David Williams
Director Environmental, Health Safety and Human Resources at Cornerstone Detention- Claim this Profile
Click to upgrade to our gold package
for the full feature experience.
Topline Score
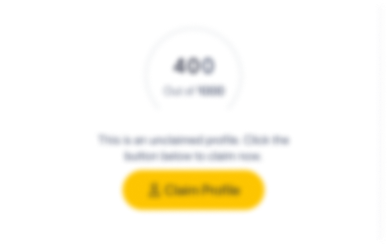
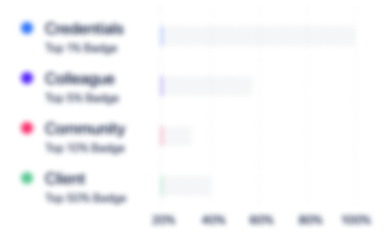
Bio


Credentials
-
Navigating Organizations: A Manager's Roadmap
Vanderbilt University - Owen Graduate School of ManagementNov, 2023- Oct, 2024 -
Strategic Innovation
Vanderbilt University - Owen Graduate School of ManagementJun, 2023- Oct, 2024
Experience
-
Cornerstone
-
United States
-
Construction
-
1 - 100 Employee
-
Director Environmental, Health Safety and Human Resources
-
Apr 2020 - Present
-
-
-
P&C Construction, INC.
-
United States
-
Construction
-
1 - 100 Employee
-
Human Resources/Safety Director
-
May 2008 - Apr 2020
Handle all safety related issues: reporting, record keeping, and training. OSHA 30 hour, First Aid and CPR, Competent Person, & Accident Investigation. Human Resources functions: Recruiting, interviewing, onboarding, benefits, performance reviews, disciplinary actions, terminations. Created job descriptions Implemented formal review program Handle all safety related issues: reporting, record keeping, and training. OSHA 30 hour, First Aid and CPR, Competent Person, & Accident Investigation. Human Resources functions: Recruiting, interviewing, onboarding, benefits, performance reviews, disciplinary actions, terminations. Created job descriptions Implemented formal review program
-
-
-
-
Purchasing and Inventory Manager
-
Sep 2005 - May 2008
Southeast Rubber & Safety., Inventory Control, Database Management, Purchasing; Purchasing inventory for a multi-million dollar business. Cycle counts, identifying needs and keeping stock levels correct. Implementing new computer system to help control inventory, track sales and purchases. Southeast Rubber & Safety., Inventory Control, Database Management, Purchasing; Purchasing inventory for a multi-million dollar business. Cycle counts, identifying needs and keeping stock levels correct. Implementing new computer system to help control inventory, track sales and purchases.
-
-
-
U.S. Xpress, Inc.
-
United States
-
Truck Transportation
-
700 & Above Employee
-
Extended Coverage Coordinator & Load Planner
-
Jan 2004 - Jan 2005
Responsible for about 200 trucks on weekend night shift. Responsible for the timely delivery of loads for customers and to keeping the drivers of the trucks happy. Responsible for about 200 trucks on weekend night shift. Responsible for the timely delivery of loads for customers and to keeping the drivers of the trucks happy.
-
-
-
BOC UK & Ireland
-
United Kingdom
-
Mechanical Or Industrial Engineering
-
700 & Above Employee
-
Parts Manager
-
Jan 2000 - Jan 2004
Responsible for the daily activities in the National Trailer Rehab Center's parts department. Work with the truck shops throughout the nation to help keep downtime on the trucks to a minimum. Purchase the best parts for the job at the best price. Responsible for the daily activities in the National Trailer Rehab Center's parts department. Work with the truck shops throughout the nation to help keep downtime on the trucks to a minimum. Purchase the best parts for the job at the best price.
-
-
-
Sears Home Services
-
Consumer Services
-
700 & Above Employee
-
Parts Redesign Implementer & Routing Manager
-
Mar 1993 - Jul 2000
Responsible for implementing the inventory redistribution of slow-moving parts throughout the United States. Work with corporate headquarters to develop standards and procedures on part “sweeps”. Work with unit managers on parts issues; train field associates on part quality identification and inventory accuracy best practices. Provide leadership in identifying continuous improvement opportunities within parts supply chain. Report to the National Inventory Manager. “Sweep” process… Show more Responsible for implementing the inventory redistribution of slow-moving parts throughout the United States. Work with corporate headquarters to develop standards and procedures on part “sweeps”. Work with unit managers on parts issues; train field associates on part quality identification and inventory accuracy best practices. Provide leadership in identifying continuous improvement opportunities within parts supply chain. Report to the National Inventory Manager. “Sweep” process redistributed over $20M of excess inventories Initiated several process enhancements; established packing list requirements for all returns, including special handling of “no longer available” parts Responsible for all activities related to routing service orders, including scheduling and routing approximately 130 service technicians over a six-state region to maximize technical payroll. Provided leadership for Route Specialists, Clerical Associates and Message Center Specialists. Essential functions include customer service, payroll management, audits to maximize productivity, and communication of performance issues to Technical Managers. Show less Responsible for implementing the inventory redistribution of slow-moving parts throughout the United States. Work with corporate headquarters to develop standards and procedures on part “sweeps”. Work with unit managers on parts issues; train field associates on part quality identification and inventory accuracy best practices. Provide leadership in identifying continuous improvement opportunities within parts supply chain. Report to the National Inventory Manager. “Sweep” process… Show more Responsible for implementing the inventory redistribution of slow-moving parts throughout the United States. Work with corporate headquarters to develop standards and procedures on part “sweeps”. Work with unit managers on parts issues; train field associates on part quality identification and inventory accuracy best practices. Provide leadership in identifying continuous improvement opportunities within parts supply chain. Report to the National Inventory Manager. “Sweep” process redistributed over $20M of excess inventories Initiated several process enhancements; established packing list requirements for all returns, including special handling of “no longer available” parts Responsible for all activities related to routing service orders, including scheduling and routing approximately 130 service technicians over a six-state region to maximize technical payroll. Provided leadership for Route Specialists, Clerical Associates and Message Center Specialists. Essential functions include customer service, payroll management, audits to maximize productivity, and communication of performance issues to Technical Managers. Show less
-
-
Education
-
Covenant College
Bachelor’s of Science, Organizational Management -
Dalton State College
Associate of Science (A.S.), Early Childhood Education and Teaching
Community
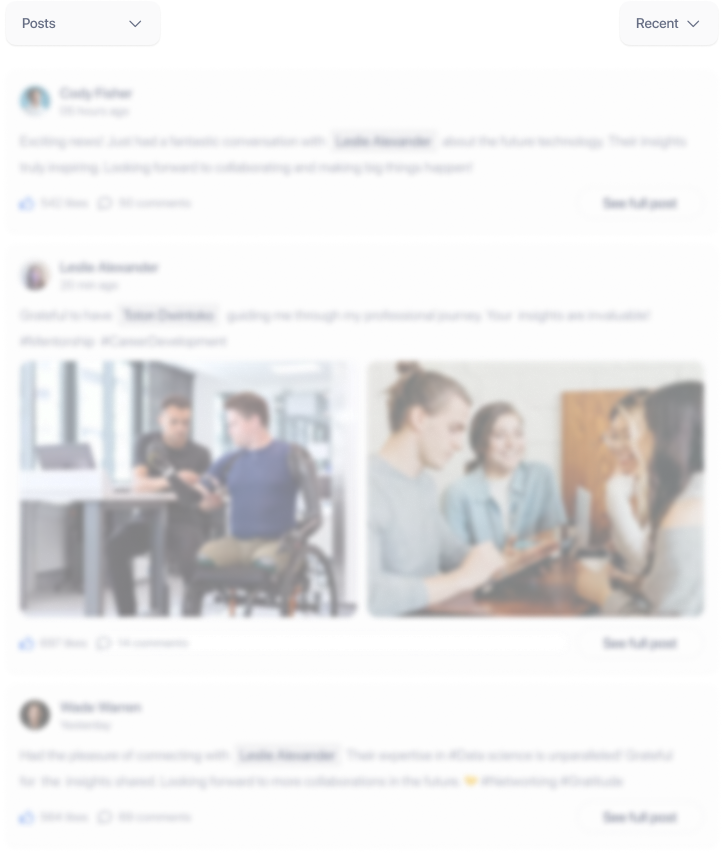