Christian Davidson
Project Manager at Global Management Partners- Claim this Profile
Click to upgrade to our gold package
for the full feature experience.
Topline Score
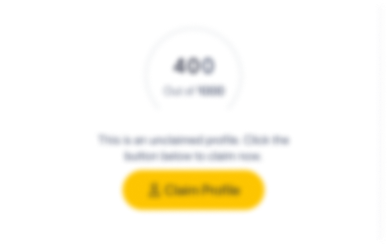
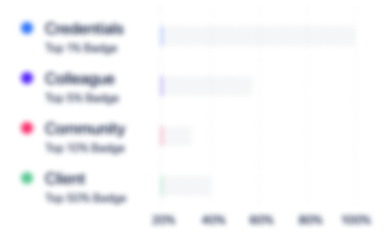
Bio


Experience
-
Global Management Partners
-
United States
-
Business Consulting and Services
-
1 - 100 Employee
-
Project Manager
-
Feb 2022 - Present
-
-
-
-
Small Business Owner
-
Jun 2021 - Present
Owner and operator of a handyman business providing a wide range of services to clients in need of home or business repair, cleaning, construction, demolition, improvement, or upkeep. Owner and operator of a handyman business providing a wide range of services to clients in need of home or business repair, cleaning, construction, demolition, improvement, or upkeep.
-
-
-
Faith and Fitness, LLC
-
United States
-
Small Business Owner
-
Mar 2019 - Present
Owner and operator of a health and wellness business providing personal fitness training and instruction for achieving fitness goals while also strengthening ones faith through prayer, support, and developing a more personal relationship with God. Owner and operator of a health and wellness business providing personal fitness training and instruction for achieving fitness goals while also strengthening ones faith through prayer, support, and developing a more personal relationship with God.
-
-
-
QuEST Global
-
Singapore
-
IT Services and IT Consulting
-
700 & Above Employee
-
Center Manager & Operations Leader
-
Sep 2016 - Apr 2021
Responsible for leading and overseeing the operations, performance, and delivery of multiple engineering centers in the United States providing engineering services to key customers such as GE Power and Siemens Energy.• Assumed leadership over the QuEST Greenville, SC Center supporting GE Power and implemented organizational structures, processes, policies, process improvements, quality standards, and employee engagement activities for 105 employees in 5 different locations; as well as set and drove culture changes, resolved issues as a human resources liaison, developed sales collateral, executed contract negotiations, established customer contact plans, improved communication strategies, provided annual forecasts, set training and development standards, executed periodic and annual performance reviews, managed, coordinated, and implemented workforce reductions, set, tracked, and managed performance metrics, KPI’s and budgets, and built professional relationships with QuEST and business customers to enhance the overall operations of the center resulting in a performance improvement that exceeded the annual target metrics and KPI’s and set the benchmark for other centers in North America as one of the top performing centers.• Assumed leadership over the QuEST Charlotte, NC Center supporting Siemens Energy from March 2018 to March 2019; and implemented all of the above for 43 employees in 3 different locations; which resulted in a performance improvement that exceeded the annual target metrics and KPI’s and set the benchmark for other centers in North America as one of the top performing centers.• Managed, tracked, and coordinated the onboarding, transitioning, renewals, and exits of international employees on work VISA’s; as well as implemented export control laws and regulations for data security and IP protection per policy.• Crisis Management Leader, Incident Management Leader, and Fire Marshal for Greenville Center.
-
-
Program Manager
-
Oct 2014 - Sep 2016
Responsible for leading and overseeing the operations, performance, and delivery of multiple engineering teams providing Testing, Project Management, and Control Systems engineering services to Pratt & Whitney.• As a result and continuation of my success in building the Control Systems team (See Engineering Team Lead section); QuEST shifted the Product Management and Integration (PMI) team under my leadership because they were struggling to perform and were in conflict with their existing leadership, causing significant attrition and loss of quality and execution. Within 3 months the team was performing alongside my Control Systems team as one of the top two highest performing teams in the organization – exceeding all performance metric targets and KPI’s, and having the highest employee satisfaction rating (ESAT) in the Center.• As a result and continuation of my success with the Control Systems and PMI teams, QuEST shifted theTesting & Validation (T&V) team under my leadership as well; allowing me to lead and oversee all threeteams simultaneously. Within 1 month the T&V team was among the top 3 highest performing teams inthe organization alongside my Control Systems and PMI teams.• Business forecasting, finance management, capability development, resource management andallocation, project management, budgeting, and all activities associated with the daily operations of theprogram execution.• Process improvement, quality, delivery execution, metrics tracking and reporting, export control, performance evaluations, interviewing / hiring, human resource activities, sales support, employee satisfaction, training & development of resources, risk management and mitigation, new business development, customer relations, change management, and productivity improvement.• Executing day-to-day Control Systems engineering services for requirements management, validation, and verification of multiple PW turbine engines using IBM DOORS.
-
-
Team Lead
-
Jan 2012 - Oct 2014
Solely took on a first-of Control Systems work package performing requirements clean-up and traceability for multiple Pratt & Whitney turbine engine programs which led to the creation of a new “Control Systems” department within QuEST and a 92% increase in revenue within the first 2 years. • Solely hired and trained a control systems team of 12 people, defined processes, established best practices, developed training curriculum, created engineering standard work, managed projects and finances, and worked tasks to completion to ensure 100% on-time delivery with 0 escapes. This resulted in the creation of the highest performing team in the organization.• Provided individual training to employees on job tasks, project management, process tailoring, best practices, and earned value; and increase employee morale through team building exercises, encouragement, inspiration, emphasizing employee value to the company, and providing ownership and responsibility to empower individuals and build self-esteem. • Provided business forecasting, finance management, capability development, resource management and allocation, project management, budgeting, and all activities associated with the daily operations of the team execution.• Executed process improvements, quality, delivery execution, metrics tracking and reporting, export control, performance evaluations, interviewing / hiring, human resource activities, sales support, employee satisfaction, training & development of resources, risk management and mitigation, new business development, customer relations, change management, and productivity improvements.• Export Control Reviewer - Reviewed proprietary documents and technical data; determined the correct export control classification; applied proper export control markings to documents, and exported the data to the necessary approved recipients to ensure 100% data security and integrity with 0 incidents.
-
-
Project Engineer
-
Oct 2011 - Jan 2012
• Provided requirements traceability and clean-up for Airbus, BA, and MRJ engine programs using the DOORS system for the Control Design Systems group at Pratt & Whitney, as well as Validation and Verification services for Airbus engine certification with 100% on-time delivery. • Created and/or revised Engineering Standard Work (ESW) to improve processes and provided over $325K in approved annual cost savings to Pratt & Whitney.• Created, tracked, and managed implementation, flow-down, and completion of engineering design changes via Engineering Coordination Memo’s (ECM’S) to ensure 100% accuracy in design manufacturing. • Scheduled and hosted meeting with chief engineers and technical leaders to review design changes and approve them in real-time to reduce drag and improve delivery times and efficiency which resulted in a reduction of required man-hours and an additional cost-savings to Pratt & Whitney.• Drove actions throughout engineering teams to solidify communication between groups and levels in the organization and keep tasks on track and on time with a 100% on-time success rate.• Developed training material to reduce drag and streamline employee onboarding which resulted in a process improvement that increased efficiency and saved man-hours.• Implemented and managed quality processes resulting in 100% on-time delivery with 0 escapes or quality issues.• Tracked project budget, earned value, and progress resulting in 100% on-time delivery within budget for all projects owned.
-
-
-
-
Avionics Engineer
-
Jan 2008 - Sep 2010
• Supported systems integration of UH-60M military Blackhawk helicopters and HH-60M military Medevac helicopters contracted by the U.S. government by ensuring quality and efficiency of installed avionic and electrical systems and components resulting in 100% mission-effectiveness for the U.S. military.• Ensured the quality of system software through testing and inspection, and maintained a database of all components; resulting in a 100% success rate of avionic and electrical systems integration on the UH and HH-60M military Blackhawk helicopters.• Troubleshot and resolved unexpected system failures and procure a means of repairing them within the scheduled production time allotted.• Trained and monitored new engineers on functions required to perform job tasks according to company expectations and policies.• Interfaced with individuals in numerous departments on a daily basis to ensure complete reliability in the production process, to include: Quality Assurance, Aircraft Flight Controls, Software Technicians, Wiring and Design Personnel, Electrical Leads, Production Leads, Checkout Personnel, Installers, Production Foreman, Hangar Personnel, and Aircraft Pilots.• Created and manage databases on a weekly basis that account for aircraft productivity factors used in identifying possible short falls and improving the production process and manufacturing of aircraft; along with providing a history of components and known failures that aided in saving many man-hours of troubleshooting.• Performed and developed Engineering Test Procedures (ETP's) and Acceptance Test Procedures (ATP's) of Integrated Avionics Systems in a lab environment to ensure 100% system compatibility.• Trained in water survival, egress, and F.O.D. prevention.• 6S manager for Zone 3 in the Sikorsky new engineering building 2nd floor, bringing the zone from ACE Silver to ACE Gold in just under two months.• Trained individuals at Sikorsky Aircraft on F.O.D. prevention and awareness.
-
-
-
-
Equations & Sequences Editor
-
Jan 2007 - Jan 2008
• Interpreted, transformed, edited, proofed, and input mathematical equations and DNA sequences into a computer database used in the pre-grant process for the U.S. Patent Office, exceeding output metrics by three times the required amount with a 99% accuracy rating.• Inspected on-going patents for quality resulting in 100% accuracy in the data therein.• Trained and supervised other employees on computer-based job tasks and supplementary work functions within the company.• Gave feedback and tallied up work and error ratios for employees on a weekly basis to improve overall operational efficiency.
-
-
-
United States Air Force
-
United States
-
Defense and Space Manufacturing
-
700 & Above Employee
-
Aircraft Weapon Systems Senior Controller
-
Oct 2003 - Aug 2006
• Managed all military personnel involved in military mission deployment by controlling operations for McGuire Air Force Base, NJ; to include aircraft maintenance, refueling, defueling, towing , coordinating emergency responses, mishap prevention, air-to-ground communications for flight arrivals and departures, and flight scheduling; resulting in 100% mission effectiveness.• Trained and monitored individuals on all responsibilities, duties, data systems, and tasks required to effectively coordinate all maintenance and operations for over 50 aircraft resulting in 100% aircraft mission readiness.• Managed and tracked the maintenance and recovery of aircraft worldwide by organizing deployable repair teams, parts required, travel arrangements, and maintenance processes to ensure 100% effectiveness in the deployment of military aircraft.• Gathered and managed intelligence on all aircraft status and maintenance activities on base, and debriefed the expeditors and commanders in order to aid them in military mission planning and decision-making.• Compiled and managed four completely different military aircraft databases simultaneously to aid in keeping detailed records of each aircraft on base to aid in mission planning and decision-making regarding military operations both during war and peacetime resulting in 100% mission effectiveness. • Served in this role running base operations during a tour overseas for post 9-11 wartime operations: Operation Iraqi Freedom and Operation Enduring Freedom ensuring 100% mission effectiveness and earning 4 military war medals to include the Air Force Achievement Medal, Global War on Terrorism Service Medal, National Defense Service Medal, and Global War on Terrorism Expeditionary Service Medal with Gold Border for serving in hostile territory.
-
-
Air Force Honor Guard
-
Jun 2003 - Oct 2003
• Performed duties as flag bearer, flag folder, flag presenter, firing party, pall bearer, and detail leader for over 86 military funerals throughout Connecticut, New York, New Jersey, and Pennsylvania that brought honor to the U.S. Air Force, the United States of America, and the men and women who gave their lives to defend it.• Performed duties as a swordsman and detail leader for several military weddings.• Performed duties as a ceremonial guardsman, flag bearer, and detail leader for dozens of military retirement ceremonies, promotion ceremonies, and military events held on base; as well as major events off base such as Major League Baseball games at Yankee Stadium and the Miss America Pageant in Atlantic City, NJ.• Trained local school ROTC students in honor guard rifle drills and ceremonial procedures.• Trained other honor guard members in performing ceremonial procedures for each type of event.• Performed duties as a key note speaker for middle school and high school assemblies, promoting support for our military, higher education, and a drug-free lifestyle to hundreds of school students around New York and New Jersey.
-
-
Air Force Security Forces
-
Oct 2002 - Jun 2003
• Volunteered to support military security forces to reinforce base security and ensure the safety and security of all military personnel on base during an active time of war when short on staff.• Ensured the safety and security of all personnel and equipment on base by performing guard duties at the front gate, and searching all commercial vehicles for illegal and explosive contraband during an active time of war.• Inspected vehicles and issued passes for individuals visiting or delivering to the Air Force Base.
-
-
Electronic Warfare Systems Technician
-
Jul 2001 - Jun 2003
• Performed, trained, and supervised individuals on performing inspections, installation, and maintenance on electronic warfare (EW), radar, analysis equipment, and special purpose support equipment to ensure 100% effectiveness during military operations.• Assembled wiring harnesses, tool kits, circuit boards, cannon plugs, coaxial cables, and various system mock-ups used to train new individuals and repair aircraft on base.• Inspected, accounted, maintained, organized, and replenished bench stock for the Electronic Warfare (EW) shop to ensure 100% dependability in resource availability. This includes purchasing items from various vendors to ensure cost efficiency for the given budget.• Conducted in-progress and final inspection of components to ensure 100% compliance with standards.• Conducted policy and safety briefings to ensure 100% mishap prevention in the EW shop.• Managed and maintained the safety program for the EW shop which resulted in 0 mishaps and injuries in and around the work place.• Managed, inspected, accounted, maintained, and supplied hazardous material within the EW shop to include training individuals on proper storage, usage, and contamination procedures using the MSDS (Material Safety Data Sheets).• Managed, maintained, and inspected Technical Order (T.O.) system for the Maintenance Operations Center to ensure 100% effectiveness in the accuracy of mission essential information and technical data for maintenance procedures.• Managed inspections, maintenance, and upkeep of shop vehicles to ensure 100% efficient operation at all times.
-
-
Education
-
GlobalNxt University
Certification in Global Business Leadership, International Business -
University of New Haven
Master of Business Administration - MBA, Business -
Embry-Riddle Aeronautical University
Bachelor's Degree, Professional Aeronautics -
Community College of the Air Force
Associate's Degree, Avionic Systems Technology
Community
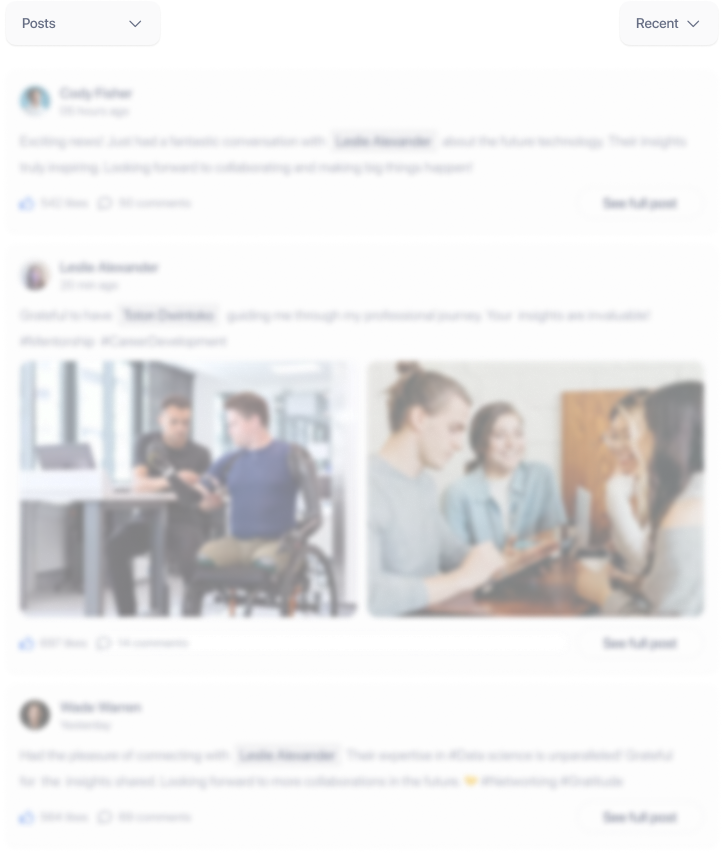