Clayton Malaney
Project Manager at NORESCO- Claim this Profile
Click to upgrade to our gold package
for the full feature experience.
Topline Score
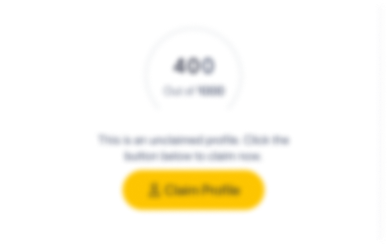
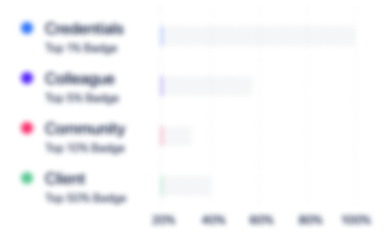
Bio


Experience
-
NORESCO
-
United States
-
Construction
-
300 - 400 Employee
-
Project Manager
-
Sep 2017 - Present
Responsible for the coordination of a project team responsible for the management of customers, subcontractors, and vendors for design-build Energy Savings Projects Lead project plans, schedules, and budgets for projects and identifies, develops, and gathers necessary resources to ensure project completion Manage aspects of a project: allocate resources, drive strategic planning, and assign tasks to ensure targets are met Prepare reports to communicate the status of the project within the project team Identify project problems and recommend solutions, such as reallocating resources, changing contractual specifications, and assisting resolution development Show less
-
-
-
US Navy
-
United States
-
Armed Forces
-
700 & Above Employee
-
Facilities Manager
-
Oct 2015 - Apr 2023
Responsible for managing the day-to-day equipment, maintenance and operations, contract services, material, and supplies purchases for plant operations. Monitor and ensure location is maintained up to standard by making recommendations to improve the appearance and safety of the location. Coordinate all equipment, HVAC, plumbing, flooring, locks, and sprinkler systems. Plan, direct and manage all phases of maintenance, facilities modification and building projects. Primary contact for facilities maintenance, project activities and conduct project reviews of cost, schedule and technical performance. Initiates bid processes with vendors on all aspects of project build-outs. Provide supervision and daily guidance to the janitorial team. Maintain cleaning and trash pick-up on a daily basis. Coordinate employee moves and scheduling within designated buildings. Maintain office equipment such as copiers, fax machines, and network printers. Show less
-
-
-
USS San Francisco SSN 711
-
San Diego CA
-
Logistics and Distribution Manager
-
Aug 2012 - Oct 2015
Lead a team consisting of managers, supervisors, inventory control specialists and material handlers to own and execute all store room, inventory control, materials and shipping & receiving functions. Reviewed products delivered. Determined adherence with and compliance to quantity and quality of product ordered. As required, initiates process to return unusable and/or unwanted products and supplies. Establish work processes that supported objectives in a cost effective manner. Managed and execute inventory control processes. Monitored and track all shipments to and from the ship to resolve or prevent delays. Created and manage budget for department Set performance standards, ensuring employees have appropriate and realistic job goals, provided ongoing feedback about employees’ performance, conducted performance appraisals, including assessing how the employees have performed and how they can improve their performance. Developed performance improvement plans if employees’ performance is not adequate and provided rewards for employee accomplishments. Show less
-
-
-
USS Boxer LHD-4
-
USS Boxer LHD-6 San Diego CA
-
LPO
-
2006 - 2012
Supervised the daily operation of the ship's engineering planet auxiliary and support systems. Provided leadership to over 50 personnel in the repair of critical auxiliary equipment during the Board of Inspection and Survey (INSURV) assessment and received a grade of “Outstanding”. Oversaw installation and equipment upgrade projects while serving as a point contact for all vendors and contractors. Managed personnel in the operational/corrective maintenance, repair and provided technical assistance for service equipment such as galley equipment, hot water heaters, water purification, compressed air systems, dehydrators, air conditioning units, steering systems, two emergency diesel generators, six cargo elevators, 2 aircraft elevators, 4 conveyors, one personal elevator, eight electric fire pumps, and all ships hydraulic systems, ensuring safe and efficient operation. Ensured proper maintenance compliance in accordance with Naval Ship’s Maintenance and Material Management Program and audited shipboard programs using a computerized self-evaluation checklist. Zero reportable safety incidents. Show less
-
-
Education
-
Naval Submarine School
Community
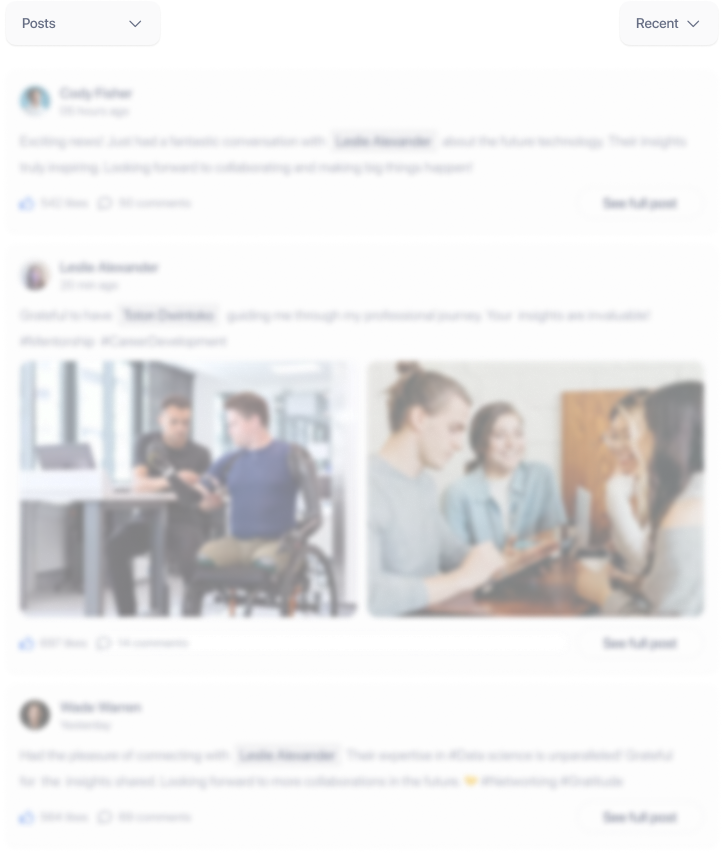