Mark Sutherland
VES Operational Excellence Leader at Trojan Technologies at Trojan Technologies- Claim this Profile
Click to upgrade to our gold package
for the full feature experience.
Topline Score
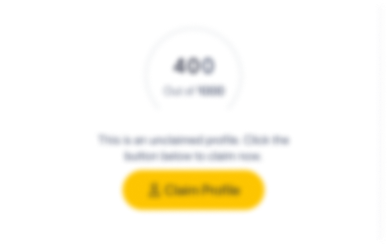
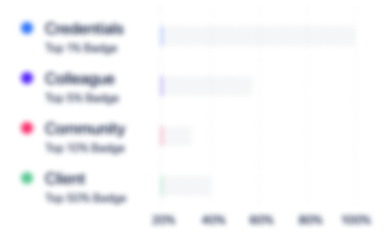
Bio


Experience
-
Trojan Technologies
-
Canada
-
Environmental Services
-
400 - 500 Employee
-
VES Operational Excellence Leader at Trojan Technologies
-
Feb 2015 - Present
London, Canada Area Provide overall lean leadership to manufacturing operations globally significantly impacting the areas of Safety, Quality, Delivery, Inventory and Production Implementing Lean Status Scores Audits and developing improvement priorities in conjunction with cell leaders Instrumental in the development of a lean culture across all levels of management and operations Led Kaizan that developed Pilot Sale and Delivery Process from an undefined state across multifunctional business units… Show more Provide overall lean leadership to manufacturing operations globally significantly impacting the areas of Safety, Quality, Delivery, Inventory and Production Implementing Lean Status Scores Audits and developing improvement priorities in conjunction with cell leaders Instrumental in the development of a lean culture across all levels of management and operations Led Kaizan that developed Pilot Sale and Delivery Process from an undefined state across multifunctional business units and resource teams including Value Stream Maps and Key Process Indicators resulting in clear and concise process flow, roles and responsibilities
-
-
Manager - Technical Assitance
-
Apr 2010 - Feb 2015
Responsible for providing direction to five teams: Technical Assistance; Aftermarket Controls; Warranty; Retrofit and Aftermarket Project Management ensuring the satisfactory resolution of customer concerns and continuous product and process improvements Led the development of Customer Defect Tracking and Resolution process (CDTR) which incorporates daily management activity to identify and resolve customer issues, resulting in reduction of warranty cost, increased technician competency and… Show more Responsible for providing direction to five teams: Technical Assistance; Aftermarket Controls; Warranty; Retrofit and Aftermarket Project Management ensuring the satisfactory resolution of customer concerns and continuous product and process improvements Led the development of Customer Defect Tracking and Resolution process (CDTR) which incorporates daily management activity to identify and resolve customer issues, resulting in reduction of warranty cost, increased technician competency and a significant decrease in concern resolution time Led Kaizen events in 2014 which identified 25% reduction in equipment startup expenses through the elimination of waste and increase efficiencies Achieved a 83% cycle time reduction over two years in 2013 and 2014 while undergoing a 12% head count reduction through the introduction and application of lean process management and the leveraging of technologies resulting in 12% year to year budget savings Led the development of the first team Vision, Mission and Strategy creating the foundation and providing direction for process improvement, now established as an annual event resulting in being ranked as one of the top 1% of managers in Danaher Corporation for two consecutive years Introduced process improvements that lead to a 20% increase in Customer Satisfaction pushing monthly approval scores consistently above 95% consistently for the last 3 years
-
-
Municipal Technical Assitance Centre Team Leader
-
Dec 2010 - Apr 2013
Leader of TAC Controls and TAC Product Teams Responsible for providing direction to two teams of high skilled controls programmers and electricians to ensure the satisfactory resolution of customer concerns
-
-
Project Manager
-
Sep 2009 - Jan 2011
Led the investigation and resolution of chronic, high profile, and potentially damaging customer issues through the use of sound problem solving and project management techniques; ensuring customer satisfaction while maintaining and enhancing the reputation of the company as a provider of innovative solutions
-
-
-
Rugby Ontario
-
Canada
-
Spectator Sports
-
1 - 100 Employee
-
Coach Jr. Men (U-14 /U-17/U-16)
-
2014 - Present
Toronto, Canada Area Coach responsible for delivery of a comprehensive program to develop athletes in accordance with the Long Term Rugby Development Model. The focus is on developing each athlete in terms of their technical, tactical, physical, mental and lifestyle capacities.
-
-
-
-
Coach - Jr. Mens
-
2009 - Sep 2019
London, Ontario Certified IRB Level 2 Certified IRB Strength and Conditioning Coach Level 1
-
-
-
-
ERP Implementation Analyst
-
Jan 1999 - Jan 2008
Directed Value Stream Mapping of current versus ideal state resulting in a Need Gap Analysis of the current business systems, soliciting input from the global operations, gaining their input and buy in, the outcome being a comprehensive Request for Quote for a replacement ERP. Collaborated with various functional teams throughout the company to successful launch new finance, purchasing, quoting and operational modules within the Enterprise Resource Plan (ERP). Acted as Interim Project… Show more Directed Value Stream Mapping of current versus ideal state resulting in a Need Gap Analysis of the current business systems, soliciting input from the global operations, gaining their input and buy in, the outcome being a comprehensive Request for Quote for a replacement ERP. Collaborated with various functional teams throughout the company to successful launch new finance, purchasing, quoting and operational modules within the Enterprise Resource Plan (ERP). Acted as Interim Project Leader as a result of restructure and elimination of the Director of Information Services role. Provided direction and set objectives for activities of the ERP Team; successfully championed the project kick off and negotiated project metrics with executive leadership in North America and China. As a team member authored the project plan, including scope of work, Gantt chart, budget and resources allocation plan, clearly communicating objectives to all levels of the organization. Influenced the Board of Directors to provide budget and resources to execute the implementation of a multi-million dollar ERP project with a significant reduction of global sales and general administration costs. Negotiated, as part of a team, to secure an ERP well below the original quoted price, meeting all criteria in the Request for Quote, leveraging the company's position as a global manufacturing, as well as demonstrating benefits to the vendor. Conducted differential analysis of 10 potential suppliers, evaluating and identifying the vendor best suited to meet the company's current and future business needs. Show less
-
-
-
Wescast Industries Inc.
-
Canada
-
Motor Vehicle Manufacturing
-
200 - 300 Employee
-
Program Manager
-
2001 - 2006
Managed the launch of a number of programs for exhaust components supplied to major automotive OEMs Led the launch of multiple new exhaust manifold programs meeting or exceeding all launch metrics. Mentored Program Managers and Quality Technicians providing expertise and advice to resolve non typical or problem situations. Spearheaded alternative part supplier when re-sourced supplier failed to meet launch timing, which threatened the delivery of 2004 model. Conceived a solution… Show more Managed the launch of a number of programs for exhaust components supplied to major automotive OEMs Led the launch of multiple new exhaust manifold programs meeting or exceeding all launch metrics. Mentored Program Managers and Quality Technicians providing expertise and advice to resolve non typical or problem situations. Spearheaded alternative part supplier when re-sourced supplier failed to meet launch timing, which threatened the delivery of 2004 model. Conceived a solution, negotiated the terms with the OEM, including: engineering; financial; and quality criteria. This achieved uninterrupted production of 60,000 engines per week, for several months. Ran several complex design changes involving detailed planning for building part banks and part validation. Coordinated the activities of various groups such as external customers, Sales, Manufacturing, Purchasing and Human Resources, meeting and typically exceeding all customer criteria, including engineering validation, budgets and deadlines. Expedited the launch timing of an alternate material critical to the company's fiscal well being, allowing cost savings to be realized several months earlier than budgeted, while satisfying all customer engineer testing requirements. Sought out by General Motors senior quality management, based on close business relationships and high degree of competency, to aid in the training of GMPT Supplier Quality Engineer.
-
-
Product Quality Engineering Technician
-
1999 - 2001
All quality aspects for the launch of automated machining lines Developed and launched a test program for exhaust manifolds which eliminated false rejects 100% and eliminated two man-hours per shift for non-value added work and increased throughput by 10%. Demonstrated knowledge of PPAP and Run at Rate requirements resulting in 100% acceptance rate.
-
-
-
-
Supplier Quality/ Customer Quality Engineer
-
1998 - 1999
-
-
-
-
Quality Assurance Supervisor
-
May 1997 - Mar 1998
-
-
-
-
Quality Project Leader
-
1997 - 1997
-
-
-
-
Project Coordinator
-
1996 - 1996
-
-
-
-
Commercial Quality Representative
-
Jan 1991 - Jan 1995
-
-
-
-
Commercial Sales and Service Representative
-
Jan 1989 - Jan 1991
-
-
Education
-
The University of Western Ontario
Diploma, Leadership -
Fanshawe College
Dip, Quality Assurance -
Brock University
BA, Sociology -
Medway High School
OSSHGD -
York University
Community
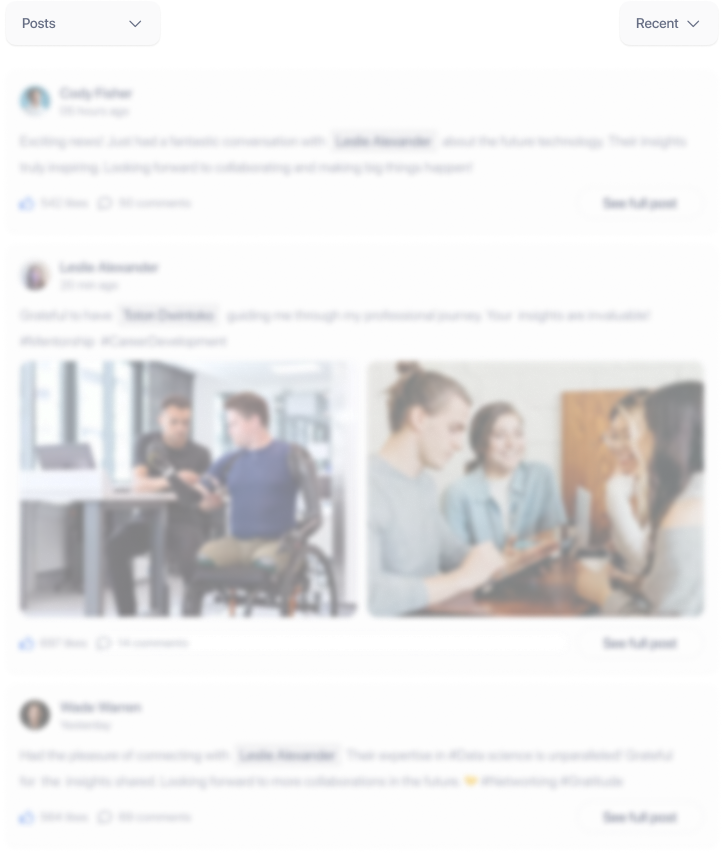