Paula Loucas
Manufacturing Quality Office Director at Naval Surface Warfare Center Indian Head Division- Claim this Profile
Click to upgrade to our gold package
for the full feature experience.
Topline Score
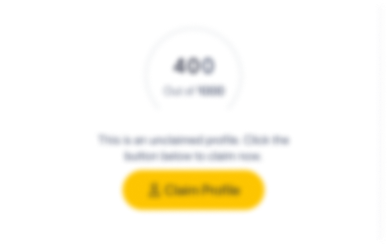
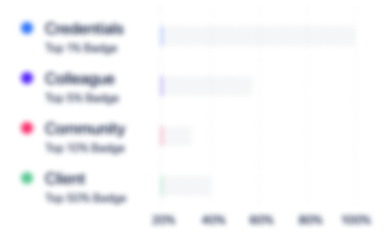
Bio


Experience
-
Naval Surface Warfare Center Indian Head Division
-
United States
-
Defense and Space Manufacturing
-
100 - 200 Employee
-
Manufacturing Quality Office Director
-
Nov 2021 - Present
Lead a growing team which supports the Energetics Manufacturing Department. Specifically, the functions include Documentation Control and Publication, Qualification/Certification, Quality Engineering, and Receipt Inspection.
-
-
Corporate Quality Engineer
-
Apr 2015 - Nov 2021
• Support 5 departments with over 100 active projects. • Participate in the Quality Community of Practice across all Warfare Centers• Develop quality management systems, instructions and guidance in accordance with ISO 9001:2015• Assist with planning/documenting in preparation of production• Monitor compliance via internal and supplier audits.• Conduct internal QMS audits at both the systems and the process level in accordance with ISO 9001:2015, ISO 17025, and mandated best practices. • Conduct calibration verification audits to verify compliance with ANSI/NCSL Z540-1• Conduct external (supplier, surveillance) audits and evaluate performance• Evaluate potential manufacturers’ submittals using objective evidence per contract requirements• Train employees in quality management system policies, procedures, roles, and responsibilities • Guide production engineers in quality planning and review quality plans and shop travelers• Participate in technical design reviews, test readiness reviews, and production readiness reviews as an independent panel member• IPT team member working with customer and design agents to address project concerns• Lead lean manufacturing project teams as certified lean six sigma greenbelt• Facilitate problem solving teams, using appropriate root cause analysis tools (5 Whys, fishbone)• Initiate and track corrective/preventive action reports• Lead investigation teams• Maintain electronic discrepancy reporting database for manufacturing and testing Show less
-
-
-
-
Chemical Engineer
-
Nov 1989 - Present
-
-
-
-
Quality Engineer
-
Apr 2006 - Nov 2015
• Support approximately 30 engineers with over 40 active projects. • Develop quality management systems, instructions and guidance in accordance with ISO 9001:2008 • Assist with planning/documenting in preparation of production • Monitor compliance via internal and supplier audits. • Conduct internal QMS audits at both the systems and the process level in accordance with ISO 9001:2008, ISO 17025, and mandated best practices. • Conduct calibration verification audits to verify compliance with ANSI/NCSL Z540-1 • Conduct external (supplier, surveillance) audits and evaluate performance • Evaluate potential manufacturers’ submittals using objective evidence per contract requirements • Train employees in quality management system policies, procedures, roles, and responsibilities • Guide production engineers in quality planning and review quality plans and shop travelers • Participate in technical design reviews, test readiness reviews, and production readiness reviews as an independent panel member • IPT team member working with customer and design agents to address project concerns • Lead lean manufacturing project teams as certified lean six sigma greenbelt • Facilitate problem solving teams, using appropriate problem-solving tools (5 Whys, fishbone) • Initiate and track corrective/preventive action reports • Lead investigation teams • Designed and maintain electronic discrepancy reporting database for manufacturing and testing • Developed cost of poor quality tool for quality metrics tracking • Manager of quality and production control branch (16 employees, 2010-2012) Show less
-
-
-
-
Chief Learning Officer
-
2005 - 2006
• Department respresentative for 400+ employees• Assessed technical health and developed gap analysis • Developed progressive development plans for each job series represented at the facility. • Assisted employees with Individual Development Plans• Led teams of judges involved with local science fairs• Teamed with local university and county educators to develop, implement, and subsequently teach industry-relevant science/engineering lesson plans to K-12 students.
-
-
Facilities Engineer
-
2004 - 2005
• Re-activated abandoned equipment and facilities essential to extrusion operations in support of time-critical production efforts• Configured a lean manufacturing assembly line• Conducted hazards and OSH analyses of operations
-
-
Production Engineer
-
1992 - 2004
• Engineer in charge of production and rework of various products for both military and private sector use • Developed new process capabilities for novel chemicals, including preparation of TSCA submittals and OSH considerations• Responsible for small-scale equipment design/set-up/proof-out, testing and approval for use of materials, developing hazards analyses, standard operating procedures, quality documentation, scheduling, execution, and costs. • Submitted TSCA applications and responded to EPA queries • Presented research and development findings to technical audiences at conferences• Developed operator training in support of manufacturing• Developed specifications and estimates to replace a 1959-era chemical production facility with a new agile chemical facility Show less
-
-
Pre-production Engineer
-
1989 - 1992
• Worked with developers and pilot plant to ensure manufacturability at production scale versus experimental• Transitioned to low rate initial production and then to full-scale manufacturing• Designed casting configurations, assisted in developing munitions specifications, and developed all necessary operating documentation, hazard control briefings, and readiness reviews• Responsible for production of items manufactured via mixing and casting, including optimizing mix formulations, scheduling work efforts, execution, and financial tracking/reporting• Presented quarterly reviews to management, customers, and technical personnel. Metrics included cost performance, statistical process control charts/analysis, discrepancy assessment, and schedule. Show less
-
-
Education
-
West Virginia University
Bachelor's Degree, Chemical Engineering
Community
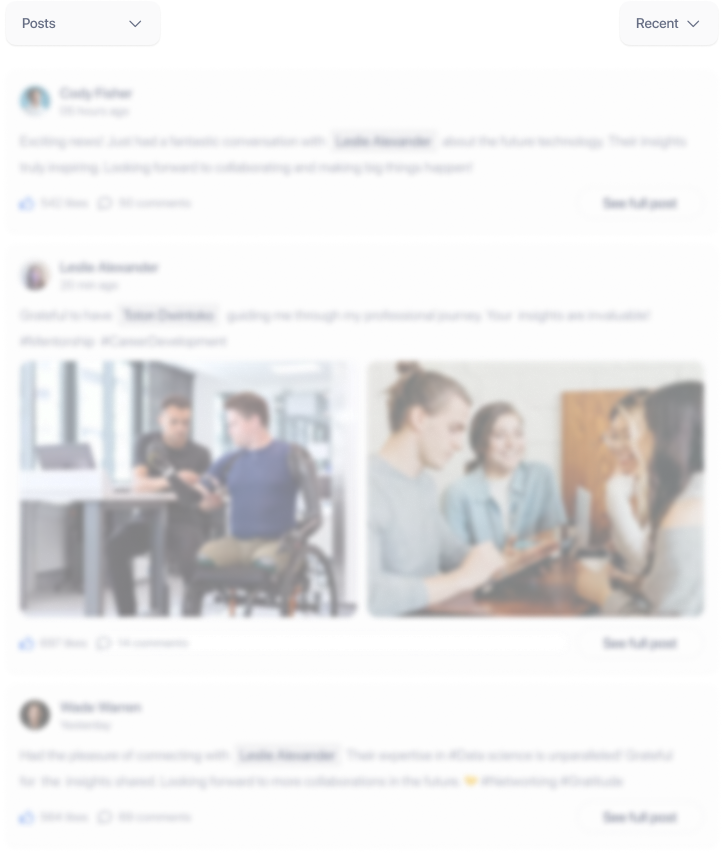