KPIs including savings, OTIF, PPM and inventory value.• Leading cost reduction initiatives to meet challenging annual target of £1m+ on £22m annual spend. • Category Management of direct materials including machining, sheet metal, plastics and electronics. • Representing Procurement at the monthly project reviews attended by the board of directors and CEO.
-
-
-
ATLAS ELEKTRONIK UK
-
United Kingdom
-
Defense and Space Manufacturing
-
200 - 300 Employee
-
Head of Procurement
-
Oct 2015 - Apr 2017
• Head of function with control of circa £20m+ on direct and indirect spend.• Leading a Procurement team of 12 staff including procurement managers, buyers and administrators.• Category Management of direct materials including fabrications, machining, cables, plastics and pcbs. • Controlling indirect spend including MRO, consumables, research, capex, facilities and site services.• Negotiating Commercial Terms and Conditions for major supplier contracts including offset obligations• Developijng and implemeting a procurement startegy for the company.• Leading on both internal functional and customer led supply chain audits.
-
-
-
Honeywell
-
United States
-
Appliances, Electrical, and Electronics Manufacturing
-
700 & Above Employee
-
Site Sourcing Leader (Head of Procurement)
-
Feb 2011 - Oct 2015
• Leading a Sourcing team of 14 buyers and material controllers with a total spend in excess of $100m across 380 direct suppliers and 500+ indirect suppliers. Spend of $25m on 3rd party and $75m+ on intercompany.• Categories managed include machining, fabrications, COTS, castings, electronics and plastics.• Managing a global supply chain with suppliers based in China, Korea, Mexico, USA and Europe.• Management and reporting of KPIs including “OTTR”, savings, lead times, PPM and inventory value.• Plan for Every Part – increased % of parts ordered via pull systems to 73% (target 50%).
-
-
-
Goodrich
-
United States
-
Aviation & Aerospace
-
700 & Above Employee
-
Assistant Procurement Manager
-
Jan 2008 - Feb 2011
• Navigation procurement lead sourcing parts and materials for global defence and aerospace markets. • Projects included Eurofighter, Merlin, NLAW anti-tank weapon and legacy support.• Category management of machining, e-mech, fabrications and castings with a spend of approx. £10m. • Supplier assessment and development including negotiation of new contracts and KPIs.• Contract management, compliance and customer flow-down reviews plus supporting bid assessments.
-
-
-
Royal Air Force (RAF)
-
Armed Forces
-
700 & Above Employee
-
Senior Aircraftsman
-
Jan 1987 - Nov 1990
Personnel and Administration Branch (Trade Group 17).• Clerk to senior officers including an Air Commodore and Group Captain at HQ Strike Command. Providing administration support for the supply of 3rd party services to global RAF stations e.g. runway resurfacing, new buildings and equipment maintenance.• Following promotion and further training I was posted to RAF Brize Norton, home to the UK tanker fleet where I managed the personal documentation of officers and aircrew.• Operational clerk working shifts in an ops cell during the build up to the first Gulf War.
-
-
Education
-
Plymouth University
BA (Hons), Business Studies -
Honeywell
Six Sigma Green Belt Core, Total Quality Management -
Plymouth CFE
Graduate Diploma, Purchasing & Supply (MCIPS) - license 005049805
Community
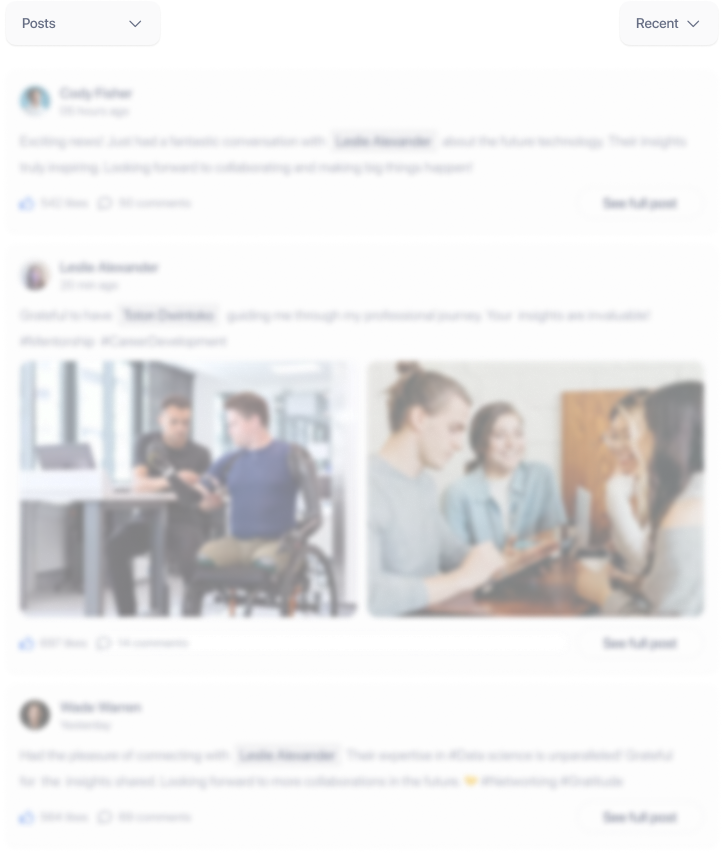