Patrick Hall
Utility and Environmental Engineer at Fuyao Glass Corporation of America- Claim this Profile
Click to upgrade to our gold package
for the full feature experience.
Topline Score
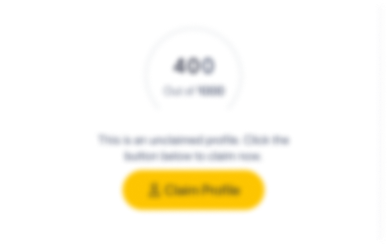
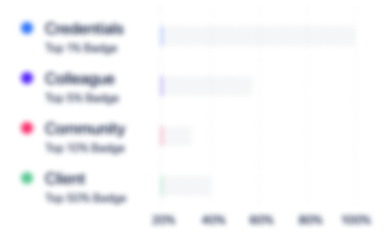
Bio

John Steel
I have worked on projects with Patrick at 3 different companies. I have found him to very knowledgeable in water chemistry, corrosion and scale control. Patrick has in-depth experience in waste water systems. I Highly recommend Patrick for help in these type systems!

Jessica Boynton, Ph.D.
Pat and I worked together when Hawkins Inc. started to buy chemical from King Lee Technologies to distribute. He was a leader at Hawkins, dedicated to organization and getting his team on the same page. He is passionate about imparting knowledge and worked with us to start a webinar series so that his team always knew about the technical aspects of the products they sold. He is not afraid to adopt changes that he knows will benefit his customers and keep the industry on the cutting edge. Every time I spoke with Pat he was working hard to further company goals and to uphold best business practices. He believes in business practices that support a partnership in the distributor/supplier relationship and is a creative problem solver.

John Steel
I have worked on projects with Patrick at 3 different companies. I have found him to very knowledgeable in water chemistry, corrosion and scale control. Patrick has in-depth experience in waste water systems. I Highly recommend Patrick for help in these type systems!

Jessica Boynton, Ph.D.
Pat and I worked together when Hawkins Inc. started to buy chemical from King Lee Technologies to distribute. He was a leader at Hawkins, dedicated to organization and getting his team on the same page. He is passionate about imparting knowledge and worked with us to start a webinar series so that his team always knew about the technical aspects of the products they sold. He is not afraid to adopt changes that he knows will benefit his customers and keep the industry on the cutting edge. Every time I spoke with Pat he was working hard to further company goals and to uphold best business practices. He believes in business practices that support a partnership in the distributor/supplier relationship and is a creative problem solver.

John Steel
I have worked on projects with Patrick at 3 different companies. I have found him to very knowledgeable in water chemistry, corrosion and scale control. Patrick has in-depth experience in waste water systems. I Highly recommend Patrick for help in these type systems!

Jessica Boynton, Ph.D.
Pat and I worked together when Hawkins Inc. started to buy chemical from King Lee Technologies to distribute. He was a leader at Hawkins, dedicated to organization and getting his team on the same page. He is passionate about imparting knowledge and worked with us to start a webinar series so that his team always knew about the technical aspects of the products they sold. He is not afraid to adopt changes that he knows will benefit his customers and keep the industry on the cutting edge. Every time I spoke with Pat he was working hard to further company goals and to uphold best business practices. He believes in business practices that support a partnership in the distributor/supplier relationship and is a creative problem solver.

John Steel
I have worked on projects with Patrick at 3 different companies. I have found him to very knowledgeable in water chemistry, corrosion and scale control. Patrick has in-depth experience in waste water systems. I Highly recommend Patrick for help in these type systems!

Jessica Boynton, Ph.D.
Pat and I worked together when Hawkins Inc. started to buy chemical from King Lee Technologies to distribute. He was a leader at Hawkins, dedicated to organization and getting his team on the same page. He is passionate about imparting knowledge and worked with us to start a webinar series so that his team always knew about the technical aspects of the products they sold. He is not afraid to adopt changes that he knows will benefit his customers and keep the industry on the cutting edge. Every time I spoke with Pat he was working hard to further company goals and to uphold best business practices. He believes in business practices that support a partnership in the distributor/supplier relationship and is a creative problem solver.

Experience
-
Fuyao Glass Corporation of America
-
United States
-
Glass Product Manufacturing
-
1 - 100 Employee
-
Utility and Environmental Engineer
-
Mar 2022 - Present
-
-
-
H2 Global Solutions
-
Colorado Springs, Colorado, United States
-
Technical Director
-
May 2020 - Jun 2022
-
-
-
4A Water Consulting
-
United States
-
Small Business Owner
-
Mar 2020 - May 2020
4A Water Consulting offers a unique combination of technical knowledge and analytical expertise with the ability to give an unbiased assessment of vulnerable points and provide chemical recommendations to improve system efficiency. 4A Water Solutions can apply Patrick's extensive water treatment experience in areas of equipment, chemicals, reporting, training, and legionella risk management to your systems to ensure optimum system performance. 4A Water Consulting offers a unique combination of technical knowledge and analytical expertise with the ability to give an unbiased assessment of vulnerable points and provide chemical recommendations to improve system efficiency. 4A Water Solutions can apply Patrick's extensive water treatment experience in areas of equipment, chemicals, reporting, training, and legionella risk management to your systems to ensure optimum system performance.
-
-
-
Solid Blend Technologies
-
Dayton, Ohio Area
-
Project Manager
-
May 2019 - Mar 2020
-
-
-
BEAVER RESEARCH COMPANY
-
United States
-
Chemical Manufacturing
-
1 - 100 Employee
-
Technical Director, Water Technologies Division
-
Nov 2018 - May 2019
-
-
-
4A Water Consulting
-
Avon, IN
-
Owner
-
Dec 2017 - May 2019
4A Water Consulting offers a unique combination of technical knowledge and analytical expertise with the ability to give an unbiased assessment of vulnerable points and provide chemical recommendations to improve system efficiency. 4A Water Solutions can apply Patrick's extensive water treatment experience in areas of equipment, chemicals, reporting, training, and legionella risk management to your systems to ensure optimum system performance. 4A Water Consulting offers a unique combination of technical knowledge and analytical expertise with the ability to give an unbiased assessment of vulnerable points and provide chemical recommendations to improve system efficiency. 4A Water Solutions can apply Patrick's extensive water treatment experience in areas of equipment, chemicals, reporting, training, and legionella risk management to your systems to ensure optimum system performance.
-
-
-
Hawkins, Inc.
-
United States
-
Chemical Manufacturing
-
200 - 300 Employee
-
Business Development Manager for the Boiler, Cooling, and RO Division
-
Aug 2016 - Dec 2017
Developing the boiler and cooling water, closed loop, and RO division for Hawkins Chemical, Inc. Overseeing all technical support for the company in the division including emergency phone calls, emails, and remote online monitoring. Implementing training webinars for remote branches in the division. Managing and maintaining the Hawkins EServe online reporting system as the key contact and administrator. Traveling to various branches throughout the country to conduct site and system surveys.
-
-
Boiler, Cooling, and RO Technical Applications Specialist
-
Nov 2015 - Jul 2016
Supported the boiler and cooling water, closed loop, and RO division for Hawkins Chemical, Inc. Assisted with technical support including emergency phone calls, emails, and remote online monitoring. Procured AWT membership for Hawkins to continue improving training for their water treatment professionals. Developed and maintained the Hawkins EServe online reporting system as the key contact and administrator. Traveled to various branches throughout the Midwest to conduct site and system surveys. Created sales proposals for various applications in the water treatment, boiler and cooling water, and RO divisions. Show less
-
-
-
H2O Innovation
-
Canada
-
Environmental Services
-
200 - 300 Employee
-
Territory Service Specialist
-
Feb 2014 - Nov 2015
Managed H20’s assets at customer locations in a 5 state territory. Ordered inventory and equipment on an as needed basis while maintaining accounts receivable. Demonstrated safe working behaviors and procedures. Established relationships at all levels of customer accounts. Developed and executed service plans based on customer driven need. Generated and maintained up-to-date process data, system diagrams, and customer organizational charts. Serviced all forms of pretreatment including green sand, ultra filtration, reverse osmosis, and various other filtration systems. Problem solved and discussed continuous improvement with customers. Effectively resolved complaints. Continued education by taking advantage of training opportunities when available. Show less
-
-
-
Fremont Industries
-
Sioux City, Iowa Area
-
Account Manager
-
Apr 2011 - Nov 2013
Account Manager Managed chemical inventory for a $300,000 territory. Provided customer service and water testing for more than twenty customers. Maintained service reports detailing product usage, operational compliance, and system analysis. Troubleshot production efficiencies. Supervised new startup and system transitions for new and current customer base. Completed assessments and developed new clientele for territory growth through cold calls and networking with current customers. Sold chemical programs based on surveys and operational analyses to meet client needs. Show less
-
-
-
Nalco
-
Sioux City, Iowa Area
-
Technical Service Specialist
-
Jun 2006 - Apr 2011
Met with customers on a weekly to monthly basis to develop and follow service plans meeting their needs. Participated in business reviews. Responsible for all aspects of job safety, including following local safety regulations and meeting OSHA codes. Performed a multitude of water sampling tests. Executed flow and elution studies. Developed customer relationships. Ordered chemicals and completed service reports. Reported safety concerns at customer sites and corrected hazards. Completed monthly schedules to accommodate personal training and district meetings while maintaining customer service plan needs. Conducted customer training on equipment standards, test methods, and operations. Show less
-
-
-
Advanced Brand Foods
-
Orange City, IA
-
2nd Shift Production Supervisor
-
Jun 2004 - Jun 2006
Interviewed and hired employees for 2nd shift production. Acted in a human resources capacity for employee complaints and conflicts. Produced ready-to-eat products from raw materials through the cooking stage on three separate lines simultaneously. Reviewed and verified all HACCP documents pertaining to the cooking process, including oven temps and deviated product. Completed employee evaluations and reviews. Scheduled daily production. Communicated in both English and Spanish with an average of 15 employees on a daily basis to avoid accidents and product loss. Investigated and completed all safety documentation for employee accidents and production downtime. Show less
-
-
-
US Filter
-
Columbus, Ohio; Indianapolis, IN; LaVista, NE
-
Resin Regeneration Lead
-
Oct 2000 - Jun 2004
~ FIELD TECHNICIAN 2/2004 - 6/2004 Responsible for the exchange of exhausted resin tanks, ultraviolet bulbs, micron and carbon filters, and other equipment responsible for maintaining water quality in a variety of work environments including testing laboratories, hospitals and dialysis facilities, the Henry Doorly zoo, and various other water treatment facilities. Performed basic plumbing repairs and installations. Integral part of assessing and communicating customer needs. ~ REGENERATION SUPERVISOR 6/2002 - 1/31/04 Ran regeneration and production of general industry end of largest US Filter plant in the continental United States. Constantly monitored and maintained quality, conductivity, and resistivity of regenerated resin and water. Repaired and maintained plumbing and other necessary equipment to finish regeneration processes. ~ 2ND SHIFT REGENERATION LEAD PERSON 10/2000 - 8/2002 Regenerated Cation and Anion resin for water purification. Maintained all safety and batch records in accordance with Company and City Municipality policies. Responsible for the supervision of safe unloading of bulk HCL (acid) and NAOH (caustic soda). Delegated as Safety Coordinator for 2nd and 3rd shift employees. Responsible for quality control and production reports. Show less
-
-
Education
-
Jackson High School
-
Ohio University
Education
Community
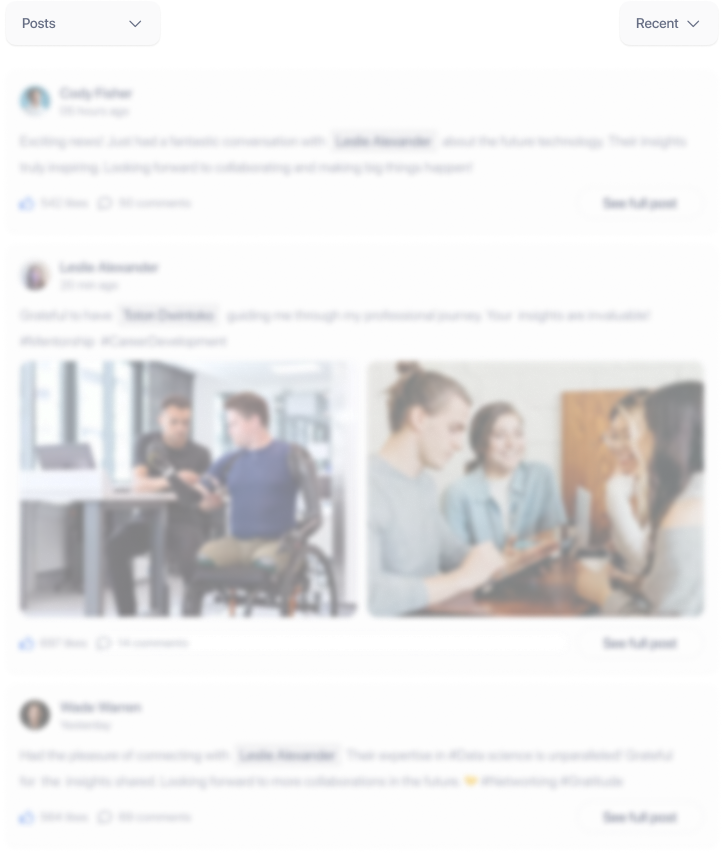