John Ziadat
Engineering Lead – Stoke Analysis at STOKE Space Technologies- Claim this Profile
Click to upgrade to our gold package
for the full feature experience.
Topline Score
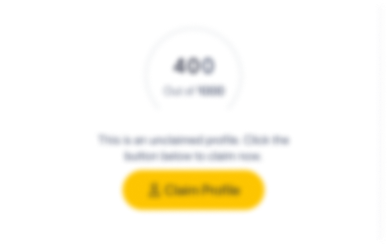
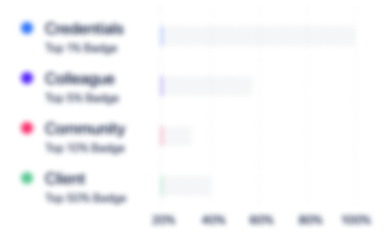
Bio


Experience
-
Stoke Space
-
United States
-
Defense and Space Manufacturing
-
1 - 100 Employee
-
Engineering Lead – Stoke Analysis
-
Dec 2021 - Present
-
-
-
BLUE ORIGIN
-
United States
-
Defense and Space Manufacturing
-
700 & Above Employee
-
Senior Propulsion Analyst
-
Oct 2020 - Dec 2021
Lead Structural Analyst - BE4 Turbomachinery and Gimbal Assembly +Lead team of engineers in high-velocity structural design/analysis of the BE4 Turbomachinery – Boost Pump, Spin Start, Main LOx Pump, Main Fuel Pump, Main Turbine Assembly, and Preburner System. Also the responsible analyst for the Gimbal Assembly. +Spearheaded full powerpack assembly design/analysis cycle in order to meet evolving program strength, life, and performance requirements. Deliverables included the development of the industry’s first fully reusable, orbital class, additively-manufactured Main Turbopump Housing architecture at fractional cost compared to single use systems; from concept to successful test campaign in under one year. +Development of the Propulsion department's Joint Loading Software Program (MatLab) which automates the combinations of fundamental engine environments - including but not limited to combustion-induced vibe, sine tones/harmonics, and mission-specific loading (e.g. vehicle-maneuvering) - for direct consumption by stress engineers. +Standardized strain gaging procedures & processes as a means of anchoring analysis predictions. +Built Powerpack Assembly Dynamic Model for quantifying harmonic environments; anchored predictions to test data.+Propulsion Methods Document Review Board Member: Strength, Fatigue, and Weld Analysis Methods. Show less
-
-
Propulsion Analyst
-
Jun 2017 - Oct 2020
Positions Held +Initially hired as Propulsion Analyst Level I in June 2017. +Promoted through levels I, II, and III, to IV (Senior) in October 2020. Key Roles/Projects +Responsible Structural Analyst for the BE4 Heat Exchanger (autogenous pressurization). +Constructed company’s first ever 3D fits/clearance model for an entire turbine assembly. Fully coupled thermal/mechanical, including thermal shock and hot re-start/soakback effects. +Analytical design of virtually every liquid engine component type: Ducts, small lines, valves, manifolds, housings, brackets, bolted joints, gimbals, thrust chambers, heat exchangers, and rotating equipment. +Significant experience performing a wide array of analysis tasks: Static, modal, forced response, thermo-mechanical (SS and transient), fatigue, and fracture. +Played key roles in several engine anomaly Root Cause Investigations – fault tree construction, burndown, and modeling efforts. Show less
-
-
-
SpaceX
-
United States
-
Aviation and Aerospace Component Manufacturing
-
700 & Above Employee
-
Propulsion Structural Analyst - Turbopumps (Summer Position)
-
May 2016 - Aug 2016
•Provide structural, thermal, fatigue, and fracture analysis for SpaceX's Merlin 1D and MVacD turbopump assembly •Utilize various numerical methods, including Finite Elements (ANSYS), to help ensure engines meet strength and life margins • Oversee/conduct cyclic pressure tests on turbopump hardware to anchor numerical results and to ground more complex (e.g. elastic-plastic) analyses. • Conduct sensitivity analyses to quantify the impact of design variables on structural margins (e.g. geometric tolerances/stack-ups + repairs) Show less
-
-
-
SpaceX
-
United States
-
Aviation and Aerospace Component Manufacturing
-
700 & Above Employee
-
Mechanical Design Engineer (Intern & Full Time)
-
May 2014 - Sep 2015
• Part of team that conceptualized, designed, and manufactured an automated Phased-Array Ultrasonic (PAUT) Friction-Stir Weld Inspection System that reduced associated inspection times by 66% • Coded MatLab program that took data collected on the production floor as input and used this information to create informative and meaningful graphical outputs; the likes of which aided in high-level probability of detection studies as a means of qualifying new & cutting-edge NDE (Non-Destructive Examination) technologies • Design and validation of numerous custom systems and tools for the purpose of improving the quality, efficiency, and repeatability of the NDE performed on some of the most advanced spacecraft technology in the world • Utilized high-end CAE/CAD tools to form, analyze, document, and communicate my designs. Documentation included information necessary for manufacturing - 2D drawings and MBD/3D PMI • Worked with machine shop and external vendors to meet compressed timelines in a fast-paced environment Show less
-
-
-
South Dakota Mines
-
United States
-
Higher Education
-
400 - 500 Employee
-
Research Assistant – Large Underground Xenon (LUX)-Zeplin Experiment (Gen-2 Dark Matter Experiment)
-
2014 - 2014
• Designed a cryogenically-cooled vacuum chamber and gas feed system for the world’s most sensitive detector of radioactive contamination on surfaces • Performed fluid and thermo-mechanical analyses to inform my design; communicated conclusions to a multi-disciplinary team of professors and student researchers • Vetted and incorporated off-the-shelf products to be combined with my own, custom mechanical components • Established documentation, plans, and procedures for operating the resulting system and interpreting results Show less
-
-
SDSMT “Moonrocker” Robotics Team – Design Lead
-
2010 - 2014
• Led team of 12+ interdisciplinary STEM students in the design of a fully-autonomous and/or remote controlled mining robot for application on the Moon, Mars, or an asteroid • Implemented “Test Early, Test Often” methodology to drive reliable and rapid system iteration • Performed flexural, fatigue, static, thermodynamic, control, manufacturability, and cost benefit analyses to – in combination with test results – inform design direction• Carried out numerical analysis to predict static and dynamic response of vehicle under operating conditions Show less
-
-
-
Burns & McDonnell
-
United States
-
Construction
-
700 & Above Employee
-
Pressure Vessel Design Intern
-
2013 - 2013
• Aided in the design and analysis of refinery pressure vessels per ASME Section VIII • Created engineering drawings that documented and specified design criteria, nondestructive examination and inspection acceptance standards, and field testing procedures • Traveled to on-site construction locations to help ensure quality of installation processes • Performed analysis of custom piping systems using 1st principle fluid-mechanics • Designed Visual Basics-driven spreadsheet program to automate certain thermal-mechanical analysis processes and yield important outputs that informed downstream equipment selection Show less
-
-
Education
-
South Dakota School of Mines and Technology
Master’s Degree, Mechanical Engineering -
South Dakota School of Mines and Technology
Bachelor’s Degree, Mechanical Engineering
Community
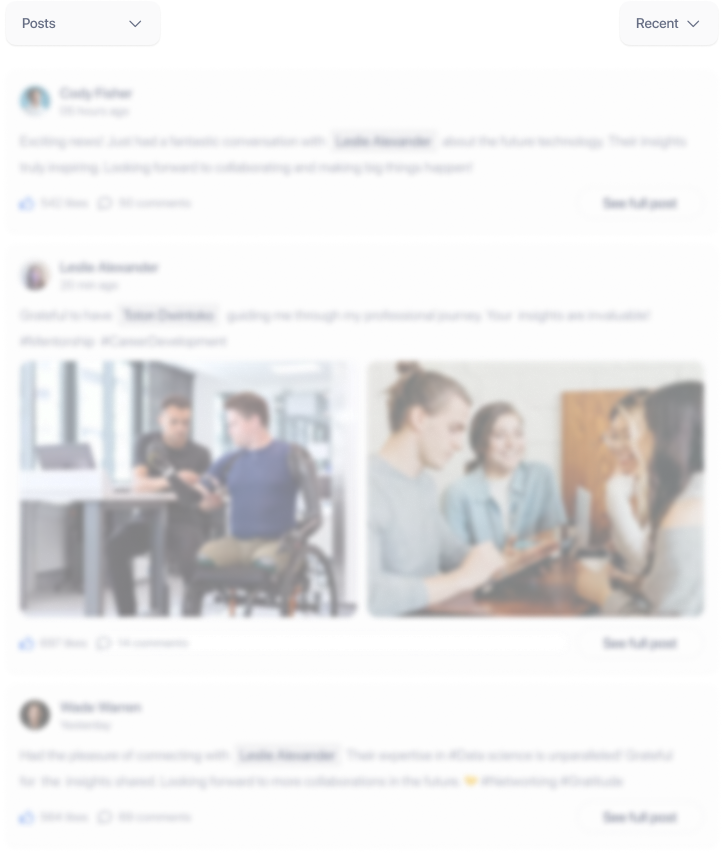